¿Por qué los fabricantes apuestan por la impresión 3D FFF de cerámica?

Desde su llegada al mercado de la fabricación aditiva en 2018, Nanoe se dedica a democratizar el uso de la impresión 3D FFF cerámica y de metal gracias a un proceso accesible y fácil de implementar. Además de que sus filamentos se han abierto paso en muchos centros de investigación alrededor del mundo, están ganando cada vez más terreno entre los fabricantes que apuestan por la integración de la fabricación aditiva en sus empresas. Los materiales cerámicos del fabricante francés ofrecen buenas propiedades térmicas, químicas y mecánicas que resultan interesantes para actividades exigentes como la soldadura orbital, la producción de piezas para calderas o la fabricación de piezas torneadas. Gracias a los filamentos Zetamix, varias empresas internacionales pueden aumentar su rendimiento reduciendo los tiempos de producción y el tiempo de inactividad de las máquinas, a la vez que reducen los costes.
Entre los usuarios de las soluciones de impresión 3D FFF cerámica de Zetamix se encuentran tres fabricantes destacados: MGB, SAPCO y Orbital Service. Ya que las tecnologías 3D ofrecen muchas ventajas hoy en día, los tres han optado por beneficiarse de las capacidades térmicas de los filamentos cerámicos, tanto de zirconia como de alúmina. Estos tres fabricantes tenían problemas concretos que eran difíciles de resolver mediante la fabricación sustractiva, o al menos con costes y tiempos mucho más elevados.
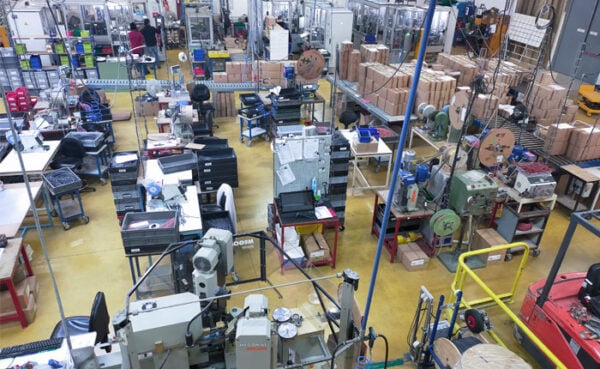
Cada vez son más los fabricantes que integran la fabricación aditiva. | Créditos: SAPCO
La alúmina, un material resistente a las altas temperaturas
MGB es una empresa francesa fundada en 1956 que se especializa en la fabricación de piezas torneadas para la industria de los conectores. Trabaja principalmente con empresas de los sectores médico, aeronáutico y electrónico que necesitan tornillos a medida. Estos tornillos tienen diferentes niveles de dureza, siendo la parte inferior del tornillo generalmente menos resistente que la superior. Para producir este tipo de tornillo a medida, MGB ha desarrollado una máquina especial que recuece la parte superior por inducción para proporcionar la dureza necesaria.
En esta máquina, MGB ha integrado una pieza impresa en 3D hecha de alúmina. Se trata de un soporte a medida perforado en el extremo en el que se coloca el tornillo en cuestión. Después, se calienta mientras un sensor térmico controla la temperatura. El reto estaba en encontrar una guía que aguantara una temperatura tan elevada, se adaptara perfectamente a la forma del tornillo y soportara la presencia del sensor eléctrico. Se trataba de un reto que no podría haberse superado tan rápidamente sin la integración de la fabricación aditiva. MGB afirma que el proceso de diseño y fabricación del nuevo porta tornillos duró menos de una semana. Este plazo de tiempo hubiera sido inimaginable si la empresa hubiera recurrido a la fabricación sustractiva o a un proveedor de servicios.
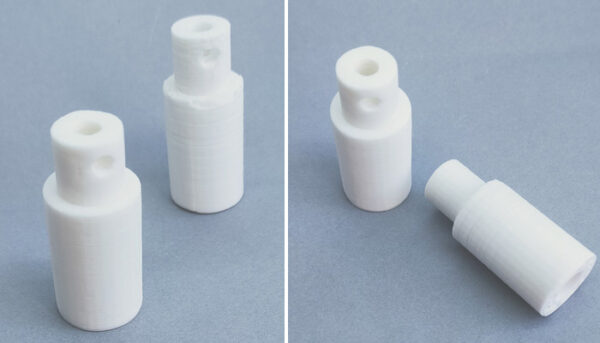
Los soportes para tornillos impresos en 3D. | Créditos: Nanoe
Mejorando los procesos de soldadura orbital con filamentos Zetamix
Orbital Service es una empresa alemana especializada en la soldadura orbital, que también ha confiado en la solución Zetamix para crear piezas a medida. En su actividad, las operaciones de soldadura TIG (gas inerte de tungsteno) plantean muchos retos, sobre todo a la hora de evitar la oxidación y la contaminación del aire. Para superar esto, la empresa debía crear un arco eléctrico y rociar un gas de protección inerte alrededor de la zona a soldar. Sin embargo, en la soldadura orbital, los tubos eran muy grandes y las boquillas de soldadura TIG no eran adecuadas. Esto favorecía la oxidación y el postratamiento de las piezas. La salida se ralentizaba y el proceso era poco fiable.
