#Working3D: Six Questions for an Additive Manufacturing Innovation Engineer
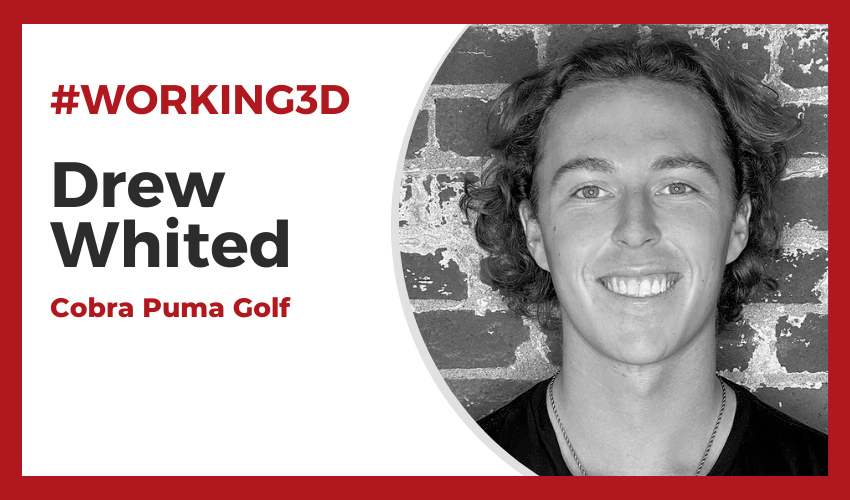
We are back with the #Working3D series in which we get to know first-hand the different professions in the 3D printing sector. On this occasion, we will learn about the day-to-day life of an additive manufacturing innovation engineer. Closely related to product design and development, this job consists of identifying opportunities and creating integrated technology-based solutions, in an innovative and sustainable way, in this case applied to 3D printing. To learn more, we met Drew Whited, innovation engineer at Cobra Puma Golf, who works in the world of additive manufacturing in the world of sports, specifically the development of golf equipment. We caught up with him to find out more about the position, the qualifications required and what his routine is like at work.
3DN: Could you introduce yourself?
My name is Drew Whited and I currently work at Cobra Puma Golf as an Innovation Engineer within our Innovation team. I graduated from Eastern Washington University with a B.S in Mechanical Engineering followed by an M.S in Sports Product Design from the University of Oregon. While attending UO I specialized in equipment design with my thesis project focusing on designing and building a set of golf clubs for the niche world of Urban Golf (golfing on the street). This eventually led to my introduction into the golf industry and my career at Cobra Puma Golf where I am helping to build new design and manufacturing workflows that utilize computational design techniques blended with traditional and additive manufacturing methods to build innovative and high performing golf equipment.
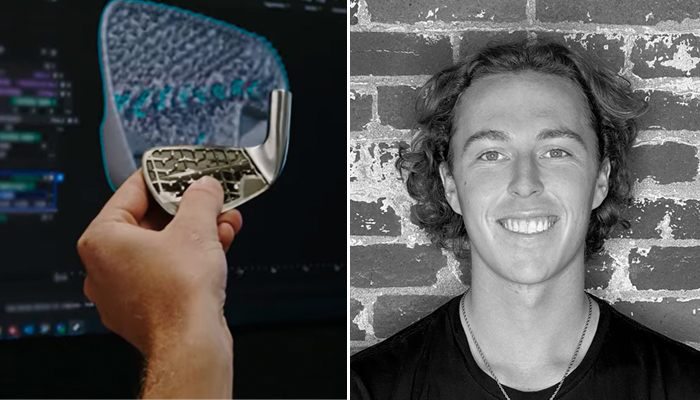
On the right Drew Whited, innovation engineer at Cobra Puma Golf.
3DN: How did you discover additive manufacturing?
My undergraduate capstone project was my first introduction to additive manufacturing. My team and I were tasked with designing and manufacturing a hydraulically controlled prosthetic foot for a fellow teammate. Throughout the design process we quickly learned the advantages of the rapid iteration capabilities additive offers where we were able to quickly print components for both shape validation and tolerance verification. As well, for our final design additive played a key role in helping to reduce weight savings and manufacturing cost through the use of a continuous carbon fiber reinforced nylon printed via FDM which helped to reduce weight, save on manufacturing costs, and offer strength comparable to some metals.
Further introduction to metal additive came through my thesis project where the three clubs I designed (putter, iron, driver) were all printed using 316L stainless steel via binder jetting process. This helped to remove design restrictions to achieve parts that would not be possible with traditional methods such as casting or forging as well as cutting down on time and prototyping cost dramatically by being able to avoid manufacturing a casting or forging tool.
3DN: What is your current role at COBRA Puma Golf? What is a typical day like for you?
My current role is Innovation Engineer. Within our innovation team it is our job to dream up the next big ideas to be used in future generations of golf clubs whether that be through new materials, processing, shaping, construction, or manufacturing methods. We achieve this through brainstorms and ideation followed by design/manufacturing and validated through various testing methods to ensure design goals are met.
