X-Plorer: The 3D Printed Jet Engine Made of 965 parts
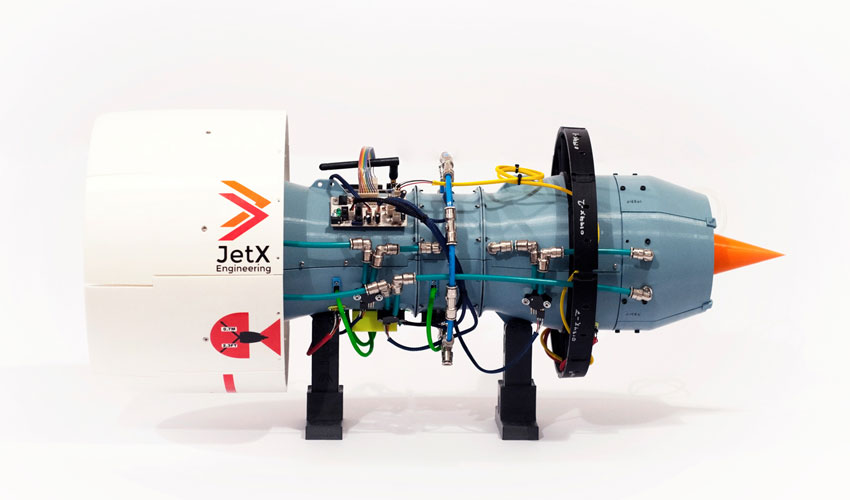
Developed by a group of engineering students named JetX, this functional 3D printed jet engine is one of the finalists of the Student Grant 3D Hubs competition. The competition is held to discover who can make the best project displaying 3D printing and its applications in engineering, design and architecture. JetX’s X-Plorer is a very special jet engine however, as it consists of over 950 3D printed parts.
965 Parts, 1 3D Printed Jet Engine
Previously, additive manufacturing has contributed to projects involved in planes and even space, within the engines, motors and turbines. However, this time an entire engine was 3D printed, once the 965 parts were assembled. It is also worth noting that the jet engine is fully functional.
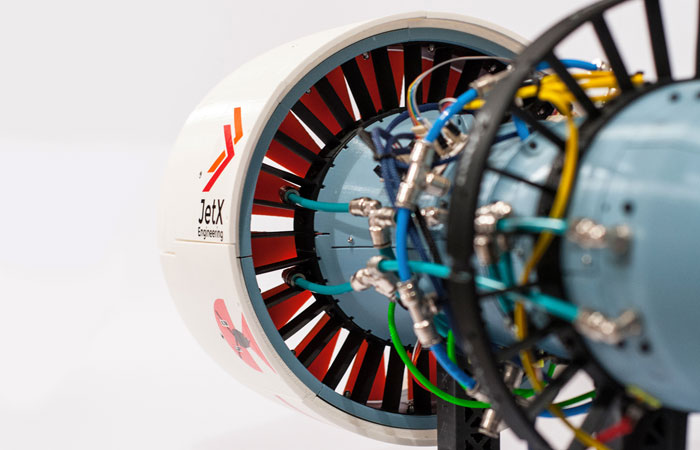
A closer look at JetX’s 3D printed jet engine
JetX: a Rolls Royce collaboration
Over 50 students of aerospace engineering at the University of Glasgow developed the X-Plorer in collaboration with Rolls Royce. The students used Fused Deposition Modeling (FDM) to create the engine, and used a DreamMaker Overlord Pro 3D printer. This versatile 3D printer can print PLA, ABS, Nylon and more. In the engine’s creation, parts varied from 7 minutes to print, up to a massive 58 hours! The final result was a jet engine 75cm long, with a 27cm diameter which weighed 8.1kg.
Before printing the pieces, the students had to carry out various analyses and models on the computer. Chris Triantafyllou, founder and founder of JetX, said, “The first step in optimizing the design is to perform computer analysis to see how the flow in the engine changes and how the effect is, what forces are acting and how affects the individual components. If multiple designs are possible for the same part, Computational Fluid Dynamics (CFD) analysis is performed with tools such as Solidworks Flow Simulation to see which design achieves the best results.”
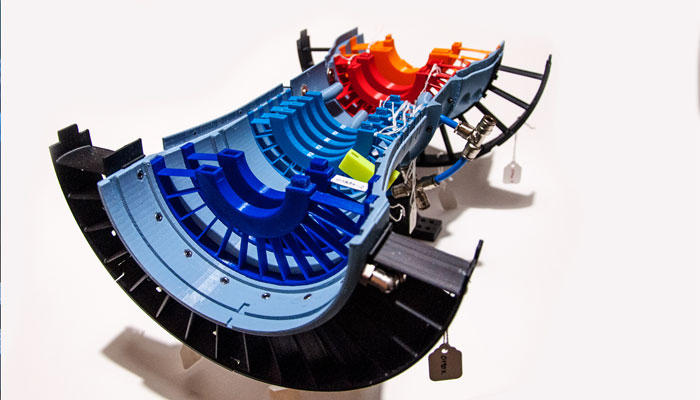
Inside JetX’s X-Plorer 3D printed jet engine.
The team installed a bespoke monitoring system inside the engine, including printed circuit boards and specially designed software. This system includes wireless transceivers, microcontrollers, temperature, pressure, and rotational speed sensors.
3D printing, a more efficient manufacturing method for JetX
Chris went on to explain further why they chose 3D printing technologies over CNC models, they were too expensive. He said “The implementation of a CAD to a finished part is easier and time is significantly shorter when using 3D printing and especially if it is an FDM 3D printer is.” Therefore, 3D printing was ideal for JetX for testing prototypes to achieve the desired design. They tested 21 prototypes in just 7 days before arriving on the correct model, which would have taken months using traditional manufacturing methods.
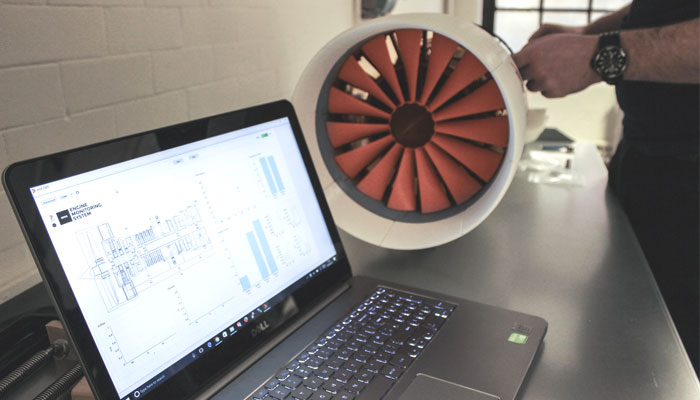
The laptop screen displays detailed CAD models for the X-Plorer 3D printed jet engine.
JetX plans to further improve its X-Plorer jet engine. With the help of Rolls Royce, the team will be able to advance technology and seek advice from industry experts on current practices. More information about the project can be found here or in the following video:
What do you think of the X-Plorer by JetX? Let us know in a comment below or on our Facebook and Twitter pages! Sign up for our free weekly Newsletter, all the latest news in 3D printing straight to your inbox!