Zap&Buj, making fashion through additive manufacturing
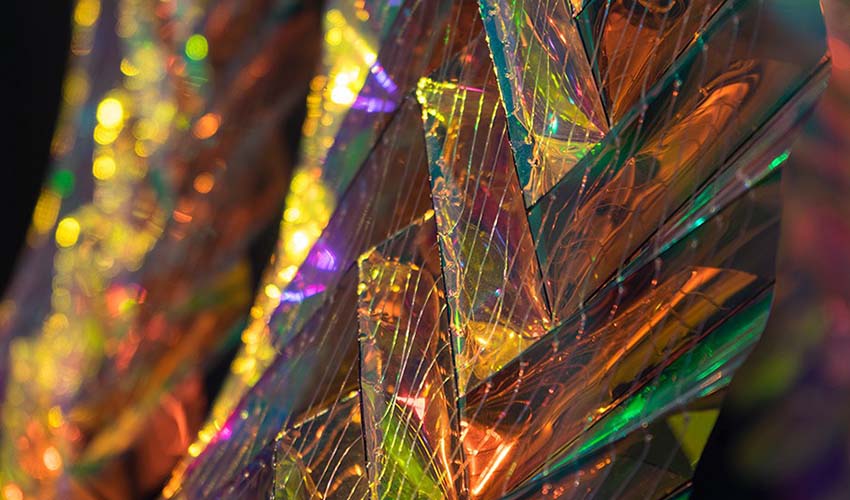
The development and manufacture of fashion through additive manufacturing is not new in the technology sector. Many firms have already benefited from 3D printing for fashion design and production. Innovation and originality in the creation of unique products opens up a world of possibilities for brands. For this reason, we wanted to learn more about how companies that decide to integrate new technologies do so. We spoke to Raquel Buj, one of the creators of the Zap&Buj brand, which stand at the intersection between architecture, fashion and technology.
3DN: Can you introduce yourself and tell us about your relationship with 3D printing?
I am Raquel Buj, architect, fashion designer, teacher and researcher. My approach to 3D printing was, first, discovering incredible 3D printing works such as the shoes made in collaboration with United Nude and 3D Systems with the architect Zaha Hadid or the Kinematic Dress by Nervous System in 2014-15. Later on I discovered Iris van Herpen’s suits and her experimentation with different techniques and materials in 3D . At the prototype level, I began to carry out some tests, firstly failed, in a postgraduate course at the ETSAM on Architecture and Fashion. Later, in the studio I co-founded with Elena Zapico, Zap&Buj, we continued experimenting with 3D printing in several of our designs.
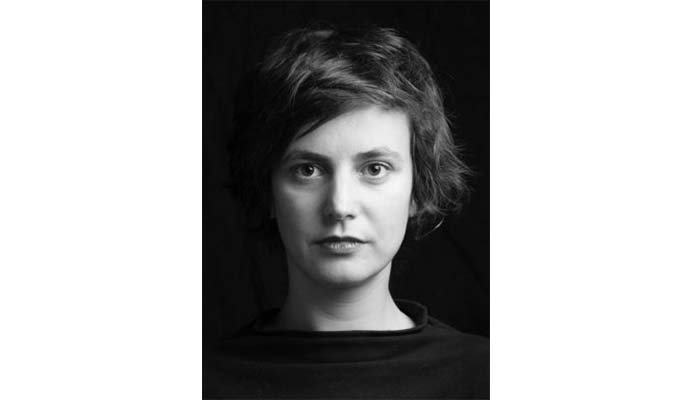
Raquel Buj
3DN: How did the creation of the Zap&Buj studio come about?
As architects and fashion designers, Zap&Buj emerged as a meeting place between both disciplines. We like to think of it as a “laboratory” where we investigate this relationship in an experimental way, both at a concept level and in the use of materials. We work with materials brought from very different fields and mix them with technologies. All this to generate new horizons between the hard of Architecture and the soft of Fashion.
3DN: How important is additive manufacturing in your work? Could you give us some examples where you have used them?
In our work, digital manufacturing techniques, such as 3D printing, have allowed us to be able to materialize complex organic processes that otherwise we would not have been able to consider in our designs. For example, we carried out a study of how a humidity grew in a vertical wall, we drew in 3D this geometry as well as its evolution. Later, we printed it in 3D with a flexible filament on an elastic tulle fabric. The final piece was an elastic monkey that adapted to the different movements of the body. The 3D printing made it easier for us to materialize organic geometries as well as the whole process of experimentation and prototyping.
