What were the 3D printing trends of 2019?
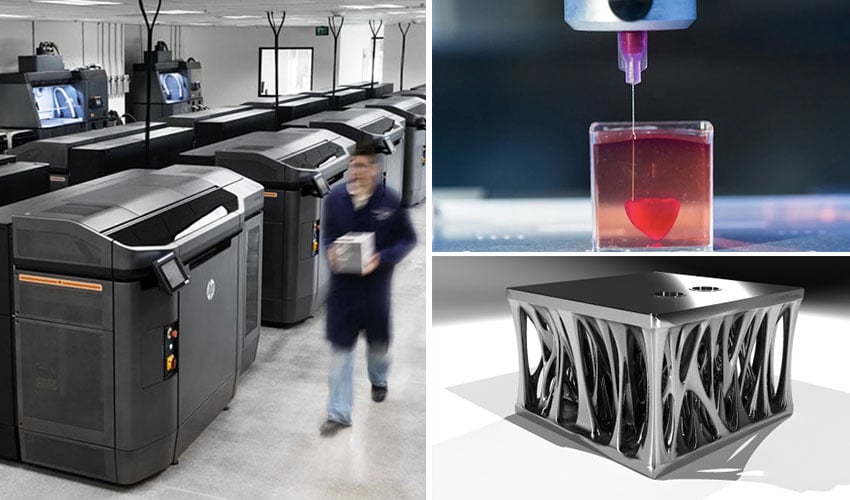
Are you wondering about the state of 3D printing in 2019? What to expect for 2020? Today, we look back on the trends that shaped the AM industry in 2019! Underlying all these trends is the fact that additive manufacturing is becoming a production-ready process, which means that the involvement of companies and players in the industry is growing. We identified 5 3D printing trends in 2019, which we present to you below!
Industrial Scale 3D Printing
3D printing will not substitute traditional manufacturing methods, nevertheless in complementing these methods, it can transform manufacturing across industries. In Essentium’s survey, the number of manufacturers who’ve incorporated additive manufacturing for full-scale production doubled compared to 2018. Over the course of 2019, we’ve observed a wider adoption across sectors and an increased number of industrial solutions brought to market by manufacturers – just consider the number of industrial solutions unveiled at Formnext 2019! 3D printing technologies have always had this potential but in the past, barriers to entry have limited their use. Another interesting fact from the Essentium-commissioned study reveals that 47% of companies surveyed are using additive manufacturing for runs of thousands of parts in 2019, compared to 17% in 2018. For example, HP is working with Volkswagen to 3D print parts at scale. This year, the car manufacturer installed 90 HP printers in its factories and produced 10,000 parts in just a few weeks. Volkswagen’s goal is to print 50,000 to 100,000 functional parts the size of a football per year.
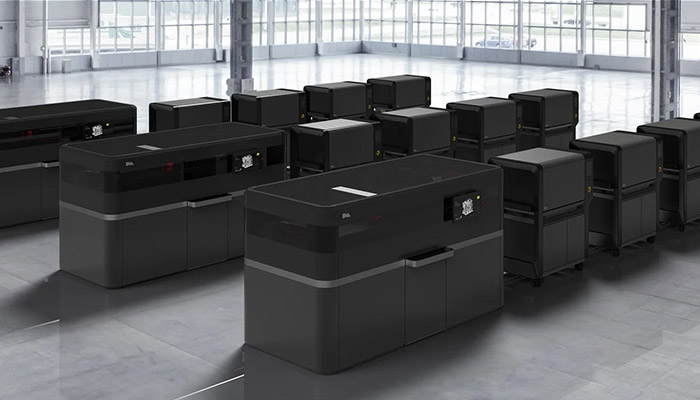
Desktop Metal’s Production System | Credits: Desktop Metal
As for the machines themselves, larger and more industrial systems are now available. In a study by CONTEXT, shipment of industrial machines, experienced a year-on-year growth rate of 18%. Take Carbon’s launch of the L1 for example, used by multiple leading companies such as adidas, Riddell or Specialized for their production. Additionally, artificial intelligence, as well as machine learning is enabling 3D printers to operate by themselves for larger, more efficient production and automation. For example, the MIT-developed 3D printer, Inkbit, aims to be a solution for industrial production by using machine-learning and machine-vision technologies in order to correct 3D printing errors in real-time. Moreover, specialized software such as 3YOURMIND or AMFG’s allows for companies to automate their additive manufacturing production seamlessly. Finally, post-processing, one of the key steps in the additive manufacturing workflow is also experiencing a revolution. Automatization of post-treatment is advancing rapidly, as seen by solutions like PostProcess Technologies’.
