#Working3D: Six Questions for a Additive Manufacturing Materials Engineer
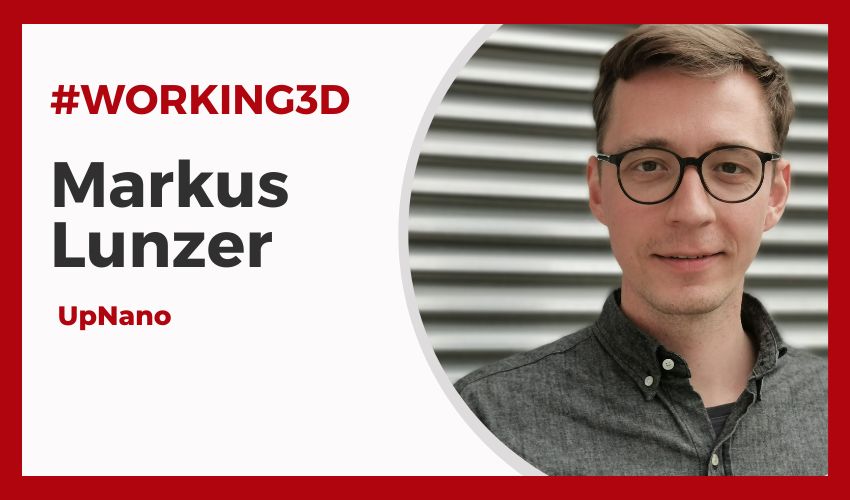
It’s time once again for a new article in the #Working3D series, wherein we present the various professions in the additive manufacturing industry. But no material, no print – that’s why this time we’re taking a closer look at the jobs of the people behind the material and who develop it. What exactly do engineers who are responsible for materials do? What skills and experience do they bring to the table so that 3D printing materials can be created and used for additive manufacturing in a wide variety of areas? We explored these questions in conversation with Markus Lunzer, Team Leader for Materials & Application at the Viennese company UpNano GmbH. He explained what a materials engineer needs to bring to the table and what his day-to-day work looks like.
3DN: Could you introduce yourself?
My name is Markus Lunzer. I studied technical chemistry at the Vienna University of Technology (TU Wien), with a special focus on synthetic chemistry. As part of my dissertation, I worked on photopolymerization and light-cleavable hydrogels. After completing my studies, I started working in materials development at the then newly founded 2-photon 3D printing company UpNano GmbH in 2019, where I have been leading the materials and applications team for four years.
3DN: How did you discover additive manufacturing?
During my master’s thesis, I synthesized molecules that were particularly suitable as photoinitiators for 2-photon polymerization (2PP) due to their structure. This is a particularly high-resolution 3D printing technology that uses a pulsed laser and makes it possible to produce components with resolutions in the sub-micrometer range. While testing these molecules on machines at the university that were still experimental at the time, I realized how exciting this technology is and how much potential it has as a manufacturing technology. So I decided to take a closer look at the application of the technology in my dissertation, while retaining the material development aspect. I then worked on hydrogels for biomedical research, which can be cleaved at a very high resolution using 2PP, for example to create microchannels or locally expose reactive chemical groups.
However, the disadvantage of the high resolution of the 2PP was that it was relatively slow, as a printed component was made up of many tiny voxels. Around this time, however, work was carried out on a prototype of a much faster 2PP system as part of a research project at the Vienna University of Technology. This machine was the basis for the foundation of UpNano GmbH. With this, it was suddenly possible to print much faster and thus also to advance into unimagined sizes for this technology, namely the cm range and below.
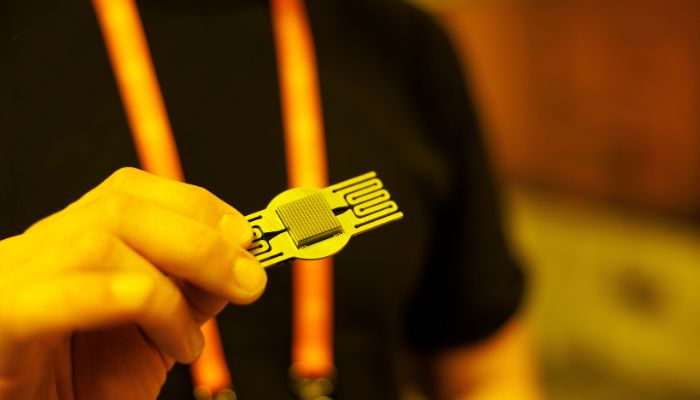
With 2-photon polymerization, components can be 3D printed in the sub-micron range (photo credits: Rainer Fehringer)
3DN: What is your current role at UpNano? What is a typical day like for you?
