El acabado de superficies en la impresión 3D: los diferentes métodos existentes
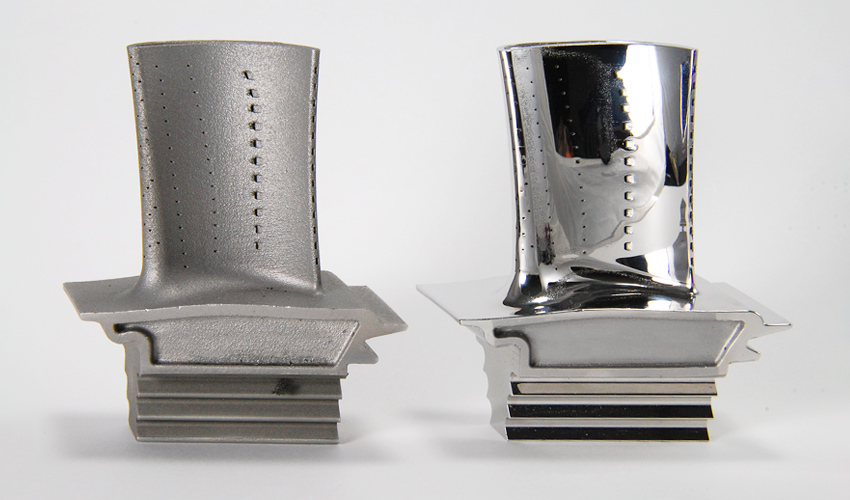
La fabricación aditiva ha experimentado un gran crecimiento en los últimos años, evolucionando de ser una tecnología de nicho a un método de prototipado y producción de piezas finales. No obstante, a pesar de la tendencia de la impresión 3D hacia la libertad de diseño y la producción personalizada, la tecnología por sí sola no es capaz de crear piezas con acabados de calidad profesional. Con frecuencia, se requieren diversos procesos de post-procesado para obtener modelos finales de alta calidad. Anteriormente vimos una introducción al postratamiento en la fabricación aditiva y conocimos la importancia de la limpieza de las piezas impresas en 3D. Además de esto, también es fundamental abordar la rugosidad de dichas piezas en función del material y la tecnología utilizada. Por ello, hoy os traemos una guía completa sobre el acabado de superficies en la impresión 3D. Este tratamiento también puede ser necesario para cambiar el aspecto de la pieza en bruto, alisar las superficies, ajustar el tamaño y la forma, o para mejorar su vida útil.
El lijado de superficies
En las piezas impresas en 3D, sobre todo en las creadas mediante métodos de extrusión, se suelen apreciar visiblemente las líneas de las capas, así como otras posibles imperfecciones. Para eliminar estos defectos superficiales, uno de los métodos más utilizados es el de lijado. Este sistema implica el uso de un material áspero como el papel de lija de diferentes tamaños de grano para eliminar las líneas de las capas y proporcionar un acabado uniforme libre de imperfecciones. Resulta muy útil si se va a aplicar algún tipo de revestimiento posterior a la superficie, ya que ésta tendrá que ser lisa para que se aplique de manera óptima.
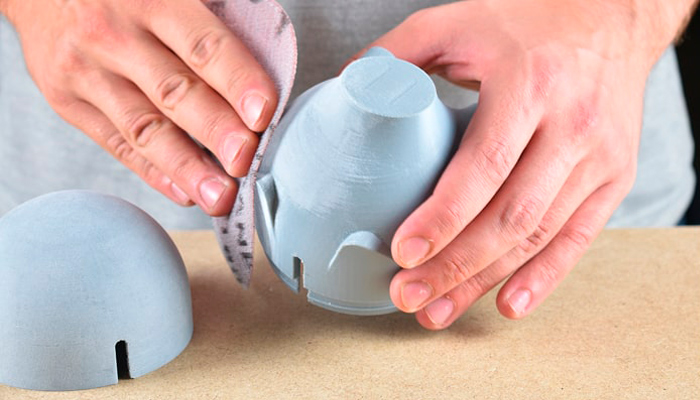
El lijado de las piezas puede hacerse de forma manual, aunque también existen herramientas automáticas.
El lijado se realiza típicamente comenzando con un papel de lija de grano grueso y avanzando a un papel de lija más fino para obtener una superficie cada vez más suave. Es importante tener cuidado al lijar para no dañar la geometría del modelo. Además, un inconveniente de este método es que puede ser difícil llegar a algunos puntos de las piezas, especialmente pequeños agujeros y socavones. El lijado puede realizarse de forma manual, aunque esto puede llevar mucho tiempo. Por ello, también hay herramientas y maquinaria de lijado automáticas disponibles en el mercado.
