APG fabrica mordazas para mandriles de torno con la tecnología MoldJet de Tritone
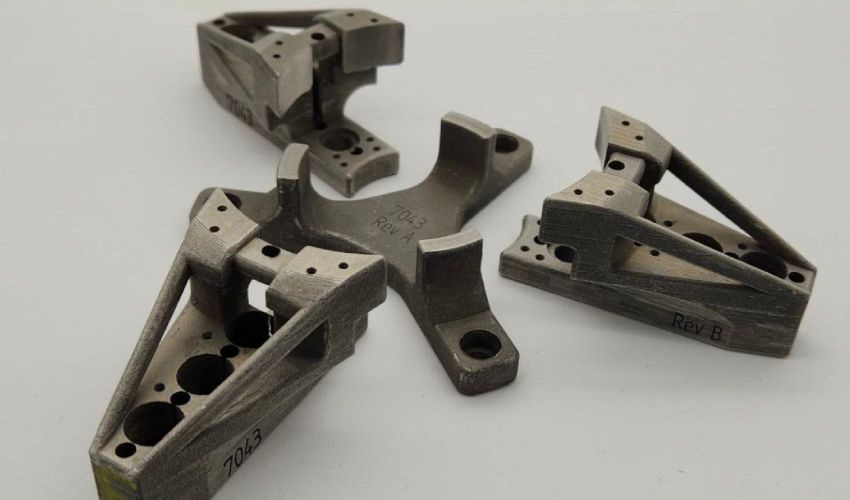
Una de las ventajas de la fabricación aditiva más conocidas y apreciadas por diversas industrias es la libertad de diseño. Aunque hay que seguir unas reglas y ciertas limitaciones en función de la pieza que se vaya a producir, el diseño para la fabricación aditiva (DfAM) permite geometrías y prestaciones que a menudo no se pueden conseguir con otros métodos. Técnicas como el diseño generativo o la optimización topológica se utilizan cada vez más en combinación con la impresión 3D para crear piezas poco convencionales y hacerlas más ligeras y optimizadas.
La empresa estadounidense Alpha Precision Group (APG), uno de los principales proveedores de piezas de precisión, válvulas especiales y componentes metálicos, decidió utilizar la impresión 3D precisamente con este fin. Necesitaba encontrar una solución a un problema que no podía resolverse con otras técnicas y procesos. Rediseñando e imprimiendo en 3D las mordazas de los platos de torno, fabricadas anteriormente mediante mecanizado CNC, la empresa pudo mejorar su proceso de producción. ¿Cómo? Veámoslo en detalle a continuación.
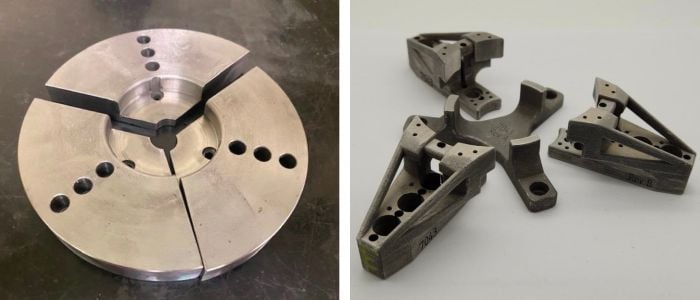
A la izquierda, el diseño original del plato fabricado por CNC. A la derecha, el nuevo diseño de mandril ligero fabricado con la tecnología aditiva MoldJet de Tritone.
El DfAM para conseguir mordazas de husillo más ligeras
En sus más de 50 años de actividad, APG ha reunido bajo su marca a empresas pioneras en tecnologías de mejora de materiales y procesos. En la actualidad, trabaja con diversas técnicas, como el moldeo por inyección de metal (MIM) y la fabricación aditiva.
Uno de los últimos ejemplos del uso que APG hace de la fabricación aditiva de metal para piezas finales ha sido la producción de nuevas mordazas para mandriles de torno. El uso de esta tecnología surgió a raíz de un problema específico en una de las instalaciones de producción de polvo metálico de la empresa. El problema radicaba en el peso excesivo de las mordazas de los platos, que ponía en peligro el cumplimiento de las tolerancias críticas durante el mecanizado de las piezas.
Las mordazas convencionales de acero al carbono, utilizadas para sujetar los engranajes durante el mecanizado, eran demasiado pesadas y generaban una fuerza centrífuga excesiva cuando el torno giraba a gran velocidad. Por tanto, se necesitaba una gran fuerza de sujeción para mantener la pieza, lo que a su vez provocaba distorsiones en la misma.
Tras intentar reducir el peso de las mordazas con mecanizado CNC, sin resultados satisfactorios, el proyecto pasó a manos del equipo Additive de la empresa, que exploró nuevas formas de mejorar el mecanismo. El equipo Additive de APG rediseñó las mordazas, aprovechando al máximo las ventajas de la impresión 3D, incluida la mayor libertad de diseño que ofrece el DfAM.
