#Startup3D: LEAM mejora la densidad de capas de las piezas XXL impresas en 3D
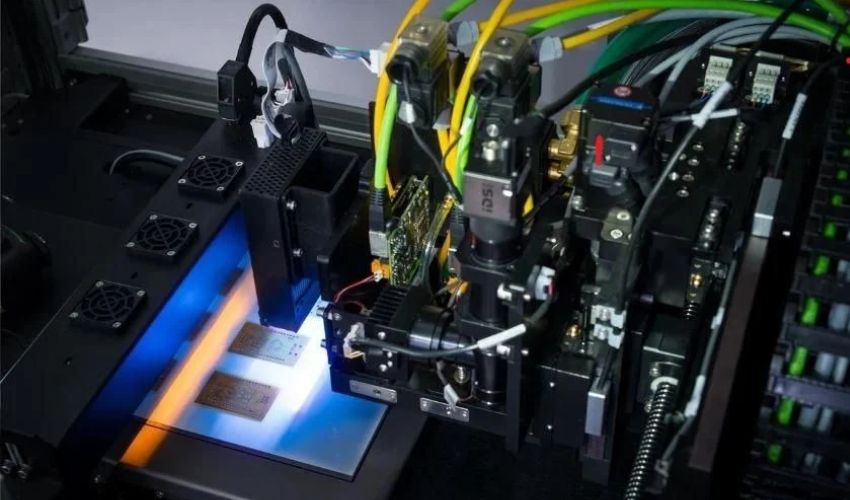
De la ciencia a la impresión 3D y, en última instancia, a los negocios: esta ha sido la trayectoria de LEAM hasta la fecha. La spin-off de la Universidad Técnica de Múnich ya sentó en esta última las bases de la tecnología que ahora está lista para salir al mercado. Con su sistema DEMEX, LEAM está abriendo nuevos caminos en el sector de la fabricación aditiva, ya que la empresa no utiliza láseres para fundir el material como otras startups, sino un espectro de luz continuo. De esta manera, el material se calienta justo antes de que pase la boquilla y la tecnología también asegura una mejor adhesión entre las capas. El sistema DEMEX desarrollado por LEAM está disponible como complemento para impresoras 3D de gran formato y la joven empresa ya ha reunido a sus primeros clientes. Hablamos con el equipo de LEAM para conocer más sobre las etapas por las que la startup ha pasado hasta la fecha, conocer más de cerca su tecnología y hablar sobre los planes que LEAM tiene para el futuro.
3DN: ¿Podrían presentarse brevemente y contarnos cómo llegaron a la impresión 3D?
Somos tres fundadores (Patrick Consul, Ting Wang y Benno Böckl) y entramos en el tema de la impresión 3D desde nuestros estudios de ingeniería mecánica o desde que comenzamos nuestra actividad como colaboradores científicos en la cátedra de compuestos de carbono (LCC) de la Universidad Técnica de Múnich, donde también nos conocimos. Patrick ya ha había intentado en su tesis de maestría producir núcleos para estructuras sándwich en la aviación a partir de PEEK y la impresión 3D. Sin embargo, esto no se logró en ese momento, ya que no se podían alcanzar las resistencias necesarias. Sin embargo, a partir de 2017 siguió el tema como asistente de investigación en la cátedra de compuestos de carbono. En los años siguientes solicitó y tramitó varios proyectos de investigación en los que continuó investigando el tema
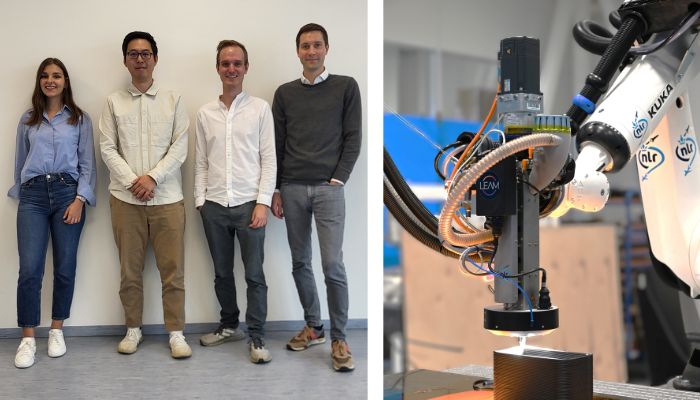
Izquierda: el equipo de LEAM. Derecha: el sistema DEMEX
Ting Wang trabajó en un proyecto de investigación en el que se debía estudiar específicamente el calentamiento del sustrato para lograr una mejor unión de las capas. Por lo tanto, Ting ya ha realizado los primeros trabajos preparatorios concretos en su tiempo como colaborador científico, en los que se basaron los desarrollos posteriores del sistema DEMEX. Benno también trabajó durante varios años como investigador en la cátedra de compuestos de carbono y se ocupó del proceso de colocación de fibra automatizada para la fabricación de componentes de carbono. El cual tiene ciertas similitudes con la impresión 3D. Así que hemos llegado a la impresión 3D a través de la ciencia y hemos aprendido los retos del proceso. Hoy en día, esto nos permite desarrollar soluciones que abren nuevas posibilidades para la impresión 3D en la fabricación de componentes.
