Cramik y el desarrollo de cerámicas de ingeniería para fabricación aditiva
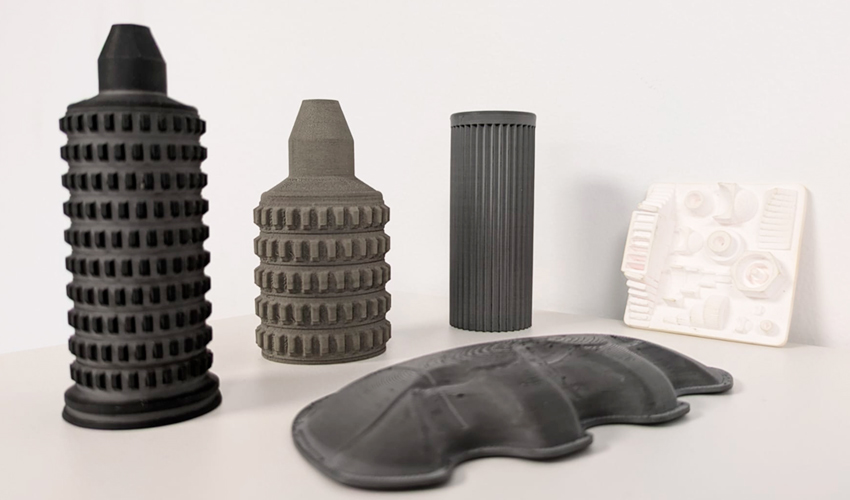
En un mundo en constante evolución tecnológica, especialmente en la Industria 4.0, muchas empresas en el ámbito de la fabricación aditiva apuestan por avanzar en la investigación de nuevos materiales. En España, Cramik se destaca como un pionero en el desarrollo de cerámicas de ingeniería compatibles con la impresión 3D. En esta entrevista, exploramos la visión de la empresa, sus materiales y las tecnologías con las que se pueden utilizar, así como algunos casos de éxito y los sectores objetivo a los que se dirigen. Hemos hablado con Alberto Santana, de Cramik, para descubrir cómo están redefiniendo el panorama de las cerámicas avanzadas aplicadas a las nuevas tecnologías.
3DN: ¿Puedes presentarte y contarnos tu relación con la impresión 3D?
Me llamo Alberto Santana y mi relación con la impresión 3D comenzó cuando a los 19 años asistí a un taller de “electrónica Creativa” dentro de mi Universidad, donde nuestro profesor en aquel entonces nos enseñaba nuestros primeros pasos en prototipado sencillo, con una Prusa, (de las que no se nivelaban automáticamente). Desde entonces me picó el gusanillo de la aditiva y he tenido diversas oportunidades de desarrollándome con el paso de los años en las distintas tecnologías tanto en formato filamento como polvo sinterizable. He pasado tanto por la fase de imprimir figuritas para amigos en PLA como por la de cruzarme media Europa haciendo piezas funcionales en materiales más avanzados en polímero y metal, como la cerámica técnica en la que nos hallamos actualmente sumergidos.
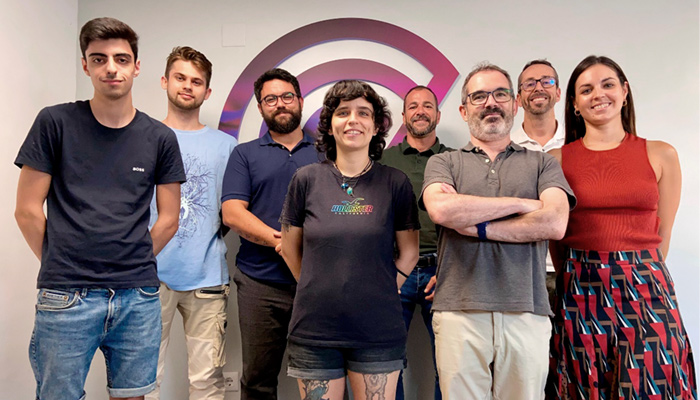
El equipo de Cramik
3DN: ¿Qué es Cramik y cómo surgió la idea de crear empresa?
CRAMIK es una pequeña compañía de grandes ideas, surgida como spin off de un departamento de investigación de materiales universitario allá por el 2018. Esta iniciativa desarrolló una patente de un binder polimérico capaz no solo de albergar altas cargas cerámicas o metálicas, sino que además permitía realizar de-binding y tratamiento térmico aplicando sólo calor, sin presencia de químicos agresivos. Una de las aplicaciones clave fue, el almacenamiento energético, en el cual se desarrolló una primera prueba de concepto de material con carga cerámica capaz de almacenar pequeñas cantidades de energía en ciclos de carga y descarga. El potencial de esta fórmula patentada sirvió de chispa para que una firma de Private Equity situada en Madrid BEABLE CAPITAL SGEIC, S.A. creyera en el potencial de este proyecto, apoyándolo con una inversión inicial y marcando el nacimiento de la compañía (anteriormente denominada Laboratorio Print3D Solutions CLM).
