#Working3D: Six Questions for a Footwear Engineer
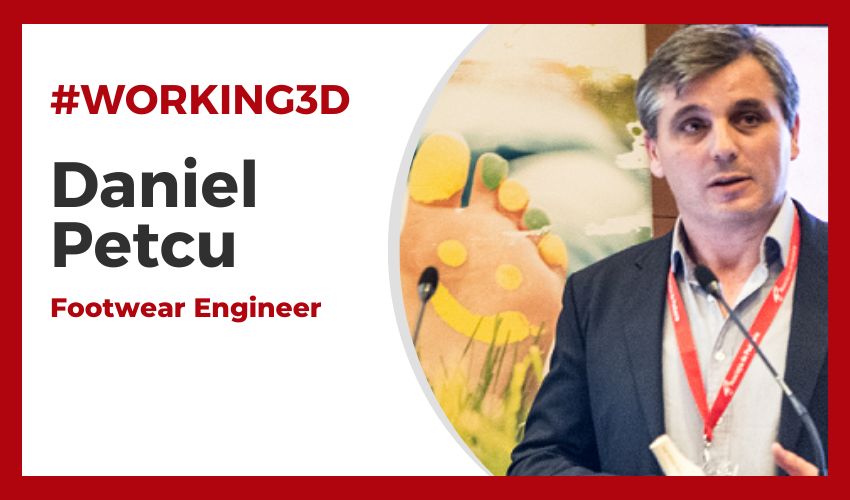
We have seen in numerous projects how 3D printing is being used to make shoes. This is especially the case for the consumer goods sector, where we are seeing particularly fashionable examples, but also sports shoes, which enable greater performance for athletes. However, it is also relevant for the orthopedic shoe industry, which focuses on creating footwear that contribute to the health of their wearers. Daniel Petcu focuses on the latter in his work as a footwear engineer. He has already been involved in numerous projects and designed the first complete 3D-printed orthopedic shoe presented in a case study at OTWorld 2024 in Leipzig, where he also wore a pair of 3D printed footwear created for him. We asked him a few questions to find out more about the work of a footwear engineer and the challenges he faces on a daily basis.
3DN: Could you introduce yourself?
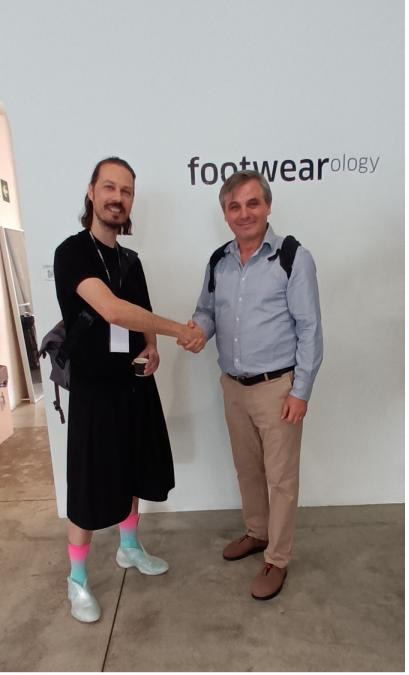
Petcu (right) meeting Philippe Holthuizen founder of Fused Footwear at Footwearology’s event in Barcelona.
I am a footwear engineer with a Ph.D. awarded based on a thesis focused on foot orthoses for diabetic feet. My interest is in the area of medical footwear (including foot orthoses) which is not included in the scope of practice of footwear engineers, so it was an extensive self-education process to gain knowledge in the Pedorthics field. I have developed the new concept of Pedorthic Information Modeling, defined as the environment for the digital representation of the aesthetic, physical, and functional characteristics of the information model of medical footwear.
The concept was translated into practice through a Grasshopper visual programming code and 3D-printing of foot orthoses and orthopedic footwear. The Pedorthic Information Modeling concept and the Grasshopper code are being continuously developed and tested to be further validated by practice. They have been presented at significant events such as OTWorld in Leipzig, Germany (2022, 2024), IVO-OST in Koln, Germany (2022), FootPRINT3D in Barcelona, Spain (2023), International Rhino User Meeting in Wroclaw, Poland (2024), Pedorthic Association of Australia Conference (2024).
3DN: How did you discover additive manufacturing?
I am not the type of engineer who likes to fix their car on their own or build the technical installations they designed! I am what you could consider an ‘all-thumbs’ engineer and never liked to develop my manual skills. But custom-made medical footwear is mainly about the traditional ‘handmade’ workflow that gives it its ‘flavor’. Then a couple of years ago, an inspirational interview in MAEKAN with Philippe Holthuizen from Fused Footwear made me change my mindset and see that it is possible to fully 3D print footwear. Because 3D printing aligns well with my desire to be independent in my work and to bring a complex product to life without developing my manual skills over time.
