Formnext destaca las aplicaciones y el potencial de la fabricación aditiva en el sector aeroespacial

Como cada año, Formnext 2024 funcionó como una radiografía para analizar lo que está impulsando actualmente el sector de la fabricación aditiva y hacia dónde se dirigen las tendencias en un futuro próximo. Mientras que el año pasado la atención se centró en la automoción y la sostenibilidad, este año vimos una mayor presencia de las tecnologías de impresión 3D de metal y las aplicaciones aeroespaciales. Por un lado, esto se puso de manifiesto directamente en los stands de los expositores a través de los casos de uso y las innovadoras soluciones de impresión 3D que se expusieron. Por otro lado, en el programa del evento, donde se dedicaron numerosas conferencias y presentaciones al procesamiento de metales y la fabricación aditiva para el sector aeroespacial. Ya hemos destacado las innovadoras aplicaciones de la impresión 3D de metal en Formnext en un artículo anterior. Así que ahora, analizaremos la razón por la que la fabricación aditiva se utiliza cada vez más en el sector aeroespacial, qué retos siguen existiendo y qué soluciones pueden ayudar a aprovechar el potencial de la impresión 3D en este campo.
La fabricación aditiva se utiliza principalmente en la industria aeroespacial para componentes de naves espaciales, como piezas para la propulsión de cohetes, cámaras de combustión, cabezas de inyectores y sistemas de bombeo. Otro importante campo de aplicación es la producción de estructuras en el espacio, es decir, elementos que se fabrican en el espacio y algunas veces con material espacial. Ejemplos de ello son las pistas de aterrizaje y las estructuras de edificios fabricadas con regolito lunar.
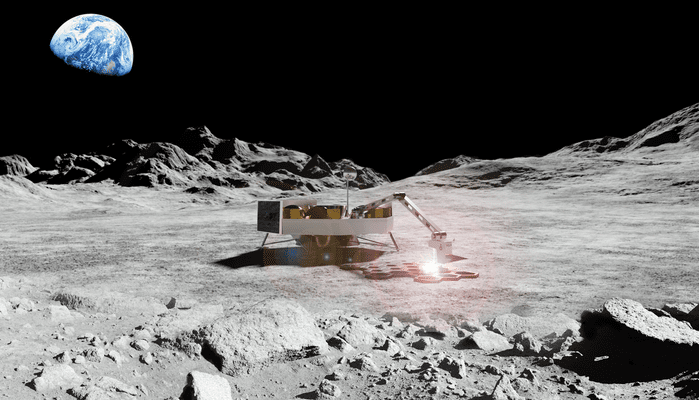
Créditos: ICON
La fabricación aditiva permite conseguir diseños intrincados y complejos e integrar sistemas de refrigeración en motores de cohetes en un solo paso de producción. En muchos ejemplos de esta aplicación, las piezas fabricadas mediante un proceso aditivo permiten aumentar el rendimiento. Esto también se debe a que en algunos casos se utilizan materiales personalizados con propiedades específicas para satisfacer las altas necesidades de la industria. Las ventajas mencionadas no solo se aplican a los componentes, sino también a las estructuras espaciales. La fabricación aditiva es flexible y a la carta, garantiza una gran precisión con un consumo de energía de bajo a medio y se valora por la eficiencia de sus materiales, como aprendimos en la presentación de Mohammad Azami, del Concordia Aerospace Robotics Lab. Sin embargo, los procesos tradicionales, como el moldeo y el sinterizado del hormigón de regolito, siguen utilizándose para la producción de componentes con geometrías sencillas debido a su rapidez.
Procesos de fabricación aditiva para la exploración espacial y retos existentes
Sin embargo, si nos quedamos con la fabricación aditiva, vemos que se utiliza sobre todo el proceso L-PBF, aunque la tecnología DED también se implementa cada vez más. La empresa The Exploration Company, por ejemplo, se centra actualmente en la fusión láser por lecho de polvo, pero está considerando la deposición de energía directa para el 2025. La empresa alemana ponticon fabrica sistemas industriales de DED de alta velocidad y su proceso de Deposición Dinámica de Material se utilizó para revestir el motor Ariane 6. En este proceso, el polvo se funde mientras aún está en el aire, y de este modo puede lograrse una precisión notable.
