What is Two-Photon Polymerization?
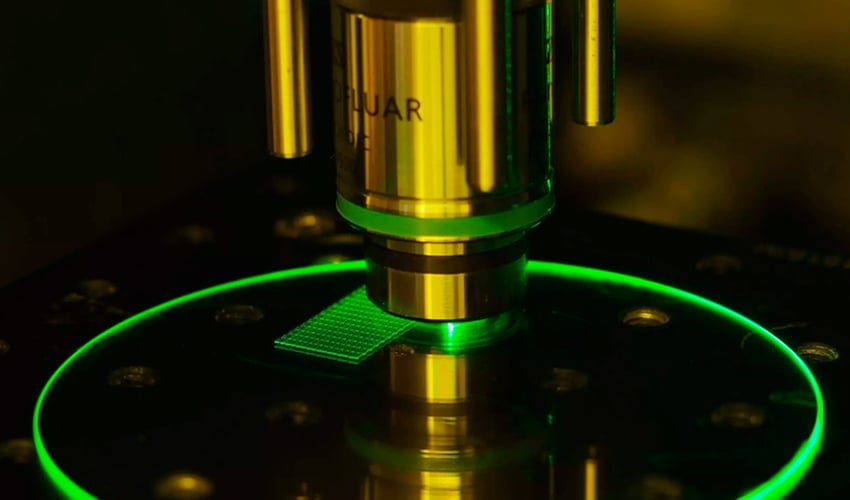
Nano- and microscale 3D printing offers design freedom and efficiency, paving the way for numerous pioneering innovations, particularly in the fields of micro-optics and micromechanics. In turn, these achievements drive new developments, promoting technological progress. As a result, the commercialization of 3D printing techniques that can be used to produce these micro- and nano-objects has increased in recent years. One of the most important processes in this context is two-photon polymerization.
Two-photon polymerization is often abbreviated simply as 2PP. Other terms that can be found concerning this technology are two-photon lithography, direct laser writing, or two-photon polymerization graphene. 2PP falls under the umbrella microscale 3D printing and could be considered an advanced additive manufacturing technology. The basic principles were developed by Shoju Maruo, Osamu Nakamura and Satoshi Kawata at Osaka University in 1997. Since then, numerous companies have continued developing the technology, bringing their equipment to market under various patented names.
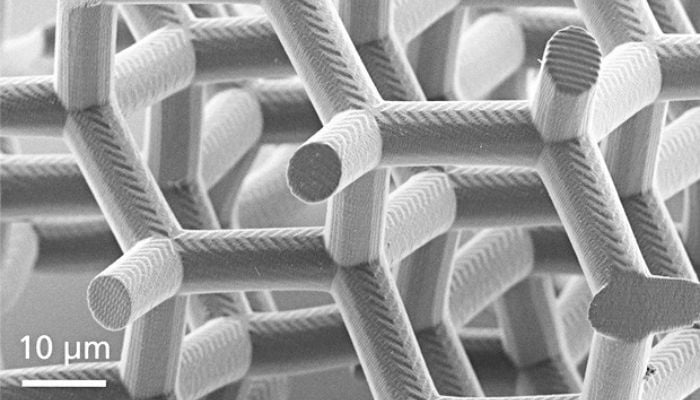
A 3D printed microstructure: two-photon polymerization can be used to produce complex structures at the micro- and nanometer scale (photo credits: Fraunhofer ISC)
How Does Two-Photon Polymerization Work?
Two-photon polymerization, as the name suggests, is based on the principle of photopolymerization. Here, targeted exposure to light triggers the polymerization, or the process to bring monomers together to create a polymer chain, of synthetic resins. This chain reaction causes the molecules to bond and harden, resulting in 3D models. All light-curing processes work in similar ways, but differ in the procedure.
2PP can best be compared to stereolithography, in which a laser beam hardens liquid resin point by point until the object is created layer by layer. The difference between stereolithography and 2PP lies in the interaction with the implemented photons. The term two-photon polymerization is derived from the polymerization process of the material, i.e. its solidification. In stereolithography, this is achieved by an entire beam of light emitted by a laser. In two-photon polymerization, on the other hand, visible radiation in the form of lasers or infrared radiation is used.
Still, generally speaking, the principle of 2PP is very similar to that of stereolithography. Laser light strikes the resin molecules, activating them and triggering a reaction that causes them to harden. However, this activation only occurs when a molecule simultaneously absorbs two photons of the laser beam. Two-photon polymerization is therefore based on this process of excitation of light-sensitive molecules by simultaneous absorption of two photons. To achieve this effect with a high probability, the intensity of the laser beam must be very high. The laser intensity is maximum at the center of the focal spot, so that the absorption of two photons only occurs there.