El enfoque a partir del 2020 empezó a mirar hacia el extranjero en busca de retos y aplicaciones de altas prestaciones en la que la anterior CEO, Ines Leopoldo Merino lideró la compañía durante un importante periodo de lucha y sacrificio con el apoyo de Ines Blanc Acebal (R&D director). En 2021 cambia su localización a unas acogedoras instalaciones dentro del Parc Cientific de la Universidad de Valencia en Burjassot, donde el esfuerzo principal se centraba en encontrar la estabilidad de las formulaciones de materiales y afianzar la patente en diversos territorios con el apoyo y experiencia del nuevo CTO José Antonio Reglero Ruiz.
A partir del año 2022, yo me incorporo al equipo de la compañía como siguiente CEO y BD Manager para el período de escalado de la compañía, cambiando nuestras instalaciones durante 2023 a una nueva localización donde se alberga nuestra planta piloto, en parque empresarial táctica, Paterna. Desde Inicios del 2024 la compañía ha recibido tanto un nuevo apoyo de su anterior inversor como la incorporación de CDTI INNVIERTE a su estructura, afianzando la apuesta por el potencial de su tecnología, y fortaleciendo además su equipo directivo con un nuevo director financiero Antonio Sanchis y un apoyo estructural de estrategia interino personificado por Jose María Ferrándiz. También hacer una mención a nuestro equipo de procesos formado por Estefania Lara, Adrián Sanchez, y Sebastian Szafranski, sin los cuales nuestros progresos no hubieran sido posibles.
3DN: ¿Qué variedad de materiales desarrolláis? ¿Con qué tecnologías de fabricación son compatibles?
Debido a la versatilidad de nuestra formulación patentada, es posible desarrollar una variedad prácticamente ilimitada de materiales cerámicos, fundamentalmente centrados en aplicaciones de altas prestaciones (resistencia térmica y propiedades estructurales). Entre los materiales que trabajamos, podemos incluir la alúmina, el óxido de silicio, dióxido de titanio o cerámicas denominadas UHTC (Ultra-High Temperature Ceramics), tales como Carburo de Silicio, actualmente muy demandadas por sectores de defensa o aeronáutico.
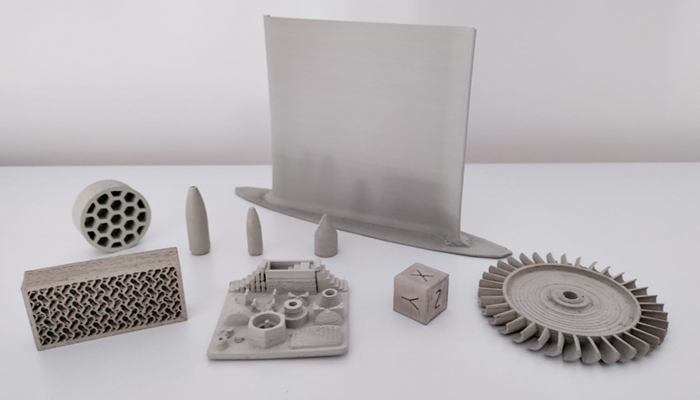
La empresa cuenta con una amplia variedad de cerámicas técnicas compatibles con la impresión 3D.
Otra de las líneas en las que trabajamos se centra en cerámicas con propiedades de almacenamiento energético, fundamentalmente electrodos y electrolitos cerámicos para ser capaces de imprimir de manera sencilla baterías de Litio duraderas y ligeras. Las tecnologías de fabricación que abordamos son fundamentalmente a partir de fundido, ya sea LDM, FDM o impresión a partir de pellets. Sin embargo, estamos evaluando emplear nuestros materiales en procesos de inyección cerámica y coating o pulverizado, para reforzar propiedades en superficies determinadas.
3DN: ¿Puedes contarnos brevemente un caso de éxito de vuestras cerámicas utilizadas con la impresión 3D?
Dentro de los procesos de validación de materiales, estamos trabajando con proveedores de polvo cerámico que quieren incluir la aditiva dentro de sus tecnologías de fabricación, de cara a ofrecer a sus clientes alternativas diferentes a los procesos tradicionales de obtención de piezas cerámicas. Recientemente hemos llegado a un primer acuerdo con el productor de carburo de silicio más importante del mercado, FIVEN NORGE (Grupo Kymera) para poder combinar nuestra tecnología y sus polvos cerámicos en un producto común que ofrecer al mercado. Los resultados de esta colaboración se expondrán como caso de estudio en la próxima reunión de la “Ceramic Applications Society” en Dresden, uno de los foros más especializados del mundo cerámico, y que engloba a los principales actores del sector.