Design for Additive Manufacturing
Additive manufacturing has introduced an enormous amount of design freedom and unique capabilities to manufacturing. For this reason, specific design methods for AM technologies have emerged, called Design for Additive Manufacturing (DfAM). These techniques have enabled to create new designs and innovation for a range of sectors. Consider the Uptis puncture-proof tire as a perfect example of how studying and adapting the design of a part can change its function. MX3D is another company that showcased some of the ways you can optimize parts by modeling them with DfAM techniques such as generative design, topology optimization, etc. Behind these design methods is sophisticated software. nTopology is one of the software that enables to take full advantage of additive manufacturing technologies. We can also mention Hyperganic’s software which allows users to design objects as complex as nature. Overall, we’ve seen a growing number of examples of AM designs that optimize the functional performance, cost and reliability of parts this year. The success of these techniques is largely due to their ability to cut costs and manufacturing time!
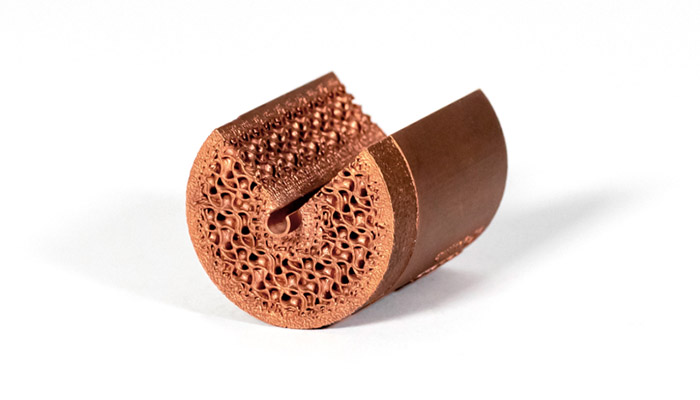
An iteration of a 3D printed heat exchanger | Credits: Hyperganic
Materials
Materials have been at the centre of many advancements this year. As expected, the thermoplastics market continues to grow each year. Nevertheless other AM materials are catching up: metal additive manufacturing has been growing especially fast, confirmed by Wohlers’ 2019 report, which announced that the revenue from metal had grown by 41.9% since 2018. In fact, Formnext 2019 was the perfect opportunity to experience firsthand how many players in the market were betting on this segment of additive manufacturing. There were more than 180 exhibitors showcasing machines for metal AM production at the show! This year we were particularly impressed by Desktop Metal’s expansion – the company raised $438 million in equity funding for its metal solutions – but also the emergence of new players such as Meltio.
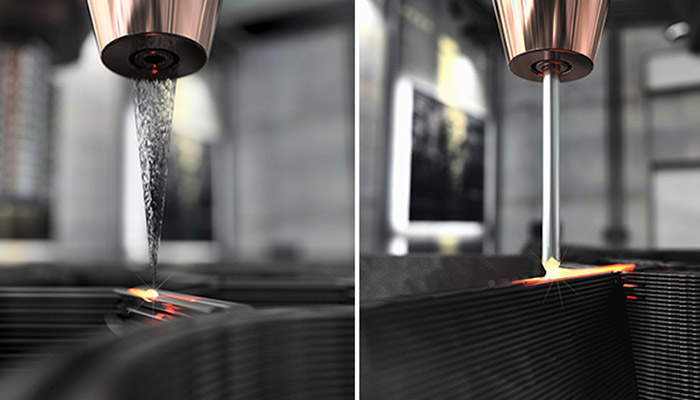
Meltio’s technology enables to 3D print metal wires or metal powders | Credits: Meltio
Composites have also been growing, and even competing with metal on some applications. AREVO, the Silicon Valley company that develops technology to enable direct digital additive manufacturing of ultra-strong, lightweight composite parts created the first ever carbon fiber unibody frame for its bike this year. In general, continuous fiber composite 3D printing is comparable to metal 3D printing in strength, yet it is lighter and more affordable. The benefits of these materials are therefore pretty obvious for some end-use applications, and the number of players for this segment has been building up over the course of 2019. One player gaining attention in this segment is Anisoprint, its latest solution being the ProM IS 500 for industrial composite production. Even Desktop Metal launched a new 3D printer dedicated to these materials this year, named the Fiber.
In other sectors, high-performance polymers such as PEEK, PEKK and ULTEM are being adopted for their unique properties. In the medical sector, its biocompatible property means you can create customisable 3D printed implants for patients. Manufacturers are developing new HPPs such as Roboze and Sabic, which unveiled a new material, EXTEM™AMHH811F that can can withstand continuous operating temperatures of up to 230°C! We also observed more machines being developed to work with these materials, including INTAMSYS’ FUNMAT PRO 610 HT and 3DGence’s INDUSTRY F420 system. Other trends in materials included the growth in silicone 3D printing and ceramics 3D printing. Additionally, Sandvik also unveiled the world’s first ever 3D printed diamond composite!