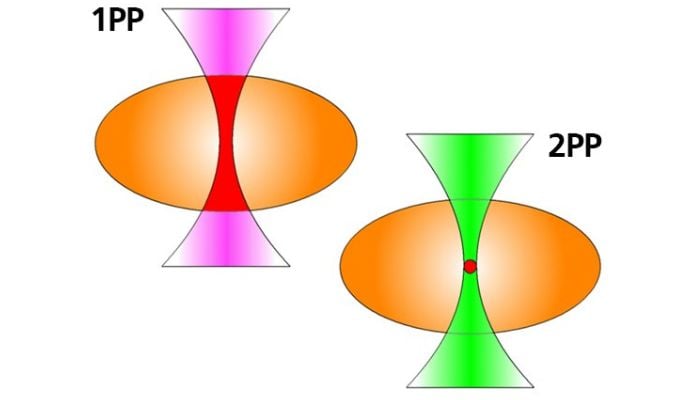
Two-photon polymerization utilizes the effect of two-photon absorption. (Credits: Fraunhofer ISC)
The laser light energy is generated so strongly at the focus of the radiation (the voxel), that local, controlled curing of the light-sensitive polymer can take place there while the rest of the surrounding material remains liquid. However, in 2PP, an ultrashort pulsed laser beam must be used in the range of mere fractions of a second. This is because the process can be carried out with the help of a laser in such a way that the photon density is high enough for the simultaneous absorption of two photons at the focal point of the laser beam. Normally, these wavelengths would not be absorbed by the resin. However, the strong focusing and the nature of the irradiation cause the two-photon absorption effect within the focal volume. As a result, curing is limited to a tiny focal volume, allowing complex 3D microstructures and nanostructures to be created.
Thus, the resin only reacts at the focal point of the laser beam and the laser beam can be directed through several layers, so that only the desired layer, or a specific spot, is cured. Computer-controlled guidance allows 3D structures to be written point-by-point, hence the name laser direct writing. This means that both the strong laser focus and laser intensity are decisive in ensuring the curing of complex structures with nanometer diameters. After exposure, post-treatment with solvents is performed to remove the unexposed liquid resin. The final parts 3D printed with 2PP have extremely high precision and resolutions of less than 25 nm.
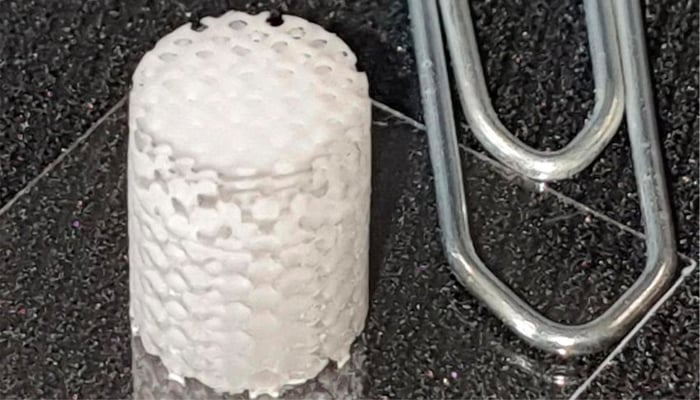
In two-photon polymerization, the laser “writes” a structure and pattern in the liquid resin. (Credits: Heidelberg Instruments)
As a rule, printing with high-precision resolution is associated with a relatively long production time. The precise working method and the punctual curing of the material result in an extremely long production time for macroscopic prints. Therefore, the process is more suitable for small objects of limited mass.
In the micro and nano range, on the other hand, two-photon polymerization has made numerous applications possible. There are no design restrictions, so arbitrary structures can be produced on a small scale. Scalability ranges from 100 nm to centimeters. Furthermore, 2PP is not limited to layer-by-layer fabrication, as mentioned above, but relies on an inherent process in which specific spots are polymerized.
Compatible Materials and Notable Applications
The areas of application for this technology are those where maximum precision is required in the tightest of spaces, such as in micro-optics. Two-photon polymerization can be used to manufacture fiber ends for microscopy and microlenses. In micromechanics, the process is used to manufacture chips. In addition, numerous microelectronic components and microfluidic devices are also manufactured with 2PP.
