El papel de la fabricación aditiva en la automoción
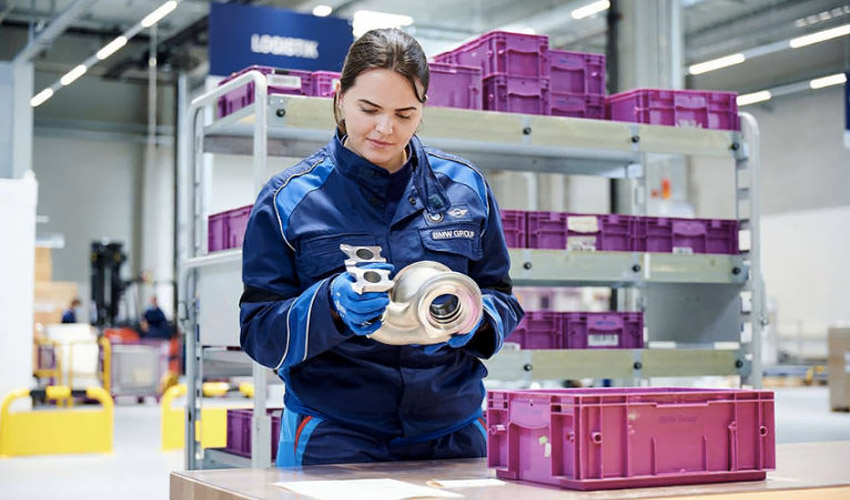
En la industria de la automoción, los OEM (en español, Fabricante de Equipo Original) han utilizado la fabricación aditiva para la creación rápida de prototipos. Sin embargo, recientemente los avances en esta tecnología han ido transformando las formas en que se diseñan, fabrican y distribuyen las piezas de uso final. El estudio de Deloitte, llamado 3D opportunity in the automotive industry, explica que actualmente las empresas no buscan alteraciones radicales ni en las cadenas de suministro ni en los productos. La impresión 3D se adopta para crear iteraciones de diseño, mejorar la calidad mediante la creación de prototipos rentable y crear piezas de herramientas específicas. Sin embargo, existen otras rutas de la fabricación aditiva en la automoción, que transforman los productos y las cadenas de suministro de forma más radical. De hecho, el informe de SmarTech Analysis reveló que para 2029, la impresión 3D automotriz generará $9 mil millones en ingresos con la producción de piezas de uso final, en comparación con los $1,39 mil millones de 2019. Entonces, ¿hacia dónde se dirige la impresión 3D en este sector?
Beneficios de la preproducción
Acelerar la fase de diseño en el desarrollo de nuevos productos es clave en cualquier industria. Afortunadamente, la impresión 3D puede reemplazar la producción CNC costosa y de larga duración en esta fase. Concretamente, permite a los diseñadores pasar de manera rentable por varias iteraciones antes de decidirse por el producto final. Para ello, una vez que los diseñadores han identificado una necesidad del usuario y han generado ideas para satisfacerla, desarrollan un prototipo. La siguiente etapa es probarlo para mejorar su diseño. Este proceso iterativo es también lo que llamamos creación rápida de prototipos.
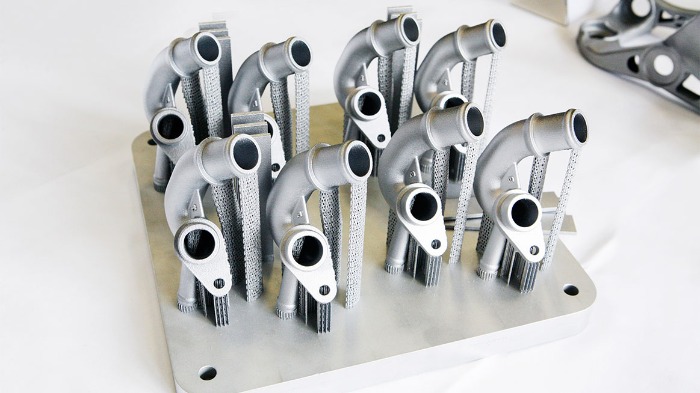
Muestra de conectores de agua impresos en 3D de metal para el motor Audi W12 | Créditos: Volkswagen AG
Volkswagen, por ejemplo, ha estado trabajando con tecnologías de impresión 3D durante los últimos 25 años, y en 2020 invirtió en dos impresoras 3D Stratasys más. Peter Bartels, director del centro de pre-serie de Volkswagen, comentó que estas inversiones representan “capacidades adicionales que fortalecen las operaciones de impresión 3D y permiten optimizar aún más el proceso de diseño”. Además, el diseño de herramientas (agarres, plantillas y accesorios) también se puede optimizar y producir a un coste menor. Las herramientas juegan un papel importante en la línea de ensamblaje para crear productos en serie y de alta calidad. Estas aplicaciones son lo que Deloitte llama la ruta estándar actual de la fabricación aditiva en la automoción.
