¿Cómo están revolucionando los materiales cerámicos de Lithoz el sector aeroespacial?
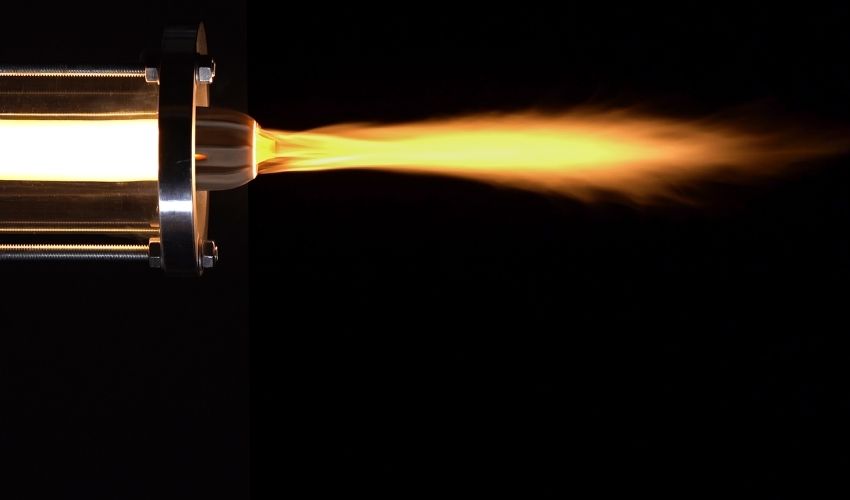
Los futurólogos predicen que el mercado de la impresión 3D cerámica alcanzará los $4.800 millones de cara a 2030. Uno de los sectores que más está adoptando la impresión 3D de cerámica es la industria aeroespacial. Dentro de esté ámbito encontramos a la empresa austriaca Lithoz, que se dedica a la fabricación aditiva cerámica aplicada al sector aeroespacial, entre otros. Lithoz ha conseguido desarrollar un sistema basado en la fabricación de cerámica por litografía (LCM o Lithography-based Ceramic Manufacturing). Esto permite utilizar cada vez más la cerámica para aplicaciones aeroespaciales. Pero, ¿qué posibilidades y ámbitos de aplicación tiene en este caso la impresión 3D de cerámica y los materiales desarrollados para ella? ¿Y cómo contribuyen a mejorar las necesidades de la industria?
Piezas de cerámica impresas en 3D
Más rápido, más sencillo y más barato. Este es el principio que siguen muchas empresas y organizaciones dentro del sector aeroespacial. En casi ningún otro sector los requisitos y las expectativas de las piezas impresas en 3D son tan elevados. Probablemente, los mayores retos a superar son las cargas extremas, así como el calentamiento y el sobrecalentamiento. A menudo, las aspas de las turbinas se mueven a una velocidad tan alta, que el calor generado es mayor que el que se utiliza con el metal en su fabricación. Esto hace que los procesos de fabricación convencionales se lleven al límite. Sin embargo, las piezas no sólo deben ser capaces de soportar el sobrecalentamiento, sino también el frío extremo. Teniendo en cuenta que la temperatura exterior en el espacio puede descender a más de -200°C, surgiendo así otra necesidad. El sector aeroespacial requiere de una alternativa para el proceso de fabricación de sus piezas.
Estas condiciones extremas no deben influir en el rendimiento de las piezas, ya que la estabilidad continua y la porosidad son indispensables en los viajes espaciales. El tamaño de los catalizadores, por ejemplo, también desempeña un papel importante en la fase posterior. Si las piezas son demasiado grandes, pueden sufrir pérdida de calor, pero si son demasiado pequeñas, pueden impedir la descomposición máxima del propulsor. El resultado en ambos casos es un menor rendimiento y mayores costes. Pero, ¿cómo puede la impresión 3D de cerámica solucionar estas cuestiones? La cerámica es especialmente conocida por sus propiedades térmicas, el rendimiento mecánico y también por su uso en la producción de componentes finos de alta calidad. La fabricación aditiva permite diseñar formas complejas reduciendo los costes y los plazos de entrega, algo que no es posible con otros métodos convencionales.