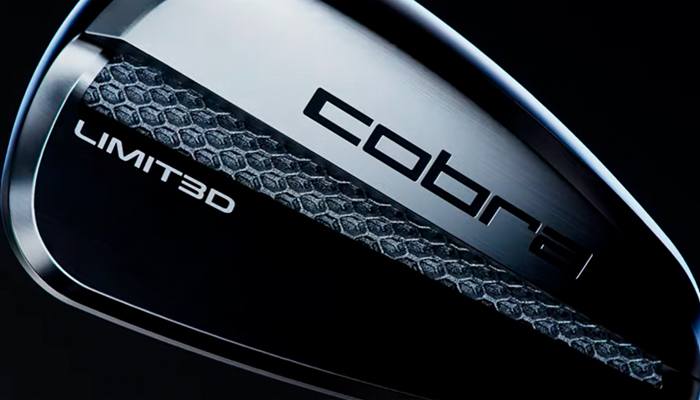
The Limit3d created with additive manufacturing (photo credits: Cobra Puma Golf)
As stated previously, much of my job is focused on designing computational design workflows which incorporate multiple different software packages which are controlled and connected through a coding environment. This allows us to iterate over a countless array of design possibilities using design goals as inputs and reach an optimized design in a fraction of the time compared to traditional CAD methods. Utilizing these methods, we can not only evaluate more designs in less time but also focus on the creativity aspect of the design process rather than the time-consuming CAD work that typically slows down the design process. Here at Cobra Puma Golf we are the leader in additive manufacturing within the golf equipment space, highlighted by latest release of the Limit3d iron – the first 3D printed iron available to the consumer, which lends itself to this type of workflow being able to manufacture new designs that forging and casting cannot.
3DN: What qualifications and experience are required to work as an Innovation Engineer?
Most CAD engineers here at Cobra Puma Golf have backgrounds in mechanical engineering which is a great starting qualification but more importantly is a desire and skill of learning rapidly. Within the golf industry we must focus on all aspects of the club including materials, processes, design, testing, and manufacturing and while a depth of knowledge in all those areas would be beneficial it is largely unobtainable goal for a single engineer. Therefore, we are required to adapt and learn constantly to look into the future of what is possible and to ultimately make a better performing club. Showing experience in encountering problems and how you overcame those problems is the most important characteristic. Even if you don’t arrive at the solution you desired, problem solving will often teach you things you didn’t expect, and you will be better prepared to face the next obstacles.
3DN: What are the biggest challenges you face?
In the golf industry, we are constantly in a battle between aesthetics and function. Golfers expect a high performing club that will in some way help them play better, whether that be more distance, forgiveness, spin, etc. but at the same time expect this piece of equipment to look like a piece of jewelry even while repetitively beating it into the ground. This balance is a large part of the job, where you can design the highest performing club in terms of a given design goal but maybe makes the club so large that the golfer can’t stand to look at it.
On the other end you can make a small and sleek clubhead that to the golfer looks amazing but put into the hands of an elite player, cannot seem to hit it to their desired consistency. This remains a big obstacle in the job but luckily, with additive we can bridge this gap more than ever before. Through the use of new multi material constructions and weight savings methods, utilizing lattice structures, we can offer the mass properties of a game improvement forgiving club with the looks of a player’s iron.
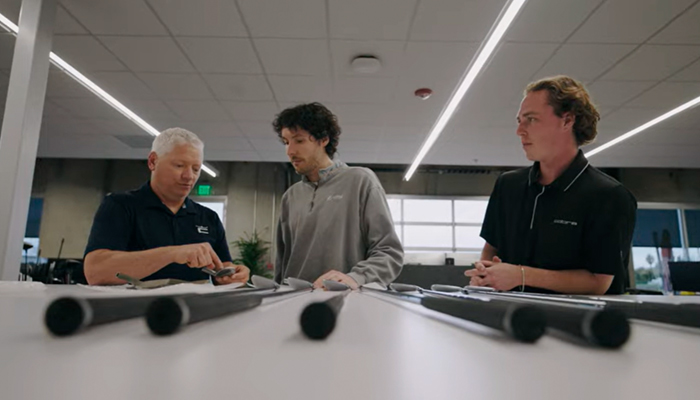
Photo Credits: Cobra Puma Golf
3DN: What advice would you give to someone hoping to work as an Innovation Engineer in additive manufacturing?
Be ready to learn and adapt quickly. Additive is evolving at an astounding rate with new machines, materials, and process methods being introduced constantly allowing for new design capabilities. In any competitive industry, especially golf, to keep producing high level innovative products new technologies must be adopted quickly and effectively. In the golf industry, additive is finally starting to gain support which is very exciting. However, being a new technology, this creates new challenges and constraints that must be understood.
Lattice types are a great example of this where no previous golf products had incorporated lattice within its construction, until our Limit3d irons. This presented itself with many obstacles to overcome such as lattice type, beam thickness, positioning, lattice orientation, print orientation and more. To be able to make these clubs high performing and stick to the product timeline all these factors had to be learned quickly to arrive at a product launch. This sentiment holds true in any industry utilizing additive where with every new technology new learning and problem solving will need to take place at a fast pace in order to arrive to effective solutions.
What do you think of the position of innovation engineer in additive manufacturing? Let us know in a comment below or on our LinkedIn, Facebook, and Twitter pages! Don’t forget to sign up for our free weekly newsletter here for the latest 3D printing news straight to your inbox! You can also find all our videos on our YouTube channel.