El uso de la impresión 3D de cerámica para crear estructuras aeroespaciales complejas
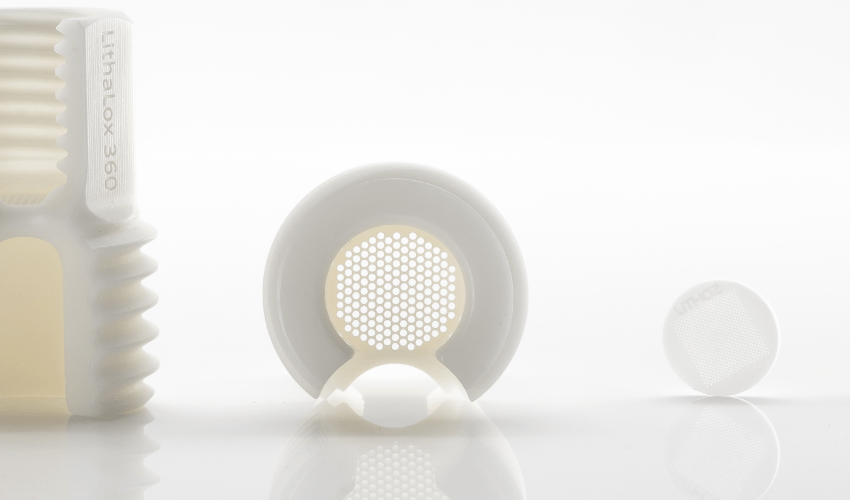
Las industrias buscan cada vez más materiales y procesos nuevos y avanzados para mejorar sus productos, y el sector aeroespacial no es una excepción. Las necesidades de la industria evolucionan rápidamente con la introducción de requisitos más estrictos. Por ello, demandan nuevas tecnologías que puedan ofrecer soluciones innovadoras y eficientes. La fabricación aditiva destaca como una solución ideal para las aplicaciones aeroespaciales. Según un informe de Research and Markets, el mercado aeroespacial y de defensa para la impresión 3D se valoró en $1.900 millones en 2021, con una CAGR de más del 24% para 2027. La impresión 3D está aportando así cambios y ventajas significativas para aplicaciones aeroespaciales, como la producción de estructuras más ligeras, resistentes y complejas, la libertad de diseño, la capacidad de combinar varias piezas en una sola unidad, la reducción del desperdicio de materias primas y la eficiencia de costes y recursos.
Si nos fijamos en los materiales innovadores que pueden utilizarse en la impresión 3D, la cerámica está en pleno auge. Ésta ha demostrado tener las propiedades necesarias para satisfacer las necesidades de la industria y los altos estándares exigidos en las aplicaciones aeroespaciales. Entre las empresas que se han centrado en la fabricación aditiva de cerámica se encuentra el fabricante austriaco Lithoz, que ha desarrollado la tecnología Lithography-based Ceramic Manufacturing (LCM) para piezas complejas de alta resolución. La empresa duplicó las ventas de sus soluciones de impresión 3D de cerámica y la facturación en el año 2022, lo que indica el interés del mercado por esta tecnología en múltiples industrias, incluidas la médica y la aeroespacial.
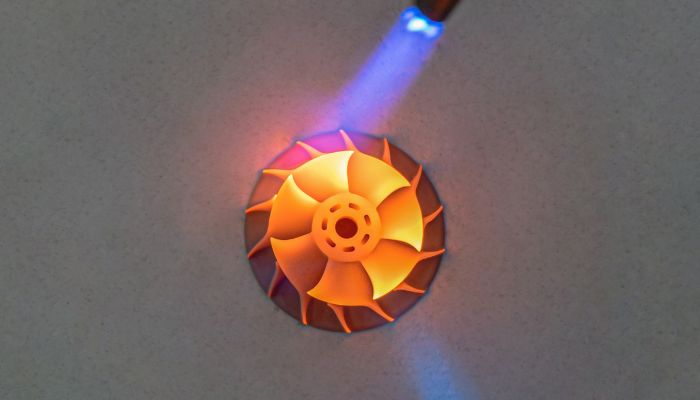
Pieza impresa en 3D con cerámica.
