Impresión 3D y producción en masa: ¿en dónde nos encontramos?
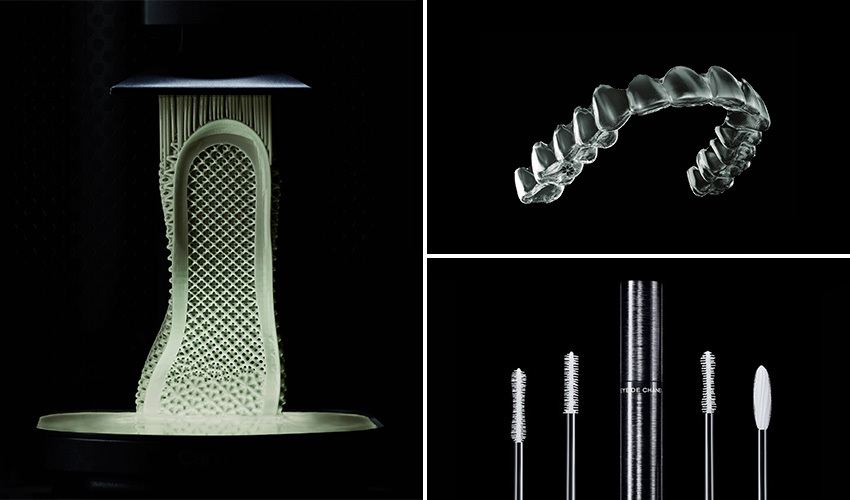
La impresión 3D ha dejado de ser exclusivamente usada en el desarrollo de prototipos para abrirse camino en la producción de piezas finales. Aunque en ocasiones se ha cuestionado su viabilidad en la fabricación a gran escala debido a los costes y tiempos de producción, esta percepción está cambiando. Cada vez más empresas están demostrando que es posible combinar calidad, personalización y eficiencia en la producción de grandes cantidades. Desde componentes industriales hasta artículos personalizados, la impresión 3D está ganando terreno como una solución real para la producción en masa. Por ello, hemos explorado algunos casos concretos donde la fabricación aditiva ha sido clave para crear miles de piezas en serie, demostrando su potencial y desafiando los métodos tradicionales de producción.
Adidas y Carbon fabrican miles de zapatillas para correr
En 2016, Adidas se asoció con Carbon para revolucionar la forma de fabricar zapatillas de running. En 2017, las dos empresas lanzaron Futurecraft 4D, una entresuela «multizona» hecha en una sola impresión y con una innovadora estructura de malla. Juntas, lanzaron la producción de 100 000 pares de zapatillas Futurecraft 4D con entresuelas impresas en 3D. A Futurecraft 4D le siguió AlphaEDGE en 2018, a la que se añadieron grosores respecto al modelo anterior justo debajo del talón, el punto donde el corredor ejerce más presión durante la carrera. En 2021 se lanzó la Adidas 4DFWD, la tercera generación de la entresuela 4D, que explota la propiedad física de la anisotropía para hacer que la zapatilla sea cómoda y funcional para correr. También fruto de la colaboración entre Adidas y Carbon, la nueva entresuela está fabricada con el proceso Carbon DLS™ y utiliza el elastómero EPU 44, una versión actualizada del anterior EPU 41 utilizado en las Futurecraft 4D. Este material de nueva generación es muy elástico, resistente al desgarro y más sostenible, gracias a una formulación con un 40% de base biológica. Adidas 4DFWD es la última evolución de la marca, que combina innovación tecnológica, diseño avanzado y sostenibilidad a escala industrial.