Métodos de granallado: shot peening y bead blasting
Tanto el shot peening como el bead blasting son técnicas utilizadas para el acabado de superficies en la impresión 3D. Se usan generalmente en una amplia variedad de piezas de metal, incluyendo aleaciones de aluminio, acero, titanio, cobre y otros metales. Ambos procesos permiten mejorar la resistencia y durabilidad de las piezas, sin embargo, hay algunas diferencias clave entre ellos.
El shot peening implica el uso de pequeñas esferas de metal o cerámica, que se disparan mediante aire comprimido a alta velocidad contra la superficie de la pieza. Este impacto genera una deformación plástica controlada en la capa superficial de la pieza, lo que a su vez aumenta la resistencia a la fatiga y reduce la posibilidad de fisuras y fracturas. El shot peening también puede mejorar la resistencia a la corrosión y la adherencia de recubrimientos posteriores. Por otro lado, el bead blasting implica el uso de pequeñas perlas de vidrio, metal, plástico u otro material abrasivo para limpiar, pulir o texturizar la superficie de la pieza. A diferencia del shot peening, que causa deformación en la forma exterior de la pieza, el bead blasting solo remueve la capa superior del material, lo que puede mejorar la apariencia estética, eliminar la suciedad y la corrosión, y preparar la superficie para recibir recubrimientos posteriores.
En resumen, la principal diferencia entre el shot peening y el bead blasting es muy simple. El primer método genera deformación plástica en la superficie de la pieza, lo que mejora su resistencia y durabilidad final. Por su parte, el segundo solo alisa la capa superior del material, mejorando la apariencia estética y preparando la superficie para recubrimientos posteriores. Estas técnicas de postratamiento son especialmente útiles en piezas que estarán sujetas a esfuerzos mecánicos o tensiones, como engranajes, resortes, componentes de turbinas y piezas estructurales de aviones y vehículos.
Métodos de pulido en bombo: vibración y volteo
A diferencia de los métodos previamente mencionados, en los que se tratan las piezas una a una, los sistemas de pulido en bombo sirven para procesar varios objetos impresos en 3D al mismo tiempo. En este grupo podemos dos técnicas que, aunque a priori pueden parecer similares, tienen algunas diferencias sustanciales a tener en cuenta. Estos son el acabado por vibración y el volteo (también conocido como «tumbling» o «rumbling», en inglés). Ambas tecnologías consisten en colocar las piezas impresas en 3D en un tambor o bombo junto a medios abrasivos que, con el movimiento giratorio o de vibración, generará el roce necesario para que las piezas obtengan un acabado óptimo. Sin embargo, la elección entre un método u otro dependerá de los requisitos específicos de la pieza y del resultado deseado.
Aunque ambos métodos consiguen acabados de calidad, el sistema por vibración suele ser más adecuado para lograr una superficie más lisa y homogénea al crear una distribución más uniforme del material en las piezas. Así, la vibración es ideal para piezas de gran tamaño, u con bordes redondeados que no tengan alto nivel de detalle. Por otro lado, el volteo se basa en un sistema de cilindro centrífugo que aplica un movimiento más suave, por lo que resulta mejor para piezas pequeñas, más delicadas y con detalles finos. La velocidad es otro aspecto diferencial de ambos métodos. Mientras que el acabado por vibración es una técnica más rápida, el volteo suele requerir más tiempo para obtener superficies de alta calidad. Dependiendo del acabado deseado y de los materiales utilizados, el volteo puede durar desde unas horas hasta varios días. Por su parte, el acabado por vibración puede lograr los mismos resultados en una fracción del tiempo, a menudo en unas pocas horas.
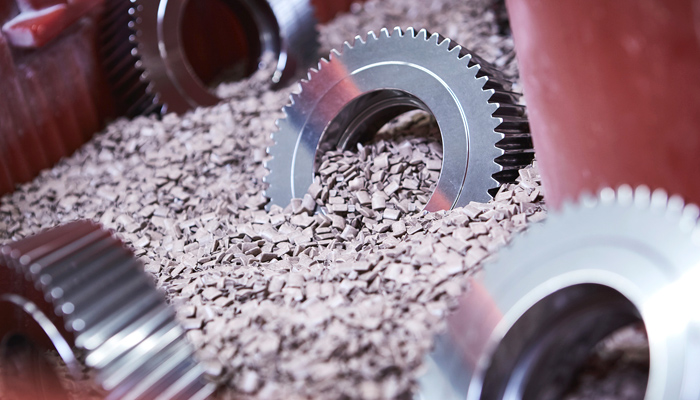
Esta técnica de postratamiento puede utilizarse en piezas tanto de metal como de plástico.
