XJet’s NanoParticle Jetting (NPJ) Technology Is Unlocking Powderless Ceramic and Metal Additive Manufacturing
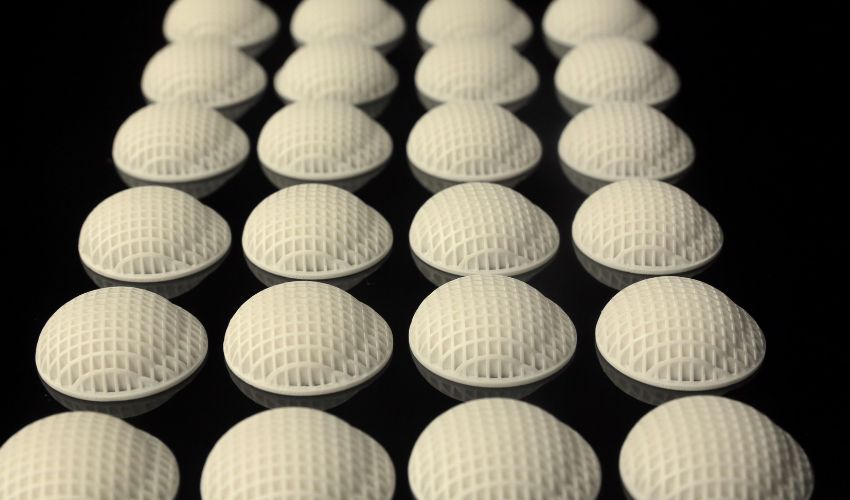
Per the most recent Wohlers Report, the market for additive manufacturing goods and services has seen a growth of about 18.3% over the past year, confirming not only the continued market recovery from the pandemic, but also the increasing importance of the sector. Not only that, but among the different technologies, those using metal and ceramics have grown particularly quickly. Indeed, the metal additive manufacturing market is currently worth over $3 billion according to a report from AMPOWER, with a projected growth of CAGR 26.1%. Meanwhile, ceramic AM is expected to be worth $400 million by 2032, a sevenfold increase since 2020.
Nevertheless, barriers for adoption of metal and ceramic 3D printing remain. Notably, those that reflect the use of powder and slurries, which make up the majority of ceramic and metal AM. This not only leads to waste, but also requires considerable post-processing. Not to mention, the handling and processing of these raw materials along the manufacturing process poses several inherent shortfalls that impact adoption and scale. This relates especially to the fact that it is necessary to deal directly with hazardous materials and lasers, as well as with manual and lengthy powder removal and recycling. Thankfully, alternative technologies are answering this concern. Israeli manufacturer XJet is known for its NanoParticle Jetting™ (NPJ) technology, which uses inks rather than powder, yielding parts with high levels of detail, finish, and accuracy. We took a closer look at how exactly the technology works.
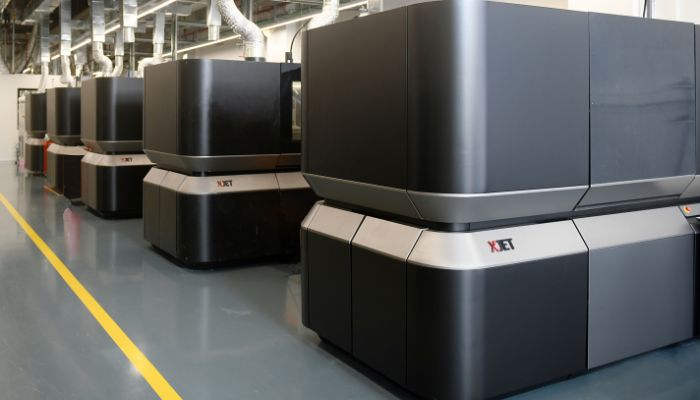
Xjet’s NPJ solution
How Does NPJ Work?
NPJ is unique among both metal and ceramic AM processes. Typically, printing with either of these materials will require using loose powder or slurry. Undoubtedly, it is safe to say that the build process in most metal and ceramic AM technologies involves the spreading the loose material before binding or sintering the layer.