3DN: ¿Cómo se fundó LEAM y cuáles han sido los mayores hitos hasta ahora?
Patrick ha investigado diferentes vías en sus proyectos de investigación para aumentar la adhesión de las capas y, por lo tanto, la resistencia de los componentes en la impresión 3D por extrusión. Cada vez está más claro que el único enfoque realmente prometedor es el calentamiento y la fusión puntual de la capa subyacente. Ting ha investigado este enfoque concreto en un proyecto de investigación y ha desarrollado un primer prototipo de nuestro sistema DEMEX posterior, que, sin embargo, todavía utilizaba láseres como fuentes de energía. El enfoque ha dado resultados prometedores, pero la comercialización era cuestionable, ya que los costes y los dispositivos de protección necesarios habrían hecho que el producto no fuera rentable. Entonces se nos ocurrió la idea de utilizar LED blancos con un espectro de banda ancha en lugar de láseres. Estos son mucho más seguros y económicos que los láseres y, después de que las primeras pruebas preliminares demostraran su funcionabilidad, decidimos fundar una empresa que ofreciera el sistema como producto.
Un hito importante fue la obtención de la financiación en el marco de la transferencia de investigación de Exist. Esto nos permitió financiar los primeros 18 meses y construir LEAM lo suficiente como para que podamos existir como empresa. El año pasado también recibimos la aprobación del Centro de Incubación de Empresas ESA de Baviera, que apoya nuestro proyecto. Otro hito fue la primera prueba de concepto con un cliente, que demostró no solo que nuestro sistema funciona, sino también que existe un gran potencial de mercado. A continuación, también pudimos vender e instalar los primeros sistemas a los clientes. A mediados del año pasado contratamos a nuestra primera empleada a tiempo completo, que trabaja para nosotros como ingeniera de desarrollo, por lo que ahora también nos hemos convertido en empleador. Finalmente, pudimos presentar una solicitud de patente para nuestra tecnología, lo que es crucial para el desarrollo de la empresa.
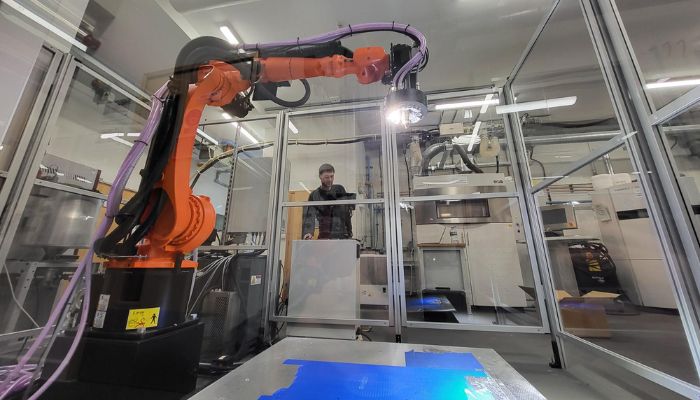
LEAM ha solicitado una patente para su sistema DEMEX
3DN: ¿Podrían presentarnos brevemente el sistema DEMEX? ¿Qué ventajas ofrece la tecnología en comparación con otros procesos?
