Las impresoras 3D de composites que podemos encontrar en el mercado actual
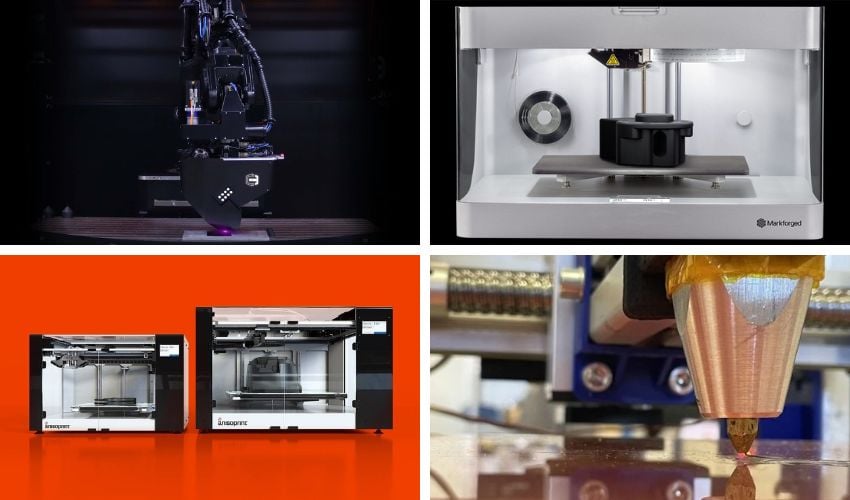
En el sector de la impresión 3D, los fabricantes buscan cada vez más materiales compuestos porque ofrecen propiedades mecánicas más interesantes, particularmente en términos de resistencia. El material en cuestión llamado «matriz» (a menudo un termoplástico) incluye fibras (carbono, aramida, vidrio) que aumentan la solidez de la pieza final, reducen su peso total o incluso reemplazan el uso de metal. Hoy en día, la mayoría de las impresoras 3D FDM de escritorio pueden imprimir composites siempre que tengan una boquilla de acero endurecido. Sin embargo, estas máquinas no permiten que las fibras se depositen directamente en el material de la matriz durante la impresión. Es por eso que varios fabricantes han desarrollado soluciones capaces de extruir tanto la matriz como las fibras para obtener piezas aún más resistentes. Por lo tanto, hemos seleccionado algunas impresoras 3D de composites basadas en diferentes tecnologías, capaces de mezclar dos materiales durante la impresión.
9T Labs y su solución Red Series
Fundada en 2018, 9T Labs es un fabricante suizo especializado en la impresión 3D de composites. Su proceso, Additive Fusion Technology, permite depositar fibras de carbono continuas en una matriz de polímero de forma automatizada y controlada. Esto se consigue mediante la Red Series, que comprende la unidad de impresión, el Build Module y la máquina de postprocesado Fusion Module. La impresora 3D de composites es capaz de colocar fibras continuas según la orientación y las trayectorias elegidas por el usuario durante la fase de diseño y preparación del archivo 3D. Esto optimiza el peso y el coste de la pieza y garantiza una resistencia óptima. Si determinadas partes de la pieza no necesitan fibras continuas, la impresora 3D las rellena con un polímero convencional o incluso con un plástico reforzado con fibras cortas. La máquina está equipada con varios sensores para supervisar todo el proceso de impresión. Además, cuenta con un sistema de gestión de la temperatura para minimizar la acumulación de humedad y garantizar una buena adherencia entre las capas.
