Las aplicaciones más destacadas de la impresión 3D en la aeronáutica
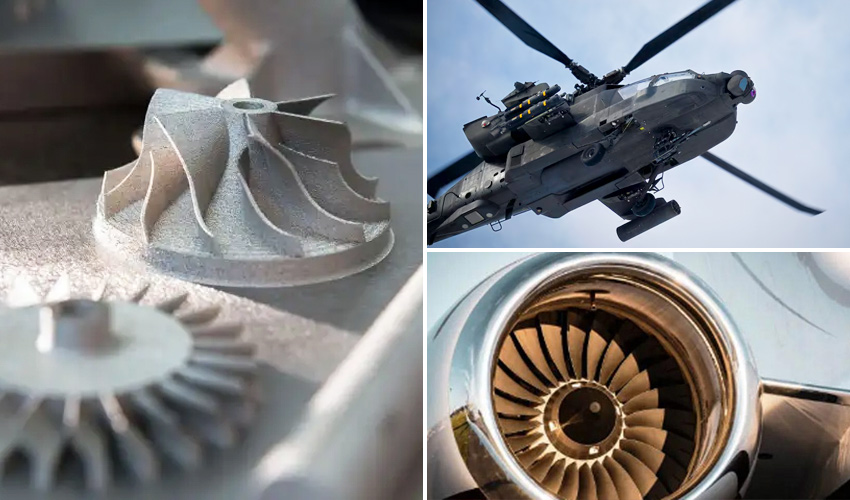
La fabricación aditiva es una opción ideal para producir piezas ligeras, resistentes y geométricamente complejas. Se trata de una tecnología especialmente valiosa en el sector aeronáutico, donde la optimización de la resistencia y el peso son fundamentales. La aeronáutica es la ciencia y la práctica del diseño, la construcción y el pilotaje de todas las aeronaves, excepto las que viajan al espacio. Este sector fue uno de los primeros en adoptar la fabricación aditiva, utilizándola inicialmente para el prototipado. Hoy, sin embargo, sus aplicaciones se han ampliado para incluir piezas de uso final en aviones, helicópteros, drones y más. Para mostrar la versatilidad de la impresión 3D hemos recopilado una lista de algunas de sus aplicaciones más destacadas en la aeronáutica.
Safran y su campus de impresión 3D para la aeronáutica
Safran es un grupo internacional de alta tecnología que opera en los sectores aeroespacial, aeronáutico y de defensa. Ha invertido la suma de 80 millones de euros para abrir un campus dedicado a la fabricación aditiva en Le Haillan, cerca de Burdeos. El objetivo era crear un gran centro de excelencia para la fabricación aditiva. El campus cuenta con unos 200 empleados especializados en impresión 3D y tiene una superficie aproximada de 12.500 m2. Alberga al menos ocho impresoras 3D basadas en la fusión láser por lecho de polvo, equipos de acabado, dos hornos de tratamiento térmico, un microscopio electrónico de barrido, un laboratorio metalúrgico y un laboratorio de polvo. El objetivo de Safran es integrar la fabricación aditiva en los componentes de sus motores entre un 1% y un 25%. Esta inversión de Safran representa un paso más hacia el fortalecimiento de la colaboración entre empresas europeas, institutos de investigación y defensa, acercándolas a las inversiones masivas de Estados Unidos, que sigue dominando en este sector hasta la fecha.
