Fibras continuas VS cortas: ¿qué tipo de refuerzo elegir para las piezas impresas en 3D?
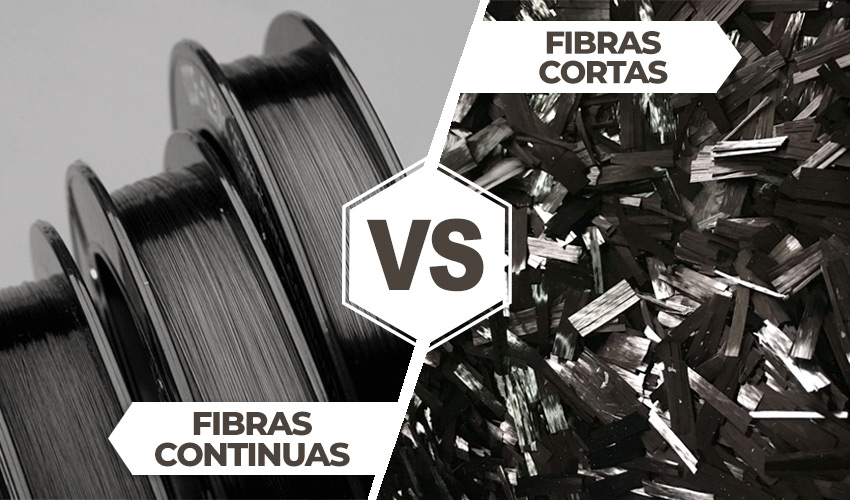
Cuando se quieren conferir propiedades específicas y superiores a las piezas impresas en 3D, se suele recurrir a los materiales compuestos. Estos pueden ser incluso más resistentes que algunos metales y ofrecer un alto rendimiento. También llamados composites, están formados por al menos dos materiales que se combinan para conseguir propiedades nuevas o mejoradas en comparación con las materias iniciales. Como podemos imaginar, existen numerosos materiales compuestos, aquí nos centraremos en los formados por una matriz polimérica y fibras de refuerzo. En la industria de la impresión 3D, la fibra de carbono, la fibra de vidrio y el Kevlar son tres de los materiales de fibra más utilizados para los materiales compuestos.
En este artículo, analizaremos y compararemos la impresión 3D de materiales compuestos reforzados con fibras cortas y continuas. Estas dos técnicas similares dan resultados diferentes y pueden ser usadas en diferentes tecnologías. La que destacaremos en este caso es la tecnología más común, es decir, la extrusión de material. Pero, ¿cuáles son las similitudes y diferencias de estas dos técnicas y cómo elegir el tipo de refuerzo más adecuado para cada aplicación específica? Veámoslo a continuación.
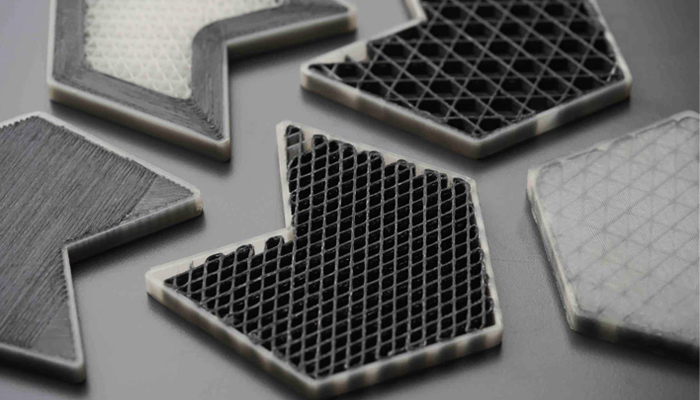
Créditos: Anisoprint
Características de las fibras cortas y continuas
Entendemos las fibras cortas como trozos más pequeños de material fibroso, que pueden variar en longitud desde centímetros hasta milímetros, e incluso más pequeños. Se trata de un proceso similar al utilizado para reforzar el hormigón con trozos de barras de refuerzo. De esta forma, las fibras se dispersan en la matriz plástica y actúan como refuerzo a lo largo de todo el material. Por su parte, las fibras continuas son hilos largos que se extienden a lo largo de toda la pieza de material compuesto. Estas fibras se integran en una matriz plástica mediante el proceso de impresión 3D, creando un material compuesto que combina las propiedades de ambas. Antes de pasar al proceso de fabricación aditiva en sí y los puntos a tener en cuenta a la hora de crear dichas piezas, es importante conocer las características de ambos refuerzos.