El segmento creciente de piezas para uso final
Además, varios OEM han apostado por la impresión 3D para desarrollar piezas de uso final, yendo más allá de las aplicaciones de prototipos rápidos. Esto se debe a la búsqueda de innovación de productos en un sector competitivo como el automotriz. Una forma de lograr la innovación de productos es aumentar drásticamente el rendimiento de una pieza, reduciendo su peso, por ejemplo. La innovación de productos a través de la personalización también es de gran interés, especialmente para los automóviles de lujo.
Además, una ventaja de usar la impresión 3D es la producción potencial de piezas más ligeras para que los vehículos consuman menos combustible. Así, el papel del software de diseño industrial es fundamental. A lo largo de los años, las soluciones CAD y CAM han mejorado drásticamente, especialmente para la fabricación aditiva. A menudo incluyen herramientas de diseño generativo, optimización topológica y generación de celosía, que reducen el peso total de las piezas mientras mantienen o mejoran su función. Las piezas más ligeras suelen ser más complejas, sin embargo, esto no constituye un desafío para la fabricación aditiva. Cabe señalar que la simplificación de piezas también es posible gracias a impresión 3D, mediante la consolidación de varias piezas en un solo diseño. Por lo tanto, la complejidad del ensamblaje podría reducirse si fuera necesario producir un gran volumen de estas piezas.
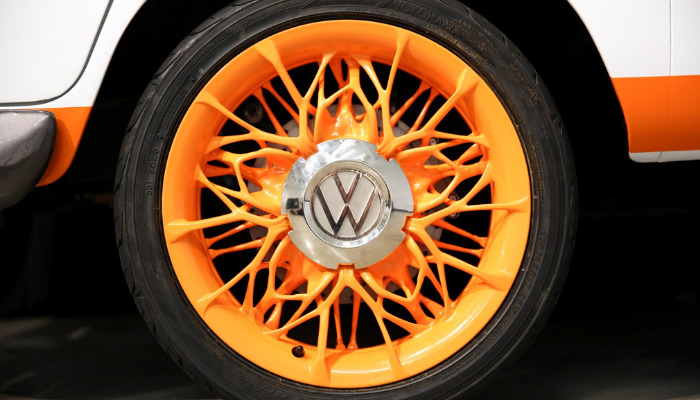
Las herramientas de diseño generativo de Autodesk ayudaron a diseñar ruedas más ligeras en un microbús Volkswagen 1962 Tipo 2 de 11 ventanas
La tecnología 3D también significa mayores posibilidades de personalización. De hecho, algunos fabricantes de automóviles de lujo ya la utilizan para ofrecer diseños especializados según los requisitos del cliente. En este sentido, los métodos de fabricación tradicionales no podrían ofrecer piezas únicas en plazos de entrega competitivos. El coste de producir tales piezas también sería considerablemente diferente. Además, la personalización también se puede utilizar para entregar repuestos, por ejemplo, para reparar un modelo de automóvil más antiguo.
Un ejemplo de aplicación para uso final es el colector de admisión de aluminio impreso en 3D por Ford (parte del motor que suministra la mezcla de combustible y aire a los cilindros), que se instaló en un Hoonitruck de 1977. Según el fabricante, esta fue la pieza de repuesto impresa en 3D para automóviles más grande jamás creada. Se tardaron cinco días en imprimirla con el Concept Laser X LINE 2000R, de GE Additive. Históricamente, Ford es una de las empresas que más investigaciones ha realizado en la industrialización de la fabricación aditiva. Además, en 1986, ya había invertido en una solución SLA. La empresa declaró: “No pasó mucho tiempo para ver que el invento podía utilizarse para crear nuevos diseños de prototipos de forma más rápida y eficiente que nunca”. En la actualidad, la empresa ha impreso más de 500.000 piezas y ha ahorrado miles de millones de dólares y horas de trabajo. En su Advanced Manufacturing Center de Detroit, ha invertido en impresoras 3D FDM, SLS y de arena.