En resumen, el acabado por vibración y el volteo son métodos eficaces para el post-procesado de piezas tanto de metal como de plástico, pero difieren en su movimiento, velocidad, acabado superficial e idoneidad para diferentes geometrías de piezas. Además, hay que tener cuidado al mezclar distintos tipos de medios abrasivos, ya que algunas combinaciones provocan un desequilibrio y dan lugar a un acabado desigual o a daños en las piezas.
Postratamiento de alisado por vapor
El alisado por vapor es otro método para obtener una superficie lisa del objeto impreso, con la diferencia de que el acabado será brillante en lugar de mate. Para ello, se utiliza un disolvente en estado gaseoso que funde la superficie del componente hasta dejarla uniforme. Una vez que las piezas son expuestas al disolvente en la cámara de vapor, se introducen directamente en una cámara de refrigeración para detener la licuefacción. La licuefacción es el proceso en el que una sustancia en estado sólido o gaseoso pasa directamente a estado líquido, debido a un cambio radical en sus condiciones físicas. Este enfriamiento garantiza que sólo se funda la superficie y se mantenga la forma del objeto deseada.
Este proceso de alisado por vapor también sirve para rellenar los poros del exterior del objeto y sellar la superficie, haciendo que las piezas sean útiles para contener líquidos o gases. Aunque dicha tecnología es compatible con una amplia gama de termoplásticos, cabe destacar que no puede utilizarse con ciertos materiales ya que podría provocar una reacción química perjudicial. Entre los plásticos incompatibles encontramos el policarbonato (dependiendo de máquina de postratamiento), la polifenilsulfona (PPSF), el ULTEM 1010 y el ULTEM 9085.
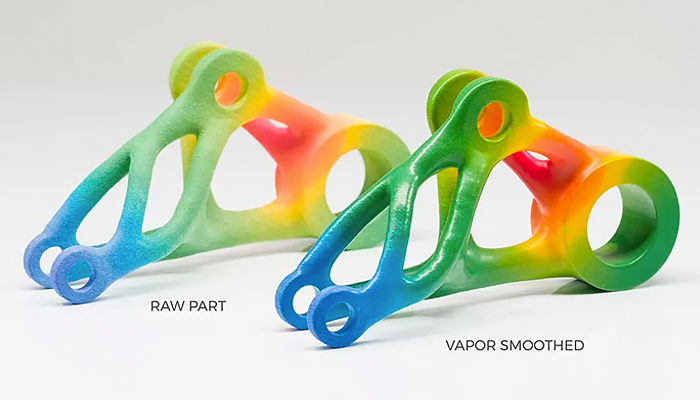
Comparativa entre la pieza en bruto y la pieza después de aplicarle el alisado por vapor. (Créditos: AMT)
Una alternativa al alisado con vapor es la inmersión en disolvente (o solvent dipping, en inglés). Como su nombre indica, consiste en sumergir las piezas impresas en 3D en un disolvente en lugar de exponerlo al químico vaporizado. Aunque los resultados son bastante similares a los del alisado por vapor, resulta más difícil mantener la precisión dimensional ya que el disolvente actúa con mayor rapidez y agresividad. Este método suele resultar útil si las piezas son mayores que el tamaño de la cámara de vapor.
Uso de resina epoxi: recubrimiento e infiltración
Las llamadas resinas epoxi son una clase de polímeros reactivos, que contienen grupos epóxidos (éteres cíclicos de tres miembros que contiene dos átomos de carbono y uno de oxígeno). A la hora de tratar las piezas en impresión 3D, estas resinas permiten un acabado de superficies sellado haciendo la pieza hermética, así como aumentando su resistencia a altas temperaturas y a ciertos productos químicos. Este método es ideal para componentes que se deban enfrentar a duras condiciones de funcionamiento. A la hora de aplicar este tipo de resina, podemos optar por dos métodos: recubrimiento e infiltración.
