Aplicaciones de la impresión 3D en el sector de la automoción
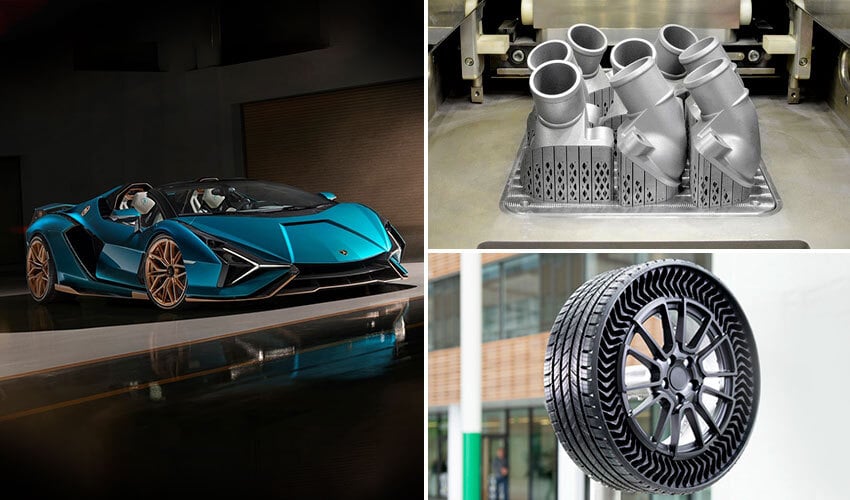
Entre los sectores de aplicación en los que podemos encontrar las tecnologías de fabricación aditiva, la automoción es uno de los que más está aprovechando sus ventajas. Esta tecnología permite a las grandes empresas automovilísticas reducir costes, tiempo y peso a la hora de producir piezas complejas. Además, la fabricación aditiva también permite una mayor personalización a nivel de diseño, que convierten los modelos de coches en experiencias de usuario inolvidables. Con el crecimiento tan significativo que está teniendo la impresión 3D en la automoción, se espera que para 2028 se alcancen unas cifras de $12.4 mil millones. Para entender mejor el impacto que está teniendo la integración de esta tecnología en el sector, hemos hecho una recopilación con las principales compañías que utilizan la impresión 3D en la automoción, así como las distintas aplicaciones que tienen. Las empresas se han listado en orden alfabético.
Audi acelera el diseño automotriz
Audi es una multinacional alemana dedicada a la fabricación de coches deportivos y de alta gama, y que desde 1965 forma parte del grupo Volkswagen. Hace unos años, la empresa apostó por utilizar las soluciones de Stratasys con el objetivo de acelerar el diseño automotriz. La tecnología PolyJet permitió a Audi desarrollar y evaluar diferentes prototipos antes de producir las piezas de un vehículo. Al incorporar la impresora 3D J750 a su línea, el fabricante pudo extender la producción de modelos, como cubiertas de ruedas, rejillas, manijas de puertas o incluso cabujones de luz trasera, que suelen ser de plástico transparente. Con la impresión 3D, pudieron acelerar el diseño de automoción y creación de piezas finales, cumpliendo la demanda de sus clientes.
Bentley: ya hay más de 15.000 piezas impresas en 3D
En la segunda aplicación de la impresión 3D en la automoción, os hablamos de Bentley. El fabricante británico de automóviles Bentley no sólo es conocido por sus renombradas carrocerías, sino también por sus ambiciones de ampliar la impresión 3D dentro de la fabricación aditiva. Con una inversión de más de 3 millones de euros, la empresa podrá fabricar más de 15.000 componentes en 3D en 2021, ahorrando así tiempo de diseño y producción y minimizando los residuos generados. Además de las ventajas de proceso y económicas para Bentley que se derivan del uso de la fabricación aditiva, sus clientes también experimentan un valor añadido: gracias a la impresión 3D, pueden disponer de componentes producidos de forma totalmente individual y personalizada.
BMW apuesta por la fabricación aditiva
La empresa alemana BMW, con sede en Múnich, lleva utilizando la fabricación aditiva desde hace más de 25 años, siendo una de las primeras automovilísticas en integrar dicha tecnología. Para ellos, la impresión 3D en la automoción es una apuesta hacia el éxito. De hecho, en junio de 2020 abrieron finalmente su propio centro de fabricación aditiva con el objetivo de unir sus habilidades de producción. Este campus cuenta con más de 80 empleados y más de 50 soluciones industriales de fabricación. Además del centro, BMW ha demostrado sus capacidades en numerosas ocasiones, como por ejemplo, con el deportivo i8 Roadster. Este modelo integra piezas mucho más ligeras de lo normal, si se hubieran creado con métodos tradicionales. Partes como el soporte de la cubierta de la capota, son ahora más resistentes además de tener un menor peso. Un método avanzado de optimizar la producción de automóviles.