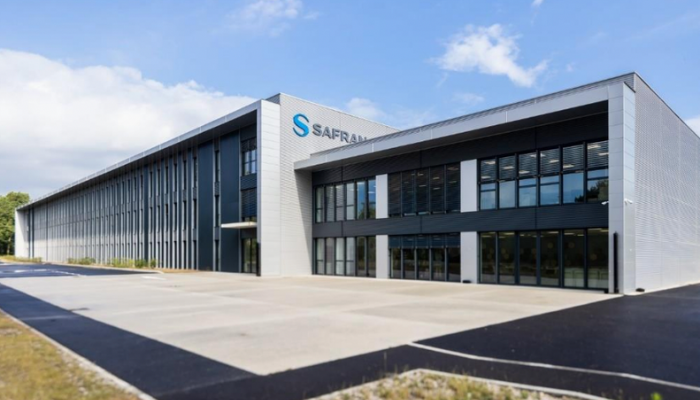
Créditos: Safran
Norsk Titanium suministra piezas y lanza una nueva asociación de proveedores
El líder en fabricación aditiva de titanio en la industria aeroespacial Norsk Titanium US Inc, ya ha suministrado piezas para el Boeing 787 Dreamliner en 2021. Norsk es más conocida por su tecnología patentada Rapid Plasma Deposition®, que mejora la resistencia y durabilidad de la pieza acabada y funciona de forma similar a la deposición de energía directa (DED). Sin embargo, Norsk utiliza un haz de electrones que permite calentar el polvo en varios lugares simultáneamente. Entre las piezas producidas había componentes de titanio impresos en 3D que fueron certificados por la FAA (Administración Federal de Aviación). Ahora, la empresa ha firmado un acuerdo para suministrar piezas de producción en serie directamente a The Boeing Company, lo que marca el inicio de una relación de proveedor directo. Norsk Titanium espera suministrar cientos de piezas estructurales de aquí a 2025. “Nuestra tecnología RPD® y las especificaciones de material establecidas permiten a Norsk Titanium responder rápidamente a los requisitos de nuestros clientes”, explica Nick Mayer, vicepresidente comercial.
ITP Aero obtiene certificación EASA para componentes 3D
Con sede en Vizcaya, ITP Aero ha logrado obtener las certificaciones de la Agencia Europea de Seguridad Aérea (EASA) y de la Agencia Estatal de Seguridad Aérea (AESA) para componentes estructurales impresos en 3D. La compañía se convierte así en la primera en la industria de motores aeronáuticos en recibir estas aprobaciones para piezas fabricadas mediante sinterizado selectivo por láser (SLS), aplicada en las palas traseras del motor TP400. Este proceso de fabricación aditiva industrial permite crear componentes complejos utilizando menor material y energía, lo que contribuye a la sostenibilidad del sector. Además, ITP Aero ha desarrollado sus propios estándares y especificaciones de fabricación aditiva para componentes de motores aeronáuticos de alta temperatura. La empresa cuenta con una célula de fabricación especializada y está construyendo el centro de investigación “ADMIRE” para continuar avanzando en tecnologías de fabricación digital y sostenible.
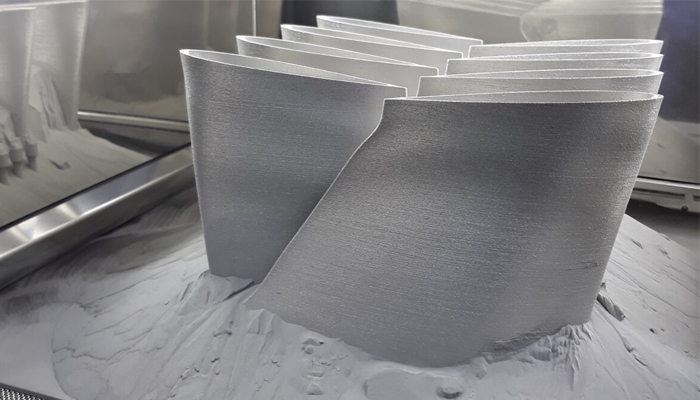
Créditos: ITP Aero
Materialise desarrolla soluciones de cabina impresas en 3D
La empresa Materialise ha ampliado su papel en el sector aeronáutico de mantenimiento, reparación y revisión (MRO). Ahora trabaja con Proponent, el mayor distribuidor del mundo, y Stirling Dynamics, una organización de diseño líder con certificación EASA 21.J, para desarrollar soluciones de cabina impresas en 3D. Materialise se ha asociado anteriormente con Airbus y EOS para producir con éxito piezas impresas en 3D para el avión A350, incluidas unas 100 piezas ignífugas. El objetivo de la nueva asociación es ahora proporcionar piezas de repuesto creadas mediante impresión 3D y certificadas para la industria aeronáutica. Stirling Dynamics se centrará en mejorar los diseños de las piezas del interior de la cabina, mientras que Materialise utilizará su capacidad de producción certificada. La colaboración ya ha dado lugar a varias soluciones de reparación de cabinas que abordan problemas específicos de las cabinas de los aviones. Proponent, en particular, ha desempeñado un papel clave colaborando con los fabricantes de equipos originales para ofrecer estas soluciones en todo el mundo.
