La impresión 3D de composites abre nuevas aplicaciones en la industria aeroespacial y la robótica en China
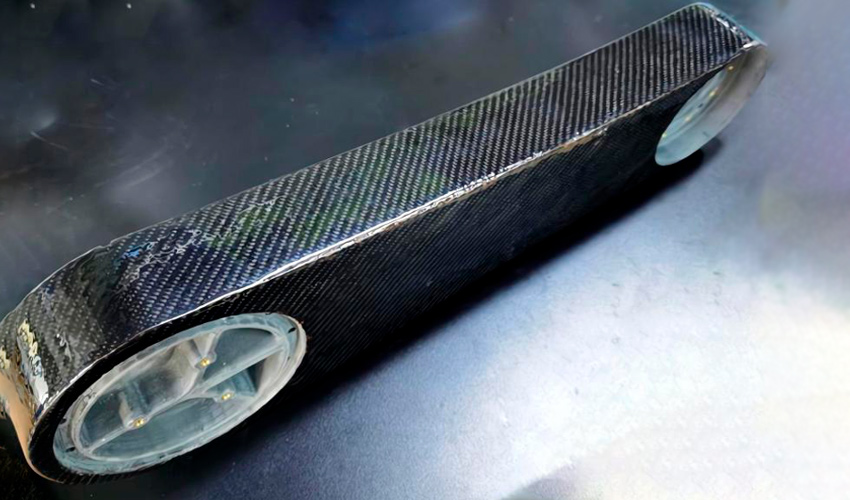
Aunque en los últimos años se ha prestado mucha atención a la impresión 3D con polímeros y metales, hay una familia de materiales que ha experimentado un inmenso crecimiento en el ámbito de la fabricación aditiva: los materiales compuestos. Tan resistentes como el metal y tan ligeros como muchos polímeros, los composites para la impresión 3D FFF suelen incluir una matriz de polímero y rellenos como fibra de vidrio o de carbono. Se han vuelto tan prevalentes que se espera que el mercado mundial de impresión 3D de materiales compuestos alcance los 490,47 millones de dólares en 2030, habiendo alcanzado ya un valor de 198,31 millones de dólares en 2023. Y la importancia de los composites para la impresión 3D también ha sido reconocida por el Instituto de Nuevos Materiales Industriales de Dezhou (China).
Fundado en enero de 2021, el instituto se dedica a investigar, desarrollar y comercializar materiales compuestos para aplicaciones en sectores como el marítimo, la comunicación 5G, los procesos de fabricación avanzados y los equipos de gama alta. Se trata de una “institución de I+D de nuevo tipo” provincial en China, que también ha visto la ventaja de pasarse a la impresión 3D. En colaboración con INTAMSYS, el instituto lidera dos iniciativas para aplicar la impresión 3D al desarrollo de piezas compuestas para los productos.
Sustituyendo del moldeo tradicional de materiales
No es ninguna novedad que la impresión 3D se ha propuesto como sustituto o incluso complemento de muchos procesos de producción tradicionales. La razón es que con la impresión 3D se consiguen geometrías complejas con mayor facilidad. Además, el diseño puede optimizarse aún más para reducir costes y plazos.
En una ocasión, se encargó al instituto el desarrollo de colectores de admisión para un motor de avión específico. Los colectores de admisión son componentes críticos dentro de los sistemas de motor con un impacto directo en el rendimiento general del motor, ya que suministran aire fresco a los cilindros para garantizar la mezcla adecuada de aire y combustible quemado. Sin embargo, su desarrollo puede resultar difícil debido a su complejo diseño, así como a las dificultades relacionadas con la fabricación de moldes, los elevados costes y el largo proceso de soldadura por vibración. Aquí es donde entra en juego la impresión 3D.
El instituto decidió fabricar estos colectores de admisión mediante impresión 3D FFF. Más concretamente, utilizaron la impresora 3D 610HT y PEEK-CF de INTAMSYS. Se eligieron por el rendimiento del material, las capacidades del equipo y la asistencia técnica.
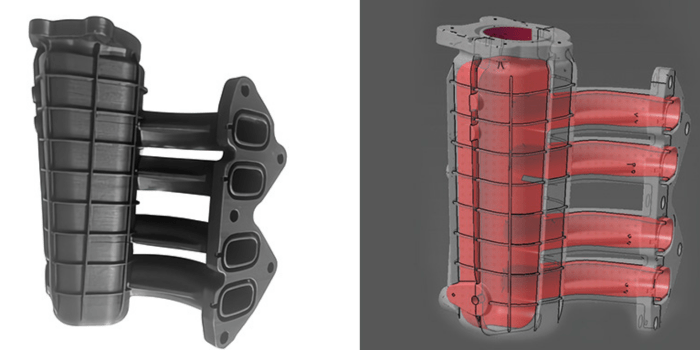
El colector de diseño acabado (izquierda) y el diseño de la pieza, incluido el interior (derecha).