I identified with the man in the interview, and when I realized that I could transfer my ideas into a real product without depending on others and my manual skills, I said to myself, probably listening to Frank Sinatra: this is my way! More than that, being able to use it to ‘think’ about the (meta)materials for a given therapeutic purpose is fascinating. I’ve implemented different lattice structures in my programming code but when I realized that their testing/manufacture is not accessible to me I decided to focus on the more affordable FDM printing. I developed a Grasshopper code for Gradient Stiffness G-Code post-processing which will allow me to extend it not just to insoles/foot orthoses but also to midsoles and even fully 3D printed footwear.
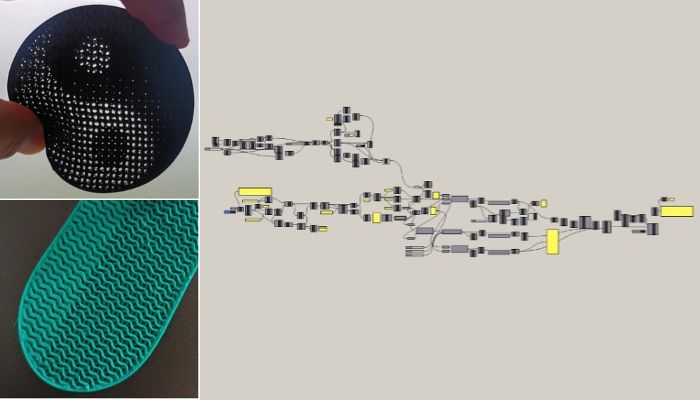
Grasshopper code for Gradient Stiffness G-Code post-processing
But the driving force behind the decision to “bet” solely on additive manufacturing was a particular medical footwear case, in which a nice young lady who could not stand upright or walk without shoes due to a permanent medical condition was in a very difficult situation. She was not able to find someone who would even try to replicate the solution I arrived at through traditional design and manufacturing methods eight years ago at my previous place of employment.
And here is the interesting thing – I am sure that in the countries with tradition in the hand-made driven workflow, she would have benefited from a solution. And this could be the problem with the countries having established a very functional traditional craftsmanship manufacturing system: once you have it it is hard to change it or at least to improve it thinking outside the box. Moreover, the education system that does not teach about parametric thinking and design does not sow the seeds of change or innovation.
This is why fields like AEC (architecture-engineering-construction) are highly innovative; they use parametric thinking and design. There are a lot of architects and computational/product designers dealing with fully 3D printed footwear but not with medical footwear. Why? Because they lack the medical knowledge (functional anatomy, biomechanics, pathomechanics,…) necessary to evaluate a clinical case and design the proper medical footwear.
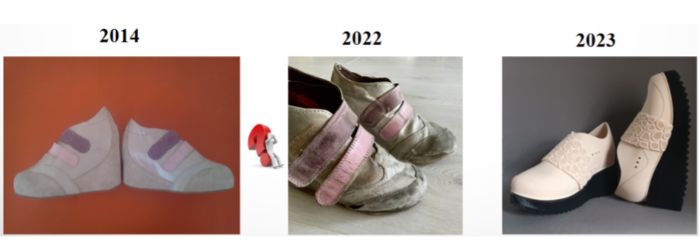
The road from traditional orthopedic footwear to the first fully 3D Printed one
This was my advantage: to know what medical, technical, and computational knowledge is needed to design and manufacture the medical shoe. Having this case as a reference I started to develop the concept of Pedorthic Information Modeling (an adaptation of Building Information Modeling from AEC to the Pedorthics). Initially, I developed it according to the traditional design workflow. But when I decided to buy my own 3D printer (because it was much more affordable than paying for a printing service), and I saw that I could bring ideas to life that otherwise were impossible to achieve through my manual skills, I deleted all the work related with the traditional workflow and decided to ‘bet’ only on 3D printing.
In 2022, the lady kindly asked me to try to solve her shoe problem, and the only way to solve it totally independently was through 3D printing. A powerful argument to me to go forward just with 3D printing and to give me the chance to be the first one who has designed and manufactured the first fully 3D printed footwear worn daily by the patient/customer.
But additive manufacturing also has the potential to help you create new types of designs by yourself or in collaboration with other digital/computational designers. That is what I have tried to do with Oran Sheinman. Additionally, it opens the way to collaborate with local artists in a mixed traditional-digital workflow as was the case with Corina Coroi where the shoe sole and foot orthoses were 3D printed while leather uppers were traditionally manufactured and attached to the sole with a 3D printed sealing system.
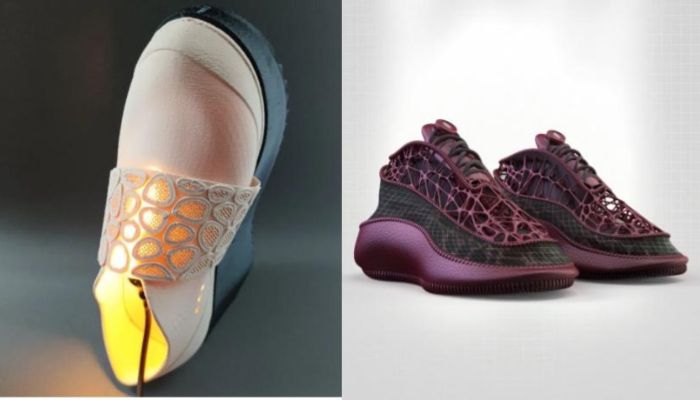
Left: Petcu’s fully 3D Printed shoe; Right: Collaboration with computational designer Oran Sheinman.