Another field of application is the medical sector. 2PP can be used to create scaffold structures for cell growth, which initiate tissue formation. It is also used for implants at the cellular or molecular level. For example, drug delivery systems that are inserted into the body can be produced. The production of implants based on the patient’s tissue limits rejection reactions. Micro-imprinting the patient’s own material could also avoid the shortage of donor implants in the near future. Thus, two-photon polymerization is used in numerous sectors and is driving important advances in these fields.
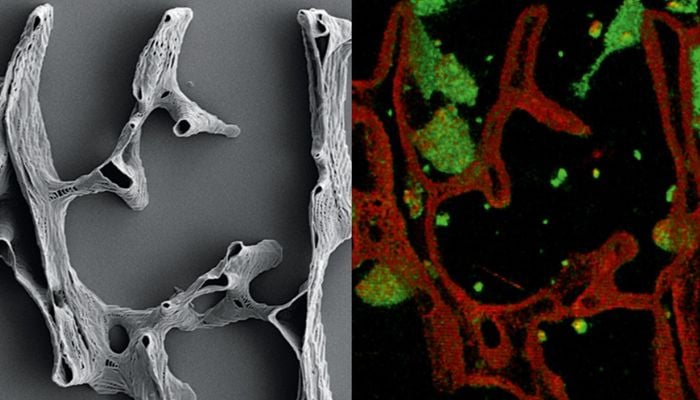
A High-precision reproduction of a trabecular human bone structure from a 3D µ-CT scanner (left). Bone cell culture in “Osteoprint” (right). (Credits: A. Marino, IIT Pontedera)
The materials used depend on the application to be performed. Epoxy resin, photoresists and hydrogels are the most common materials used in two-photon polymerization. More and more organic materials are being used, as well as hybrid materials. For example, hybrid polymers are used to produce ceramic or preceramic structures, which have higher stability.
Two-Photon Polymerization 3D Printer Manufacturers
Among the leading manufacturers of 3D printing systems for two-photon polymerization are Nanoscribe (Germany), UpNano (Austria), Microlight (France), Multiphoton Optics (Germany) and Moji-Nano-Technology (China). Nanoscribe has developed its own process based on two-photon polymerization, known as two-photon grayscale lithography (2GL). The Nanoscribe Quantum X is the world’s first industrial 3D printer to run on 2GL. Another Nanoscribe printer is the Quantum X Shape for rapid prototyping and mass production. For its part, UpNano announced the world’s fastest high-resolution printing system, the NanoOne series. The company has also unveiled the NanoOne Bio System, a printer designed for 3D bioprinting with living cells.
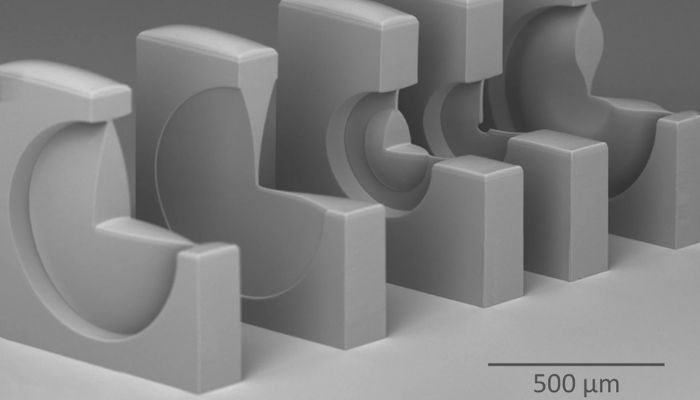
A vertical microlens system manufactured by 2PP. (Credits: Heidelberg Instruments)
Many of these 3D printer manufacturers also offer their own materials. UpNano, for example, has developed a black 2PP material, UpBlack, ideal for optical systems. In addition, the temperature-resistant plastic UpThermo was developed in collaboration with Cubicure. Microlight 3D also offers its own microFAB materials for use with its own printers, such as the MicroFAB-3D. Meanwhile, the Fraunhofer Institute excels in materials development and the advancement of two-photon polymerization. In addition to materials for biological applications, they want to develop two-photon polymerization into an established proprietary process domain technology.
3D printing in the micro and nano range is becoming increasingly important due to the requirements of various industries. Two-photon polymerization is a highly versatile process, which is why it is being used in more and more areas. The technology enables pioneering innovations and breakthroughs in medicine, micro-optics and microelectronics, contributing to many exciting developments in the industry.
What do you think about two-photon polymerization? Let us know in a comment below or on our Linkedin, Facebook, and Twitter pages! Don’t forget to sign up for our free weekly Newsletter here, the latest 3D printing news straight to your inbox! You can also find all our videos on our YouTube channel.
*Cover Photo Credits: Heidelberg Instruments