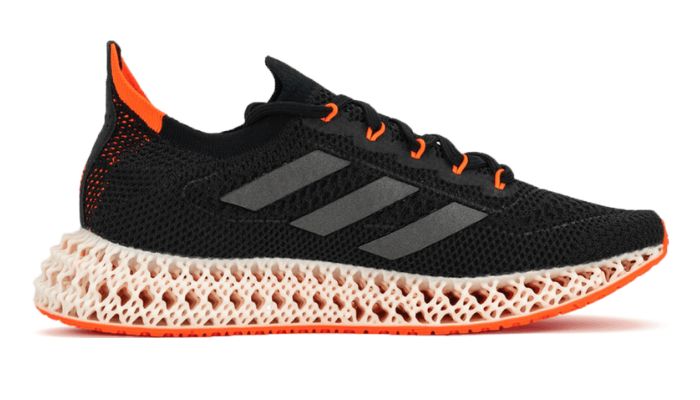
Créditos de la foto: Carbon
Align Technologies utiliza la impresión 3D para la producción en masa de dispositivos dentales
Cuando hablamos de producción en masa con impresión 3D, Align Technologies es un ejemplo destacado. La empresa estadounidense es especialista en soluciones de ortodoncia realizadas mediante la impresión 3D y es inventora de Invisaling. De hecho, siempre ha sido una firme partidaria tanto de la impresión 3D como del escaneo 3D. Prueba de ello es la adquisición del fabricante de escáneres 3D intraorales iTero en 2011 y del fabricante de impresoras 3D de polímeros Cubicure en 2024. Además, ha sido socia de 3D Systems desde hace mucho tiempo. Align Technology utiliza la impresión 3D para todo, desde moldes para sus alineadores estrella hasta expansores palatinos, el primer dispositivo de ortodoncia impreso en 3D del fabricante. La producción de la empresa no es para nada desdeñable considerando que fabrica hasta un millón de piezas únicas de alineadores al día, utilizando la impresión 3D para cientos de miles de moldes de alineadores. Un ejemplo perfecto de cómo combinar personalización, producción en masa e impresión 3D.
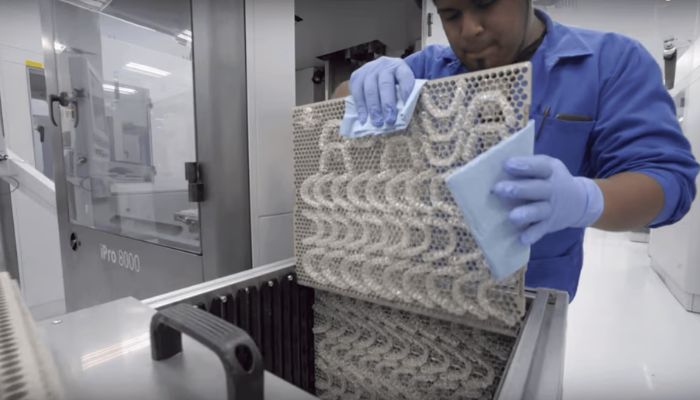
Créditos de la foto: Align Technology
Chanel desarrolla brochas para su rímel
Seguro recordarás la máscara de pestañas Volume Révolution de Chanel. Lanzada en 2018, tiene la particularidad de incorporar una brocha impresa en 3D. El proyecto causó bastante revuelo en su momento porque se trataba de una auténtica producción en serie. Erpro 3D Factory, la start-up responsable de la impresión de los cepillos, afirmó que podía producir 250 000 cepillos a la semana utilizando unas 15 máquinas. Desde entonces, las dos marcas han lanzado E.Y.E, un servicio de máscaras de pestañas impresas en 3D a medida. Mediante una aplicación en tableta, las usuarias pueden elegir entre 10 cepillos diferentes para el rímel, en función de sus necesidades y preferencias de maquillaje. A continuación, el cepillo se imprime en 3D con PA11. No sabemos exactamente cuántos cepillos se han impreso en 3D hasta la fecha, pero lo cierto es que este ejemplo muestra claramente todas las ventajas de la fabricación aditiva y que es posible combinar la personalización y la producción en serie.