3DN: ¿Cuáles son los sectores a los que se dirigen vuestros desarrollos?
Principalmente a aquellos que tienen retos en impacto, abrasión y muy altas temperaturas. Para que os hagáis una idea, un polímero cargado standard podría aguantar los 100-250ºC de operación dependiendo de las condiciones. Algunos con carga metálica además de esto, también disponen de una buena resistencia a la abrasión, lo que ocurre es que cuando la aplicación necesita valores de impacto o temperatura superiores a los 1500ºC, ahí entramos nosotros. Dicho esto, nuestro valor añadido es claro en defensa, aeroespacial, energía y útiles de medicina compatibles. La particularidad de nuestro material es que nuestro binder polimérico es tan versátil que estamos iniciando pruebas en sector del moldeo por inyección, con bastante potencial o incluso en casos de aplicaciones en coatings de protección, por lo que nuestro abanico está creciendo gradualmente.
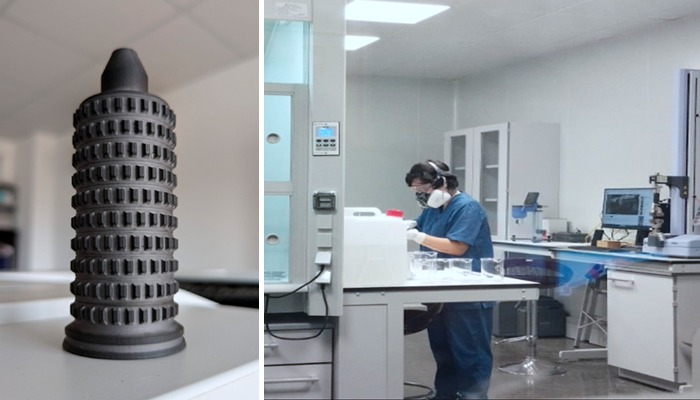
Sus campos de aplicación incluyen defensa, aeroespacial, energía y médico, entre otros.
3DN: ¿Cómo ves el futuro de la impresión 3D en España?
Los profesionales y empresas que se subieron al “carro del hype” estarán empezando a ver que no es oro todo lo que reluce, y que la aproximación debe ser hacia problemas de valor añadido, en los que el cliente tenga una fricción real a solventar. España en general dispone de un muy buen fondo de profesionales y técnicos dentro de los sectores químicos, físicos y de ingeniería (Naval, Mecánica, Industrial, Química, Producto…) pero por desgracia no hay una educación avanzada en lo que a diseño se refiere, que esté realmente al tanto de todas las posibilidades que ofrece la fabricación aditiva, y caemos en la tarea repetitiva de «dar clase al cliente, para que sea consciente de las posibilidades de fabricación que ignora”.
Respecto a la experiencia en máquinas y fabricantes también hay músculo de ingeniería y poco a poco ciertas empresas con margen de maniobra financiero empiezan a entender y crear su propio conocimiento en las distintas tecnologías disponibles con vistas a oportunidades en el extranjero. Si hablamos desde el punto de vista de los materiales primero vino el polímero simple, luego las cargas, después el metálico y lo siguiente es el cerámico.
Luego está la barrera generacional, y es que hay determinados puestos ocupados por perfiles de decisión que , simplemente por deformación profesional, o falta de conocimiento no pueden transmitir correctamente las posibilidades que le ofrece la fabricación aditiva dentro de sus respectivos departamentos. La clave estará en todos los profesionales que ahora están en montaje e imprimiendo, que irán creciendo y que tras ocupar puestos de responsabilidad, si han tenido experiencias satisfactorias, esos serán los verdaderos clientes. El futuro es optimista y creo que tras alguna que otra adquisición por aquí o joint venture por allá, la industria se acabará consolidando y el pastel se repartirá entre los que realmente aporten valor en conocimiento y solucionen a retos reales y nuevos productos customizados.
3DN: ¿Unas últimas palabras para los lectores?
Que no pierdan la ilusión frente a la adversidad, que disfruten el camino, aunque sea accidentado, porque si fuera fácil ya se habría realizado. Pueden encontrar más información en nuestro sitio web, aquí.
¿Qué piensas de los materiales desarrollados por Cramik? Deja tus comentarios en nuestras redes sociales: Facebook, LinkedIn y Youtube. Sigue toda la información sobre impresión 3D en nuestra Newsletter semanal.
*Créditos de todas las fotos: Cramik