Un proceso SLS invertido para imprimir en 3D con múltiples materiales a la vez
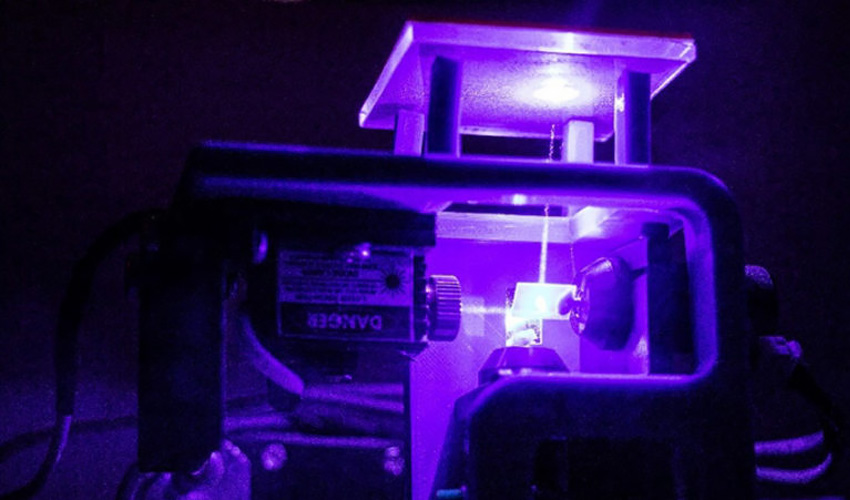
La tecnología de sinterización selectiva por láser es uno de los procesos más utilizados en el mercado de fabricación aditiva. Permite que las partículas de plástico calentadas por una fuente de calor, normalmente un láser, se unan. Una de las limitaciones de esta tecnología en la actualidad es la imposibilidad de combinar varios materiales en una sola impresión, lo que reduce el rango de posibilidades. Sin embargo, parece que los investigadores de la Universidad de Columbia han logrado superar este obstáculo desarrollando un proceso SLS invertido: en lugar de tener un láser apuntando hacia abajo, lo colocaron para que se dirija hacia arriba. También eliminaron el lecho de polvo real reemplazandolo con placas de vidrio transparente recubiertas con el material (o materiales) de impresión. La pieza se imprime de arriba a abajo y puede combinar varios plásticos.
Convencido del potencial de la fabricación aditiva, un equipo de profesores de innovación en ingeniería mecánica examinó la tecnología de sinterización selectiva por láser. Según ellos, uno de los mayores obstáculos para este proceso es el hecho de que no se pueden mezclar diferentes materiales, pero también que no podemos ver la pieza que se está imprimiendo, evitando que se note un error o anomalía, como en una máquina de deposición de material fundido, por ejemplo. Uno de los investigadores, Hod Lipson, agrega: “¿Cuántos productos están hechos de un material? Las limitaciones de la impresión de un solo material obsesionaron a la industria y bloquearon su expansión, impidiendo que alcanzara su máximo potencial”. De hecho, el proceso SLS deposita una capa de polvo que el láser fusiona en puntos muy precisos, de forma selectiva. Una vez terminado, la máquina deposita una nueva capa de polvo, y así sucesivamente, capa por capa. El problema hoy en día es que no se puede colocar un polvo diferente al primero; no se puede tener nylon y luego TPU, por ejemplo.