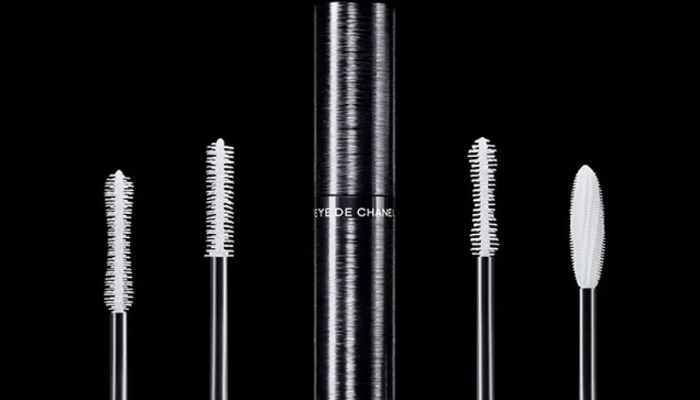
Créditos de la foto: ERPRO/Chanel
General Electric Aviation impulsa la producción en serie en la industria aeronáutica
GE Aviation ha logrado varios hitos en la fabricación aditiva. La planta de GE Aviation en Asheville (Carolina del Norte) ha producido a lo largo de los años más de 100 000 componentes de turbinas fabricados con materiales compuestos de matriz cerámica (CMC), mientras que la planta de Auburn (Alabama) ha producido más de 100 000 componentes de toberas fabricados mediante procesos aditivos. El CMC es un material avanzado que contiene fibras de carburo de silicio. Este pesa un tercio de lo que pesan las aleaciones metálicas tradicionales y soporta el doble de temperatura. Características que ayudan a mejorar la eficiencia térmica de los motores, reduciendo así el consumo de combustible y las emisiones de carbono.
La planta de Asheville fue el primer centro de fabricación aditiva de la industria aeronáutica para componentes de motores a reacción hechos con CMC, se inauguró en 2014. La planta de Auburn comenzó a producir boquillas de combustible en 2015 y fue el primer sitio de producción en masa de la industria para componentes de motores de aeronaves utilizando la fabricación aditiva. </span>
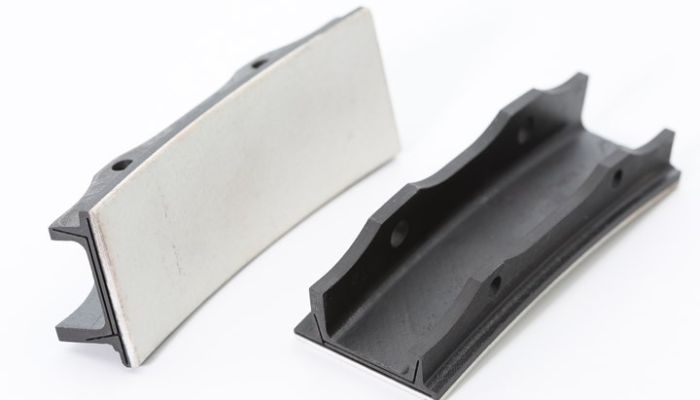
Componentes de turbina impresos en 3D en CMC (Créditos de la foto: GE Aviation.
Photocentric imprime en 3D insignias para Badgemaster
Otro ejemplo del uso de la impresión 3D para la producción en masa es la colaboración entre la empresa británica Badgemaster y el fabricante de impresoras 3D Photocentric. Ante la necesidad urgente de fabricar insignias personalizadas en un plazo reducido, Badgemaster recurrió a la tecnología de impresión 3D con resina de Photocentric, utilizando sus máquinas LC Magna. Este método permitió producir 30.000 piezas finales con rapidez y calidad, sin necesidad de moldes o herramientas tradicionales. La elección de esta tecnología se debió en parte a los desafíos logísticos derivados de la pandemia, que limitaron la producción convencional. Esta colaboración resalta el potencial de la fabricación aditiva para responder a exigencias industriales, ofreciendo soluciones rápidas, flexibles y eficientes, incluso en escenarios de alta demanda.