Por último, la Fusion Module, esta máquina permite el moldeo por compresión para lograr un mejor rendimiento en términos de acabado superficial, consolidación y calidad de la pieza. Para saber más sobre el proceso de fabricación de 9T Labs, vea el vídeo a continuación:
Anisoprint
Cuando se piensa en soluciones completas de impresión 3D de fibra continua, tanto de sobremesa como industriales, Anisoprint es inevitablemente una de las principales empresas que nos vienen a la mente. Dirigida por Fedor Antonov y con sede actual en Singapur, el fabricante se ha dedicado a «introducir una nueva tecnología de fabricación industrial de demanda mundial para estructuras optimizadas hechas de materiales compuestos». Para ello, Anisoprint utiliza su tecnología patentada de coextrusión de fibras compuestas (CFC), que añade fibras continuas a un termoplástico base que incluye PLA, ABS, PETG y naylon, entre otros. Con sus impresoras 3D de sobremesa, la A3 (460 x 297 x 210 mm de volumen de construcción) y la A4 (287 x 210 x 140 mm de volumen de construcción), es posible trabajar con composites de hasta 900 MPa.
Por su parte, la PROM IS 500 es la solución industrial de la empresa y es compatible con plásticos de alta temperatura (hasta 410 °C) como PEEK y PEI con un volumen de construcción de 600 x 420 x 300 mm. Lo que también hace destacar al fabricante es el hecho de que los usuarios pueden modificar la densidad del relleno del composite o variar la dirección de las fibras para obtener piezas óptimas, lo que Anisoprint denomina «anisoprinting».
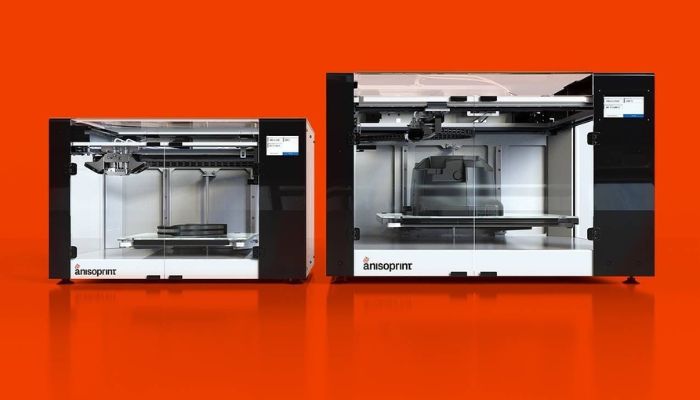
Las dos soluciones de sobremesa de Anisoprint, la A4 (izquierda) y la A3 (derecha). (Créditos: Anisoprint)
Continuous Composites
Fundada en 2015, Continuous Composites es una empresa que promueve el desarrollo de tecnologías innovadoras para la industria. Con el objetivo de resolver ciertos problemas de velocidades lentas, materiales débiles y pequeños volúmenes de fabricación, crearon la solución CF3D®. Este proceso de fabricación automatizado comienza con una fibra continua seca que se impregna con una resina termoendurecible de curado rápido, que es depositada por el efector final. El método elimina la necesidad de utilizar moldes, hornos y autoclaves, proporcionando un alto rendimiento al material, a un coste más bajo. La utilización de materiales compuestos ligeros proporcionan a la fabricación aditiva un alto nivel de rendimiento y funcionalidad. Además, la tecnología CF3D® está alcanzando la capacidad de imprimir fibras estructurales y funcionales en procesos de un único paso.
Impossible Objects
La empresa estadounidense Impossible Objects ha desarrollado CBAM 25, una tecnología de impresión 3D especialmente diseñada para materiales compuestos. La solución está optimizada para trabajar con materiales como la fibra de carbono y la fibra de vidrio, combinados con polímeros de alto rendimiento como el nylon y el PEEK. Diseñada para satisfacer las exigentes necesidades de los entornos industriales, la impresora 3D de composites CBAM 25 pretende transformar la fabricación aditiva ofreciendo un alto rendimiento en términos de velocidad y precisión. Esta tecnología es capaz de imprimir cada capa en menos de 4 segundos, lo que le permite producir piezas hasta 15 veces más rápido que las soluciones competidoras del mercado.