As I mentioned, I lead the materials and applications team at UpNano. Together, we develop new 3D printing materials and application processes and carry out feasibility studies with (potential) customers. Another important activity is the production and quality control of the existing material portfolio. As we operate in a high-tech field, there is also a lot of interaction with customers and users. As our customers are scattered all over the world, this also results in some interesting trips.
3DN: What qualifications and experience are required to work as a Materials Engineer?
The applications of our 2PP technology are extremely exciting as they cover many different scientific and technical fields. We have customers who print integrated microfluidic devices for in vitro fertilization, others who manufacture micro-optics or tiny components for medical devices and still others who work with hydrogels on 3D cell cultures for pharmaceutical research.
I can say that I can apply knowledge from all the areas that I learned about during my broad studies to my work. There are customers for whom printing materials with certain characteristics, such as defined mechanical properties, are important. Others need materials that are as colorless as possible, or want components made of ceramic or glass at the end of the production process. This requires a great deal of detailed knowledge in material production, as well as in analytics and metrology.
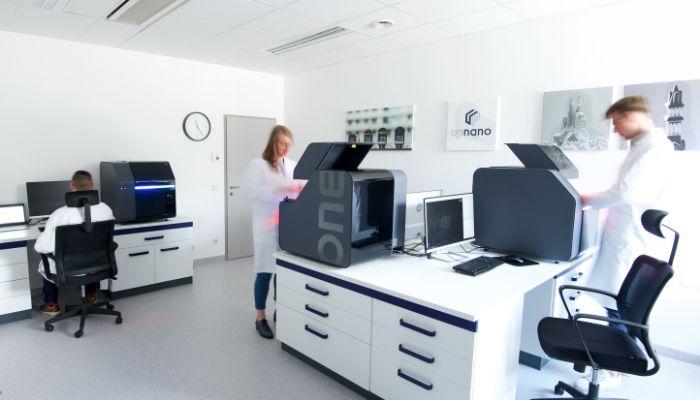
Together with customers, Lunzer and his team develop new 3D printing materials and application processes. (photo credits: UpNano)
A large proportion of our customers are also top researchers from academia. We are working on a highly innovative technology that is currently the focus of much research. In this respect, it is important to keep abreast of the latest scientific developments in the 2PP field. I wouldn’t want to miss out on scientific work. Our team is involved in several exciting and highly topical research projects, ranging from cancer research and biomedical engineering to high-precision manufacturing techniques. Through scientific publications, we can make the strength of our technology known to a wider audience and demonstrate the potential of 2PP.
3DN: What are the biggest challenges you face as a Materials Engineer?
The aim is always to develop a reliable and universal solution to a problem, because we want to offer a solid process for industrial production. Challenges often only become apparent at an advanced stage of product development, as our application is very broad and we cover dimensions from the nanometer to the centimeter range. It is important to recognize these challenges, identify the causes and then use our expertise to resolve them. I am very happy to be working with a team of extremely talented and enthusiastic people. Many solutions are developed in close collaboration with our software and hardware team, as the three areas of material, software and hardware are so closely linked in 3D printing.
3DN: What advice would you give to someone hoping to work as a Materials Engineer in additive manufacturing?
It’s always good to know about the latest trends and developments. However, when you’re fresh out of training, a certain amount of rethinking is sometimes necessary. In research, attempts are often made to make the initially almost impossible possible. This is very often impressive and an important incentive for many later developments. In industry, however, it is also about creating reliable and stable solutions to a problem. It often turns out that the simpler solution is not only more efficient, but also more useful and universal.
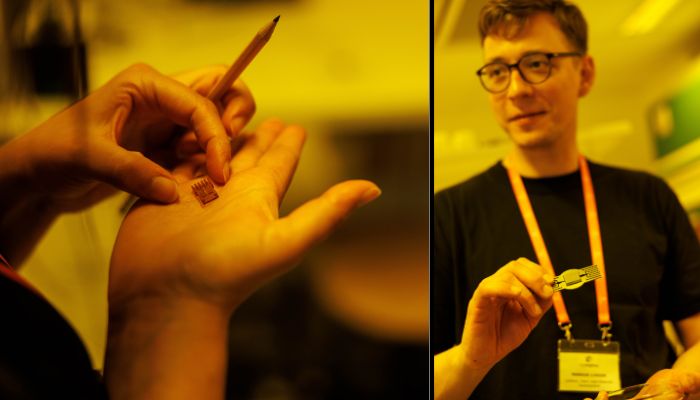
Recognizing challenges, identifying causes, proposing solutions – this is part of a materials engineer’s daily business when developing new materials for 3D printing (photo credits: Rainer Fehringer)
What do you think of the job of a materials engineer in additive manufacturing? Let us know in a comment below or on our LinkedIn, Facebook, and Twitter pages! Don’t forget to sign up for our free weekly Newsletter here, the latest 3D printing news straight to your inbox! You can also find all our videos on our YouTube channel.
*Cover Photo Credits: Markus Lunzer, UpNano