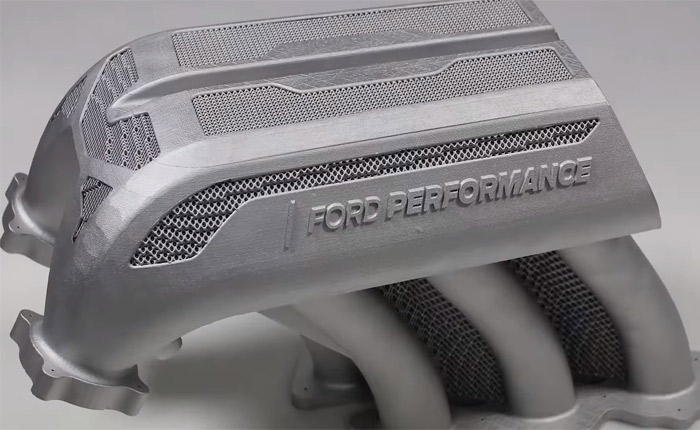
Colector de admisión de aluminio impreso en 3D| Créditos: Ford
Otro ejemplo es el grupo BMW, que en 2020 abrió un Campus de Fabricación Aditiva, no lejos de Múnich. Actualmente, opera alrededor de 50 sistemas industriales para procesar metales y plásticos. La creación de prototipos, piezas en serie, I+D y la formación de los asociados en la fabricación sin herramientas se llevan a cabo en las instalaciones. Esta inversión demuestra la confianza de BMW en las tecnologías de impresión 3D. Al igual que otros fabricantes de automóviles, el grupo apostó por la fabricación aditiva en 1991 para realizar prototipos conceptuales. Posteriormente, se produjeron pequeñas series de piezas para coches de carrera DTM, el Rolls-Royce Phantom, el BMW i8 Roadster y el MINI, entre otros. En un año, se imprimieron en 3D alrededor de 300.000 piezas. El miembro de la junta, Milan Nedeljković, comentó: “La fabricación aditiva ya es una parte integral de nuestro sistema de producción mundial hoy en día, y una parte establecida de nuestra estrategia de digitalización. En el futuro, las nuevas tecnologías de este tipo harán que la producción sea aún más rápida y nos permitirán beneficiarnos aún más del potencial de la fabricación sin herramientas”.
El cambio en la cadena de suministro
El estudio de Deloitte también señala que los cambios mencionados anteriormente afectarán en última instancia a las cadenas de suministro. Hoy en día, los OEM subcontratan la mayoría de sus piezas. El informe explica: “A medida que los OEM adoptan la ruta de evolución del producto, el resultado final será doble: cadenas de suministro más pequeñas y mayor contribución de valor de los OEM. Un efecto importante de la fabricación aditiva puede acortar y simplificar las enormes cadenas de suministro en la automoción que operan actualmente. Los OEM trabajan con miles de proveedores para obtener los diferentes componentes de los automóviles, y constantemente buscan formas de recortar sus cadenas de suministro”. Por lo tanto, las empresas pueden aprovechar la impresión 3D para transformar las cadenas de suministro, produciendo localmente y reduciendo el inventario de piezas.
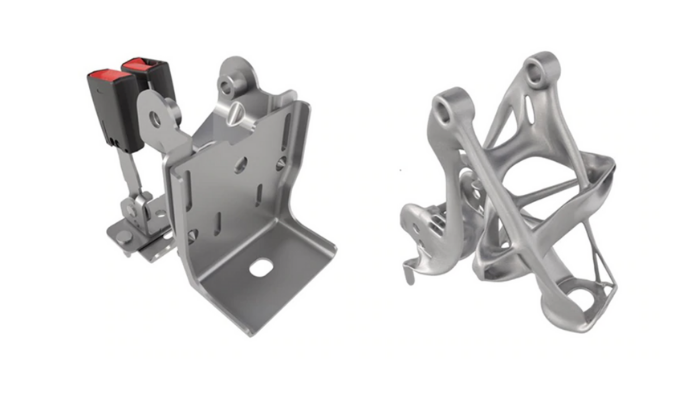
Utilizando el diseño generativo y la fabricación aditiva, General Motor pudo consolidar los ocho componentes diferentes de un soporte de asiento en una sola pieza impresa en 3D.