El Bugatti Bolide es un vehículo ligero y rápido gracias a la impresión 3D
Para crear su vehículo más ligero, más rápido y más agresivo hasta la fecha, el fabricante francés de automóviles Bugatti ha recurrido a la AM. El Bolide, como se llama este deportivo con un surtido de nuevas tecnologías, lleva impresas en 3D algunas piezas que reducen el peso de sus componentes de forma significativa. El fabricante integró muchas de las piezas individuales fabricadas con AM que había revelado anteriormente. Una pinza de freno impresa en titanio y un soporte de alerón y un soporte de motor procesados por SLM Solutions son sólo algunos ejemplos de las numerosas piezas impresas en 3D del innovador vehículo. La integración de la impresión 3D fue especialmente importante para las piezas de formas complejas, así como para ayudar a hacer del Bugatti Bolide un deportivo ligero y, por tanto, mucho más rápido.
Dallara y sus intercambiadores de calor impresos en 3D
El fabricante italiano de automóviles Dallara ha recurrido a la empresa Conflux Technology para fabricar los intercambiadores de calor de sus coches de Fórmula 3. La empresa utiliza la fabricación aditiva para obtener piezas más eficaces y más resistentes al calor. Más concretamente, utiliza máquinas de fusión láser EOS sobre un lecho de polvo. La particularidad de este proyecto radica en el tamaño de los intercambiadores de calor: Dallara necesitaba componentes pequeños que pudieran cumplir los requisitos del deporte del motor. Por ello, Conflux Technology creó varios diseños CAD y CFD e imprimió varias iteraciones para validar la geometría y estudiar las características de la pieza, como la rugosidad de la superficie.
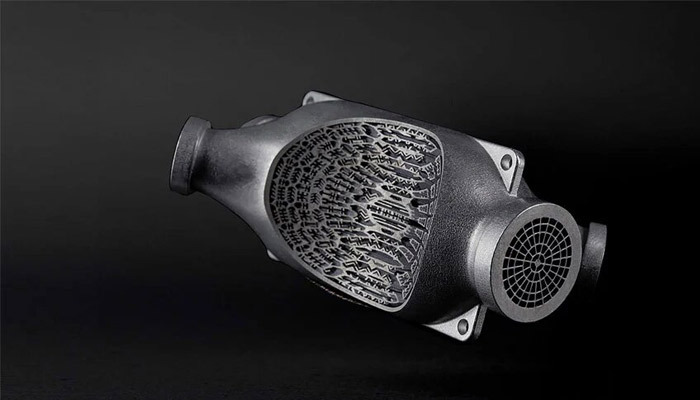
Créditos de la imagen: Tecnología Conflux
Ferrari y fabricación aditiva de metal
La impresión tiene un papel clave en la automoción, ya que permite diseñar piezas más ligeras, resistentes y eficientes en plazos mucho más cortos. El fabricante italiano Ferrari se basó en esta tecnología, en particular la impresión 3D de metal, para imaginar los pistones de uno de sus motores. Ferrari explica que utilizó una máquina de EOS y polvo de titanio, y que la fabricación aditiva le ha permitido imaginar una pieza mucho más compleja, resistente y ligera, gracias en particular a la optimización topológica. Este método también aumenta el número de posibles iteraciones: la empresa pudo imaginar tantos diseños como necesitara y acelerar su fase de creación de prototipos. El fabricante de automóviles también diseñó pedales de freno impresos en 3D con una estructura hueca, un resultado que no habría sido posible con métodos de fabricación tradicionales.
Ford desempeña proyectos con impresión 3D
En 1988, el fabricante de automóviles Ford ya había invertido en 3 impresoras 3D; en 2015, estimó su producción de piezas impresas en 3D en $500.000, prueba de que la tecnología tiene un lugar importante para la empresa estadounidense. Y por una buena razón, ha forjado sólidas alianzas con ciertos fabricantes como Desktop Metal o Carbon. Si echamos un vistazo a las piezas fabricadas por Ford, destacamos el colector de admisión de aire de aluminio, una de las piezas metálicas impresas en 3D más grandes para el automóvil. Pesa 6 kilos y se desarrolló en tan solo 5 días. Más recientemente, Fors diseñó tuercas hechas a medida para proteger las llantas de posibles robos. Impresas en máquinas EOS, estas tuercas se han modelado a partir de la voz del conductor: esto se convierte en un modelo 3D y se imprime dentro de la tuerca. Un método eficaz para luchar contra el robo ya que solo la voz del conductor permitiría sacar las tuercas.
