Knust-Godwin utiliza la tecnología de VELO3D para fabricar piezas de metal sin soportes
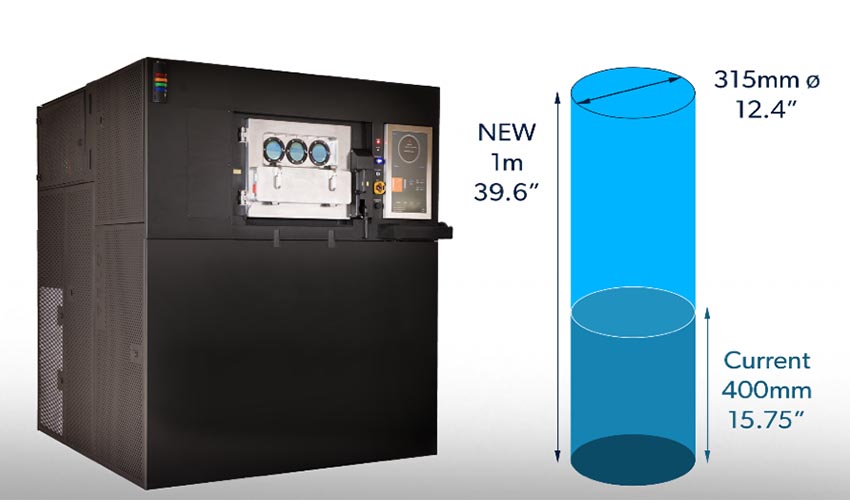
Ha sido una primera mitad del año bastante ocupada para VELO3D: la compañía lanzó una nueva impresora 3D de metal y recaudó $ 28 millones en una ronda de financiación de la Serie D. Hace unos días, también reveló que había recaudado $ 12 millones adicionales de nuevos inversionistas estratégicos, llevando el financiamiento total a $ 150 millones. Durante el lanzamiento, la compañía reveló que su sistema de fabricación aditiva metálica de próxima generación se desarrolló con un enfoque en el tamaño de la cámara de construcción. Según el fabricante, el eje vertical de 1 metro de la impresora 3D lo convierte en el sistema de fusión de lecho de polvo metálico más alto del mundo con cámara cerrada. VELO3D también anunció que su primer cliente será Knust-Godwin, un taller establecido de mecanizado de precisión que busca expandirse a nuevas industrias y ha reconocido el tremendo potencial de la impresión 3D industrial de metales. La compañía debería comenzar a enviar su nuevo sistema en el cuarto trimestre de 2020.
El sistema Sapphire de VELO3D se basa en su tecnología patentada para construir piezas de metal sin estructuras de soporte. Estas estructuras agregan considerables limitaciones de diseño y fabricación y son comunes en muchas tecnologías de impresión 3D de metal, incluida la fusión láser de lecho de polvo. La capacidad de crear piezas metálicas sin estas restricciones es uno de los principales beneficios del sistema de VELO3D. Mike Corliss, vicepresidente de tecnología de Knust-Godwin, y Zach Murphree, vicepresidente de asociaciones técnicas de VELO3D, están trabajando juntos para llevar el sistema Sapphire al conjunto de procesos de fabricación de alta gama de Knust-Godwin con el fin de aprovechar los beneficios de la impresión 3D.
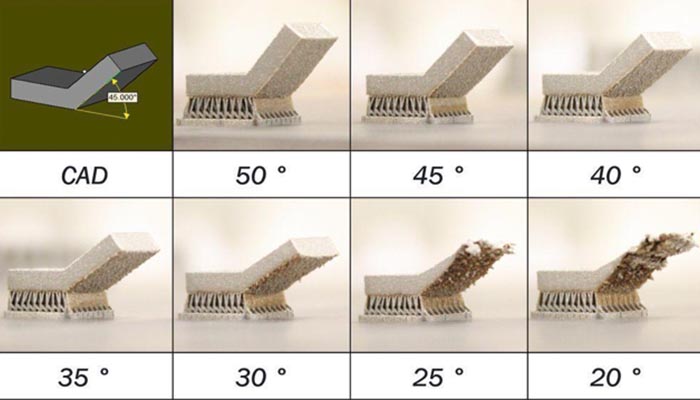
Las estructuras de soporte siempre han sido un requisito para evitar la deformación. El proceso sin soporte de VELO3D permite imprimir ángulos bajos sin fallos en las piezas | Créditos: Protolabs
¿Qué ventajas tiene invertir en fabricación aditiva de metal?
