#Working3D: Six Questions to Understand the Job of R&D Engineer
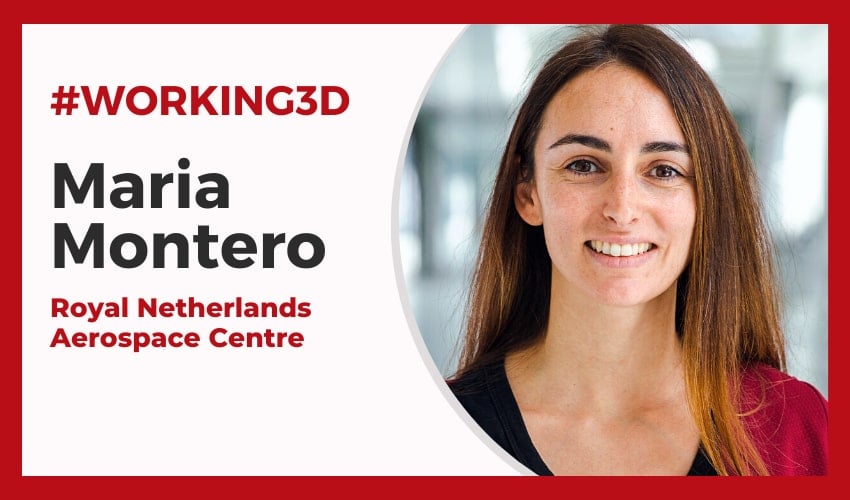
With the rise of industrial additive manufacturing, many companies are looking to hire profiles specialized in these new technologies, capable of fully making the most of its advantages. This is what we have seen on our dedicated job board, where more than 900 job offers related to the 3D sector were published last year. To continue exploring the world of work, we offer #Working3D, a series of articles that aim to present the different jobs available in the additive manufacturing market. If you’re interested in working in this field, then you’ve come to the right place! After discovering the role of Emilien Goetz at Siemens and Lorenzo Mastria at Roboze, today we explored one of the fields particularly interesting for a market in constant search of innovation. We met Maria Montero, R&D engineer at the Royal Netherlands Aerospace Center (NLR).
3DN: Could You Introduce Yourself?
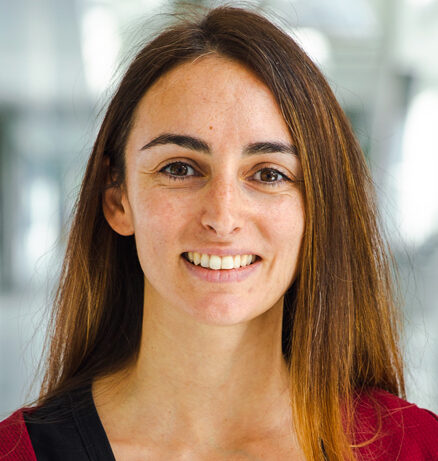
Maria Montero Sistiaga
My name is Maria Montero Sistiaga and since 2020 I have been an R&D Engineer at Royal Netherlands Aerospace Centre (NLR). My background is in materials engineering and I have a doctorate degree in Materials Engineering from the University of Leuven (KU Leuven). At NLR, I focus on bringing AM technologies to a higher level, mainly laser powder bed fusion (LPBF) and directed energy deposition (DED).
3DN: How Did You Discover Additive Manufacturing?
During my bachelor’s degree, in 2011, I had the opportunity to go on Erasmus to KU Leuven (Belgium) for my bachelor thesis. There, I spent a year working with 3DSystems (former Layerwise) and KU Leuven on the process optimization of tantalum and tungsten. This was my very first experience with AM, and since then I haven’t left the AM world. It was very enriching to be part of such a pioneering group on AM, the group of Prof. Kruth and Prof. Van Humbeeck at KU Leuven.
After my bachelor’s, I decided to stay in Leuven for my master’s and PhD where I could further develop my skills in alloy design, process optimization, mechanical characterization, powder production and microstructure investigation for LPBF.
After fruitful years in Leuven, I had the opportunity to start as R&D Engineer at the Royal NLR where I still keep learning thanks to the multidisciplinary AM team we have. NLR is an applied research center where we try to bridge the gap to transform potential concepts (from basic research) into practical solutions meant for the industry to continue with.
3DN: What is Your Current Role at NLR? What Is a Typical Day Like for You?
At NLR, I am an R&D Engineer and I am involved in several AM-related projects. I work with three main metal AM technologies: LPBF, DED and metal-filled fused filament fabrication (FFF or also known as FDM). As an R&D Engineer, I work both on the technical as well as on the project management side, which makes every day different. My day consists of assisting several meetings to follow the progress of the project or to discuss results, as well as going through the labs to follow the progress of activities done at the printers or the testing facilities.