El recubrimiento de epoxi suele aplicarse a mano. Esto permite reducir los costes al evitar la necesidad de adquirir equipos costosos, pero a la vez incrementa el tiempo y la cantidad de trabajo requerido para su aplicación. Además, esta técnica es más adecuada para pequeñas tiradas de producción, componentes de pequeño tamaño o artículos que solo necesitan sellar una parte de su superficie. No obstante, hay zonas a las que no se puede acceder con esta técnica, como canales internos y socavones. Asimismo, puede no ser la opción ideal para piezas que requieran dimensiones precisas, ya que el recubrimiento de epoxi aumentará ligeramente el grosor de la pieza.
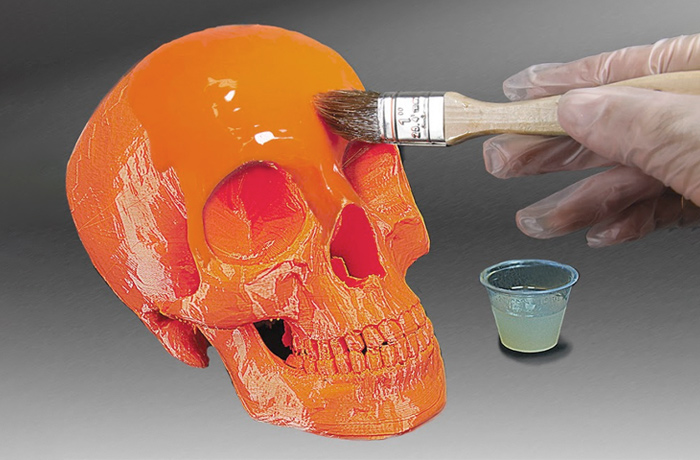
Ejemplo de recubrimiento manual de la resina epoxi.
Por otra parte, el sistema de infiltración de epoxi contrarresta muchas de las limitaciones encontradas al aplicarlo a mano. En el método de infiltración, se sumerge la pieza en epoxi y se utiliza una cámara de vacío para introducir la resina en el objeto, rellenando así los poros. Este proceso tarda unas tres horas en completarse y requiere menos mano de obra, lo que significa que es más práctico y rápido a la hora de aplicarlo en componentes grandes. Sin embargo, la principal desventaja frente al revestimiento a mano es su mayor coste. Se necesita una cámara de vacío, un horno para precalentar y curar la resina, todo eso añadido al coste de la resina epoxi en sí.
El papel del mecanizado CNC en el postratamiento
Como sabemos, pueden utilizarse las tecnologías aditivas y sustractivas de forma complementaria para combinar los beneficios de ambos métodos. Entre los sistemas de fabricación sustractiva más conocidos encontramos el mecanizado CNC que, aunque no es estrictamente un método de postratamiento, puede utilizarse como recurso para el acabado de superficies de calidad en la impresión 3D. Esto es especialmente interesante en el caso de tecnologías como la deposición de energía directa (DED). En ellas, se obtienen piezas en bruto con una superficie muy rugosa, ya que el metal se funde directamente durante el proceso de extrusión. Por eso siempre es necesario el paso de mecanizado CNC para obtener una superficie lisa y definida. En el mercado, existen soluciones de fabricación híbridas que integran ambos procesos para acelerar los pasos de producción.
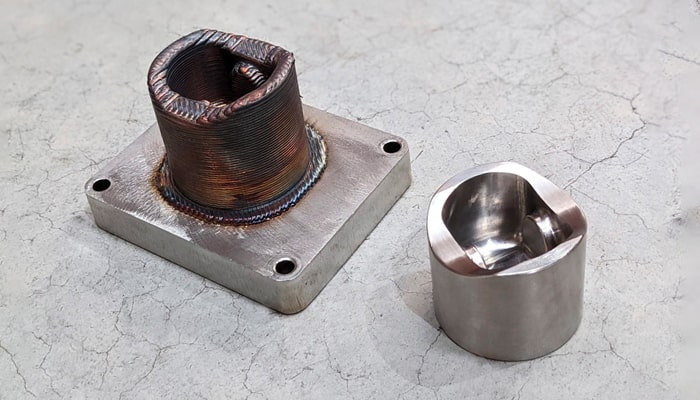
A la derecha, la pieza después de realizar el mecanizado CNC. (Créditos: Meltio)
¿Qué piensas de los diferentes métodos para el acabado de superficies en la impresión 3D? Deja tus comentarios en nuestras redes sociales: Facebook, LinkedIn y Youtube. Sigue toda la información sobre impresión 3D en nuestra Newsletter semanal.
*Créditos foto de portada: EOS