Aunque lo más probable es que la fabricación sustractiva siempre juegue un papel importante en la producción, la aditiva también tiene un papel clave. En los últimos 8 años, Knust-Godwin ha estado invirtiendo en impresión 3D de metal, aunque todavía depende principalmente de métodos sustractivos para fabricar sus productos. El taller de mecanizado de precisión se dio cuenta desde el principio de que podía aplicar la fabricación aditiva a muchas de las piezas que produce. Mike Corliss explica: “Estamos seguros de que ayudará a reducir el tiempo de la máquina, el tiempo de cola e incluso ayudará a reducir las restricciones con la geometría, tanto el peso de la pieza como su tamaño, en algunas áreas”.
Esto se debe a que la fabricación aditiva de metal ofrece un gran potencial para productos complejos, haciendo que los componentes sean más pequeños, más ligeros, más duraderos, más funcionales, más confiables y menos costosos. En el caso de Knust-Godwin, la compañía es conocida por el mecanizado de precisión en la gama alta de aplicaciones de la industria aeroespacial y de petróleo y gas. Mike Corliss agrega: “Con el mecanizado, abordamos esas piezas de una manera muy lineal. Sin embargo, con la impresión 3D, podemos cambiar esa geometría interna, aprovecharla, condensar la pieza y luego crearla con un solo proceso de fabricación. La longitud total de la pieza puede cambiar para mejor. La parte puede tumbarse porque puede aprovechar parte de la geometría y de algunas de las características internas. Y es posible que pueda organizar más funciones alrededor de la pieza en diferentes orientaciones”.
Además, poder trabajar con materiales como inconel, titanio, súper aleaciones de níquel es un gran beneficio para aplicaciones industriales. Estos materiales ofrecen resistencia a la corrosión y la capacidad de funcionar a altas temperaturas. Zach Murphree explica: “Si estás buscando tecnologías de compresión, compresión de gas industrial o válvulas para aplicaciones de cabezales, estos son todos los lugares donde deseas utilizar aleaciones de alto rendimiento y resistentes a la corrosión. Inconel es una muy buena opción en ese sentido”.
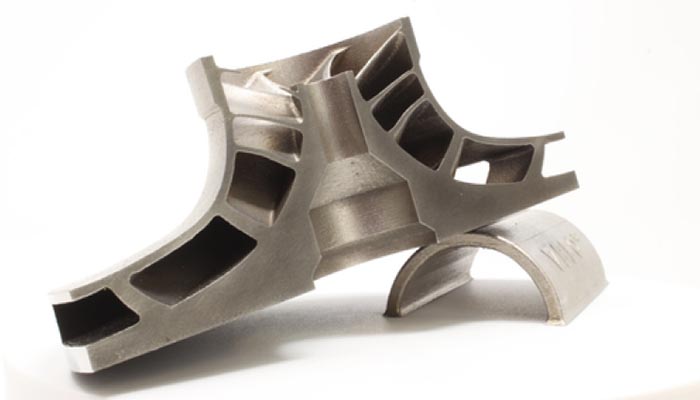
Un impulsor que muestra ángulos ultra bajos de 0 grados, lo cual es muy difícil de lograr con el sistema de fusión láser de lecho de polvo | Créditos: VELO3D
¿Cuáles son los beneficios de la tecnología de VELO3D?
Como ya sabrás, el diferenciador clave para VELO3D es sus capacidades sin soporte y su impacto en el procesamiento de piezas. Los sistemas de lecho de polvo existentes a menudo requieren soportes para cualquier superficie por debajo de 45 grados. Por otro lado, la impresora Sapphire 3D puede imprimir ángulos bajos y voladizos de hasta cero grados horizontalmente, así como diámetros grandes y pasadizos internos de hasta 100 mm sin necesidad de soportes. Como resultado, los pasos de procesamiento se reducen enormemente y se permite una mayor libertad al diseñar y construir componentes complejos para una variedad de industrias.