Desarrollo de materiales
A lo largo de los años, las mejoras en la tecnología de materiales han permitido que se califiquen más materiales para el proceso de fabricación aditiva. Las piezas de automóviles se fabrican normalmente a partir de polímeros de alto rendimiento, termoplásticos reforzados y metales. Los OEM han buscado activamente incorporar materiales más ligeros como fibra de carbono y aluminio en la carrocería del vehículo. Por lo tanto, los materiales diseñados para la fabricación aditiva pueden permitir la integración de un mayor número de propiedades en las piezas finales, pero también en el desarrollo de prototipos funcionales.
Por ejemplo, BASF Forward AM está trabajando junto con sus clientes y fabricantes de hardware para desarrollar productos innovadores mediante la adopción de la fabricación aditiva. Con Daimler, diseñaron un nuevo soporte de motor para reducir la transmisión de vibraciones con el fin de maximizar la comodidad de los pasajeros. La necesidad de ciclos de desarrollo más cortos y menores costes ha puesto bajo presión este proceso de diseño tradicional y los materiales. Forward AM eliminó el costoso requisito de nuevos moldes con cada modificación de diseño al integrar las tecnologías 3D en el proceso. El desafío era cumplir con los estrictos requisitos de rendimiento térmico y mecánico en condiciones de prueba. Para ello necesitaban un material muy rígido y térmicamente estable. La combinación perfecta fue Ultrasint PA6 MF (una poliamida 6 rellena de mineral que supera a PA11 y PA12), que produjo prototipos finales en menos de 48 horas. Aunque el diseño de la pieza impresa se veía diferente, se podía usar como el original, como un prototipo completamente funcional en la etapa de desarrollo cuando no se encontraba disponible ninguna pieza de moldeo por inyección. Por lo tanto, encontrar el reemplazo de material adecuado para reproducir el rendimiento de la pieza moldeada por inyección fue clave.
¿Cuál es el futuro de la fabricación aditiva en la automoción?
En los últimos años, los fabricantes de automóviles han tenido que explorar nuevos modelos comerciales para lograr el crecimiento. En el informe de tendencias de la industria automotriz de Jabil, afirma que el 71% de las empresas automotrices tienen un cronograma de lanzamiento al mercado de menos de 2 años. Muchos miran hacia nuevas tecnologías, incluida la fabricación aditiva, para mantener ciclos de desarrollo cortos y lograr costes más bajos. La creación de vehículos eléctricos también es de gran interés, con aproximadamente el 50% de los fabricantes de automóviles que aspiran a ser líderes del mercado de vehículos totalmente eléctricos (EV) en un futuro próximo. A medida que la industria se aleja de los motores de combustión interna, la impresión 3D surge como una solución que puede acelerar el desarrollo de piezas más ligeras para vehículos eléctricos. De hecho, el aligeramiento es fundamental para los vehículos eléctricos porque afecta directamente a la duración de la batería.
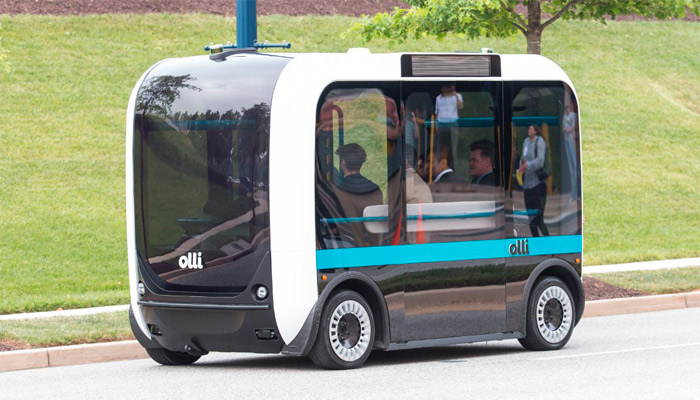
Olli, el minibús impreso en 3D.