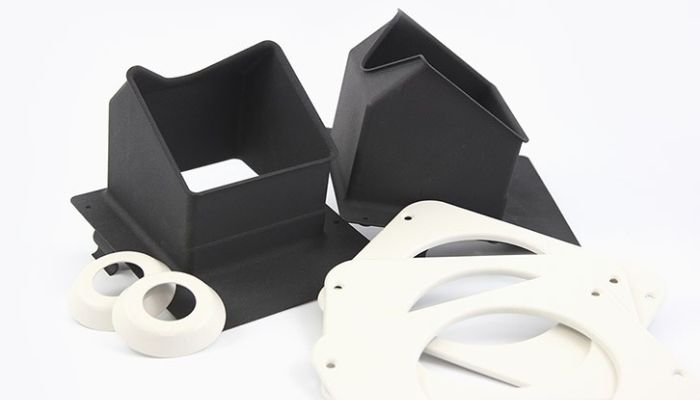
Piezas aeronavegables fabricadas con el material ignífugo PA 2241 FR ofrecido por Materialise con calidad certificada por Airbus. (Créditos: Materialise)
Lufthansa imprime en 3D piezas de cabina para sus aviones
Lufthansa Technik es proveedor líder de servicios de mantenimiento, reparación, revisión y modificación de aeronaves civiles. Ha declarado que está utilizando la fabricación aditiva de polímeros tanto para rediseñar piezas de cabina como para reproducir piezas convencionales de aviones. De hecho, Lufthansa utiliza la impresión 3D para personalizar las cabinas VIP de los pasajeros. Sin embargo, la fabricación aditiva también se utiliza para hacer más resistentes o ligeros los componentes convencionales de las cabinas de los aviones. La empresa ya ha mejorado la función de las rejillas de ventilación, los clips y las cubiertas de sus aviones. Lufthansa tiene previsto utilizar cada vez más la fabricación aditiva, especialmente en lo que respecta al uso del diseño biónico. Se trata, de hecho, de la aplicación de métodos biológicos a las tecnologías de impresión 3D. Según la empresa, los ajustes en el diseño de la cabina y la reducción de peso realizados con impresión 3D pueden contribuir significativamente a los esfuerzos de la industria aeronáutica por lograr una mayor sostenibilidad y una menor huella de carbono.
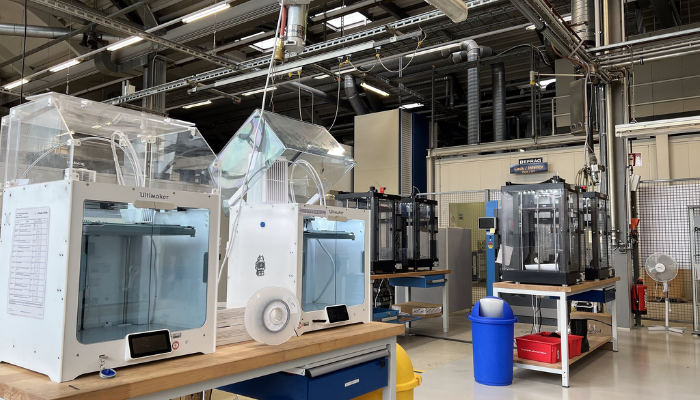
Créditos: Lufthansa Group
Rotores 3D para helicópteros Apache de Boeing
La empresa Boeing ha comenzado a probar un sistema completo de rotor principal impreso en 3D para el helicóptero de ataque AH-64 Apache. Este proyecto tiene como objetivo reducir los tiempos de espera y mejorar las cadenas de suministro de piezas normalmente forjadas. En la conferencia anual de la Asociación del Ejército de EE. UU., Boeing y ASTRO America presentaron su primer componente impreso en 3D. Se trata de un enlace del rotor principal, fabricado en una impresora 3D de metal de gran formato. ASTRO, financiada por el gobierno, ha trabajado en un contrato de 95 millones de dólares para desarrollar capacidades de fabricación aditiva de partes de gran tamaño, como los cascos de tanques. Un componente impreso en 3D del rotor principal se fabricó en 8 horas, comparado con el año que normalmente tomaría forjarlo. Así, Boeing quiere realizar pruebas de fatiga a gran escala en estas, lo cual podría acelerar la reparación de aeronaves y optimizar la fabricación de piezas.