Aquí es donde la fabricación aditiva juega un papel fundamental. Orbital Service utilizó la tecnología FFF y los filamentos Zetamix, concretamente el de alúmina, para diseñar boquillas TIG a medida. Estas boquillas tienen una forma cóncava, mejor adaptada al volumen de los tubos a soldar. Esto reduce los defectos de soldadura y el consumo de gas inerte necesario. La empresa alemana eligió la alúmina por su resistencia a la temperatura, afirmando que todo el proceso de diseño y fabricación dura tan sólo una semana.
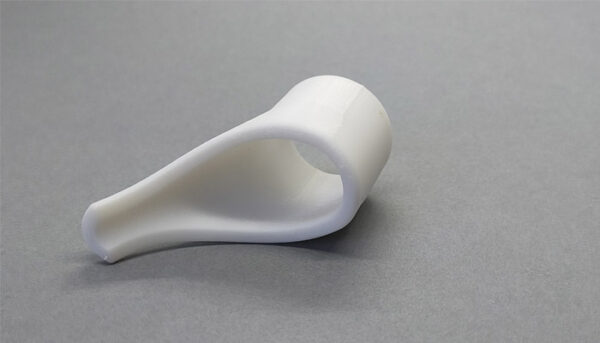
Mediante la fabricación aditiva, Orbital Service puede diseñar boquillas cóncavas más adecuadas. | Créditos: Nanoe
La solución Zetamix permite reducir el tiempo de mantenimiento
SAPCO fabrica electrodos cerámicos de encendido e ionización para su uso en calderas y quemadores industriales. Para ello, la empresa ha desarrollado procesos de producción automatizados con máquinas adaptadas a la fase de montaje. Sin embargo, el proceso de ensamblaje sigue siendo complejo. Durante la soldadura del electrodo, se colocan 2 obleas metálicas alrededor de la pieza, que se instalan mediante pasadores de soldadura de plástico. Estos se dañan rápidamente por la alta temperatura, lo que significa que la máquina se detiene al menos una vez al día. Este tiempo de inactividad afecta a todo el proceso de producción de SAPCO, lo que les obliga a encontrar otra forma de producir los pasadores.
En un principio, la empresa se planteó el uso del moldeo por inyección de cerámica, pero pronto se demostró que era poco práctico, caro y difícil de aplicar. Por ello, SAPCO recurrió a la fabricación aditiva de cerámica en lugar de usar polímeros. Se optó por el óxido de circonio, que puede soportar temperaturas de hasta 800°C. La solución de Zetamix fue fácil de implementar y utilizar. En 5 días, los equipos fueron capaces de diseñar y producir las piezas de soldadura optimizadas. Éstas deben cambiarse una vez al mes, lo que reduce considerablemente el mantenimiento y el tiempo de inactividad de la máquina.
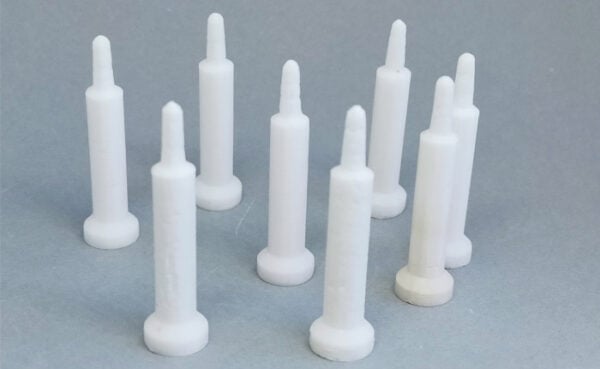
Los pernos de soldadura están impresos en 3D con circonio. | Créditos: Nanoe
Dando respuesta a los problemas del utillaje interno
Cuando se trata de producir herramientas internas, los fabricantes pueden confiar en la impresión 3D FFF de cerámica para ganar agilidad y aumentar su productividad. La elección de la cerámica permite que sectores como la aeronáutica, la automoción, la fundición o la joyería trabajen a temperaturas extremadamente altas y superen otras limitaciones químicas y mecánicas.
Por último, optar por las soluciones propuestas por Nanoe permite al usuario desplegar una oferta de bajo coste en comparación con otros procesos de fabricación. Más allá del precio, también es una cuestión de facilidad de uso. El proceso FFF es fácil de aprender y de integrar en las líneas de producción. Esto es especialmente importante cuando se trata del utillaje interno. La elección de la solución Zetamix es más adecuada que otros procesos como la fotopolimerización, que se preferirá para la fabricación de piezas muy precisas en el sector biomédico, por ejemplo. Puedes visitar el sitio web del fabricante francés para obtener más información sobre su gama de filamentos.
¿Qué piensas de la integración de la impresión 3D FFF de cerámica en la industria? Deja tus comentarios en nuestras redes sociales: Facebook, Twitter, Youtube y RSS. Sigue toda la información sobre impresión 3D en nuestra Newsletter semanal.