Hace tiempo os hablamos de Olli, un minibús eléctrico autónomo impreso en 3D diseñado por Local Motors. El fabricante afirma que alrededor del 80% de las piezas se fabricaron en 3D, lo que redujo el tiempo total de producción en un 90%. La velocidad está limitada a 40 km/h, lo que hace que Olli sea adecuado para centros urbanos, campus universitarios y hospitales. Antes de eso, Local Motors había presentado el roadster Strati, un biplaza eléctrico con 75% de piezas impresas en 3D.
Además, a medida que aumenta la demanda de vehículos conectados, también aumenta la necesidad de dispositivos electrónicos, como sensores y antenas dentro del vehículo. Con este aumento surge una mayor necesidad de diseñar y producir componentes electrónicos más pequeños y complejos. Basado en tecnologías de impresión 3D a micro y nanoescala, es posible diseñar componentes electrónicos más complejos internamente que se pueden incrustar directamente en el vehículo. La impresión 3D electrónica puede reducir los costes y el tiempo de desarrollo para crear estos dispositivos.
Como se mencionó anteriormente, la personalización ofrece muchas posibilidades en este ámbito. Por ejemplo, los clientes de MINI actualmente tienen la oportunidad de personalizar sus vehículos diseñando la banda lateral del lado del pasajero en la cabina y las inserciones laterales. También en sus diversos proyectos, BMW Group ha impreso en 3D más de 140.000 componentes. Christian Reinhardt, parte de BASF Forward AM desde 2019, comentó: “En mi opinión, una de las aplicaciones más emocionantes e importantes fue el proyecto MINI Yours Customized. Este proyecto demostró que es posible tener una pieza impresa en 3D en un automóvil de serie real, y que la individualización específica del cliente podría agregar un valor nunca antes visto. Estoy convencido de que este proyecto se convertirá en un pionero de muchas aplicaciones futuras”.
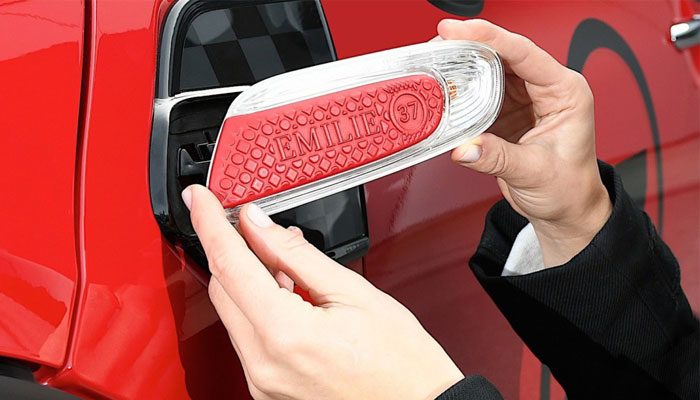
Gracias a la impresión 3D, el MINI puede ser personalizado por los clientes.
Más globalmente, casi todas las empresas del mercado están invirtiendo en tecnologías de impresión 3D para pasar a la producción de piezas más complejas y de alto rendimiento. Kevin Quinn, director de diseño y fabricación aditiva de General Motors, explica: “En promedio, hay 30.000 piezas en cada vehículo, pero no pretendemos imprimir en 3D todas ellas. En cambio, estamos siendo muy realistas. Estamos enfocados en oportunidades de producción donde podemos brindar un valor comercial para GM y para el cliente”. Por lo tanto, más allá de mejorar las capacidades generales de fabricación y reducir los costes, que ha sido la principal aplicación en el sector, los OEM están comenzando a aprovechar la tecnología 3D para crear nuevos productos y permitir la transformación de la cadena de suministro.
¿Qué piensas de la fabricación aditiva en el sector de la automoción? Deja tus comentarios en nuestras redes sociales: Facebook, Twitter, Youtube y RSS. Sigue toda la información sobre impresión 3D en nuestra Newsletter semanal.
[…] vez más, la industria automotriz y la fabricación aditiva han unido fuerzas en un mismo proyecto. Como parte del programa NISMO Heritage Parts de Nissan, […]
[…] en el nuevo MINI Cooper SE. Se suma así a las numerosas iniciativas ya desarrolladas en el sector de la automoción junto a la fabricación aditiva. El campeonato mundial de Fórmula 1 comenzó el pasado domingo y […]
[…] en el sector automotriz? Para abordar este tema y conocer el proceso de implementación de la fabricación aditiva en la automoción, 3Dnatives presenta su siguiente webinar: «Integrar la tecnología 3D en la adaptación de […]