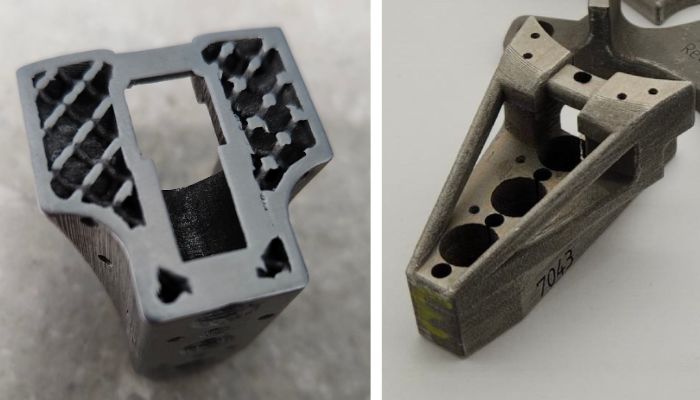
A la izquierda, sección transversal de la nueva mordaza de husillo con diseño de celosía interna. A la derecha, detalle del nuevo diseño de la mordaza externa.
Para minimizar el peso de cada componente del sistema, APG tuvo que rediseñar el exterior y el interior de los componentes, optando por estructuras internas en celosía. En cuanto a la tecnología utilizada para lograr estas complejas estructuras, la elección recayó en el proceso de fabricación aditiva de metal MoldJet de Tritone.
La tecnología aditiva MoldJet de Tritone
MoldJet es una tecnología de fabricación aditiva de metal y cerámica que, en términos de material, no utiliza polvos sino una pasta. El proces permite producir piezas a escala y con notable rapidez. Fue desarrollada por el fabricante israelí Tritone para producir piezas de geometrías complejas, con alta densidad y en volúmenes medios. Para fabricar las mordazas se utilizó el sistema Dominant de Tritone.
El proceso funciona en varios pasos y con múltiples bandejas de impresión, que trabajan en paralelo y de forma independiente. El primer paso es la impresión de moldes de polímero, el segundo es la deposición de la pasta metálica en los moldes, el tercero es la fase térmica de solidificación del material mediante aire caliente y, por último, está el control de calidad de las capas en tiempo real con corrección automática, mediante cámaras equipadas con inteligencia artificial.
Una de las ventajas de esta tecnología es la flexibilidad que ofrece, ya que permite, por ejemplo, cambiar fácilmente los cartuchos de material, producir piezas con diferentes grosores de capa o geometrías en un mismo proceso. Además, el postratamiento es muy sencillo, ya que los moldes de polímero se disuelven por completo y la pieza queda inmediatamente lista para la sinterización.
En el caso de APG, estos aspectos fueron clave para lograr el objetivo de reducir el peso de las mordazas mediante una geometría reticular propia para todas las piezas. Esto se consiguió con la tecnología MoldJet precisamente porque, durante la impresión, todo el espacio vacío de la retícula estaba ocupado por material de molde soluble. Este material se eliminó después con la solución de post-procesado de Tritone, lo que dio como resultado una estructura mucho más ligera que la que podría haberse producido con otras tecnologías.
Optimización de los componentes y la producción con impresión 3D
Los resultados del proyecto superaron incluso las expectativas de APG. El peso de las mordazas se redujo en un 84% (de 2,13 KG a 0,336 kg) y la fuerza de sujeción se redujo en un 67% en comparación con el diseño original (de 30 a 10 psi). Esto permitió a la empresa cumplir sus objetivos y conseguir tolerancias más estrictas, menos desechos, menor desgaste del torno con una carga más ligera y un coste global inferior al de otras alternativas de reducción de peso examinadas.
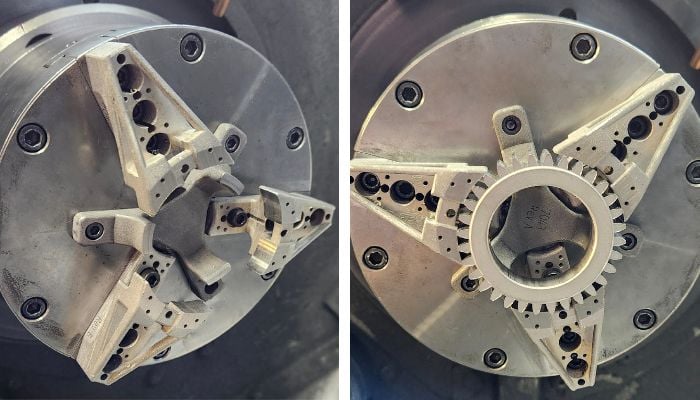
El nuevo juego de mordazas instalado en el torno, con el engranaje colocado.
Joe Taylor, ingeniero de producción de APG, comentó: “Estamos encantados con los resultados. Estamos deseando ampliar este éxito dentro de nuestras propias instalaciones y ofrecer estos dispositivos llave en mano a los clientes”.
En última instancia, la tecnología MoldJet de Tritone no sólo resolvió el problema de la fuerza de amarre, sino que también ofreció la posibilidad de mejorar la repetibilidad general y las tasas de producción en los procesos de fabricación. Esto aportó una mayor eficiencia operativa, precisión y fiabilidad a las operaciones de mecanizado. Puedes encontrar más información sobre la tecnología MoldJet y sus ventajas, AQUÍ.
¿Qué piensas de la tecnología MoldJet desarrollada por Tritone? Deja tus comentarios en nuestras redes sociales: Facebook, Twitter y Youtube. Sigue toda la información sobre impresión 3D en nuestra Newsletter semanal.
*Créditos de todas las fotos: Tritone Technologies, Alpha Precision Group