Markforged
El fabricante Markforged utiliza la tecnología CFF (Continuous Filament Fabrication) para extrudir fibra continua capa por capa. Para ello, Markforged ofrece 4 tipos de refuerzo: fibra de carbono, fibra de vidrio, Kevlar y fibra de vidrio HSHT. Los materiales compuestos son compatibles con varias de las impresoras 3D de Markforged, incluida la serie Desktop (Onyx Pro y Mark Two), que combina calidad industrial y asequibilidad, y la serie Industrial (X7, FX10, FX20) para piezas robustas y fiables incluso en materiales de gran tamaño y alto rendimiento.

Créditos: Markforged
Moi Composites y su tecnología CFM
Moi Composites es una spin-off del Politécnico de Milán creada en 2018 que propone su tecnología patentada, Continuous Fiber Manufacturing (CFM). Se trata de un método de impresión 3D que, como su nombre lo indica, utiliza materiales compuestos de fibra continua. A diferencia de las otras soluciones de esta lista, CFM consiste en un cabezal de impresión que se puede integrar en cualquier máquina CNC de más de 4 ejes. El cabezal puede trabajar con materiales compuestos con fibras de carbono, aramidas, vidrio, materiales de origen bio/natural, etc.
Por otra parte, la empresa cuenta con un software personalizado que ayuda a optimizar tanto el diseño como la producción a través de algoritmos generativos inteligentes. El programa gestiona máquinas robóticas, controla la calidad de impresión y calcula la trayectoria de todo el proceso, desde el diseño CAD hasta la impresión 3D. Las aplicaciones de la tecnología CFM son amplias. La empresa recomienda su solución para crear productos que necesitan altas prestaciones mecánicas, que sean duraderos y funcionales. Como ejemplos, los sectores que más le pueden sacar provecho son el de la energía, el aeroespacial, la construcción, el de los deportes y el marítimo.

Créditos: Moi Composites
Curado térmico por láser de SphereCube
SphereCube es una empresa italiana dedicada a la producción de componentes compuestos de alto rendimiento. La empresa no utiliza moldes y trabaja para reducir el impacto ambiental. Su tecnología, Thermal Laser Curing, les permite crear piezas de composites de alto rendimiento con refuerzo de fibra continua y matriz termoestable, gracias al cabezal de extrusión y al sistema de 5 ejes de su impresora 3D. La impresora extruye los dos materiales en dos estados físicos diferentes. La matriz polimérica en estado fluido viscoso y el material de refuerzo en forma de fibra continua.
Una vez la impresión termina, se utiliza una fuente de calor para curar parcial o totalmente el material compuesto. Normalmente, se utiliza una fuente UV para la solidificación de estos materiales compuestos. El curado térmico por láser también permite procesar diferentes tipos de matrices termoestables y utilizar cualquier tipo de fibras continuas de refuerzo. Estas también pueden ser de origen natural y vegetal, como el lino y el cáñamo. Además, SphereCube ha patentado su propio método de preparación de la fibra de refuerzo, mediante una máquina aglutinadora. Gracias a su brillante trabajo, SphereCube fue seleccionada como una de las ganadoras del Formnext Startup Challenge 2022.
¿Qué opinas de las impresoras 3D de composites? Deja tus comentarios en nuestras redes sociales: Facebook, LinkedIn y Youtube. Sigue toda la información sobre impresión 3D en nuestra Newsletter semanal.
[…] En los Países Bajos, la fabricación aditiva ha vuelto a demostrar su valía dentro del sector de la construcción. El servicio de impresión Royal3D ha creado una especie de refugio para un espacio de trabajo modular impreso en 3D. Y esta vez, no se utilizó hormigón tradicional, sino PET, el conocido plástico mediante el cual se fabrican las botellas de agua y envases de alimentos. Se dice que este refugio, llamado R-IGLO, fue diseñado en la máquina CFAM Prime del fabricante CEAD, especialista en impresión 3D de composites. […]
Buenos días, se podría fabricar un guardamanos de un rifle browing modelo long track composite con una impresora 3 D de composites, gracias, un saludo.