En los dos casos encontramos la misma composición de material: un elemento de refuerzo (fibras) y un elemento de matriz (polímero). El primero proporciona las propiedades mecánicas, mientras que el segundo sirve como recipiente y, con ayuda de una resina, se asegura de que ambos elementos se mantengan juntos, es decir, que la fibra se adhiera al material durante la fabricación. Una vez se han elegido los compuestos la matriz (polímeros como el PLA, ABS, polipropileno, HIPS, PETG, etc.) y las fibras de refuerzo (vidrio, carbono o aramida), llega el momento de juntarlas en un mismo material.
La obtención de las fibras cortas puede realizarse mediante un proceso de extrusión, donde la mezcla con la matriz se funde y se extruye para formar un único filamento. Durante este proceso, es posible controlar la temperatura y la velocidad con el fin de asegurar una buena distribución de las fibras. Las fibras continuas, a la hora de formar filamentos, se pueden coextrusionar con una resina especial a través de un proceso mediante el cual se mezcla, cura y solidifica la mezcla con la resina. En algunos casos existen sistemas de fabricación que imprimen directamente la matriz y el refuerzo al mismo tiempo durante la deposición sucesiva de capas, pero esto es algo que veremos más adelante. En ambos casos, las fibras cortas y continuas deben estar limpias y libres de contaminantes para asegurar una buena adhesión a la matriz de polímero.
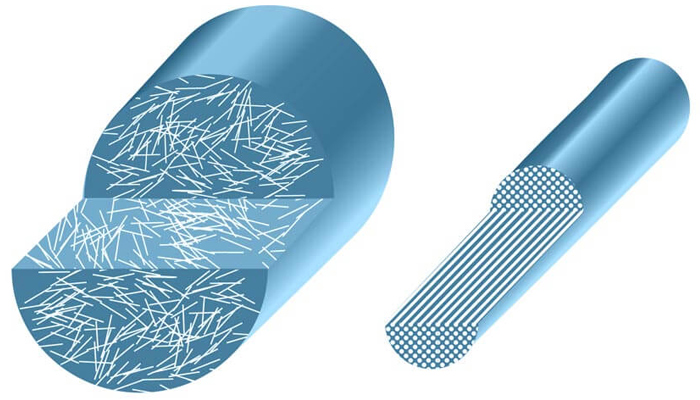
Diferencia en la disposición de las fibras cortas y continuas en la matriz. (Créditos: Coperion)
Si nos centramos en las características propias de los materiales reforzados, vemos que estas difieren mucho dependiendo del polímero utilizado como matriz y la elección del tipo de fibra. Obviamente, si el plástico base es de ingeniería, el compuesto tendrá propiedades más avanzadas que los que tengan plásticos estándar de matriz. Por ejemplo, si un compuesto tiene como polímero de matriz el polipropileno, tendrá de base una buena resistencia al desgaste, capacidad para absorber impactos y una mayor dureza y flexibilidad. Si por el contrario, se utiliza PLA, el compuesto será más fácil de imprimir, pero tendrá una tendencia mayor a la fractura debido a la baja resistencia del material.
En cuanto a los tipos de fibras que hay, tanto cortas como continuas, destacan principalmente tres: carbono, vidrio y aramida (Kevlar). Las fibras de carbono son las más utilizadas en la industria manufacturera, debido a la alta resistencia y rigidez que ofrecen a las piezas finales. Los refuerzos con fibra de vidrio son generalmente más asequibles y ofrecen también una buena resistencia, aunque no tanta como la de carbono. Por último, las fibras de Kevlar suelen usarse en chalecos antibalas por su alta resistencia al impacto y a los golpes. En cualquiera de los casos, el resultado de utilizar fibras de refuerzo, tanto cortas como continuas, será la obtención de piezas resistentes y ligeras.