Ya hemos hablado anteriormente de la FUNMAT PRO 610HT. Esta impresora 3D de gran formato y doble boquilla ha sido diseñada para trabajar con materiales termoplásticos de alta temperatura, como PEEK, ULTEM y PPSU. También es compatible con una amplia gama de materiales, incluidos polímeros personalizados. Cuenta con boquillas que pueden alcanzar hasta 500°C y una cámara que puede calentarse hasta 300°C. Esto permite imprimir materiales de alto rendimiento sin distorsión.
Además, los expertos del instituto y de INTAMSYS utilizaron el DfAM para optimizar el diseño y los procesos de impresión para fabricar la pieza de 218,4 × 216,4 × 95,4 mm. El resultado fue una reducción de peso del 30%, con un grosor de la pared más fina de sólo 1,7 mm. También se pudieron controlar las dimensiones de la pieza para conseguir un ajuste preciso y las pruebas mostraron una resistencia mecánica de 100 mPA, lo que supera en más de un 30% a los productos tradicionales de PA66-GF moldeados por inyección, todo ello a la vez que son capaces de soportar temperaturas a largo plazo de 114°C.
Teniendo en cuenta que las piezas fabricadas con procesos tradicionales de moldeo por inyección (incluido el utillaje) habrían costado unos 27.803 dólares con un plazo de entrega de 45 días, el valor de la impresión 3D se hizo evidente de inmediato. El instituto pudo fabricar los colectores de admisión como una sola pieza integrada, lo que redujo los costes a una décima parte de los que se hacían con métodos tradicionales y acortó el plazo de producción a solo 4-7 días.
Fabricación híbrida con impresión 3D de composites
Por supuesto, la impresión 3D de materiales compuestos no sólo es útil para sustituir a los métodos tradicionales. También puede integrarse en procesos ya existentes. Así lo hizo el instituto en colaboración con una universidad china para desarrollar un brazo manipulador robótico de material compuesto.
Por ejemplo, para fabricar el brazo manipulador se utilizó la FUNMAT PRO 610HT y PEEK-CF como estructura de soporte interna. El componente resultante no sólo era de gran tamaño, sino que presentaba superficies curvas, una elevada relación rigidez-peso y una excepcional resistencia específica. Esto demuestra la capacidad de la impresión 3D de composites para crear piezas complejas de alto rendimiento.
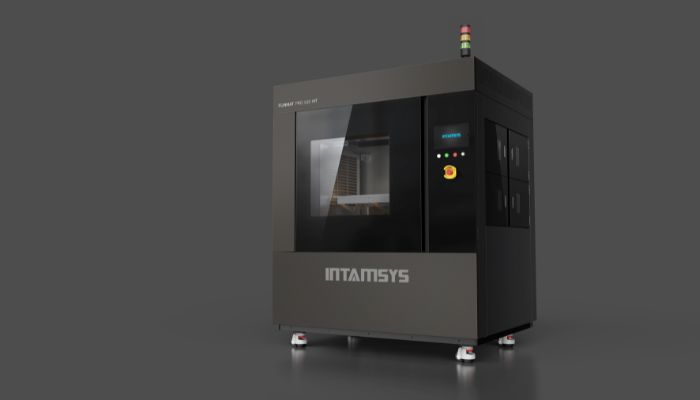
La FUNMAT PRO 610HT se utilizó tanto para los colectores de admisión como para el componente del brazo robótico.
A continuación, la universidad utilizó un método de estratificación preimpregnada para envolver la estructura impresa en 3D con fibra de carbono. Esto permitió la creación rápida y asequible de un brazo manipulador de composite ligero y robusto. ¿Y lo mejor? Fue posible evitar el costoso utillaje de moldeo y, al mismo tiempo, conseguir una resistencia estructural comparable a la de las aleaciones de aluminio. Además, la impresión 3D de composites también podía combinarse con otras técnicas tradicionales, como el bobinado de filamentos, la estratificación automatizada y los procesos de moldeo por compresión.
En cualquier caso, está claro que el Instituto de Nuevos Materiales Industriales ha demostrado las ventajas de sustituir y complementar los procesos tradicionales con la impresión 3D de composites. En concreto, mediante la mejora de la eficiencia y la reducción de costes en la fabricación de piezas con materiales compuestos.
¿Qué piensas de la tecnología de impresión 3D de composites desarrollada por INTAMSYS? Deja tus comentarios en nuestras redes sociales: Facebook, Twitter y Youtube. Sigue toda la información sobre impresión 3D en nuestra Newsletter semanal.
*Foto de portada: El componente del brazo robótico, creado mediante impresión 3D de composites. (Créditos: INTAMSYS)