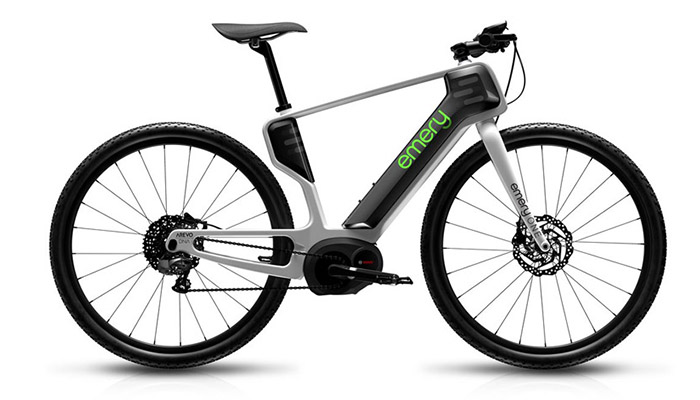
AREVO carbon fiber unibody frame | Credits: AREVO
Sectors reach a new level of maturity
Every year, the 3D printing industry will experience breakthroughs and this year was no exception. In the medical field, a team of researchers from Tel-Aviv University (TAU) successfully 3D printed a heart using human cells. This heart completely matched the immunological, cellular and anatomical properties of a human patient. Even though it consisted of the size of a rabbit’s heart, its complexity was a complete first and demonstrates the huge potential of bioprinting technologies. Another important news this year was the creation of a 3D printed boat at the University of Maine – the world’s largest 3D printed boat to be exact. The piece measured 7.62 meters in length and weighed 2.2 tons! The project teams were awarded 3 World Records: the largest 3D printed solid part, the largest 3D printed boat and finally the largest 3D printer. Another advancement in 2019 worth mentioning is additive manufacturing in space. This sector is still in its early stage of adoption, nevertheless the activity is promising – for example, Relativity Space raised $140 million to become the first company to launch an entirely 3D printed rocket to orbit this year!
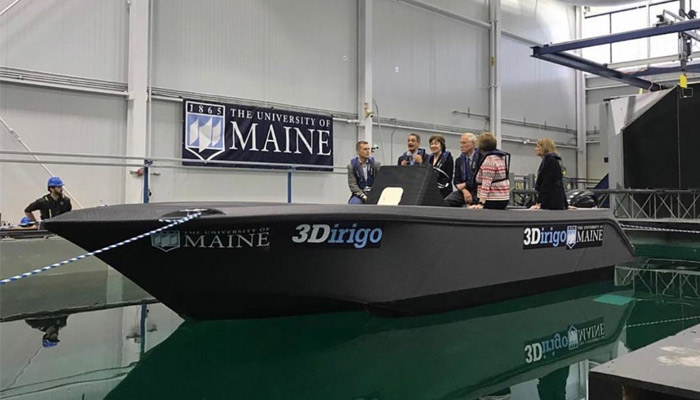
The 3Dirigio 3D printed boat | Credits: UMaine
Sustainability
Sustainability and 3D printing have a special bond. In fact, 3D printing can be considered a greener manufacturing method because it allows for just the material needed to be utilized. By contrast, subtractive production techniques by definition waste resources when producing. Some projects in the sector have highlighted this sustainable aspect by offering multiple solutions for recycling waste: 3devo’s SHR3D IT industrial system, or initiatives such as Zero Waste Future that 3D print furniture for cities are good examples. In the food industry, we came across the Upprinting Food project and Aleph Farm and 3D Bioprinting Solutions’ 3D printed meat in space, two initiatives that also demonstrate what can be done in this department. Last but not least, the 3D construction industry is maturing which means that initiatives such as WASP’s to solve the world’s housing issues by creating clay houses affordably, quickly and sustainably are becoming possible. COBOD on the other hand, delivered its first construction 3D printer to Saudi Arabia this year!
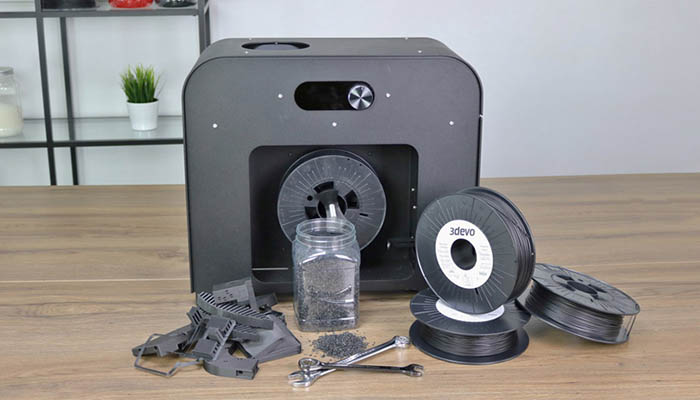
The 3devo recycler and shredder | Credits: 3devo
What did you find most impressive in 2019? Any predictions for 2020? Let us know in a comment below or on our Facebook and Twitter pages! Sign up for our free weekly Newsletter, all the latest news in 3D printing straight to your inbox!