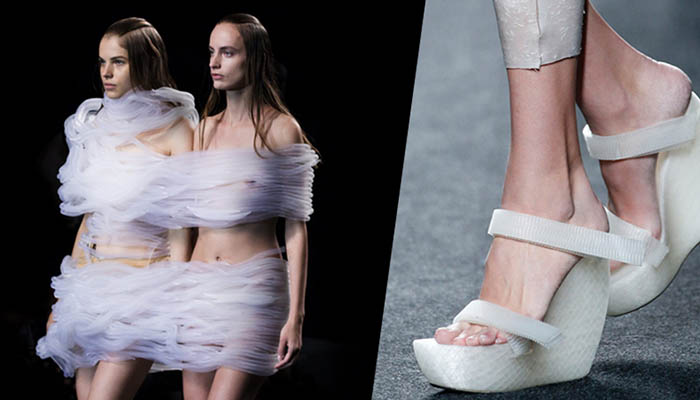
Organic designs through 3D printing | Credits: Zap&Buj
3DN: What is the relationship between new technologies and the fashion industry?
The future of fashion is moving towards the integration of technology, craftsmanship and sustainability. The integration of new technologies allows fashion to go beyond the purely aesthetic by providing a degree of interaction between our body and the environment. On the other hand, the union of technology and craftsmanship will make it possible to generate more unique garments, integrating in an innovative way both the complexity and efficiency provided by digital manufacturing technologies and the craftsmanship processes and their human value.
In addition, we will seek to make the garments of the future more sustainable both in the production processes and in the use of materials, giving special importance to innovation in this area. There is now a very interesting movement related to bio-printing technologies (also used in medicine) that allows the possibility of growing your own garments and that these are biodegradable, reversing the cycle of consumption protecting our natural resources.

The firm seeks the integration of technology, craftsmanship and sustainability | Credits Zap&Buj
3DN: What are Zap&Buj’s next projects?
We have several projects in sight. An interesting one, still in progress, is trying to bring this relationship between Architecture and Fashion, until now materialized through body suits, to the field of architecture. I am interested in this constant back and forth dialogue between both disciplines. That meeting point in which architecture becomes more like a dress, more tactile and better adapted to our bodies. Some of these materials with which we have experimented covering our bodies could, why not, cover a space, thus bringing architecture closer to the body.
3DN: Do you have any last words for our readers?
I wanted to comment that I find the integration of new materials as manufacturing technologies in disciplines such as fashion very interesting, a lot of research is being done on this and there are very interesting proposals. I think the future of fashion is to come up with innovative proposals in the use of materials and technologies that allow a better relationship with people and efficient and sustainable solutions for the planet. I also think it is essential that this is communicated in media such as this, which make other ways of doing things visible so that, together, we can evolve the future of design.
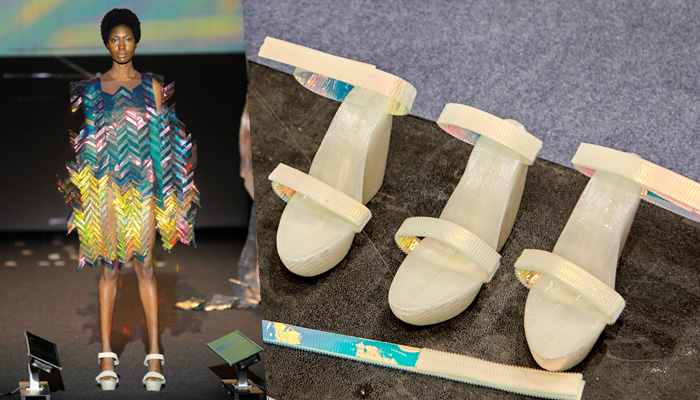
The firm seeks the integration of technology, craftsmanship and sustainability | Credits Zap&Buj
You can find more information on fashion making through additive manufacturing and on the firm Zap&Buj on its official website HERE. What do you think of Zap&Buj? Let us know in a comment below or on our Facebook and Twitter pages! And remember to sign up for our free weekly Newsletter, to get all the latest news in 3D printing send straight to your inbox!