¿Cuáles son los beneficios de la fabricación aditiva de metal sin soportes?
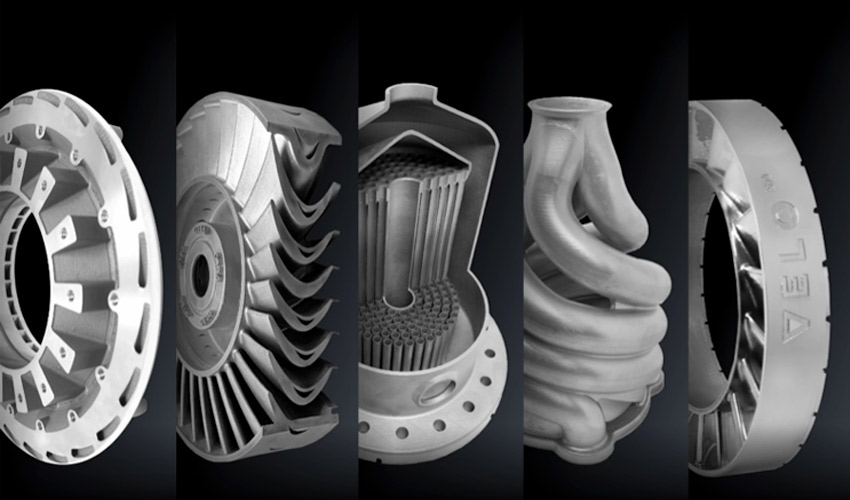
Hoy en día, la fabricación aditiva de metal con soportes todavía se usa principalmente para fabricar prototipos funcionales, componentes de herramientas y repuestos. Paso a paso, se está comenzando a emplear para un uso más orientado a la producción. En un estudio publicado por SmarTech Analysis, la firma consultora predijo que la impresión 3D de metal generaría $ 228.000 millones en componentes metálicos durante la próxima década. Uno de los beneficios clave de esta tecnología es que los diseñadores pueden crear y modelar piezas libremente. Pero, ¿cuánta libertad de diseño permite realmente la fabricación aditiva de metal?
Nos preguntamos esto, porque en la tecnología de fusión láser de lecho de polvo, a diferencia de la SLS, las partes metálicas se unen a la plataforma de construcción a través de estructuras de soporte. Estos soportes agregan considerables limitaciones de diseño y fabricación. Se construyen con el mismo material que la pieza y son esenciales para mitigar la deformación y la distorsión que ocurre debido a altas temperaturas de procesamiento. El proveedor de soluciones de fabricación aditiva de metal, VELO3D, ha desarrollado una tecnología sin soportes para optimizar aún más el tiempo, el coste y la calidad de las piezas metálicas. De hecho, la compañía ha estado permitiendo a los ingenieros producir piezas que antes eran imposibles de fabricar utilizando métodos tradicionales.
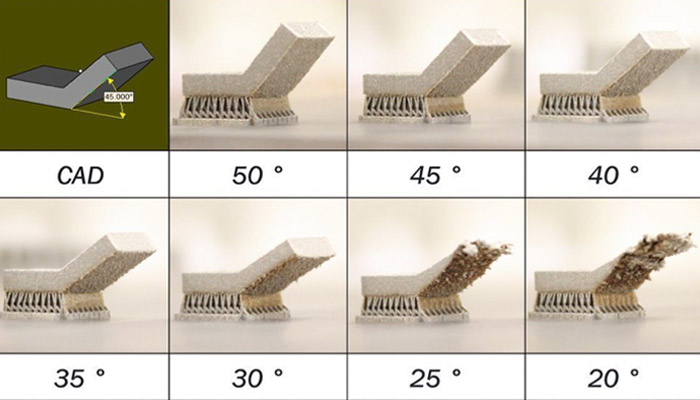
Las máquinas actuales de impresión 3D de metal requieren ángulos de menos de 45º para tener estructuras de soporte. A medida que el ángulo disminuye, la superficie se vuelve rugosa y, finalmente, la pieza fallará si el ángulo se reduce demasiado | Créditos: Protolabs
Una tecnología de impresión 3D de metal sin soportes
Las estructuras de soportes son necesarias en el 95% de las piezas creadas con fabricación aditiva de metal, según lo estimado por Protolabs. Esencialmente, son necesarias para todos los ángulos de menos de 45 grados. Por debajo de 45 grados, ofrecen una plataforma adecuada para la siguiente capa sobre la que construir, fijan la parte a la placa de construcción, evitan la deformación y también ayudan a alejar el calor. Todo ello permite que la pieza se enfríe a una velocidad mucho más controlada. Si no se incluyen, a medida que disminuye el ángulo, la superficie hacia abajo se volverá más rugosa y, finalmente, la pieza fallará si el ángulo se reduce demasiado.