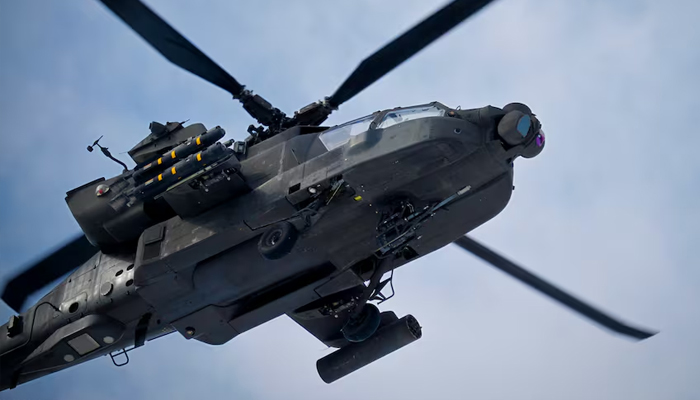
Créditos: Boeing
El centro de impresión 3D de Airbus Helicopters
Airbus lleva años integrando la impresión 3D para piezas de sus aeronaves. A menudo, han subcontratado servicios de fabricación aditiva, pero a finales de 2023 Airbus Helicopters abrió su propio centro de impresión 3D en sus instalaciones de Donauwörth (Alemania), ampliando sus capacidades internas. El centro cuenta con tres máquinas para piezas de titanio, cuatro para plástico y una para aluminio. Airbus Helicopters utiliza esta tecnología para crear piezas de producción en serie, además de prototipos como el CityAirbus NextGen eVTOL y el helicóptero compuesto experimental de alta velocidad Racer. Stefan Thomé, director general de Airbus Helicopters en Alemania, explicó las ventajas de utilizar la fabricación aditiva. “Entre otras ventajas, la impresión 3D puede reducir el peso de los componentes de las aeronaves, lo que se traduce en un menor consumo de combustible”, dijo Thomé. “Este potencial puede reportar beneficios económicos y contribuir a reducir las emisiones de CO2 durante las operaciones”.
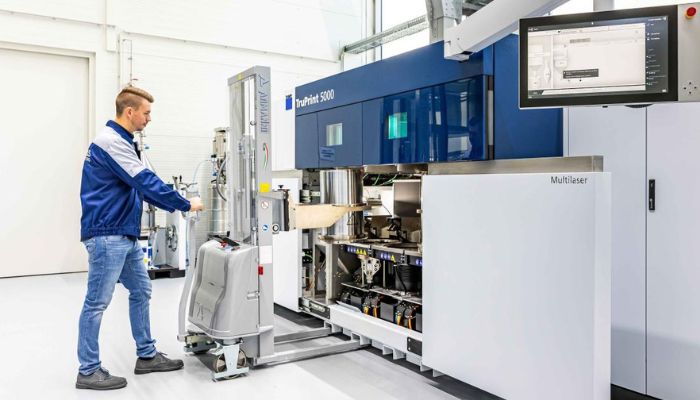
Créditos: Airbus
Finnair utiliza piezas impresas en 3D en sus aviones A320
¿Recuerdas los paneles de vídeo que muestran los asientos superiores de algunos aviones? Muchas aerolíneas, entre ellas la finlandesa Finnair, los están eliminando progresivamente. La compañía los ha sustituido recientemente por paneles ciegos impresos en 3D (paneles utilizados para cubrir «huecos» de espacio no utilizado) en sus cabinas de Airbus A320. De esta forma, ofrecen una alternativa ligera a los pesados reproductores de vídeo. La empresa de impresión 3D AM Craft creó más de 300 paneles ciegos para actualizar 17 de los aviones A320 de Finnair. Según afirman, la impresión 3D de los paneles ayudó a minimizar el exceso de inventario y a reducir los costes asociados a la cadena de suministro tradicional. Y, según Aviation Week, los paneles se diseñaron para funcionar con los raíles de montaje existentes y facilitar la instalación. Además, cualquier aerolínea con aviones A320 podría beneficiarse de este proyecto de impresión 3D, ya que los paneles ciegos están disponibles en el catálogo digital de AM Craft.