3DN: What is your current role and what is a typical day like for you?
I would say I have two roles: the one that gives me the financial input is about delivering foot biomechanical evaluations for a Podiatry clinic. The second one is the “one-man orchestra” and is about developing the Pedorthic Information Modeling till the phase where I’ll be able to use in my practice the products (3D printed medical devices) developed based on it and according to the regulations. This means learning while testing while developing as the concept (Pedorthic Information Modeling) and tools (Grasshopper code) feed and develop each other.
3DN: What qualifications and experience are required to work as a footwear engineer using 3D printing?
I graduated from technical college 30 years ago, when the only computer-related subject was basic programming. Certainly, it has nothing to do with shoe design! However, I was fortunate to have a mentor who spent many unpaid hours teaching me how to solve a programming problem by primarily designing its algorithm. Still, I have the same thinking now but now with the benefit of Grasshopper visual programming language.
As far as I have seen the footwear engineering schools don’t teach students how to think and design parametric but rather how to use existing expensive proprietary footwear software design solutions already well established on the market which makes them schools of ‘users’ and not of ‘thinkers’ as a school at a university level should be. This is why if you are looking at those who are printing shoes you will see mainly architects or computational designers! Because they are learning how to think and create code to solve their problems and not just use existing proprietary software solutions.
3D printing footwear is still at its very beginning so we can’t speak about too much experience in the field. But as knowledge, there is a need for computational/algorithmic/parametric thinking and design, visual programming, and of course 3D printing technology/materials/metamaterials. If there is an interest in medical footwear and the school doesn’t provide real specific medical knowledge, then there is a need for a lot of study of biomechanics, pathomechanics, functional anatomy, medical device regulations, etc.
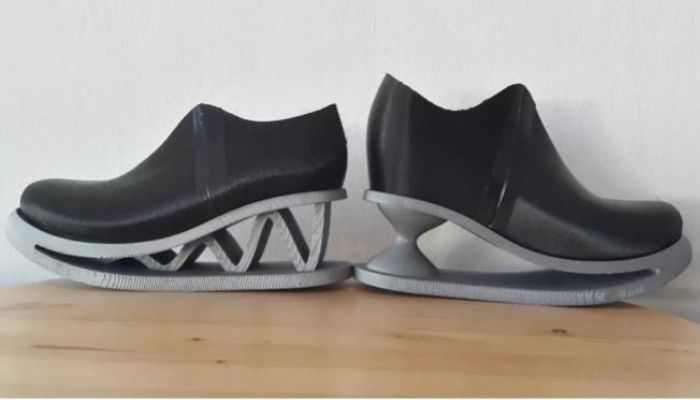
Petcu’s first exercise with shoes 3D printing based on the Grasshopper code.
3DN: What are the biggest challenges you face?
Since the Pedorthic Information Modeling project has reached sufficient maturity, the biggest challenge is to bring products designed based on this concept into my clinical practice. Then, to demonstrate that fully 3D printed medical footwear is suitable for very difficult cases, such as Charcot-Marie-Tooth. From this point of view, I believe that the 3D printing of shoe uppers represents the biggest technical challenge in terms of physico-mechanical, hygienic, and aesthetic properties. Patients’ adherence to wearing therapeutic footwear depends on their perception of the aesthetics of the footwear and of the materials used, and comparisons will constantly be made with the traditional materials used, especially leather, considered to be safe for feet.
3DN: What advice would you give to someone hoping to work as a footwear engineer using additive manufacturing?
First of all, develop parametric thinking leading to parametric design through visual programming. Rhinoceros-Grasshopper is an excellent environment with a huge community where you can get answers to your questions. Then focus on affordable and reliable 3D printing methods to test your ideas easily without significant financial pressure. If possible, buy your own printer.
Following creative people who are on their own road with 3D printing is an important information resource. Ask when in trouble, without fearing your questions are stupid and feeling embarrassed because of them! Generally, people are glad to answer questions and when a problem seems to be without an answer there are plenty of resources helping to solve it.
Search for the main events on additive manufacturing and participate because next to meeting people you are following you can see and feel similar 3D printed products – and this is mandatory! Wear your own 3D printed shoes there even if you think they are not the stylish ones. Last but not least: trust your senses and have patience. 3D printing takes time, but while the printer is working you can learn how to develop your ideas!
Here you can find more about Daniel Petcu and his work. What do you think of the role of a footwear engineer using additive manufacturing? Let us know in a comment below or on our LinkedIn, Facebook, and Twitter pages! Don’t forget to sign up for our free weekly newsletter here for the latest 3D printing news straight to your inbox! You can also find all our videos on our YouTube channel.
*All Photo Credits: Daniel Petcu