Beneficios de usar la cerámica en aplicaciones aeroespaciales
El informe titulado “3D Printing Ceramics 2022-2032: Technology and Market Outlook” destaca el crecimiento del valor de mercado de la impresión 3D de cerámica, que se estima alcanzará los $400 millones en 2023. Según el informe, las industrias aeroespacial, de defensa, dental y de ingeniería química son las más interesadas en la fabricación de cerámica para producir piezas en lotes pequeños. La cerámica ha captado la atención de la industria aeroespacial por sus excepcionales propiedades, como su alta resistencia al calor, la oxidación y la abrasión, así como su estabilidad mecánica y dimensional. Esto hace que la cerámica sea ideal para su uso en condiciones extremas, como es la construcción de naves espaciales de nueva generación, especialmente para piezas expuestas a grandes tensiones. Nos referimos sobre todo a los “materiales cerámicos avanzados” o “cerámicas técnicas”, que poseen propiedades notables como alta resistencia, resistencia a la corrosión y excelente aislamiento térmico y eléctrico. Algunas de las cerámicas avanzadas más destacadas son el óxido de aluminio (Al2O3), el nitruro de silicio (Si3N4), el carburo de silicio (SiC) y la circonia (ZrO2). Mediante la impresión 3D se pueden procesar incluso cerámicas de temperatura ultra alta (UHTC), cuyas propiedades materiales son muy solicitadas en esta industria.
La cerámica ha sustituido incluso a algunos materiales más tradicionales utilizados en la industria aeroespacial, como son los metales. De hecho, aunque los metales siguen siendo los materiales más utilizados en la industria aeroespacial, su uso se está cuestionando para algunas aplicaciones. La necesidad de crear propulsores espaciales más eficaces, reducir la basura espacial o desarrollar núcleos de fundición para aviación más precisos y complejos ha llevado a buscar alternativas. La cerámica ofrece ahora soluciones prácticas a estos problemas, ya que se desgasta más lentamente. Además, en combinación con la fabricación aditiva, se pueden conseguir piezas más detalladas.
Por tanto, la impresión 3D de cerámica tiene un enorme potencial para la industria aeroespacial, como demuestran las diversas aplicaciones de la tecnología LCM de Lithoz. Un excelente ejemplo de las excepcionales capacidades de la cerámica avanzada es la tobera de motor aerospike impresa en 3D con nitruro de silicio de la empresa. Esta tobera superó con éxito todas las pruebas de estrés, demostrando su capacidad para soportar fuertes choques térmicos, incluso cuando se somete a temperaturas superiores a 1200°C.
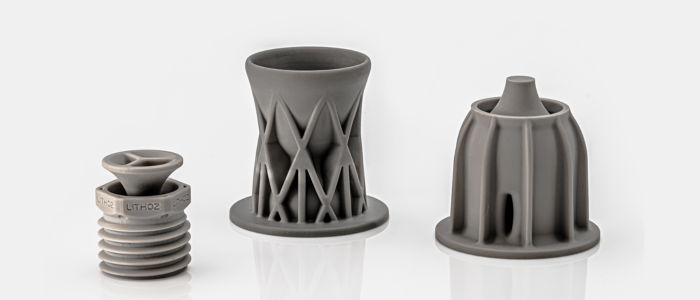
La tobera del motor aerospike impresa en 3D.
Alta resolución y precisión gracias a la tecnología LCM
En la cerámica, la precisión y la exactitud son fundamentales, ya que un solo pequeño defecto puede provocar el fallo completo de la pieza y, por tanto, de la aplicación. Por este motivo, la propia empresa Lithoz se fundó sobre los valores de resistencia y precisión. Y a lo largo de su experiencia de más de una década, la empresa ha sido capaz de perfeccionar su tecnología para lograr una tolerancia cero al error.