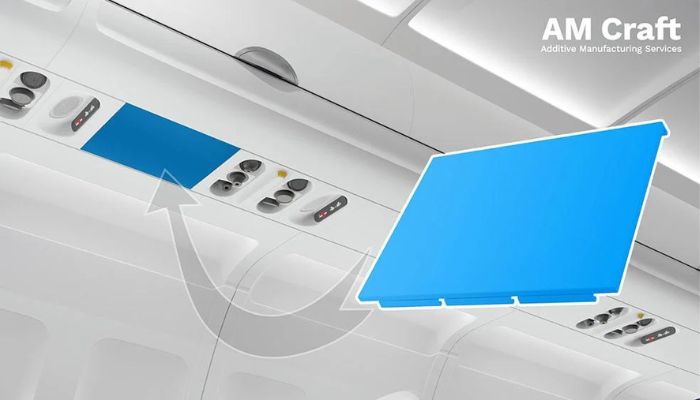
Créditos: AM Craft
Fabricación de un eje flexible impreso en 3D
Liebherr-Aerospace Lindenberg GmbH, una empresa que fabrica sistemas integrados para la industria aeronáutica, ha desarrollado ahora un eje flexible para aplicaciones aeronáuticas utilizando la fabricación aditiva por capas (ALM). Tradicionalmente, consta de siete componentes que deben unirse mediante procesos complejos. El uso de la impresión 3D simplifica este proceso, reduce la necesidad de mantenimiento y hace menos compleja la producción. El eje flexible impreso en 3D a partir de polvo de titanio, cuya producción en serie ha sido aprobada por Airbus y la AESA, se integrará en el engranaje diferencial del sistema de flaps del Airbus A350. Transmite los movimientos de rotación a un sensor de posición y ayuda a compensar los errores angulares y axiales entre el engranaje y el sensor. La aprobación del eje flexible impreso en 3D pone de manufiesto que la fabricación aditiva es una tecnología fiable para mejorar la sostenibilidad en la aviación. “El eje flexible muestra cómo se pueden integrar eficientemente diferentes funciones en un componente, allanando el camino para aplicaciones más complejas en el futuro”, explica Svenja Pestotnik, Directora de Fabricación Aditiva en Liebherr-Aerospace Lindenberg GmbH.
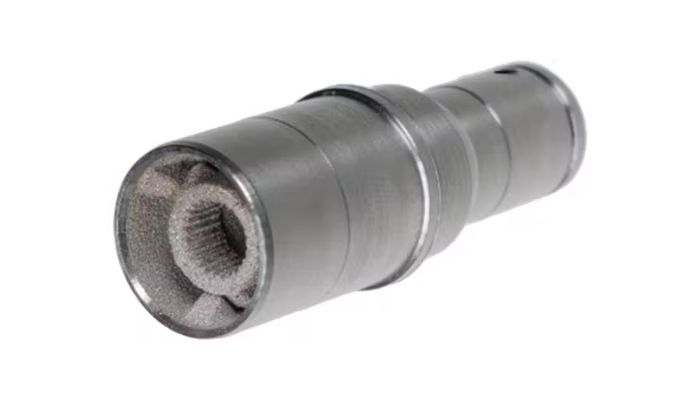
El eje flexible tiene un diseño más complejo y se fabrica con polvo de titanio mediante fabricación aditiva. (Créditos: Liebherr-Aerospace Lindenberg GmbH)
LEAP y el uso de la fabricación aditiva
Es difícil pasar por alto LEAP cuando se habla de aeronáutica e impresión 3D. Diseñado por CFM International, una empresa conjunta entre GE Aerospace y Safran Aircraft Engines, LEAP es un sistema de propulsión para aviones comerciales (como el Airbus A320neo y el Boeing 737 MAX) que se lanzó en 2016. Sus objetivos principales eran reducir la eficiencia del combustible, las emisiones de CO2 y el ruido. En vísperas de su décimo aniversario, LEAP ha cumplido sus promesas, según CFM. Pero lo que realmente nos interesa es la parte de impresión 3D. El sistema de propulsión se diseñó en parte mediante fabricación aditiva, en particular los carenados de las turbinas, las puntas de las toberas y los inyectores de combustible. Se optó por un proceso de fusión láser por lecho de polvo.
