¿Cómo obtener mejores textiles con impresión 3D?
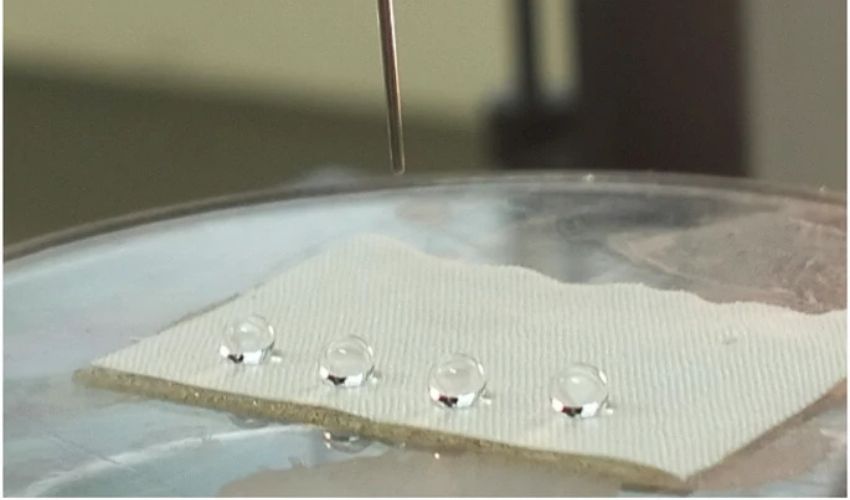
Si lees seguido las noticias que compartimos en 3Dnatives quizá ya te hayas dado cuenta de que la impresión 3D está en una continua expansión. Existen avances en sectores tan diversos entre sí como el del diseño de interiores y la automoción. En esta ocasión hablaremos de un nuevo estudio en la industria textil. Un equipo multidisciplinar en Italia ha logrado combinar técnicas de impresión con soluciones químicas sostenibles para crear textiles con propiedades avanzadas como repelencia al agua, resistencia a manchas y abrasión. ¿Cómo lo hicieron? Con un recubrimiento a base de quitosano, un biopolímero derivado de residuos naturales. Esta investigación propone una alternativa ecológica a los tratamientos tradicionales y demuestra cómo la impresión 3D puede jugar un papel esencial en la producción de textiles funcionales.
El centro de este estudio es el uso de recubrimientos basados en quitosano sobre tejidos de algodón y poliéster. Estos aditivos no solo mejoraron la estabilidad del recubrimiento, sino que también facilitaron la formación de superficies altamente hidrofóbicas, es decir, superficies que repelen el agua mucho mejor que otros tejidos sin tratar. El estudio demostró que esta combinación de materiales permite desarrollar textiles impermeables y que no atrapan la suciedad sin comprometer la textura o transpirabilidad del tejido.
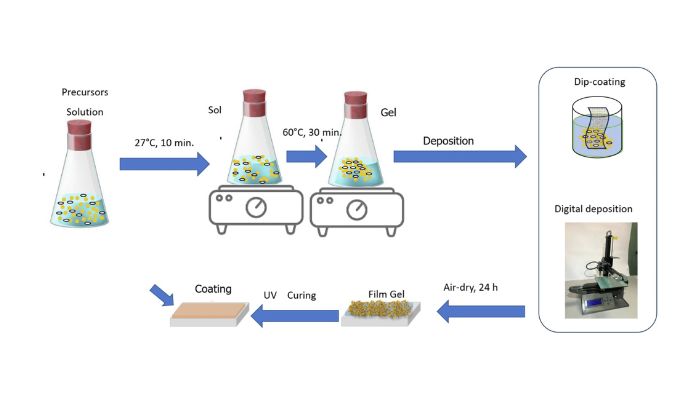
Proceso para el recubrimientos de los textiles.
Otro aspecto clave del estudio fue el uso de curado UV. A diferencia del curado térmico que implica altos consumos energéticos y puede dañar las fibras textiles, la exposición a luz ultravioleta ofrece una alternativa más amigable con el medio ambiente y más suave con los textiles. Gracias a esta técnica, se logró una adhesión duradera del recubrimiento sin afectar la integridad del tejido. Además, las pruebas de resistencia al lavado y abrasión demostraron que los recubrimientos mantenían sus propiedades incluso después de múltiples ciclos de uso, superando una de las principales limitaciones del quitosano, su baja resistencia al agua.
Precisión y control para mejores textiles
En una fase avanzada del estudio, los investigadores integraron las soluciones de quitosano con una impresora 3D de Anycubic, adaptada con un sistema de inyección por micro electro válvulas. Este sistema permitió depositar capas precisas de recubrimiento sobre las telas, garantizando una cobertura uniforme y un consumo mínimo de material. El diseño de las capas se realizó digitalmente, y los parámetros de impresión se optimizaron cuidadosamente. Este método de impresión no solo mejoró la calidad del recubrimiento, sino que también se puede usar en el futuro para personalizar las propiedades del tejido de forma rápida.
El trabajo, liderado por Rosa Taurino de la Universidad de Florencia, propone entonces soluciones híbridas basadas en quitosano como recubrimientos multifuncionales para textiles. Al utilizar compuestos no tóxicos y técnicas de curado por UV, lograron un tratamiento respetuoso con el medio ambiente que mejora significativamente la repelencia al agua y la resistencia al desgaste. Además, la incorporación de la impresión 3D como método de aplicación representa un avance notable en el control de los procesos para producir textiles con funciones específicas.
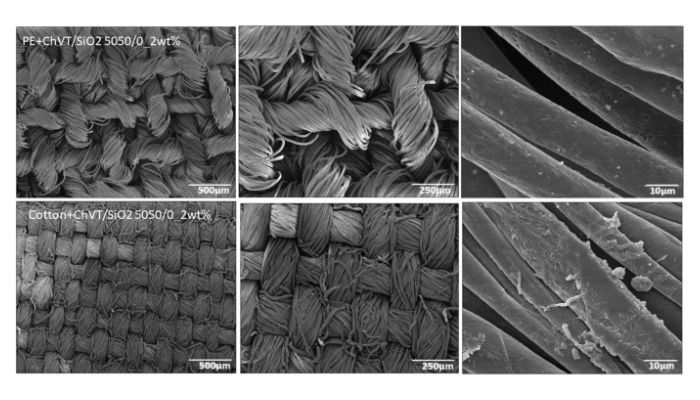
Imágenes microscópicas de los tejidos recubiertos.
La investigación abre nuevas posibilidades en la fabricación de textiles inteligentes para ropa deportiva, prendas de exterior y aplicaciones técnicas. A futuro, se podrían explorar nuevas formulaciones de biopolímeros y combinaciones con nanopartículas funcionales. Incluso, sistemas de impresión que se adapten para responder en tiempo real a las características del tejido. Un ejemplo de que la impresión 3D no solo es imprimir objetos. Si quieres conocer más sobre la investigación, haz clic aquí.
¿Qué opinas de usar la impresión 3D en la industria textil? Deja tus comentarios en nuestras redes sociales: Facebook, LinkedIn y Youtube. Sigue toda la información sobre impresión 3D en nuestra Newsletter semanal.
*Créditos de todas las fotos: Taurino, R., Cannio, M., Martinuzzi, S. et al.