¿Cómo evitar errores en la tecnología 3D de fusión láser por lecho de polvo?
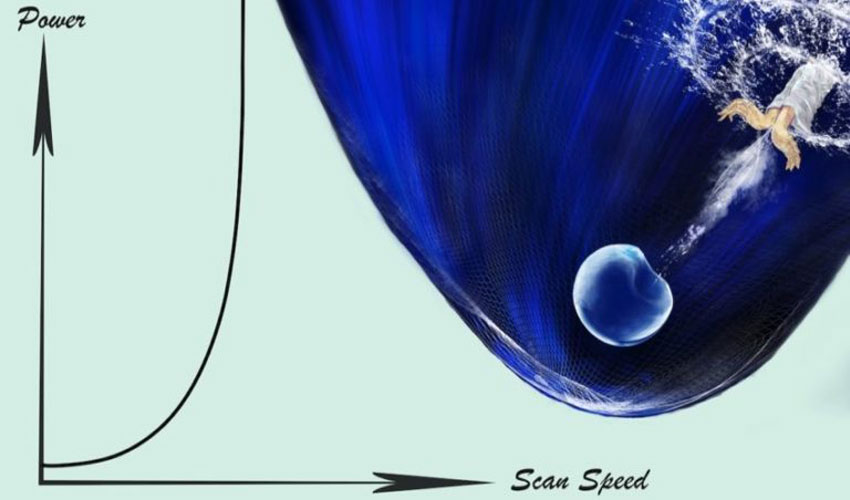
Investigadores de la Universidad Carnegie Mellon, en Pensilvania, han descubierto una forma de evitar defectos y aumentar la durabilidad y resistencia a la corrosión de las piezas metálicas producidas por la tecnología de fusión láser por lecho de polvo. La investigación se centró principalmente en comprender cómo y por qué se desarrollan debilidades estructurales durante el proceso de impresión 3D, y en extraer una solución a partir de esa información. El resultado de sus descubrimientos fue que es posible reducir la probabilidad de errores y así mejorar la integridad estructural del producto final aumentando la velocidad y restringiendo el calor de la fusión láser.
La fusión láser por lecho de polvo utiliza una plataforma de construcción que contiene material en polvo, ya bien sea polímero o metal, para la fabricación aditiva de una pieza. No fue hasta la década de 1990 que varias empresas comenzaron a explorar el uso de esta tecnología para metal. Las partículas de polvo de metal se fundían utilizando una fuente de calor como un láser o un haz de electrones para formar una pieza más o menos compleja, capa por capa. Actualmente es el proceso de fabricación aditiva de metal más utilizado. Además de ser ideal para crear piezas con geometrías complejas, los modelos tienen durabilidad y resistencia a la corrosión limitadas.
Cuando un láser de alta potencia y baja velocidad derrite el polvo metálico, se pueden crear cavidades circulares durante el proceso de impresión 3D. Esto ocurre bajo ciertas condiciones en las que la profundidad del baño fundido está controlada por la evaporación del metal en contraposición a la conducción de calor en el material sólido subyacente. La evaporación del metal puede crear surcos de vapor estrechos y profundos, conocidos como «cerraduras». Se trata de pequeñas burbujas o poros que se convierten en defectos estructurales perjudiciales si quedan atrapados en el metal solidificado. Los orificios de las cerraduras producen porosidad, lo cual degrada el rendimiento de la aleación, especialmente las propiedades de fractura.
El equipo examinó los orificios con imágenes de rayos X brillantes de alta energía, basándose en la investigación que cuantificó el fenómeno en cuestión. Descubrieron que las inestabilidades son causadas por fluctuaciones en la profundidad del ojo de la cerradura y aumentan fuertemente al disminuir la velocidad de escaneo y la potencia del láser en el lado inestable del límite. Estas fluctuaciones generan ondas acústicas en el metal líquido que fuerzan a los poros a salir del ojo de la cerradura y luego los atrapan en el metal resolidificante.
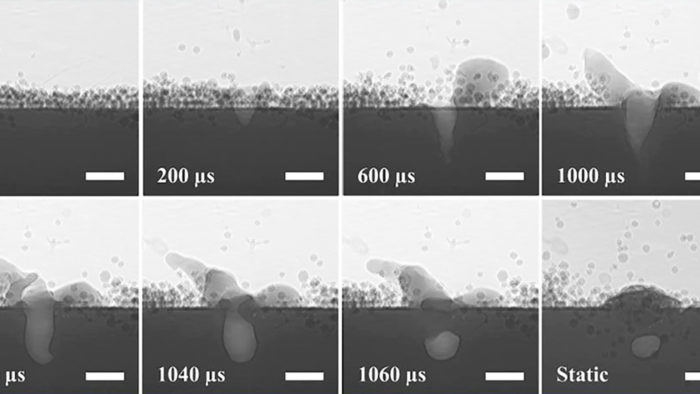
Imágenes de rayos X de alta velocidad captando la formación de defectos | Créditos: Laboratorio Nacional de Argonne
Según Anthony D. Rollett, profesor de ciencia e ingeniería de materiales en la Facultad de Ingeniería, “el valor práctico real de esta investigación es que podemos ser precisos al controlar las máquinas para evitar este problema”. La solución, entonces, es definir una velocidad mínima y un calor máximo. “Se puede pensar en el límite como un límite de velocidad, excepto que es lo opuesto a conducir un automóvil. En este caso, se vuelve más peligroso a medida que avanza más lento. Si está por debajo del límite de velocidad, es casi seguro que está generando un problema”, agrega Rollett, “Mientras permanezca fuera de la zona de peligro, el riesgo de error es bastante bajo”. Puedes leer el informe completo AQUÍ.
¿Qué piensas de los errores en el método fusión láser por lecho de polvo?? Deja tus comentarios en nuestras redes sociales: Facebook, Twitter, Youtube y RSS. Sigue toda la información sobre impresión 3D en nuestra Newsletter semanal.