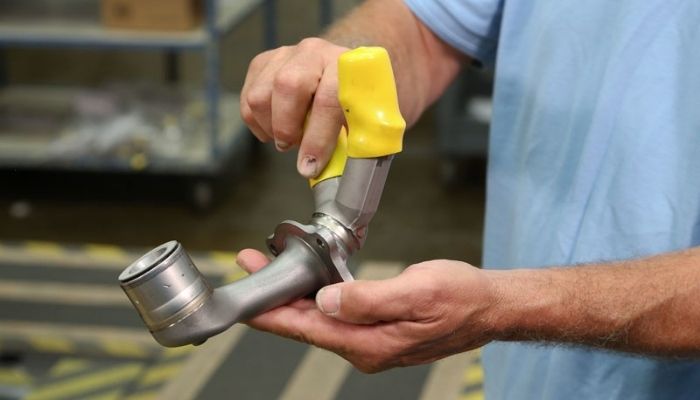
Créditos: GE
Un mantenimiento más eficiente de los escariadores del F-35B Lightning II
El objetivo del Escuadrón Logístico de Aviación de la Infantería de Marina 13 es proporcionar apoyo logístico al Grupo de Aeronaves de la Infantería de Marina, como el suministro de personal y piezas de repuesto. Sin embargo, en julio de 2024, el MALS-13 se enfrentó a una escasez crítica de escariadores para los escuadrones F-35B Lightning II. Se trata de herramientas de corte de precisión esenciales para el mantenimiento de la aviación. Los escariadores convencionales eran caros y MALS-13 no disponía de cantidades suficientes debido a los largos plazos de adquisición. Gracias a la impresión 3D, crearon una solución bajo demanda fabricando escariadores de alto rendimiento. Con ello, no sólo redujeron los costes de mantenimiento en más de un 50%, sino también los plazos de aprovisionamiento. Las piezas pasaron de estar disponibles en tres meses a fabricarse el mismo día. Para recrear los escariadores que faltaban, se adquirieron dos impresoras 3D industriales Markforged X7, lo que permitió a MALS-13 producir los componentes de calidad aeroespacial en la propia empresa, eliminando la dependencia de proveedores externos.
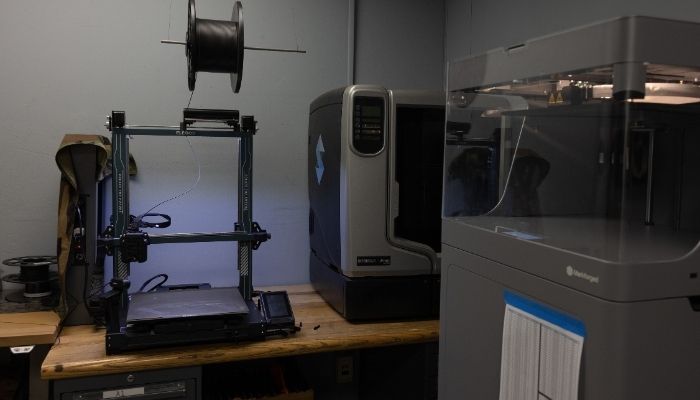
Créditos: Lance Cpl. Elizabeth Gallagher
El dron Titan Falcon
Cuando hablamos de aeronáutica e impresión 3D, no podemos pasar por alto los vehículos aéreos no tripulados, más comúnmente conocidos como drones. Sea cual sea su uso, estos dispositivos son cada vez más numerosos y pueden incorporar piezas impresas en 3D. Este es el caso del Titan Falcon desarrollado por Titan Dynamics. Tiene una autonomía de 6 horas y un alcance de 400 kilómetros, lo que le permite cubrir una amplia zona. Equipado con una cámara, es una solución ideal para vigilar los campos de batalla. De hecho, se utilizó durante el conflicto entre Ucrania y Rusia. En cuanto a la fabricación aditiva, la empresa mantiene el misterio sobre los materiales y la tecnología utilizados, pero lo que es seguro es que ha permitido reducir los plazos de entrega y facilitar las iteraciones.
