BMW utiliza la impresión 3D para fabricar pinzas robóticas más ligeras y resistentes
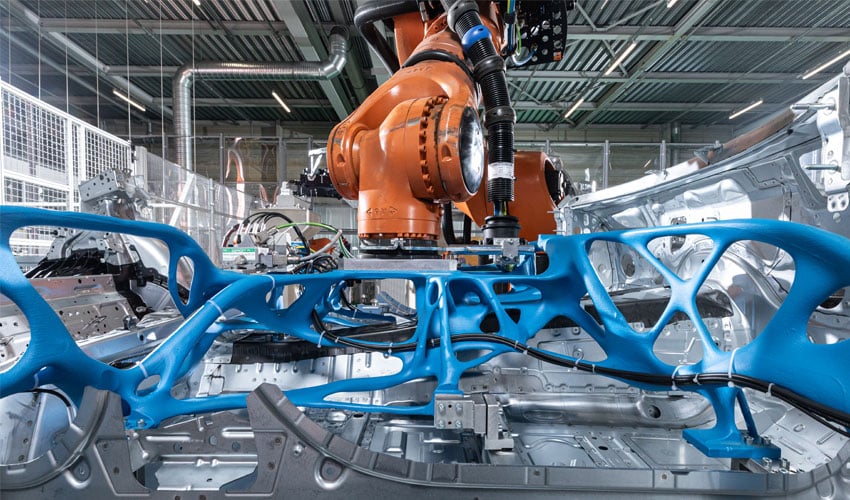
La fabricación aditiva se ha convertido en un proceso de producción por separado en el Grupo BMW. Desde hace más de 30 años, el fabricante de automóviles utiliza la impresión 3D para fabricar piezas de autos, herramientas, instrumentos de trabajo y para formar a sus empleados. El Additive Manufacturing Campus de Oberschleißheim desempeña un papel fundamental en este desarrollo. El año pasado, se imprimieron allí más de 300,000 piezas mediante diversos procesos. Recientemente, en el mismo centro, el fabricante alemán presentó unas pinzas robóticas XXL impresas en 3D que se instalaron en una prensa para la producción de los techos de polímero reforzado con fibra de carbono (CFRP) los autos de la marca.
Esta pinza robótica pesa unos 120 kilogramos y tarda 22 horas en imprimirse. Gracias al proceso de fabricación aditiva, el producto final es un 20% más ligero, lo que repercute positivamente en la vida útil de esta extensión. Durante el proceso de fabricación se combinaron juiciosamente dos procesos. En primer lugar, la tecnología SLS se utilizó para fabricar las pinzas de vacío y las pinzas de aguja utilizadas para levantar el CFRP. La cubierta de gran superficie y la estructura de soporte se fabrican por modelado por deposición fundida, concretamente mediante Large Scale Printing (LSP). Al utilizar pellets de inyección fabricados a partir de plástico reciclado, este proceso es especialmente adecuado para la fabricación económica y sostenible de grandes piezas. El resultado es una reducción del 60% de las emisiones de CO2 durante la fabricación de la pinza.
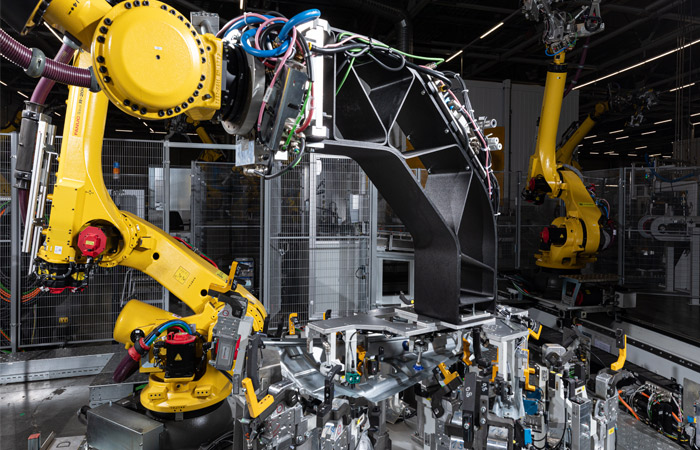
Ejemplo de una pinza robótica que se ha impreso en 3D en la fábrica de Regensburg.