El proceso de impresión 3D
La mayoría de las impresoras 3D capaces de procesar materiales compuestos se basan en el proceso de extrusión de polímeros. En lo que respecta a la impresión 3D FFF de fibras cortas, el proceso es el sencillo. Las fibras cortas se dividen en pequeños trozos que se mezclan con material plástico para formar una bobina de filamento que pueda utilizarse con impresoras 3D FFF. En este caso, las fibras simplemente se suspenden en el termoplástico, que se calienta y se extruye para formar la pieza capa a capa como cualquier otra pieza fabricada con esta tecnología. Sin embargo, se necesitará una boquilla endurecida para resistir las hebras abrasivas de las fibras.
La impresión 3D de compuestos con fibra continua, por otro lado, es un poco más compleja. En el proceso de extrusión del material, a menudo se requiere una segunda boquilla para depositar el troquel y la hebra de fibra continua por separado. Por otra parte, el cabezal de la boquilla única debe tener una construcción específica para mezclar la fibra con la matriz. El proceso consiste en colocar fibras continuas con una dirección específica dentro de la matriz. Ésta actúa como una carcasa que contiene las fibras de refuerzo. Para garantizar la adherencia de las fibras con la matriz, se suele utilizar una matriz o relleno a base de resina termoendurecible. A continuación, se polimeriza mediante luz ultravioleta o una fuente de calor para fusionar las capas y los materiales. Hay que decir que esta descripción es bastante genérica, ya que existen numerosas tecnologías patentadas para la impresión 3D de compuestos de fibra continua que difieren entre sí, aunque sólo sea ligeramente.
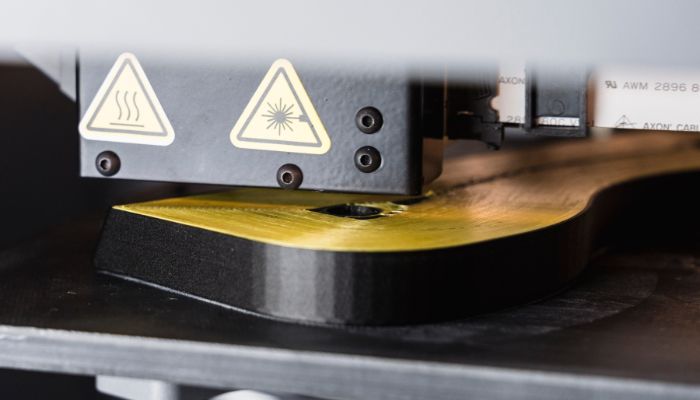
Impresión 3D de una matriz de polímero y refuerzo de fibra de Kevlar. (Créditos: Markforged)
Un aspecto importante a la hora de imprimir con fibras continuas, es el uso de software de análisis de elementos finitos (FEA). Se trata de un método informático para predecir cómo reaccionará un producto ante fuerzas y estímulos externos. Esto permite analizar las características de los materiales y definir con precisión el modelo según el cual deben disponerse las fibras continuas en la matriz. Por otro lado, esto implica cumplir ciertas limitaciones de diseño para priorizar el correcto posicionamiento de las fibras y, por tanto, el rendimiento de la pieza. Así, las propiedades específicas del material se definirán según un proceso controlado. Este no es el caso de los composites reforzados con fibras cortas, ya que con éstos no es posible controlar la cantidad y la posición de las fibras depositadas, representando un todo con la matriz.
Ventajas y limitaciones
Como sabemos, algunos de los principales beneficios de la impresión 3D con composites incluyen una mayor flexibilidad y velocidad de fabricación, así como la capacidad de crear piezas complejas en comparación con otros métodos más tradicionales. Además, otra ventaja que se puede observar con esta tecnología, siempre y cuando se utilicen fibras continuas, es que permite controlar el proceso de deposición y decidir dónde y cómo colocar el refuerzo para las piezas finales.