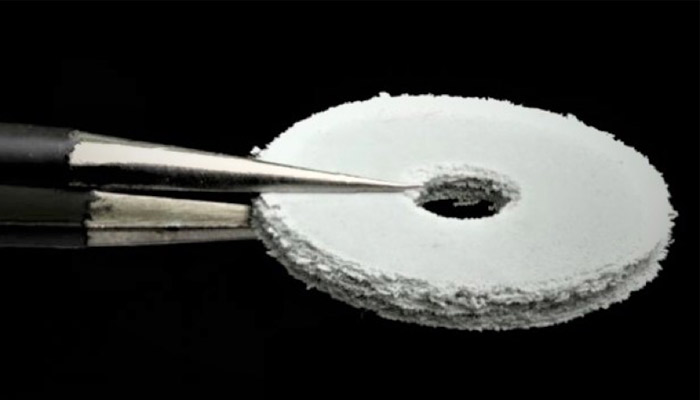
Una de las muestras impresas en 3D en TPU | Créditos: Universidad de Columbia
John Whitehead, autor principal del estudio, continúa: “Además, en una impresora estándar, debido a que cada una de las capas sucesivas depositadas es homogénea, el material sin fundir oscurece la vista del objeto a imprimir que elimine la parte terminada al final del ciclo. Esto significa que no se encontrará necesariamente un defecto de impresión hasta que se complete el proceso, lo cual es una pérdida de tiempo y dinero”. Para resolver estos dos obstáculos principales, los investigadores invirtieron el proceso.
Cómo funciona el proceso invertido de SLS
En lugar de tener un lecho de polvo clásico, los profesores optaron por placas de vidrio transparentes en las que pusieron diferentes polvos de plástico. Debajo de estas placas, los láseres apuntaban hacia arriba con el disparo, en lugar de colocarlos en máquinas convencionales. La plataforma de impresión se baja luego sobre la superficie de la placa de vidrio, por lo tanto sobre el polvo, y el láser calienta la pieza a sinterizar de acuerdo con el modelo 3D. Una vez que se termina el láser, la plataforma se eleva con el material fundido encima. Luego se puede repetir esta operación en otras placas cubiertas con otro polvo plástico.
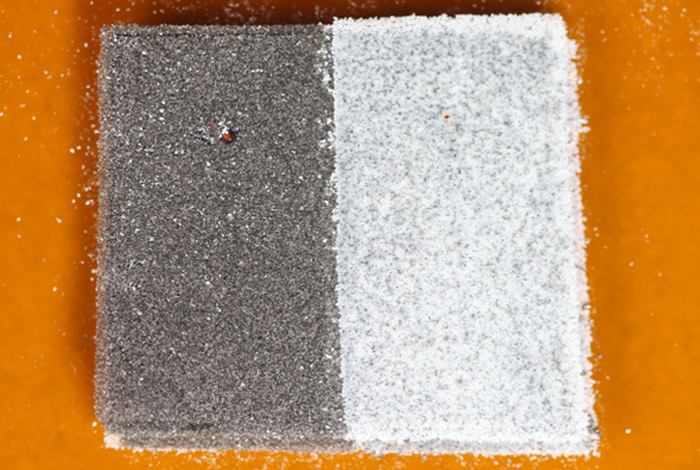
La otra muestra impresa en 3D a partir de nylon y TPU
Lipson dice: “Esta tecnología tiene el potencial de imprimir circuitos integrados, componentes electromecánicos e incluso componentes de robots. Creemos que esto ampliará la sinterización láser a una variedad más amplia de industrias al permitir la fabricación de piezas complejas de múltiples materiales sin ensamblar. En otras palabras, podría ser la clave para cambiar la industria de fabricación aditiva de la impresión de piezas uniformes pasivas únicamente a la impresión de sistemas integrados activos”.
Para demostrar las posibilidades de este nuevo proceso SLS invertido, el equipo imprimió en 3D una primera muestra de 50 capas de 2,18 mm de espesor a partir de un polvo de poliuretano termoplástico (TPU) con una altura de capa media de 43.6 micras y un segundo compuesto de nylon y TPU con una altura de capa promedio de 71 micras. Actualmente están trabajando en la combinación de resinas plásticas y metales para diseñar piezas con propiedades mecánicas, eléctricas y químicas más interesantes. Para obtener más información, puedes visitar el sitio web oficial de la universidad AQUÍ o ver el video a continuación:
¿Qué piensas del proceso SLS invertido? Deja tus comentarios en nuestras redes sociales: Facebook, Twitter, Youtube y RSS. Sigue toda la información sobre impresión 3D en nuestra Newsletter semanal.