El sistema DEMEX es un complemento para impresoras 3D de gran formato. El sistema combina emisores LED y cámaras infrarrojas distribuidas alrededor del extrusor. Con la ayuda de los emisores LED, el sistema DEMEX puede calentar el sustrato de forma específica y precisa directamente en la boquilla, asegurando así que una soldadura perfecta de las capas. Alcanzar la temperatura deseada se consigue mediante un circuito cerrado de control con las cámaras infrarrojas. En lugar de la resistencia máxima alcanzable que hasta ahora es del 60%, se puede alcanzar el 100% de la resistencia que se especifica en la hoja de datos del fabricante del material, ¡y en todas las direcciones! Además, se pueden procesar grados de material mucho más baratos. Por ejemplo, materiales de moldeo por inyección que hasta ahora eran completamente inadecuados para la impresión 3D, ya que no se podía lograr la adhesión de capas. El sistema DEMEX se comunica con el control de la impresora y, por lo tanto, siempre sabe en qué dirección se está moviendo la impresora y qué área debe calentarse. Por lo tanto, no es un parámetro a tener en cuenta al crear el código G, por lo que no interfiere con los procesos anteriores en el uso de la impresora.
Con nuestra tecnología, abordamos los problemas comunes de la impresión 3D. Un enfoque elegido con frecuencia en la impresión 3D es, por ejemplo, el volumen de impresión y la bandeja calefactada. Sin embargo, tienen la desventaja de que la temperatura no se puede seleccionar arbitrariamente alta, ya que de lo contrario el componente se vuelve inestable y se derrumba. Este problema no existe con nuestro sistema DEMEX, ya que solo calentamos una capa muy fina en la superficie en un área muy limitada delante de la boquilla. Por lo tanto, podemos ir más allá de la temperatura de fusión del material, lo que nos permite alcanzar resistencias mucho más altas. Otro enfoque es el uso de emisores infrarrojos distribuidos en el espacio de construcción o instalados localmente en la boquilla. Sin embargo, tienen la desventaja de que los emisores infrarrojos tienen tiempos de reacción muy largos de uno a tres segundos, lo que los hace difíciles de regular. La potencia de nuestro sistema basado en LED, por otro lado, se puede ajustar en milisegundos y la densidad de potencia alcanzada también es mayor que la de los radiadores infrarrojos. En comparación con los láseres, nuestros LED también tienen una clara ventaja de precio. Por un lado, las fuentes de energía en sí mismas son un 90% más baratas que un sistema láser comparable. Por otro lado, se eliminan los dispositivos de protección necesarios, que pueden costar más en una impresora 3D de gran formato que todo el sistema DEMEX que ofrecemos.
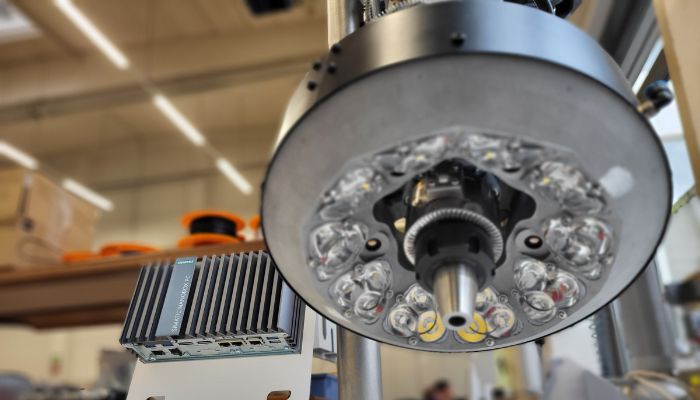
LEAM utiliza LED y no láseres en DEMEX. Los LED se pueden adaptar rápidamente y también son más económicos que los láseres
3DN: ¿A quién va dirigido el sistema DEMEX y qué aplicaciones se benefician más de él?