Se puede deducir entonces que la impresión 3D de cerámica es una solución ideal para una industria tan exigente como la aeroespacial. Lithoz se ha posicionado rápidamente en este mercado desarrollando un nitruro de silicio (Si3N4) que destaca por sus óptimas propiedades. Entre ellas, la enorme resistencia a altas temperaturas, capacidad de soportar cambios de temperatura inesperados y una impresionante dureza. Para demostrar estas propiedades y probar el material en condiciones extremas, la empresa austriaca realizó una prueba de resistencia térmica con una boquilla de Si3N4.
El equipo de Lithoz quería probar la resistencia al choque térmico de su material utilizando la boquilla de nitruro de silicio impresa en 3D. Lo calentaron a 900°C y luego lo enfriaron inmediatamente con agua hasta alcanzar la temperatura ambiente. A pesar de los cambios térmicos tan bruscos, la boquilla impresa en 3D pasó la prueba sin daño alguno. Según Lithoz, el material puede soportar incluso una temperatura superior a los 900°C, lo cual lo hace ideal para el sector aeroespacial.
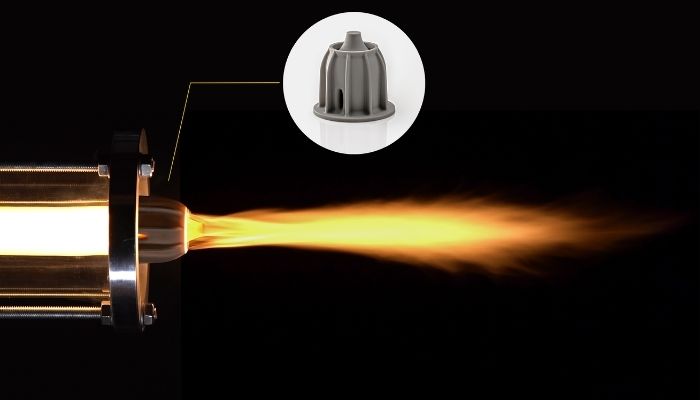
La boquilla fabricada por Lithoz es capaz de soportar las más altas temperaturas. | Créditos: Lithoz GmbH
¿Qué significa esto para la industria aeroespacial? Gracias al nitruro de silicio, las piezas impresas en 3D tienen un gran aguante a cambios térmicos, así como una enorme resistencia, dureza y la ventaja de que se pueden producir componentes cerámicos complejos. Para el sector aeroespacial, esto permite fabricar microturbinas, impulsores y herramientas de corte de forma rápida y precisa. Además pueden ser utilizados a temperaturas de hasta 1200°C, lo que supondría mucho tiempo y sería muy costoso en un proceso de producción tradicional. Asimismo, el Si3N4 también se utiliza en otras industrias. El campo de la medicina, por ejemplo, se beneficia de este material por su química superficial antibacteriana y antiviral, así como por su excelente biocompatibilidad. En concreto, el nitruro de silicio es adecuado para los campos de la odontología, la ortopedia y los implantes craneomaxilofaciales. También puede utilizarse en la lucha contra el coronavirus, ya que sus propiedades de superficie lo hacen resistente a los virus y las bacterias.
Impresión 3D en la luna: ¿realidad o ficción?
Puede parecer algo sacado del guión de una película de ciencia ficción, pero el uso del polvo lunar ya se está utilizando en la impresión 3D de cerámica gracias a Lithoz. La tecnología LCM permite producir componentes aeroespaciales a partir del regolito lunar en dimensiones muy precisas. Para las futuras misiones espaciales, las piezas de repuesto y herramientas necesarias podrían producirse in situ y bajo demanda. Este material se considera un recurso suficientemente disponible y no tóxico para el ser humano. El estrecho trabajo del proyecto con la Agencia Espacial Europea (ESA) permite una investigación continua y un mayor desarrollo del polvo lunar con respecto a la impresión 3D. En el curso del proyecto RHEFORM de Horizonte 2020 de la UE, ya se ha investigado una solución para sustituir la hidracina. La sustancia, considerada cancerígena, ha desempeñado un papel importante en los viajes espaciales desde la década de 1960. Utilizando la impresora 3D CeraFab 7500, una solución DLP (Digital Light Processing) de Lithoz, así como su aglutinante fotocurable de desarrollo propio, los investigadores pudieron lograr un progreso significativo en términos de aplicaciones mejoradas en el sector aeroespacial. Para poder explorar las posibilidades adicionales del polvo lunar, se están llevando a cabo varios proyectos en los que Lithoz participa activamente.