La tecnología LCM de Lithoz se basa en la fotopolimerización. La impresora 3D CeraFab dispensa un líquido cargado de cerámica (en forma de pasta) en una cuba transparente. La placa de impresión se desplaza de arriba abajo y se expone selectivamente a la luz azul procedente de debajo de la cuba. Mediante un dispositivo digital de microespejos (DMD) y un sistema de proyección de última generación, se produce una imagen por capas y la pieza se crea capa a capa. El proceso requiere un postratamiento térmico para eliminar el aglutinante y sinterizar los componentes, lo que da como resultado componentes cerámicos de alta densidad, resistentes y duraderos.
La ventaja de este procedimiento es que toda la superficie se expone al mismo tiempo, con tolerancia cero en toda la plataforma de construcción. Esto significa que las piezas se reproducen con coherencia y precisión en toda la placa construida, independientemente del lugar de la plataforma en el que se impriman. Esta precisión de exposición permite obtener microestructuras extremadamente complejas.
Lithoz dispone actualmente en el mercado de ocho soluciones de impresión 3D diferentes. Todas ellas son variaciones de la máquina CeraFab, y cada una de ellas tiene su punto fuerte particular. Por ejemplo, la CeraFab S25 se ha diseñado específicamente para resoluciones precisas de hasta 25µm. Curiosamente, la tecnología de Lithoz se utiliza no sólo para lotes pequeños, sino también para la producción a gran escala. Steinbach AG, por ejemplo, utilizó la solución CeraFab System de Lithoz para la producción en serie de tubos quirúrgicos. El complejo diseño de los tubos requería el uso de la fabricación aditiva desde la creación de prototipos hasta la producción final. Steinbach fue capaz de producir 12.000 piezas al año, lo que demuestra la eficacia de la fabricación aditiva en el escalado de la producción incluso a nivel de serie.
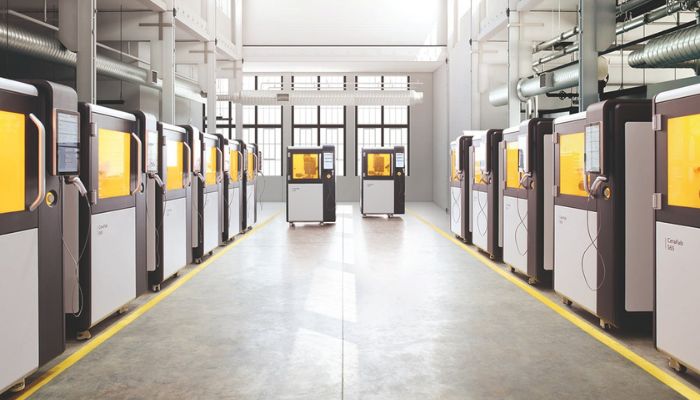
Gama de impresoras 3D CeraFab de Lithoz.
Estructuras aeroespaciales optimizadas con impresión 3D de cerámica
Como hemos mencionado, la posibilidad de combinar las propiedades de la cerámica con la flexibilidad de la impresión 3D es una de las principales ventajas en el sector aeroespacial. Poder adaptar con precisión el diseño de un componente, modificar su estructura e incluso añadir funcionalidades específicas, es algo que los actores de la industria buscan al producir piezas complejas.
Un ejemplo práctico de ello es la creación de filtros de radiofrecuencia (RF) para aplicaciones aeroespaciales. Los filtros de RF son circuitos electrónicos cruciales que mejoran la calidad de la señal y minimizan las interferencias en sistemas de comunicación como la comunicación por satélite, el radar y la aviónica. La impresión 3D de cerámica permite crear resonadores de alta ingeniería con una amplia gama de formas, órdenes y anchos de banda que pueden incorporarse en un único componente, optimizando el rendimiento, la fiabilidad y la durabilidad.
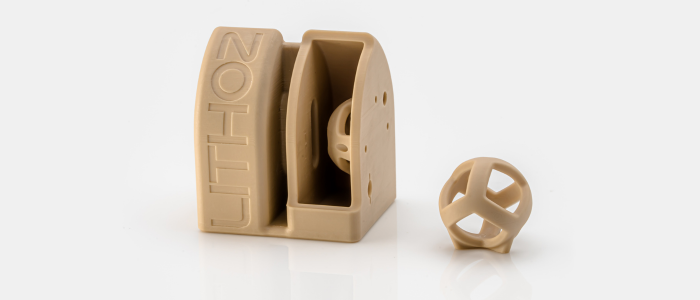
A la izquierda, un filtro de RF y, a la derecha, el resonador cerámico impreso en 3D. El resonador puede imprimirse en diferentes tamaños.