Conflux fabrica intercambiadores de calor mediante impresión 3D de metal
La empresa Conflux se ha propuesto contribuir a la industria de la aeronáutica moderna con ayuda de la impresión 3D. Ésta se enfrenta a la tarea de garantizar un mayor rendimiento y fiabilidad. Conflux fabrica intercambiadores de calor para aeronaves utilizando la impresión 3D de metal con el fin de realizar geometrías más complejas y optimizar así el rendimiento de los intercambiadores de calor. Esto contribuye al rendimiento global de la aeronave. Por un lado, se puede reducir el peso total mediante componentes ligeros y, por otro, la gestión eficaz del calor se refleja directamente en el rendimiento y la autonomía de un avión.
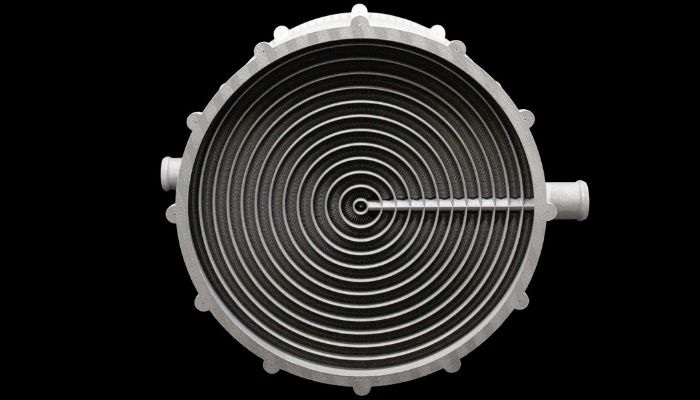
Créditos: Conflux
Cabina de helicóptero impresa en 3D para un simulador de vuelo completo
Murtfeldt Additive Solutions imprimió una cabina de helicóptero modular por encargo de Reiser Simulation and Training GmbH en 2024. Murtfeldt utilizó varias unidades de la impresora 3D de gran formato Queen 1 de Q.BIG 3D. Mediante el proceso VFGF (fabricación de granulado fundido variable), cada uno de los componentes podía imprimirse en 3D y montarse rápidamente. El tiempo de impresión más largo para un solo componente fue de 100 horas, mientras que el tiempo de producción total fue de poco más de un mes. Con unas dimensiones de 2.260 mm x 1.780 mm x 17,05 mm, la cabina pesa 200 kilogramos. La impresión 3D con gránulos de plástico resultó muy valiosa en este proyecto para alcanzar los objetivos de construcción ligera y producir de forma más económica. Dado que en la producción tradicional se necesitan muchas herramientas para un proyecto de este tipo, los costes pudieron reducirse gracias a la impresión 3D. Además, el precio de los gránulos para impresiones de gran formato es mucho más accesible que el del filamento.
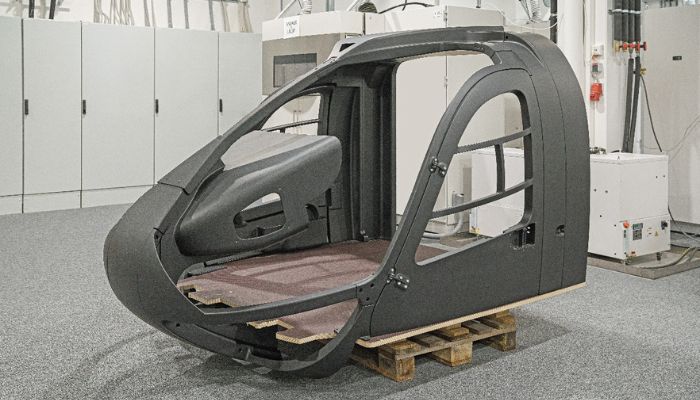
Créditos: Q.BIG 3D
Una asociación para la producción en serie con fabricación aditiva
El grupo italiano Leonardo es uno de los principales actores internacionales en la realización de capacidades tecnológicas en el sector aeroespacial, de defensa y seguridad. Es socio tecnológico de gobiernos, administraciones de defensa, instituciones y empresas. El uso de la fabricación aditiva en las actividades de Leonardo es bien conocido desde hace tiempo. En los últimos años, en la división de Aeronaves en particular, Leonardo ha renovado una asociación con el servicio BEAMIT para la producción en serie de diversos componentes con tecnología de fabricación aditiva en metal, que estará activa al menos hasta 2028. Hasta la fecha, Leonardo Aircraft ya cuenta con más de 100 piezas cualificadas con BEAMIT que actualmente están instaladas en aviones clave como el M345, el M346 y el C27J.