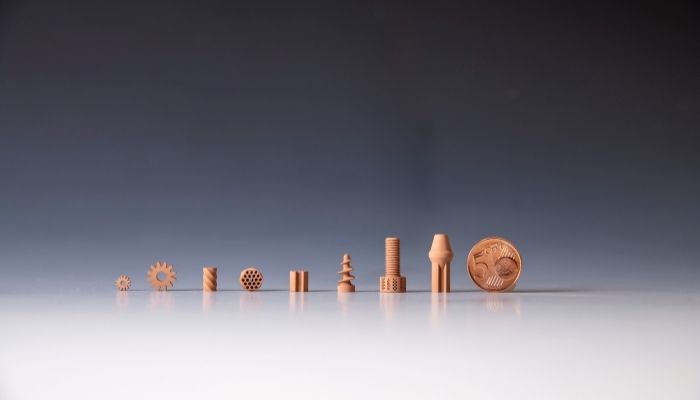
Las piezas impresas en 3D a partir de polvo lunar pueden adoptar diferentes tamaños y formas. | Créditos: Lithoz GmbH
Producción más ligera de turbinas para aviones
Las turbinas son la parte más importante en el despegue de un avión. Una de las piezas más importantes del interior de la turbina son las aspas, que tradicionalmente se fabrican mediante moldeo a la cera perdida. Sin embargo, aquí surge un grave problema. Con los núcleos convencionales creados mediante moldeo por inyección, la posibilidad de incorporar elementos de refrigeración multipala, complejos y estrechos, es limitada. A largo plazo, las consecuencias no sólo pueden ser costosas, sino que también suponen riesgos para la seguridad. Entonces, ¿cómo se pueden fabricar las turbinas de forma más eficiente e innovadora sin aumentar los costes? La solución se encuentra en la LithaCore 450, un material a base de sílice que resulta ideal para la producción de núcleos de fundición mediante tecnología LCM. Debido a su baja expansión térmica y a su gran porosidad, el material es ideal para la fabricación aditiva de núcleos cerámicos para aplicaciones aeroespaciales.
Este método de fabricación no sólo evita los altos costes y el esfuerzo adicional, sino que la tecnología LCM también permite una producción más rápida. De este modo, tanto los prototipos como las producciones en serie pueden realizarse en poco tiempo y, por lo tanto, el plazo de comercialización es más corto. Los núcleos de fundición pueden tener una delgadez de al menos 200 µm y pueden adoptar un tamaño de hasta 30 cm, incluso para formas complejas con características como los bordes de salida. Con el sistema CeraFab propio de la empresa, Lithoz pudo incluso producir varios núcleos de fundición con un tamaño de 500 mm, algo que no se había hecho antes de esta forma y que demuestra las soluciones de futuro para la producción aeroespacial. Desde prototipos hasta núcleos grandes para turbinas industriales por parte de Lithoz.
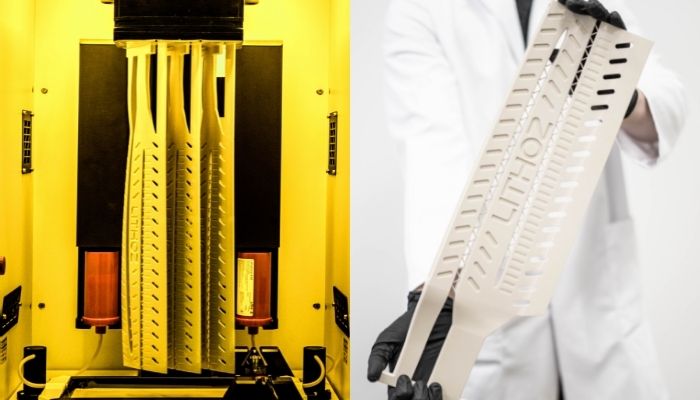
Núcleos cerámicos impresos en el CeraFab S230 con LithaCore 450 para turbinas de gas industriales. | Créditos: Lithoz GmbH
Los nuevos materiales desarrollados por Lithoz
Lithoz ha añadido dos materiales más a su gama de soluciones cerámicas. En primer lugar, el carburo de silicio infiltrado (SiSiC), un material cerámico ligero pero duro, que ofrece una muy excelente conductividad de la temperatura y una mínima expansión térmica. Por ello, las cerámicas de SiSiC se utilizan a menudo como intercambiadores de calor, boquillas o piezas finales para diferentes tipos de quemadores. Por otro lado, está el nitruro de aluminio (AIN), que se utiliza con la tecnología DLP. Al igual que el SiSiC, el nitruro de aluminio tiene una alta conductividad térmica. Por otro lado, la resistencia a la flexión del AIN, que pudo medirse en las muestras de la investigación, varió entre 320 y 498 MPa. En conjunto, estas propiedades contribuyen a que sea posible la producción de piezas muy complejas y sin grietas, creando así nuevas posibilidades de aplicación en el campo de la gestión térmica.