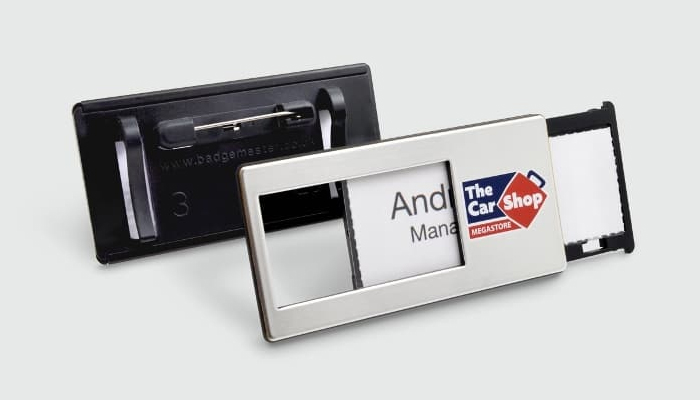
ht=»400″ /> Créditos de la foto: Badgemaster
Cobra transforma el mundo del golf con la impresión 3D de metal
La empresa ha presentado el primer putter fabricado en serie con la tecnología HP Metal Jet, que inaugura una nueva era en el equipamiento de golf. El objetivo de la empresa es combinar innovación y producción a gran escala manteniendo los costes bajo control. Desde hace varios años, Cobra Golf explora las posibilidades que ofrece la fabricación aditiva para diseñar palos con un mayor rendimiento. Gracias a la tecnología HP Metal Jet, sus ingenieros disfrutan de una libertad de diseño sin precedentes, que les permite imaginar estructuras imposibles de producir con métodos tradicionales. La impresión 3D de metal, antes limitada a prototipos, está alcanzando ahora la calidad y velocidad suficientes para la producción a gran escala. En colaboración con HP, Cobra ha podido acelerar el desarrollo de sus palos de golf y hacerlos accesibles al gran público.
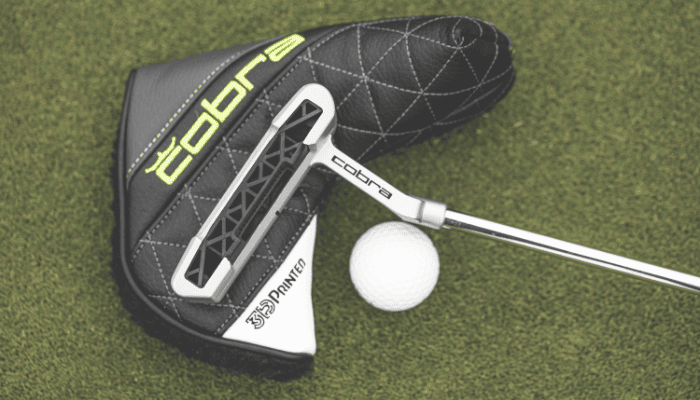
Créditos de la foto: HP
Los implantes de Stryker
Otra iniciativa que combina la fabricación aditiva y en masa nos viene del sector médico. Desde 2013, la empresa irlandesa Stryker ha mejorado su producción fabricando alrededor de 2 millones de prótesis mediante tecnologías de impresión 3D. Para ello, ha desarrollado un material propio llamado Tritanium. Este es una aleación de titanio diseñada específicamente para la impresión. Con ella la empresa ha producido tanto una prótesis de rodilla no cementada, llamada Triathlon Tritanium, como tres prótesis de columna vertebral Tritanium diferentes.