Por ejemplo, “Con la impresión 3D sin soporte, se optimiza el flujo de fluidos y gases a través de un componente. Ya sea que tenga un impulsor cubierto o una sección del difusor, o una herramienta hidraulica con cable, la estructura sin soporte de esas áreas de paso de fluido ofrece una gran ventaja”, explica Zach Murphree. En Knust-Godwin, Mike Corliss explica que el procesamiento siempre lleva mucho tiempo y es costoso. “Prefiero utilizar la tecnología de lecho de polvo láser, imprimir el producto a la forma casi completa, reducir la mayor cantidad de posprocesamiento posible, y luego hacer el tratamiento por calor y por hipping. Además, con muchos menos apoyos con los que lidiar gracias a la tecnología VELO3D, el proceso se simplifica. Podemos construir un mejor producto más rápido y a un coste final más bajo”.
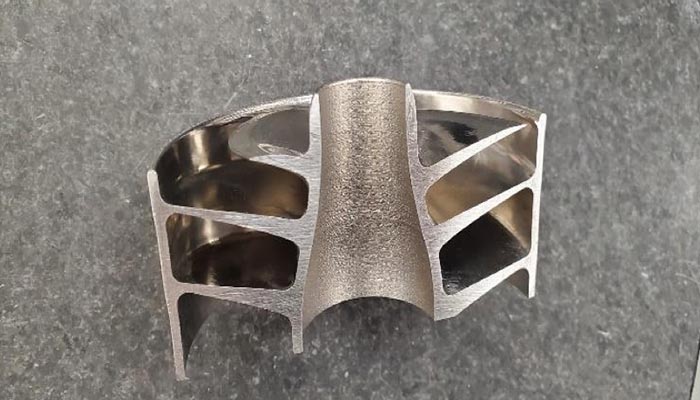
Sección transversal de un inductor de bomba de CO2 de misión crítica, impreso en 3D. Estos se producen típicamente a través de la fabricación sustractiva. Imprimirlos sin estructuras de soporte será un gran facilitador y un ahorro de costos en el futuro | Créditos: Barber-Nichols
¿Por qué aumentar la altura pero no el volumen de construcción de Sapphire?
El sistema Sapphire de última generación de VELO3D tiene una altura z aumentada. ¿Por qué? Zach Murphree, vicepresidente de asociaciones técnicas de VELO3D explica: “Hay varias aplicaciones diferentes en las que sería beneficioso tener un sistema más alto, incluso si no se cambia el ancho o el diámetro. Existen algunas aplicaciones obvias en la industria aeroespacial y otras industrias donde los componentes más altos y de forma tubular serían claramente beneficiosos. Puedes hacer algunas cosas realmente sorprendentes en relación con el peso ligero, la rigidez y la reducción parcial cuando aumentas la altura”. Esto es especialmente cierto para los ensambles que están hechos de varios componentes.
Finalmente, otra razón para aumentar la altura z sin cambiar el diámetro del volumen de construcción es que se pueden mantener recetas de proceso idénticas en las dos configuraciones de máquina. Por lo general, cuando los sistemas cambian de tamaño o de número de láseres, el cliente debe volver a calificar el nuevo sistema y las nuevas recetas de proceso.
Zach Murphree concluye: “No podemos estar más felices de que una empresa como Knust-Godwin se haya convertido casi en un pionero de nuestra tecnología. Estamos ansiosos por hacer grandes cosas con ellos este otoño y luego expandirnos a nuevos mercados y nuevas industrias muy rápidamente después de eso”. Puedes obtener más información sobre el sistema de próxima generación de VELO3D en su sitio web oficial, aquí.
¿Qué piensas de la tecnología de impresión 3D «Sapphire» desarrollada por VELO3D? Deja tus comentarios en nuestras redes sociales: Facebook, Twitter, Youtube y RSS. Sigue toda la información sobre impresión 3D en nuestra Newsletter semanal.