Esta amplia y diversa gama de materiales y desarrollos diferentes ilustra claramente hasta qué punto ha avanzado la impresión 3D de cerámica en el sector aeroespacial y qué nuevas posibilidades abren las soluciones de Lithoz. Además de la producción de componentes con estructuras complejas, la empresa también permite una gran libertad de diseño y precisión con sus nuevos materiales. Independientemente de si la pieza debe tener diferentes tamaños, existe una calidad del material de primera clase y una precisión de exposición constante y de píxeles. Esto se consigue al utilizar un sistema CeraFab de forma uniforme en toda la plataforma de construcción, lo cual hace que la producción de piezas para la fabricación en serie deje de ser un problema.
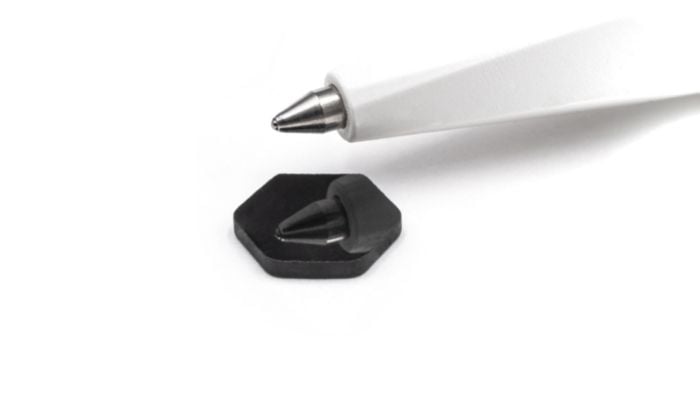
El carburo de silicio permite formas y tamaños inimaginables. | Créditos: Lithoz GmbH
¿Qué proyectos está desarrollando Lithoz en el sector aeroespacial?
Diversos proyectos en los que Lithoz participa de forma sustancial, intensifican aún más este aspecto. Junto con investigadores de la Universidad de Poitiers (Francia), FOTEC Forschungs- und Technologietransfer GmbH (Austria) y la Universidad de Ciencias Aplicadas Wiener Neustadt GmbH (Austria), Lithoz ha presentado la comparación de catalizadores cerámicos monolíticos impresos en 3D con catalizadores convencionales, así como con diferentes capas de lavado. Con respecto a la descomposición del peróxido de hidrógeno altamente concentrado, se pudo determinar que el factor de la porosidad marca una gran diferencia en la comparación directa. En general, la porosidad medida de la estructura impresa es inmensamente mayor que la de la estructura extruida. Una de las consecuencias de esto es que el comportamiento de la temperatura transitoria también mejora con una mayor porosidad. Estos resultados pueden suponer un paso decisivo para aumentar el uso de la impresión 3D de cerámica en el sector aeroespacial. Puedes obtener más información sobre los proyectos de Lithoz en este enlace.
¿Qué piensas de los materiales de Lithoz y su papel en el sector aeroespacial? Deja tus comentarios en nuestras redes sociales: Facebook, Twitter, Youtube y RSS. Sigue toda la información sobre impresión 3D en nuestra Newsletter semanal.
*Créditos foto de portada: Lithoz GmbH