Fraunhofer IAPT y su enfoque «Design to Cost».
El Instituto Fraunhofer de Investigación de Tecnologías de Fabricación Aditiva (Fraunhofer IAPT) se ha propuesto aportar su granito de arena a la producción en serie de productos impresos en 3D. Por ello, el instituto de investigación, con sede en Alemania, se ha propuesto optimizar el factor de costes, así como la rentabilidad y la eficiencia, con la ayuda de un software de desarrollo propio, resultado de una escisión con 3D Spark. Por lo tanto, este abridor de puertas para la producción en serie en la industria del automóvil promete un proceso reestructurado: reducción de las estructuras de soporte, de las necesidades de material y de los tiempos de fabricación y posprocesamiento. De este modo, la aplicación de este enfoque de «diseño al coste» podría dar lugar a una producción global de piezas de automóvil un 80 % más barata. Esto ya se ha hecho en colaboración con el fabricante de coches de lujo Bugatti.
Lamborghini personaliza su Sian Roadster
Lamborghini es la definición de coches deportivos de lujo, por lo que sus razones para elegir tecnologías de fabricación aditiva para crear su Sian Roadster ciertamente no fueron para reducir costes o producir más rápido. Entonces, ¿cuáles fueron sus motivos? Para Lamborghini, la fabricación aditiva representa una cosa por encima de todo: opciones de personalización ilimitadas. Las opciones de personalización son tan ilimitadas como las personas puedan imaginar. Lamborghini ofrece a cada comprador del Sian Roadster, un control total sobre el interior, así como la elección de trabajos respecto a la pintura. Las salidas de aire de nuevo diseño se imprimieron en 3D y permiten a los clientes personalizar, entre otras cosas, integrando sus iniciales en el diseño. ¡Una experiencia de usuario única!
El nuevo supercoche híbrido Artura de McLaren
Como muchas otras marcas de automóviles, el fabricante de coches de lujo McLaren no es ajeno a las ventajas de la AM. Para su superdeportivo híbrido de alto rendimiento, el Artura, que McLaren ha diseñado para combinar tecnología, diseño y un rendimiento inigualable, la empresa decidió confiar en la impresión 3D de metales. El fabricante de automóviles británico utilizó este método innovador para diseñar el bloque del motor y los núcleos de la culata para permitir una mejor refrigeración del motor y, por tanto, un mayor rendimiento. El objetivo general de la empresa a la hora de crear el concepto del superdeportivo era aligerar su peso en comparación con otros vehículos similares. Para ello, el equipo de diseño utilizó fibra de carbono para diseñar un chasis más ligero. Además, incorporaron núcleos impresos en 3D en el bloque del motor y en las culatas de aluminio, que, sin el uso de la AM, habrían sido imposibles de crear con tanto detalle.
Mercedes desarrolla repuestos de metal
Dado que la industria del automóvil no se limita a los vehículos de motor para el transporte de personas, sino que también incluye los vehículos de motor para el transporte de mercancías (camiones), este ejemplo está dedicado a ello. Después de que Mercedes se concentrara con éxito por primera vez en la impresión 3D de repuestos para camiones hechos de plástico, la compañía ahora también produce repuestos para camiones hechos de metal. El uso de la fabricación aditiva de metal hace que las piezas de repuesto sean más resistentes, incluso al calor. Además, existe la ventaja de que a través de esta tecnología, Mercedes tiene la capacidad de producir de manera rentable incluso piezas descontinuadas en pequeñas cantidades. Mercedes es la primera empresa que se centra en la producción de repuestos para camiones.
Michelin fabrica neumáticos en 3D
El fabricante francés de neumáticos, Michelin, presentó su primer prototipo con tecnologías de fabricación aditiva en 2019. Llamados Uptis (sistema único de neumáticos a prueba de pinchazos), estos neumáticos han sido diseñados para no necesitar aire, con el fin de reducir el riesgo de pinchazos y otros fallos en la carretera. La compañía trabajó con la estadounidense General Motors para desarrollar este modelo de neumático impreso en 3D. Si tiene éxito, podríamos esperar que Uptis equipe algunos automóviles para 2024. La impresión 3D solo se utilizó para desarrollar el prototipo, utilizando materiales renovables y de origen biológico, pero si la producción alcanza mayores volúmenes, esta tecnología podría emplearse a mayor escala. Por último, estos neumáticos a prueba de pinchazos también pueden reducir el desperdicio de material para promover la movilidad sostenible (uno de los objetivos de la visión de la movilidad del futuro de Michelin).