¿Por qué imprimirlos en 3D con cerámica? En la industria aeroespacial, los filtros de RF desempeñan un papel fundamental para garantizar unas comunicaciones fiables y precisas en bandas de alta frecuencia. Debido a las duras condiciones ambientales que deben soportar, estos filtros tienen que ser de alto rendimiento y cumplir estrictos requisitos de fiabilidad y rendimiento. Las propiedades de los materiales cerámicos los hacen adecuados para cumplir estos requisitos, al tiempo que permiten miniaturizar fácilmente estos filtros para reducir su peso, un factor crucial en las aplicaciones aeroespaciales. Además, los filtros cerámicos presentan una buena estabilidad a lo largo del tiempo y la temperatura, lo que garantiza un rendimiento fiable y constante durante mucho tiempo.
Control de la microestructura de los componentes cerámicos
Las soluciones de impresión 3D de cerámica de Lithoz ofrecen una notable ventaja para aplicaciones más complejas al permitir un control más preciso de la microestructura y la porosidad del material. Esto supone una limitación de cualquier otra técnica de fabricación aditiva o convencional disponible en la actualidad. Con la tecnología LCM de Lithoz, también es posible la impresión 3D multimaterial y de cerámicas con grados funcionales gracias a su sistema de dos cubas. En la configuración de la impresora LCM multimaterial recientemente desarrollada, este sistema permite no sólo asignar un material a cualquier capa deseada, sino también utilizar diferentes materiales en cada capa asignando los respectivos materiales a píxeles seleccionados de la imagen de la capa. Como ejemplo, Lithoz y Fraunhofer IGD crearon piezas de óxido de aluminio de gran complejidad y con un gradiente definido de denso y poroso dentro de una misma pieza. Esta capacidad es muy relevante para la impresión 3D de catalizadores complejos para aplicaciones aeroespaciales, entre otras posibilidades.
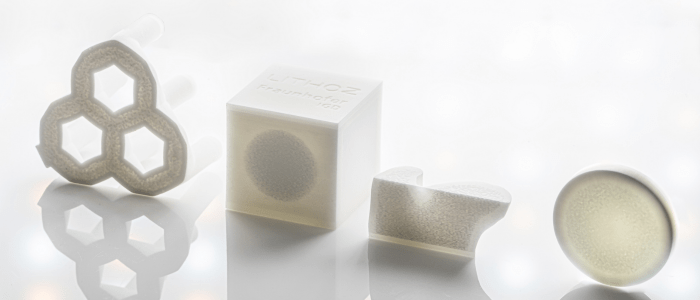
Piezas de demostración con gradación de denso a poroso para aplicaciones en diversos campos, como catalizadores, filtros o estructuras óseas.
Todos estos ejemplos demuestran que, utilizando la fabricación aditiva para mejorar las propiedades de los componentes cerámicos, es posible aumentar su complejidad y, a su vez, mejorar su eficiencia. Este enfoque también abre nuevas posibilidades de investigación en la industria aeroespacial. Con la tecnología Lithoz LCM es posible lograr una mayor complejidad y resolución en comparación con otros procesos del mercado, lo que la convierte en la opción perfecta para los requisitos cada vez mayores en cuanto a geometrías cuando se trata de componentes aeroespaciales. Puedes obtener más información sobre Lithoz y su tecnología AQUÍ.
¿Qué piensas del uso de la impresión 3D para crear estructuras aeroespaciales complejas? Deja tus comentarios en nuestras redes sociales: Facebook, Twitter, Youtube y RSS. Sigue toda la información sobre impresión 3D en nuestra Newsletter semanal.
*Créditos de todas las fotos: Lithoz