Why Does 3D Printed Stainless Steel Corrode in a Marine Environment?
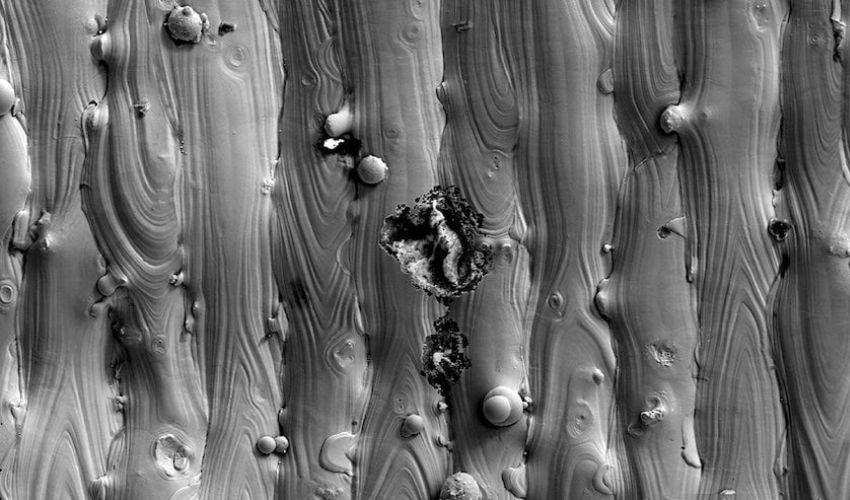
Why is 3D printed 316L stainless steel prone to pitting corrosion in seawater? That is the question researchers from Lawrence Livermore National Laboratory have been diligently trying to answer. Their thorough study of this metal, utilized in naval applications, aims to uncover the underlying causes of its degradation. Their findings suggest that slag, left behind during laser melting, accumulates on the surface of the material, resulting in the formation of cavities or pits.
Used in many industrial applications, metals are often subject to corrosion, i.e., degradation by chemical reactions caused by the environment. Corrosion can be controlled, but it’s important to know what causes it. There are several forms of corrosion, including pitting. In concrete terms, the metal undergoes degradation of its protective oxide layer, and loses electrons in the process. When present in an aquatic environment, an electrochemical reaction occurs, resulting in the creation of small holes, hence the name “pitting corrosion”. The severity of the repercussions for the part in question varies depending on the depth of these cavities. Interestingly, controlling pitting corrosion in seawater poses significant challenges. This is precisely why naval applications opt for 316L stainless steel, known for its exceptional mechanical properties and resistance to such pitting corrosion.
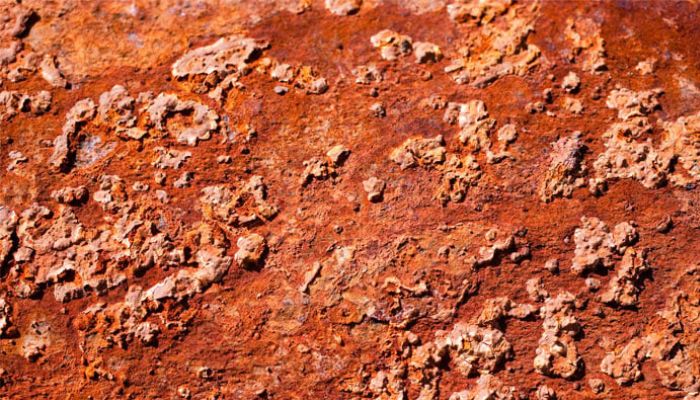
Meta degradation (or corrosion).
However, can 3D printed 316L stainless steel effectively mitigate pitting corrosion? With the marine industry showing a growing interest in additive manufacturing, both in polymer and metal, this question gains significance, particularly concerning metal certification. This is the very reason why researchers at Lawrence Livermore National Laboratory embarked on this study. Lead author Shohini Sen-Britain explains, “Pitting corrosion is extremely difficult to understand due to its stochastic nature, but we determined the material characteristics that cause or initiate this type of corrosion. While our slags looked different than what had been observed in conventionally manufactured materials, we hypothesized that they could be a cause of pitting corrosion in 316L.”
In their study, the team discovered that 3D printed metal was also subject to this pitting corrosion phenomenon, and that it was caused by slag created by deoxidizers such as silicon and manganese. However, when using more traditional manufacturing processes, this slag can be removed using tools such as grinders. In additive manufacturing, however, this type of post-treatment no longer makes sense.
Employing methods like transmission electron microscopy and ion beam milling, the researchers closely examined the slag present in the 3D printed metal and drew significant conclusions. They discovered that these processes created discontinuities within the steel, enabling seawater infiltration and subsequent degradation of the part. This discovery opens avenues for modifying the material’s mechanical properties and enhancing its corrosion resistance, thereby broadening its potential applications. Understanding the mechanisms underlying slagging could lead to the design of components with enhanced water resistance, durability, and structural integrity.
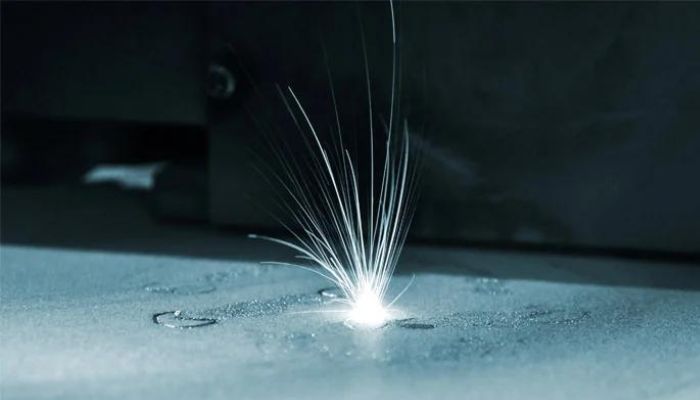
Laser melting on a powder bed could provide a better understanding of pitting corrosion.
The researchers add, “When we 3D print the material, it’s better for mechanical properties, and from our research, we also understand that it’s better for corrosion as well,” Voisin said. “The surface oxide that forms during the process is developing at high temperature, and that also gives it many different properties. What’s exciting is understanding the reason why the material corrodes, why it’s better than other techniques and the science behind it. It is confirming, again and again, that we can use laser powder bed fusion AM to improve our material properties, way beyond anything we can do with other techniques.”
This entails altering the formulation of the metal powder from the initial stages, ensuring the removal of silicon and manganese, known culprits for slag formation and subsequent corrosion. It marks a promising progression, not only for the maritime domain but also for various other rigorous industries! To learn more about this project, click here.
What do you think of this explanation of pitting corrosion? Let us know in a comment below or on our LinkedIn, Facebook, and Twitter pages! Don’t forget to sign up for our free weekly newsletter here, the latest 3D printing news straight to your inbox! You can also find all our videos on our YouTube channel.
*All Photo Credits: Thomas Voisin/LLNL