La tecnología sin soportes de VELO3D tiene como objetivo tener un profundo impacto en el tipo de piezas que puede crear. La repetibilidad y la confiabilidad son difíciles de controlar cuando se tiene que quitar los soportes utilizando el mecanizado antes de introducir más pasos de postprocesamiento para lograr la calidad deseada. Al tratarse de un proceso manual, la tasa de rechazo es mayor que en un proceso que no requeriría estos pasos. Michael Corliss, vicepresidente de tecnología de Knust-Godwin, que utiliza la técnica de VELO3D, explica: «La fabricación de piezas sin soportes reduce el elemento humano, por lo que aumenta nuestra reproducibilidad. La eliminación de soportes es un proceso manual y es muy, muy difícil de controlar».
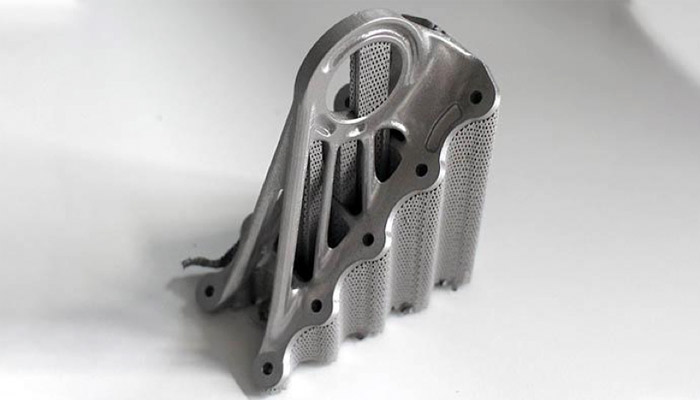
Un soporte de metal antes de ser retirado. Los soportes están hechos del mismo material que la pieza y necesitarán mecanizado CNC para retirarse | Créditos: Concept Laser
Muchas veces, las estructuras de soporte son la causa principal de problemas en la producción, como fallos de construcción y baja calidad de las piezas. Es posible que sea necesario modificar el diseño de una pieza varias veces para evitar estos problemas. El impacto positivo de deshacerse de las estructuras de soporte es mayor en partes huecas o con cavidades. David Bentley, ingeniero sénior de metales impresos en 3D en Protolabs, ha utilizado la tecnología VELO3D. Por ello, aclara que las partes más problemáticas son «cualquier parte con entradas, salidas y estructuras múltiples entre estos puntos de accesibilidad».
Si tomamos el caso de una hélice, los soportes son muy difíciles de quitar y requerirán algunos pasos de mecanizado CNC. A pesar de la fuerte demanda de este tipo de piezas, ha sido difícil satisfacerla debido al desafío que la estructura de soporte presenta. Otros ejemplos de partes o características afectadas por las estructuras de soporte, son los colectores, intercambiadores de calor y canales de enfriamiento. Piezas como estas ilustran las limitaciones de la fabricación aditiva de metal en la actualidad.
La tecnología libre de soportes de VELO3D se ha desarrollado para responder a estos problemas y reducir costes, plazos de entrega y limitaciones de diseño asociadas con la adición de estructuras de soporte. Como su nombre indica, las piezas se imprimen «flotando» libremente en el polvo. Esto significa que se pueden construir más piezas en la misma placa de construcción ya que no están unidas a ella. Tomando el caso de las palas de turbina de alta presión, el fabricante asegura que puede construir hasta 441 partes por impresión en comparación con las 85 partes en otros sistemas. Además, los pasos de postprocesamiento se reducen considerablemente. La compañía ofrece una solución integral para fabricación aditiva de metal que incluye su sistema de impresión 3D llamado Sapphire. Éste trabaja junto con su software Flow y su sistema de control y garantía de calidad, Assure.
Para escuchar a otros expertos en impresión 3D de metal sobre los beneficios comerciales de un proceso sin soporte, puedes descargar el documento escrito por Todd Grimm AQUÍ. Los colaboradores incluyen Protolabs, Incodema3D, Stratasys Direct, Knust-Godwin, Interstellar y Hanwha.
¿Qué piensas de la tecnología de fabricación aditiva de metal sin soportes? Deja tus comentarios en nuestras redes sociales: Facebook, Twitter, Youtube y RSS. Sigue toda la información sobre impresión 3D en nuestra Newsletter semanal.
Información muy completa que permite conocer más sobre este sector.
Muy importante los avances que se están produciendo en el sector.