Pero, ¿cómo funciona el sistema Triathlon Tritanium? Esta prótesis combina un diseño avanzado con una tecnología de fijación biológica altamente porosa, diseñada con las herramientas SOMA y fabricada con la tecnología aditiva propia de Stryker. Analizando el ciclo de vida de la prótesis de rodilla, la empresa ha puesto de manifiesto las numerosas ventajas de utilizar la fabricación aditiva. Destaca ventajas tanto en términos económicos como de ahorro de recursos materiales y medioambientales. Pero la cosa no acaba ahí. Stryker se ha unido a la Additive Green Manufacturing Trade Association, con el objetivo de promover el uso de la impresión 3D en la industria para adoptar opciones de fabricación cada vez más sostenibles.
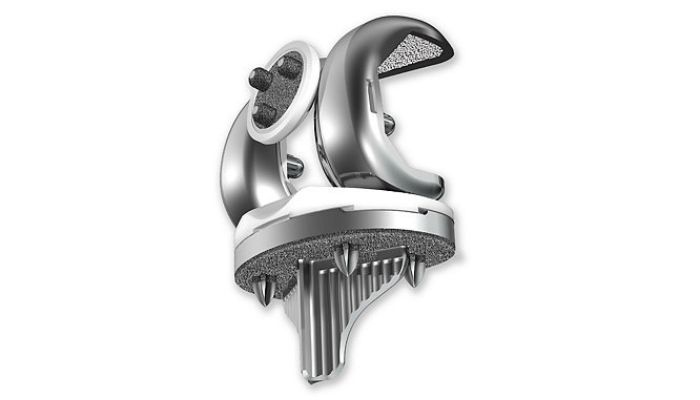
En la imagen, el modelo Triathlon Tritanium, la prótesis de rodilla no cementada.
Manguitos aislantes de Bosch Advanced Ceramics
No es ningún secreto que las cerámicas se han convertido en protagonistas dentro de la industria de la fabricación aditiva. Bosch Advanced Ceramics ha logrado sacar provecho de este material y la impresión 3D al escalar la producción de componentes médicos de alta precisión. Se trata de manguitos aislantes, un componente de los instrumentos laparoscópicos que se utilizan en cirugías invasivas. Tras una fase de muestreo exitosa, la empresa fue capaz de imprimir 1400 componentes en un solo lote. Este nivel le permitiría cumplir con una demanda anual de hasta 20 000 unidades. El desarrollo de esos manguitos aislantes fue todo un reto debido a sus dimensiones reducidas, un diámetro externo de apenas 1,3 mm y un grosor de pared de 90 micras. Para alcanzar este nivel de detalle, Bosch Advanced Ceramics utilizó la tecnología LCM (DLP) de Lithoz. Tecnología basada en un proceso de fotopolimerización capa por capa que permite fabricar geometrías complejas con un alto control de calidad y precisión.
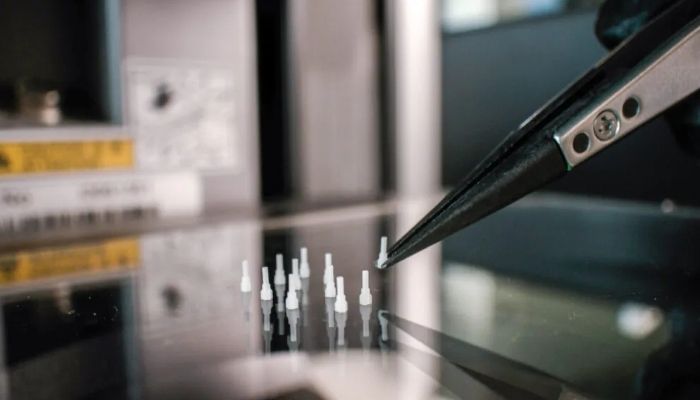
Componentes cerámicos impresos en 3D listos para su uso en instrumentos laparoscópicos. (Créditos de la foto: Lithoz)
¿Qué piensas de la combinación de impresión 3D con producción en masa? Deja tus comentarios en nuestras redes sociales: Facebook, LinkedIn y Youtube. Sigue toda la información sobre impresión 3D en nuestra Newsletter semanal.