Si nos centramos en los beneficios de las fibras cortas y continuas como refuerzos en la impresión 3D, podemos encontrar algunos puntos en común. Ambos tipos de fibras proporcionan una resistencia mecánica superior en comparación con los plásticos no reforzados. Concretamente, mejoran la rigidez del material y aumentan su resistencia a la fatiga y al impacto. Además, las fibras como la de carbono son muy ligeras, lo que ayuda a mantener un peso bajo en aplicaciones donde esto es crítico. De igual forma, las fibras cortas y continuas comparten algunas limitaciones. Este es el caso de la necesidad de requerir de equipos especializados de impresión 3D para su correcta fabricación. Asimismo, hay muchos puntos a tener en cuenta a la hora de obtener el material compuesto, como por ejemplo, la adhesión entre la fibra y la matriz plástica, que puede suponer un desafío.
Por otro lado, hay algunos aspectos en los que ambos tipos de fibras pueden diferenciarse. La principal limitación de las fibras cortas en comparación con las continuas es que proporcionan un refuerzo menos efectivo. Esto se debe a que la orientación y distribución de las fibras cortas a lo largo del compuesto es más compleja, además de aleatoria, mientras que las continuas son constantes. Así, el efecto de refuerzo con fibras cortas es menos pronunciado, lo que puede no ser suficiente para aplicaciones que requieren alta resistencia. Sin embargo, una ventaja clave de las fibras cortas es que son más fáciles de procesar y generalmente más económicas que las fibras continuas, lo cual las hace más accesibles. Además, pueden ser utilizadas con una mayor variedad de plásticos, permitiendo una alta flexibilidad de diseño.
Principales aplicaciones
La elección entre fibras continuas y cortas, así como del plástico de matriz, dependerá del tipo de aplicación y de los requisitos de rendimiento. Las fibras continuas son ideales para aplicaciones que demandan alta resistencia y rigidez, mientras que las fibras cortas son más adecuadas para proyectos que buscan facilidad de procesamiento y un coste más bajo. Por esta razón, las fibras continuas suelen ser más utilizadas para componentes estructurales en industrias avanzadas, como la automotriz (refuerzos de chasis o componentes interiores) o la aeronáutica (estructuras de soporte y componentes en aviones). También pueden implementarse en productos de consumo que requieren alta resistencia, como bicicletas o equipamiento deportivo. Por su parte, las fibras cortas impresas en 3D suelen ser más utilizadas para prototipos y piezas decorativas. Asimismo, se suelen usarse para piezas en la industria del embalaje, la robótica, los productos de consumo y otros componentes donde la alta resistencia a la tracción no sea un aspecto vital.
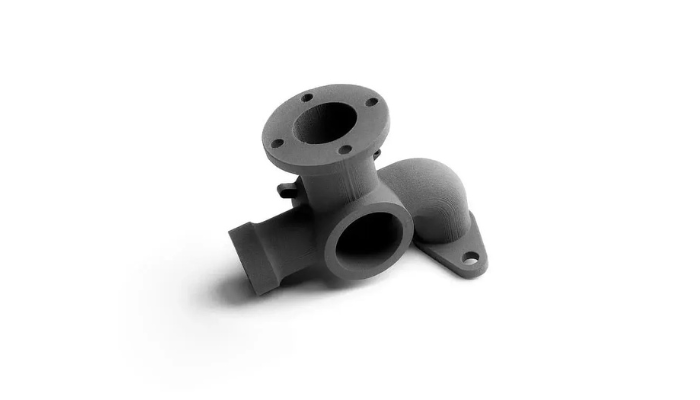
Pieza fabricada con fibra de carbono. (Créditos: Weerg)
Fabricantes y precio
Las soluciones de impresión 3D para materiales compuestos de fibras cortas y continuas, aunque no son tan numerosas como las de polímeros y metales estándar, son bastante variadas y van desde brazos robóticos a impresoras industriales o soluciones de escritorio.