Jens Ertel, director del Additive Manufacturing Campus de BMW, explica: «El creciente uso de la fabricación aditiva en el sistema de producción del Grupo BMW tiene muchas ventajas. Por ejemplo, podemos fabricar nosotros mismos medios auxiliares de producción y pinzas de manipulación de forma rápida, rentable y flexible, que podemos adaptar a necesidades específicas en cualquier momento. Además, tienen un peso optimizado, menos peso significa mayor velocidad de línea, tiempos de ciclo más cortos y costes más bajos. A medio plazo será posible utilizar robots más pequeños, lo que también reducirá las emisiones de CO2 y los costes».
El grupo alemán no se detuvo ahí: el verano pasado desarrolló una versión aún más ligera. Se trata de una pinza robótica biónica. La pinza se ha optimizado topológicamente y cuenta con una cubierta fabricada con la tecnolog íaLSP, ventosas fabricadas con SLS y una estructura de soporte optimizada biónicamente. La fabricación aditiva se utilizó para el molde necesario para el proceso de fundición en arena, que luego se rellenó con aluminio líquido. La combinación de estos procesos redujo el peso otro 25%. Como las pinzas se utilizan principalmente para fabricar techos de CFRP para los modelos M de BMW, el número de robots necesarios se puede reducir. Mientras que el modelo anterior seguía necesitando tres robots, la versión actualizada de las pinzas ahora solo necesita un robot para fabricar dichos techos, gracias a su peso reducido. La planta de Landshut ahora utiliza pinzas dobles, que se fabrican individualmente mediante impresión 3D.
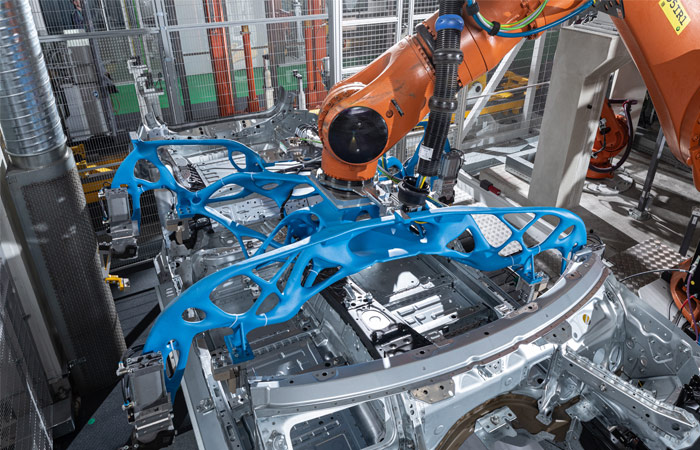
La nueva generación de pinzas biónicas instaladas en Múnich.
BMW va aún más lejos. La planta de Múnich ahora utiliza pinzas biónicas capaces de agarrar y mover todo el suelo de un BMW i4. Este modelo de pinza ha sido perfeccionado y pesa tan solo 110 kilos. Esto representa una reducción de peso del 30% en comparación con el modelo convencional anterior. Para lograrlo, el Grupo BMW utilizó la herramienta de software Synera, en la que también ha invertido. Esta plataforma de software se utiliza mucho en BMW, ya que permite optimizar componentes de forma rápida y eficaz.
Markus Lehmann, jefe de ingeniería de planta y robótica del centro de BMW en Múnich, comenta: «En la planta de Múnich, seguimos desarrollando el uso de herramientas de producción mediante fabricación aditiva. En el ámbito de los sistemas de agarre y manipulación, utilizamos la impresión 3D para equipar nuestras pinzas habituales con elementos de montaje individuales impresos y ya hemos sustituido sistemas de agarre completos por estructuras de soporte altamente integradas y de peso optimizado. Al manipular el piso completo del BMW i4, pudimos reducir el peso en un 30%, y en más de 50 kg para la pinza completa, y ampliar la vida útil de nuestros sistemas como resultado». Para obtener más información, haga clic aquí.
¿Qué opinas del uso de la fabricación aditiva en el Grupo BMW y de sus pinzas robóticas? Deja tus comentarios en nuestras redes sociales: Facebook, Twitter y Youtube. Sigue toda la información sobre impresión 3D en nuestra Newsletter semanal.
*Créditos de todas las fotos: BMW Group