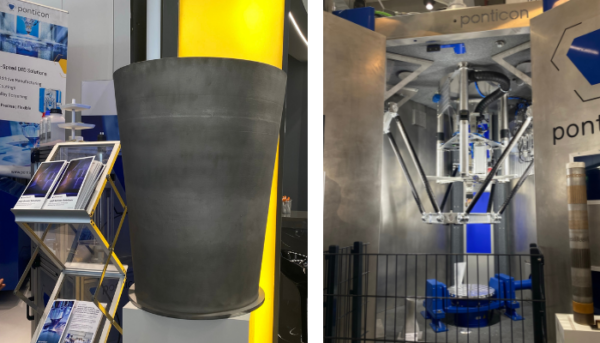
En el stand de ponticon en Formnext. (Créditos: 3Dnatives)
El proceso DED evita así un problema que constituye uno de los mayores retos de la fusión de capas de polvo en el sector aeroespacial, a saber, el desempolvado de piezas complejas. Aunque los canales de refrigeración internos y los diseños sofisticados pueden realizarse mediante impresión 3D, es difícil limpiar correctamente esos conductos de refrigeración después. Si queda polvo en estos canales, los fluidos no pueden circular y existe el riesgo de que el motor se funda o se destruya. La creciente complejidad de las piezas también sigue siendo un reto. «Imprimimos 100 canales de refrigeración en una pieza con un grosor de pared de 4 mm, lo que supone un verdadero reto», afirma Maximilian Strixner, de The Exploration Company, empresa que ha desarrollado Nyx, una cápsula espacial modular y reutilizable.
Las condiciones para la fabricación aditiva en el espacio son diferentes a las de la impresión de piezas en la Tierra, por lo que las aplicaciones en el espacio se enfrentan a requisitos y problemas especiales. Por ejemplo, en la Luna no hay una temperatura constante y las fluctuaciones extremas de temperatura dificultan la fabricación de piezas. Además, los efectos de la gravedad cero afectan a la producción de piezas y a la construcción de estructuras.
Otro reto al que se enfrentan los usuarios de la fabricación aditiva en el sector aeroespacial, ya sea en la Tierra o en el espacio, es el coste. Esto se debe principalmente a los elevados precios de los materiales que necesitan unas características específicas. Tobias Stiggen, de ponticon GmbH, explicó en su presentación que alrededor de dos tercios de los costes totales del ejemplo mostrado (el revestimiento del sistema de propulsión del Ariane 6) son atribuibles al material. El coste del hardware, en este caso, un sistema de impresión de ponticon, era relativamente bajo en comparación.
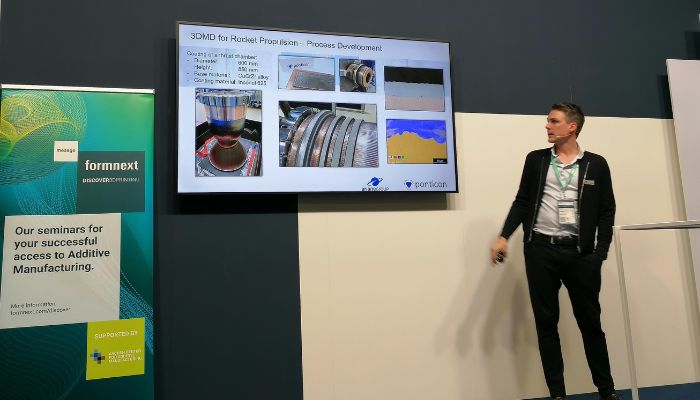
Tobias Stiggen explica las ventajas de la tecnología DED para la propulsión de cohetes. (Créditos: 3Dnatives)
Otra razón de los elevados costes es que la industria aeroespacial se centra en piezas de alto rendimiento y ligeras. Mientras que la industria del automóvil se concentra en optimizar los costes por pieza, la industria aeroespacial se esfuerza por reducir el peso de las piezas. Bill Bihlman, de SAE International, señaló en su presentación sobre “Material Qualification for Aerospace and Automotive AM Serialized Part Production» que las piezas aeroespaciales cuestan unas diez veces más que las de automoción.
Diversidad de materiales de alto rendimiento para aplicaciones aeroespaciales
Aunque el precio desempeña un papel importante, el rendimiento de los materiales utilizados y su durabilidad son primordiales. En las aplicaciones aeroespaciales existen diversos metales y aleaciones, así como materiales y compuestos de nuevo desarrollo. The Exploration Company, por ejemplo, utiliza aleaciones de cobre por su conductividad térmica y aleaciones a base de níquel por su resistencia mecánica y química. SAE también confía en las aleaciones, pero también en el aluminio y el titanio para piezas de series cortas.
