McLaren Racing y Stratasys: juntos para un mejor rendimiento de las carreras
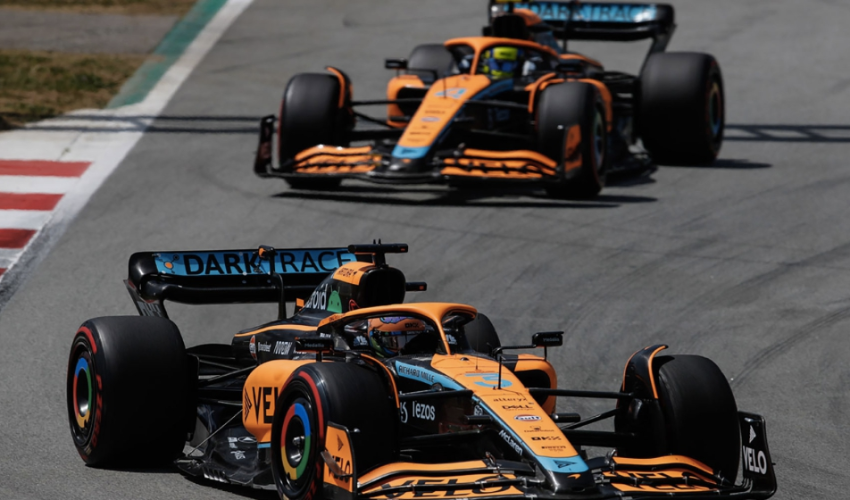
Si le interesan las carreras de coches, especialmente la Fórmula 1, y la impresión 3D, seguro que le resultan familiares los nombres de McLaren Racing y Stratasys. Estos dos han unido sus fuerzas para crear el mejor rendimiento de su clase. En la Fórmula 1, una cosa cuenta por encima de todo: la velocidad. Sin embargo, esto no sólo es de gran importancia en la propia pista de carreras, sino también fuera de ella, por ejemplo en los tiempos de producción de las piezas del modelo. Aquí es donde la fabricación aditiva puede ayudar a ganar la «carrera» contra el tiempo fuera de la pista.
McLaren Racing está respondiendo a las restricciones de tiempo y presupuesto más estrictas de la FIA para la producción de coches en 2022, entrando en una colaboración con Stratasys que les permitirá la fabricación aditiva de decenas de miles de piezas. Para ello, confían en la impresora 3D Neo800 de Stratasys para reducir el tiempo de producción de algunas piezas del modelo a sólo tres días y acelerar también el desarrollo del vehículo.
Ámbitos de aplicación de las piezas de fabricación aditiva
Con el deporte enfrentándose en tiempos inciertos y sin ingresos durante un periodo prolongado debido a la pandemia del Covid 19, la FIA había decidido reducir el tope presupuestario de 175 millones de dólares a 145 millones para el primer año de funcionamiento en 2021, más tarde a 140 millones para 2022 y 135 millones para 2023.
Por ello, McLaren confía en la impresión 3D y produce hasta 9.000 piezas al año para los alerones delantero y trasero, así como grandes partes de la carrocería lateral y superior mediante métodos de fabricación aditiva. Según la escudería, estas piezas asegurarían un gran progreso en la optimización de la aerodinámica del vehículo en las pruebas del túnel de viento. Las piezas son más precisas gracias a la impresión 3D y, además del aspecto de la calidad, el tiempo de producción de las piezas también se ha reducido drásticamente, de modo que el equipo puede ahora producir ciertas piezas grandes, como los paneles de la parte superior de la carrocería a escala, en sólo tres días, y a un precio más rentable.

Pieza de vehículo impresa en 3D (Imagen: Stratasys)
Sin embargo, el uso de la tecnología de impresión 3D no sólo aporta ventajas para McLaren Racing, sino también para el medio ambiente. Gracias a sus impresoras internas, McLaren puede producir todas las piezas aerodinámicas en su planta de Woking (Reino Unido). Esto reduce los largos plazos de entrega y las distancias de transporte, así como los costes asociados y el impacto medioambiental. La fabricación aditiva no sólo puede utilizarse para producir piezas de automóviles, sino que el equipo también puede imprimir en 3D plantillas de montaje y pequeños moldes que antes había que fresar a partir de bloques de metal. Por lo tanto, el uso del proceso de estereolitografía Neo800 no sólo ahorra mucho tiempo, sino también metal caro, ya que el fresado desperdicia grandes cantidades de virutas. Tim Champman, jefe de fabricación aditiva de McLaren Racing, también explica: «La tecnología y los materiales de la estereolitografía han evolucionado y también lo ha hecho la forma de utilizarlos. Ya no nos limitamos a fabricar prototipos, sino que ahora producimos muchos componentes y utillajes a tamaño real».
Impresión 3D para mejorar el rendimiento en McLaren
En las carreras de Fórmula 1, como todos sabemos, cada segundo cuenta. Para medir ese rendimiento, se basan en las pruebas de túnel de viento. Según Chapman, estas pruebas siguen siendo el estándar de oro cuando se trata de evaluar el funcionamiento conjunto de todas las superficies, ya sea como conjunto o como coche completo. Por ello, McLaren considera que ésta es la mayor ventaja de su nueva generación de impresoras Neo800. La resina utilizada para la impresión es Somos® PerFORM Reflect, desarrollada específicamente para los modelos de túnel de viento. Esto produce piezas robustas y rígidas con un 30% menos de tiempo de posprocesamiento. «Nuestras impresoras 3D de la serie Neo nos han ayudado a reducir drásticamente los plazos de entrega de nuestros componentes y proyectos de túneles de viento aerodinámicos», afirma Chapman. El equipo utiliza el 60% de los modelos a escala real para optimizar el paquete aerodinámico y conseguir más carga aerodinámica, lo que proporciona más agarre aerodinámico. Esto ayuda a equilibrar las cargas aerodinámicas en la parte delantera y trasera del coche.
Los componentes de alta precisión de las impresoras Neo también requerirían un reajuste manual mínimo, lo que permitiría un rendimiento mucho más rápido en el túnel de viento. Además de la ventaja de la velocidad, ahora pueden producir piezas para el túnel de viento con la mayor precisión, detalle y mejor acabado superficial. Esto ha permitido al equipo mejorar las pruebas y aportar nuevas ideas innovadoras para mejorar el rendimiento. Chapman no podría subrayar lo suficiente la importancia de estas ventajas en la Fórmula 1. Al fin y al cabo, los plazos de entrega de los coches para la siguiente carrera son siempre muy ajustados y el más mínimo ajuste de diseño puede marcar la diferencia entre ganar o perder, o ayudar a mejorar las posiciones. Andy Langfeld, Presidente de EMEA en Stratasys, también dijo:
«El valor transformador de la impresión 3D proviene de la capacidad de personalizar y adaptar rápidamente las piezas para aplicaciones específicas. En este caso, McLaren fue capaz de reducir drásticamente el tiempo de desarrollo del producto a la vez que controlaba totalmente los costes al combinar la tecnología de estereolitografía de última generación de Stratasys con los materiales de primera clase de Somos y nuestra amplia experiencia en carreras. Es una gran asociación entre dos organizaciones de categoría mundial».
¿Qué piensas de esta unión entre McLaren Racing y Stratasys para un mejor rendimiento de las carreras? Deja tus comentarios en nuestras redes sociales: Facebook, Twitter y RSS. Sigue toda la información sobre impresión 3D en nuestra Newsletter semanal.
*Foto de portada: Stratasys