La utilidad del sistema DEMEX es especialmente evidente en aplicaciones en las que se utilizan polímeros de alto rendimiento o en componentes muy grandes, por ejemplo, en la industria aeroespacial o de petróleo y gas. Aquí es donde los problemas que resolvemos tienen un efecto particularmente fuerte. Si consideramos, por ejemplo, un componente grande que sufre una interrupción durante la impresión, la pieza es hasta ahora un desperdicio con costes asociados que pueden llegar a los miles. Con la ayuda de DEMEX, la impresión puede continuar fácilmente después de la interrupción, ya que se garantiza la conexión a la capa inferior. Sin embargo, el sistema también es adecuado para otras industrias en las que se utilizan plásticos técnicos o plásticos reforzados con fibra. Básicamente, cualquier persona que quiera imprimir componentes se beneficia de las cargas mecánicas para las que las resistencias obtenidas hasta ahora con la impresión 3D no son suficientes. Aquí es concebible, por ejemplo, la construcción naval, la construcción de vehículos ferroviarios o incluso la industria automotriz.
3DN: ¿Cuáles han sido sus proyectos más emocionantes hasta ahora?
La instalación de nuestros dos primeros sistemas fue sin duda emocionante. Instalamos el primer DEMEX en el NLR, el equivalente holandés del Centro Aeroespacial Alemán (DLR). Poco después, pudimos poner en marcha el segundo sistema en la Universidad de Exeter en Inglaterra. Pero los proyectos en curso también son sumamente interesantes. Además, siempre hay nuevas solicitudes de sectores en los que nunca se habría pensado. Por ejemplo, actualmente estamos en conversaciones con clientes del sector de la construcción, pero incluso hay interesados en la piscicultura, por lo que realmente no hay límites para todo esto.
3DN: ¿Quisieran compartir algunos de sus objetivos?
El siguiente paso que queremos dar con nuestro sistema es la adaptación a impresoras más pequeñas. Por el momento, solo podemos manejar impresoras 3D de gran formato, ya que todavía necesitamos un cierto espacio de instalación. Sin embargo, ya estamos trabajando para reducir el tamaño de los componentes individuales y queremos estar listos para poder equipar las impresoras de filamentos con el sistema DEMEX a finales de este año. Hemos recibido solicitudes en esta dirección una y otra vez, por lo que hay una gran demanda aquí. Además, en las próximas semanas lanzaremos el cambio a Siemens Industrial Edge. Esto incluye nuevos componentes de hardware y software en nuestro sistema, que ofrecen posibilidades completamente nuevas en términos de mantenimiento y actualizaciones del sistema, pero también de fiabilidad.
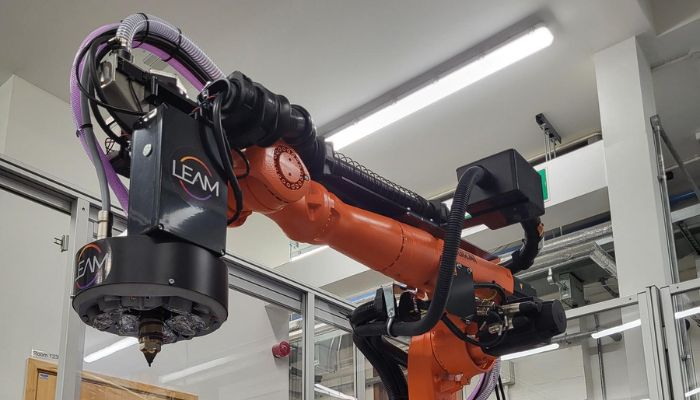
Por el momento, el sistema DEMEX solo está disponible para impresoras 3D de gran formato
¿Qué opinas de LEAM y su sistema DEMEX? Deja tus comentarios en nuestras redes sociales: Facebook, LinkedIn y Youtube. Sigue toda la información sobre impresión 3D en nuestra Newsletter semanal.
*Créditos de todas las fotos: LEAM