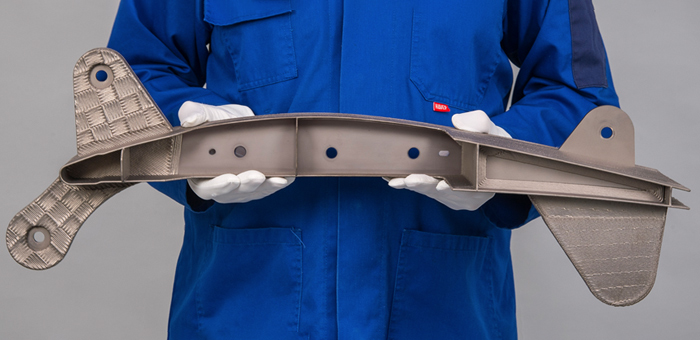
3D printed flaperon rib using DED technology (photo credits: NLR)
In R&D, we do not aim for repetitive work. Every project is unique, so every time new challenges arise from which we learn. In those cases, we meet with the working group and discuss the possible solutions. The benefit of working at NLR is that we can cover almost every step of the AM chain in-house thanks to the diverse facilities and team we have.
An example of a recent project was the production of a flaperon rib for the next-gen aircraft by titanium DED. This was the first time we were producing such a big and complex part in titanium. Therefore, we developed a production approach to build the rib with the highest quality and accuracy and minimize deflections. For that, several critical design features were optimized before producing the final part. This project was very challenging due to the size of the component and the residual stress build-up of titanium. However, it was a great opportunity to learn about the limitations of DED and a way to think outside the box.
3DN: What Are the Qualifications Or Experience Required to Do Your Job?
The advantage of AM is the versatility, since there are different disciplines that play a role when working on AM and therefore where R&D can focus: data analysis, digitalization, simulation and modelling, mechanics, material science, chemistry statistics, machine building… As such, my current position requires a combination of qualifications. On one side, knowledge of 3D modelling tools is helpful and on the other side, being experienced in the relationship between the process, material characteristics and final part performance. Therefore, I would recommend an engineering school either focused on mechanics or materials.
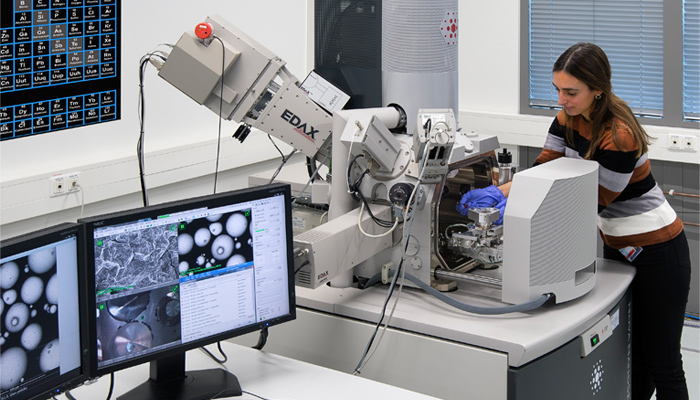
Photo Credits: NLR
3DN: What Are the Biggest Challenges You Encounter as an R&D Engineer?
The main challenge we find is building up trust in the technology. Besides the great efforts that the AM community is doing on building up knowledge and maturing the technologies, there are still steps to be done towards certification and qualification. This process of course depends very much on the sector. In the case of aerospace, certification becomes even more critical. Currently, the qualification approach is part-based, which means a fixed design, platform configuration, parameter set, powder batch and machine. In the case a small change needs to be done, for example to the design, the whole qualification process needs to be repeated. This is of course very time-consuming and requires an in-depth understanding of the process-material-design relationship. At NLR, we are currently working on new virtual qualification and certification approaches for AM.
3DN: What Advice Would You Give To Someone Wanting To Work In R&D?
I think the most important is to be willing to try a different job, willing to learn and be open to constant challenges. Especially in AM, the technology is evolving very fast and there are many challenges still to overcome. So if you like to look for solutions and to make things better and more efficient, there is plenty of opportunities within the AM world. Moreover, AM technologies cover several engineering disciplines making it an exiting field for many engineers.
What do you think of our #working3D series? Would you want to work as a R&D engineer? Let us know in a comment below or on our LinkedIn, Facebook, and Twitter pages! Don’t forget to sign up for our free weekly Newsletter here, the latest 3D printing news straight to your inbox! You can also find all our videos on our YouTube channel.
I find the 3D printing of languages a fascinating creation of an (almost) intangible thing! Where can I get copies of these for my art collection? (If I could afford the)