Entre los proveedores de soluciones de impresión 3D de fibra continua, Markforged ofrece la tecnología Continuous Fibre Fabrication (CFF) y una gama de soluciones industriales y de escritorio. Estas son capaces de imprimir PLA, TPU, White Nylon, Onyx™ y compuestos ULTEM reforzados con fibra de carbono, Kevlar o fibra de vidrio. Anisoprint, por su parte, desarrolla máquinas industriales de impresión 3D de fibra continua con su tecnología por coextrusión de fibra compuesta (CFC). Las soluciones de escritorio permiten una amplia flexibilidad en la selección de materiales con un sistema abierto, mientras que la solución industrial ProM IS 500 es compatible con plásticos de alto rendimiento como PEI, PEEK, PEKK y otros. Otras empresas que cuentan soluciones de impresión 3D de fibra continua son Continuous Composites o CEAD, que ofrece una solución LFAM.
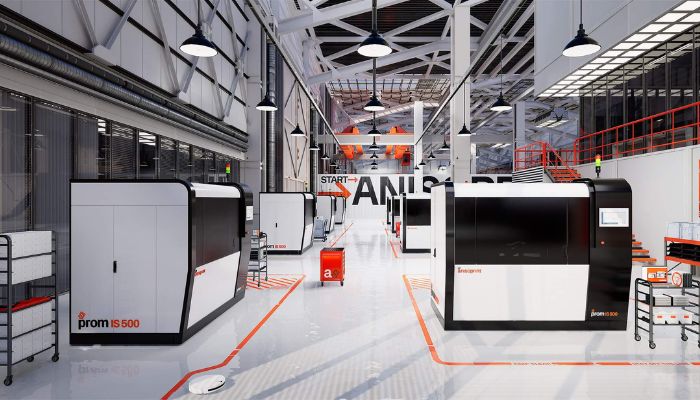
Créditos: Anisoprint
Además, como ya se ha mencionado, cada vez son más las startups que estudian y patentan nuevos procesos de impresión 3D para composites de fibra continua, entre las que se encuentran Moi Composites, SphereCube, Fabheads, 9T Labs y Arevo. Cabe mencionar que no sólo existen tecnologías para el refuerzo de fibra continua durante el proceso de producción. Por ejemplo, la startup española Reinforce 3D ideó la tecnología CFIP (Continuous Fibre Injection Process) para el refuerzo de piezas con fibras continuas en la fase de postratamiento, tras la fabricación aditiva. En cuanto a los fabricantes de impresoras 3D para materiales compuestos de fibras cortas, encontramos principalmente fabricantes de máquinas FDM capaces de procesar estos composites reforzados con fibra de carbono de alto rendimiento. Entre ellos se encuentran Roboze, Stratasys, 3ntr, miniFactory, BigRep, WASP o Creality (como vemos, la lista no es muy exhaustiva).
Si nos fijamos en los precios, la principal diferencia está relacionada con el tipo de máquina utilizada. Tanto para la impresión 3D de fibras cortas como para la de fibras continuas, el precio suele ser elevado en el caso de las soluciones industriales, ya que se trata de materiales que requieren condiciones de impresión especiales, como altas temperaturas para la boquilla, la cámara, etc. Las máquinas de escritorio para compuestos de fibra corta pueden costar a partir de 400 euros, mientras que las de impresión 3D de fibra continua rondan los 9.000 euros. En cuanto a las soluciones industriales, los fabricantes no siempre revelan sus precios, que pueden alcanzar varios cientos de euros según el proceso y el tamaño. En este caso, es posible solicitar presupuestos directamente a través de los sitios web oficiales de las empresas.
¿Qué piensas de la comparativa entre fibras continuas y cortas en la impresión 3D? Deja tus comentarios en nuestras redes sociales: Facebook, LinkedIn y Youtube. Sigue toda la información sobre impresión 3D en nuestra Newsletter semanal.