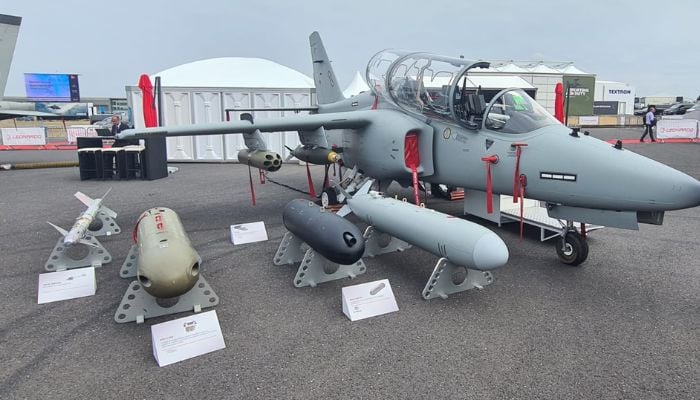
Leonardo M-345. (Créditos: Italia Vola)
El proyecto MIMOSA optimizará los aviones con impresión 3D
MIMOSA es un proyecto en el que participan varios socios institucionales y empresariales europeos. Se puso en marcha en 2022 y pretende transformar la construcción de aeronaves mediante el uso conjunto de materiales compuestos y metales impresos en 3D. El proyecto pretende dar soporte a las próximas generaciones de aeronaves, que necesariamente tendrán que seguir criterios de producción con menor impacto medioambiental y menores necesidades de materias primas. El estudio se basa en la realización de estructuras multimateriales compuestas de aleaciones metálicas y materiales compuestos sin elementos intermedios. Esto se llevará a cabo mediante la integración de la fabricación aditiva de metales, los tratamientos superficiales con plasma y las fibras de carbono. Al final del servicio, las estructuras realizadas con la tecnología MIMOSA pueden regenerarse mediante un proceso de «atomización», reduciendo los residuos y convirtiéndose en materia prima «secundaria» para los propios procesos de fabricación aditiva.
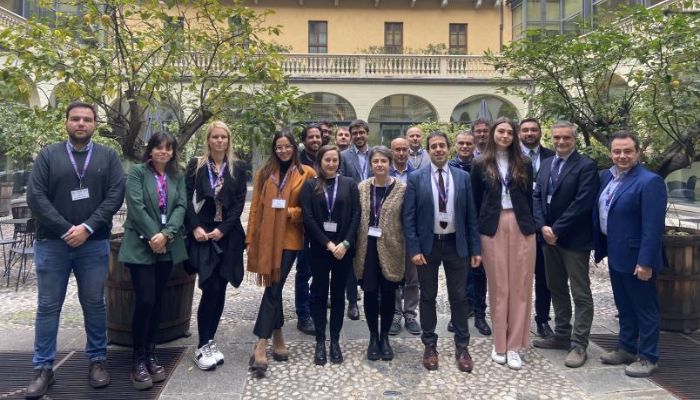
El equipo del proyecto MIMOSA (Créditos: Politecnico di Torino)
¿Qué piensas de las aplicaciones de la impresión 3D en la aeronáutica? Deja tus comentarios en nuestras redes sociales: Facebook, LinkedIn y Youtube. Sigue toda la información sobre impresión 3D en nuestra Newsletter semanal.
[…] es el equivalente al lanzamiento del primer avión. Estamos en la cúspide de una era en la que la tecnología aeronáutica finalmente puede estar en manos del consumidor y estamos orgullosos de ser los primeros en ofrecer […]
[…] hace algún tiempo la fabricación aditiva se ha utilizado en el sector aeronáutico y aeroespacial en todo tipo de aplicaciones, desde la creación de piezas hasta la fabricación de […]