Los materiales predominantes en la producción espacial son los composites. Concordia Aerospace Robotics Lab, por ejemplo, recomienda un material compuesto de PEEK y regolito. Este cumple los requisitos de la NASA en cuanto a la proporción de gases de escape y es muy resistente a la radiación y los productos químicos. Al incorporar regolito al PEEK, también podrían reducirse los costes, según lo demuestran los resultados. Con un 50% en peso de regolito en PEEK, la reducción de costes también fue del 50%.
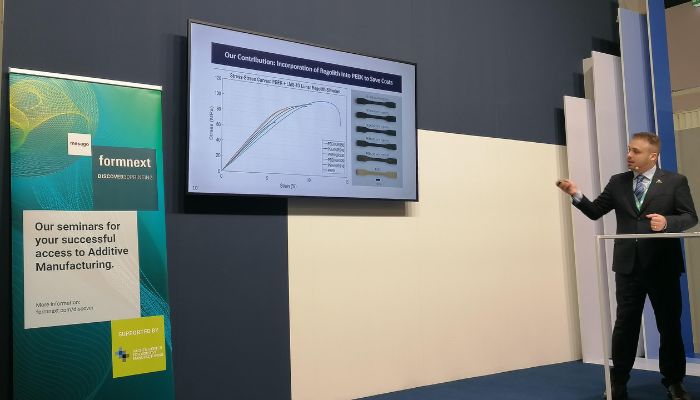
Mohammad Azami del Concordia Aerospace Robotics Lab. (Créditos: 3Dnatives)
En el último año ha aumentado la tendencia por imprimir en 3D con silicona en todo el sector de la impresión 3D. Este material también se está abriendo camino en el sector aeroespacial. Una presentación aparte en Formnext 2024, «Transforming Aerospace with silicone and soft composites 3D printing», se centró en este material. Julien Barthes, de 3DEUS DYNAMICS, presentó su proceso de polvo con silicona y cómo la empresa desarrolla nuevos compuestos blandos durante el proceso de impresión. La ventaja es que la silicona convencional moldeada por inyección también puede utilizarse para la impresión 3D, sin generar residuos, ya que el polvo reciclado puede reutilizarse. Barthes también señala que es posible cambiar el material durante el proceso de impresión, de modo que se puede producir una sola pieza con dos texturas y propiedades mecánicas personalizadas, así como geometrías complejas. «Se puede añadir polvo durante el proceso de impresión, manipular el material y fabricar compuestos durante el proceso», resume Barthes, explicando que de esta forma la empresa produjo un nuevo material compuesto ignífugo y blando que resulta adecuado para componentes expuestos al fuego, como es el caso de la industria aeroespacial.
Perspectivas a futuro
Con la amplia gama de aplicaciones aeroespaciales e informaciones técnicas de Formnext, es inevitable que la fabricación aditiva se imponga cada vez más en este sector. Aunque este año hemos sido testigos de algunas innovaciones notables en el sector aeroespacial (como el lanzamiento del Ariane 6, el mayor motor de cohete del mundo impreso en metal de Eplus3D y LEAP 71), aún quedan algunos retos. No obstante, la fabricación aditiva encierra un potencial considerable en la exploración espacial que aún no se ha explotado plenamente. Además de la construcción ligera, las geometrías muy complejas y los nuevos materiales de alto rendimiento que hacen que los cohetes sean más rápidos, más eficientes y más sostenibles, en un futuro próximo también leeremos y oiremos hablar cada vez más de la impresión 3D directamente en el espacio.
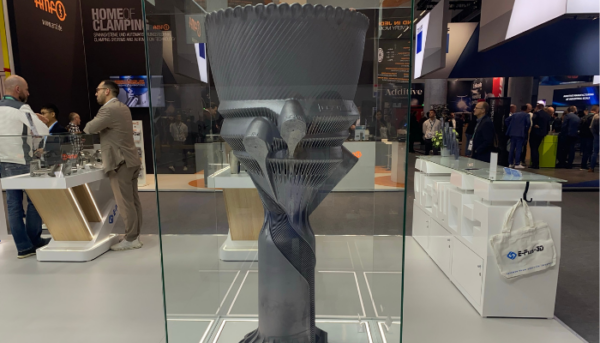
Eplus3D y LEAP 71 presentaron en Formnext 2024 el mayor motor de cohete impreso en metal del mundo hasta la fecha. (Créditos: 3Dnatives)
¿Qué opinas del estado de la fabricación aditiva en el sector aeroespacial? Deja tus comentarios en nuestras redes sociales: Facebook, LinkedIn y Youtube. Sigue toda la información sobre impresión 3D en nuestra Newsletter semanal.
*Créditos de la foto de portada: Pixabay