This is not the case with NPJ. In fact, despite using ceramics and metals, NPJ falls under the umbrella of material jetting. For those who may be unfamiliar, material jetting, in contrast to binder jetting, works by jetting the material, eliminating the need for powder. In this case, as mentioned above, XJet does this by developing inks containing dispersed solid nanoparticles of either metal or ceramic materials that are jetted on the build tray in order to build the part. Indeed, the process has been designed to be simple to use; not only do the inks come in sealed cartridges, but users can print multiple materials at once, including a soluble support material that can be removed easily. Moreover, the entire process has been optimized and automated for simplicity, resulting in what XJet refers to as “Print-Wash-Sinter.” Unlike many other available processes, this requires a mere three steps, thus lowering the barriers for entry into metal and ceramic printing.
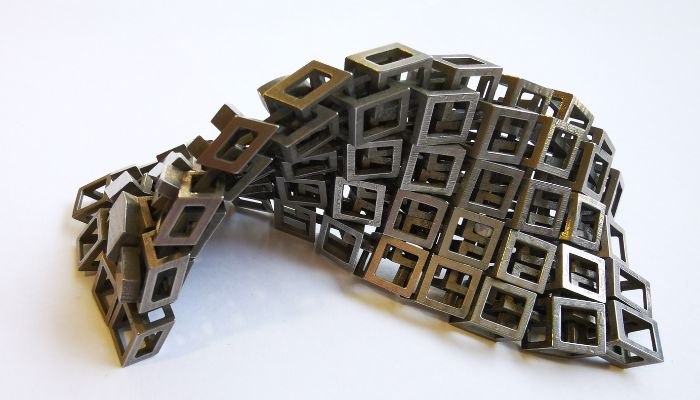
NPJ technology can be used to create extremely detailed metal and ceramic parts
Benefits of Powderless Processes Over Traditional Ceramic and Metal AM
A powderless process offers several advantages over more traditional ceramic and metal additive manufacturing, beyond ease of use. Foremost, not relying on powder makes the process safer for users. This is because working with powder requires safety gear, as it can be dangerous if it gets into the lungs, and the powderless process negates this issue.
Furthermore, the process is more sustainable overall. While 3D printing is often touted as a more eco-friendly process because it uses less material, it is well-known in the industry that waste is still produced. NPJ nearly eliminates such waste. First, as mentioned, support structures are made using a soluble material that can be washed away, eliminating the need for manual support removal. This means users are generating less waste and can be more environmentally friendly. Additionally, the necessary sintering is done at a lower temperature and in shorter time, adding onto the environmental benefits while also reducing shrinkage, a critical issue in additive manufacturing.
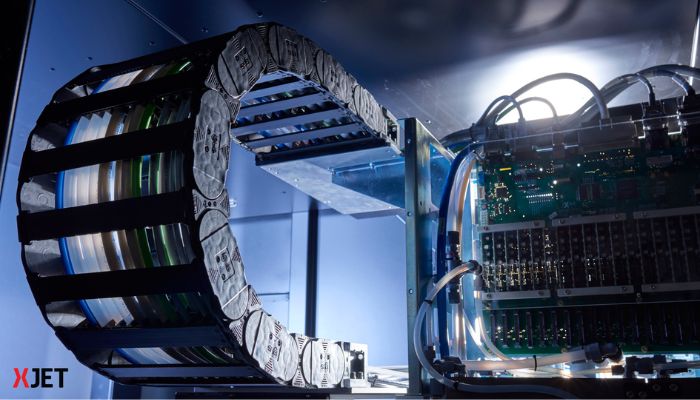
The inside of XJet’s powderless machine
Finally, thanks to the nature of the technology, parts made have a higher resolution are of a higher quality, especially in terms of surface roughness and properties of the finished part. The entire process is automated with little to no manual intervention, allowing for simplified production of metal and ceramic parts—which is especially important when it comes to adoption of additive manufacturing for end-use applications.
As a matter of fact, the technology can even be used to supplement traditional ceramic manufacturing. CeramTec, a global leader in technical ceramic manufacturing, recently acquired XJet’s solution as part of a dedicated AM manufacturing floor. The goal for the company is to expand its traditional capacity with advanced AM, thus opening up new applications and markets. You can learn more about the NPJ technology and XJet HERE.
What do you think of the NPJ powderless metal and ceramic process? Let us know in a comment below or on our LinkedIn, Facebook, and Twitter pages! Don’t forget to sign up for our free weekly Newsletter here, the latest 3D printing news straight to your inbox! You can also find all our videos on our YouTube channel.
*All Photo Credits: XJet