MINI Strip más sostenible gracias a la impresión 3D
El fabricante británico de automóviles MINI está reforzado su misión de hacer sus coches más sostenibles. Para ello, se ha asociado con el diseñador Paul Smith, quien le ha ayudado a desarrollar un modelo de automóvil más minimalista: el MINI Strip. Pero, ¿qué papel juega la fabricación aditiva en todo esto? Con el fin de conseguir parte de ese objetivo de sostenibilidad, Paul Smith recurrió a la impresión 3D de polímeros reciclados para crear piezas que se incorporan en el coche. Componentes como los paneles debajo de las puertas o los cubre ruedas han sido impresos en 3D con plásticos reciclados. Tanto estas piezas como muchas otras creadas con materiales reciclados, hacen que el MINI Strip tenga una geometría simplificada, un diseño limpio y mayor responsabilidad medioambiental.
Porsche optimiza los pistones de sus deportivos
El fabricante Porsche ha estado utilizando tecnología de fabricación aditiva desde principios de la década de 1990. Este verano, el gigante de la automoción creó pistones de motor con impresión 3D por primera vez. Los componentes fabricados con esta tecnología fueron diseñados para el motor de alto rendimiento del Porsche 911 GT2. La impresión 3D permitió optimizar los pistones y, como resultado, hacer que este elemento crítico del motor sea un 10% más ligero que los fabricados tradicionalmente. Porsche utilizó una aleación de aluminio especial para los pistones fundidos de Mahle, con el fin de obtener las mejores propiedades para esta aplicación específica. El equipo tuvo que desarrollar nuevos parámetros para el trabajo de impresión, que fue realizado por el socio de fabricación, Trumpf.
SEAT abre un centro de fabricación aditiva
El fabricante español SEAT ha anunciado recientemente una nueva localización de 3.000 m2 que unificará todos los procesos y actividades previas a la producción en masa de un nuevo modelo. Un gran espacio en el nuevo centro estará dedicado a proyectos de impresión 3D. El centro de fabricación aditiva de SEAT alberga varias soluciones 3D, nueve, para ser precisos. Entre ellas están, una HP Multi Jet Fusion, una máquina SLS, 6 impresoras 3D FDM y una solución PolyJet. Gracias a la diversidad de estas tecnologías, SEAT es capaz de producir piezas con un mayor detalle, con importantes propiedades mecánicas y funcionalidades avanzadas. Las máquinas funcionan las 24 horas del día y producen una media de 50 piezas al día. Según el fabricante, el 80% de las piezas son prototipos que se utilizan para desarrollar vehículos más rápidamente, el resto son principalmente componentes de herramientas y personalización.
Vital Auto: el diseño de los coches del futuro en 3D
El estudio de diseño industrial británico Vital Auto tiene una gran experiencia en el diseño automotriz. Entre los ilustres clientes de la compañía se incluyen a muchos de los principales fabricantes de automóviles, como Volvo, Nissan o McLaren. Vital Auto, utiliza las impresoras Form 3L y Fuse 1 de Formlabs para crear prototipos de alta calidad. Desde el diseño hasta la producción, la empresa ha integrado la fabricación aditiva en todo su proceso de producción. Profesionales de Vital Auto han explicado: «Utilizamos la impresión 3D desde el primer día, no sólo para reducir costes, sino también para dar al cliente más diversidad en sus diseños e ideas. La parte más interesante de las impresoras 3D es su versatilidad, la posibilidad de cambiar de material en menos de cinco minutos y la variabilidad de estos materiales desde blandos y flexibles hasta duros y rígidos no tiene precio para nosotros.»
YOYO, el vehículo eléctrico impreso en 3D
Para terminar con esta selección de impresión 3D en la automoción hablaremos del proyecto de YOYO. A medida que el calentamiento global se convierte en una preocupación creciente en todo el mundo, cada vez más personas recurren a alternativas más ecológicas a los productos tradicionales, incluidos los coches eléctricos. Y la impresión 3D no es una excepción en este sentido. Por ejemplo, YOYO, el coche urbano totalmente eléctrico de XEV. El coche se ha fabricado en su mayor parte con impresión 3D, fabricación aditiva de gran formato para ser exactos. Según la empresa, YOYO es la solución más sostenible para la movilidad urbana gracias a un motor 100% eléctrico y, por supuesto, se eligió la impresión 3D debido a su naturaleza más sostenible en comparación con los métodos de fabricación tradicionales.
¿Qué piensas de la utilización de la impresión 3D en el sector de la automoción? Deja tus comentarios en nuestras redes sociales: Facebook, Twitter, Youtube y RSS. Sigue toda la información sobre impresión 3D en nuestra Newsletter semanal.
Impresionante
Muy interesante.