What Does Resolution Mean in 3D Printing?
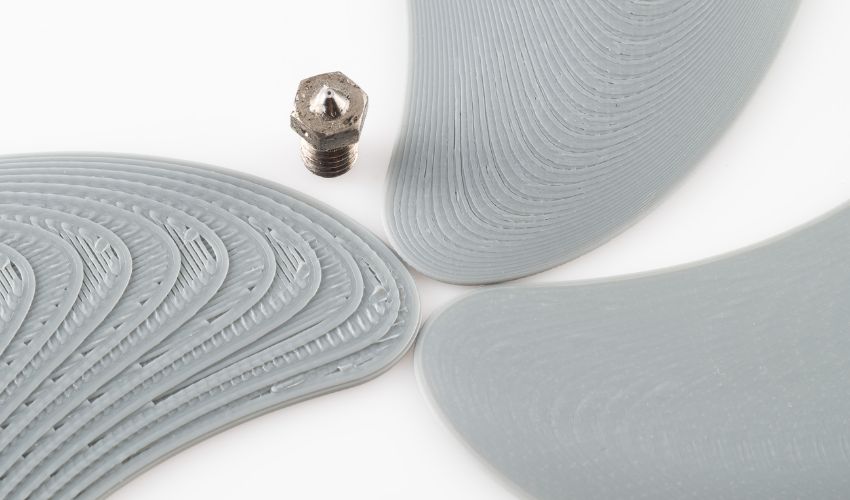
In 3D printing, resolution generally refers to the degree of detail and precision a printer can achieve when creating an object, but more specifically, it refers to the minimum feature size of the X, Y and Z axes. The XY plane is horizontal, and the Z-axis, which is vertical, refers to layer height. So, resolution in 3D printing should correspond to two numbers: the measurements of the XY plane and the Z-axis. We often think of resolution in terms of images on a screen: i.e., the pixel density of a television, and we know that the smaller the pixel, the higher the resolution. For 3D printing, know that a voxel is the 3D equivalent of a pixel.
Resolution is important because it determines the level of detail in the final product, influencing the aesthetics, functionality and surface quality of a print. However, be careful not to confuse resolution with dimensional accuracy and tolerance. Accuracy refers to a printer’s ability to produce parts with the desired measurements, and tolerance refers to the allowable deviation in the dimensions of a printed object compared to its original design specifications.
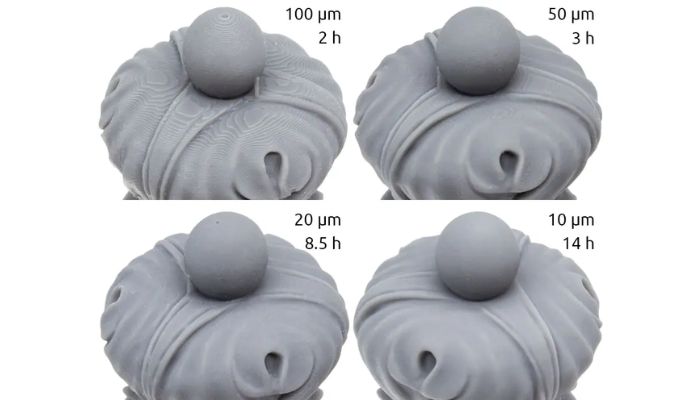
An object printed with SLA with four different layer heights (Image credit: Ameralabs)
If you are searching for a high-resolution 3D printer, you should find one that performs well in the X, Y and Z dimensions. Generally, lower numbers mean smaller, more defined details. Keep in mind that resolution is relative to the type of 3D printing technology being used. In this article, we will discuss it relative to FDM and vat photopolymerization.
Factors that Affect Resolution
In FDM printers, nozzle size and the smallest possible movement a printer can make side-to-side are major factors in determining the resolution. A nozzle with a smaller diameter will be able to deposit lines with a smaller width and height, although significantly slowing down the printing process. Larger nozzles will be less precise, but this is not bad if you are printing something larger that does not require fine detail.
The same principle applies with stereolithography (SLA), a type of vat photopolymerization, but instead of nozzle diameter, you measure the diameter of the laser curing the resin. These laser points can be much smaller than a nozzle, resulting in more precise results compared to FDM.
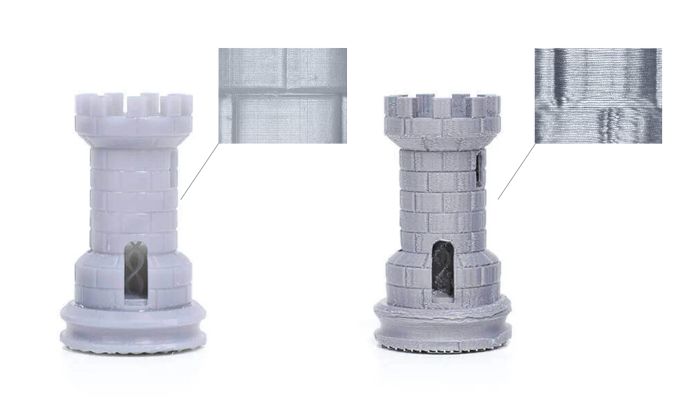
Two chess pieces with 0.1mm layer thickness, the right one printed with FDM and the left with SLA (Image credit: Formlabs)
For masked stereolithography (MSLA), which is also referred to as LCD, the resolution along the XY plane is dependent on the resolution of the LCD screen. For digital light processing (DLP), which cures resin with a projector, the resolution will mainly be determined by the size of the individually controlled microscopic mirrors that control which points of the resin will be cured.
Another determining factor for both FDM and resin processes is layer height, which can be determined by the print settings and the printer’s capabilities. A shorter layer height can result in a smoother surface, and a larger one means more visible layers. Desktop FDM printers can often achieve layer heights of 100 microns (0.1 mm). By contrast, vat photopolymerization solutions like SLA can have details as small as its layer height, around 30 to 50 microns.
Choosing the Right Settings
It might seem counterintuitive, but having a high resolution is not always optimal. A high resolution can significantly increase print time—for example, halving your layer height will double your print time—so it is important to know if it is necessary. A longer print time is less efficient, and it can also increase the potential for errors to occur.
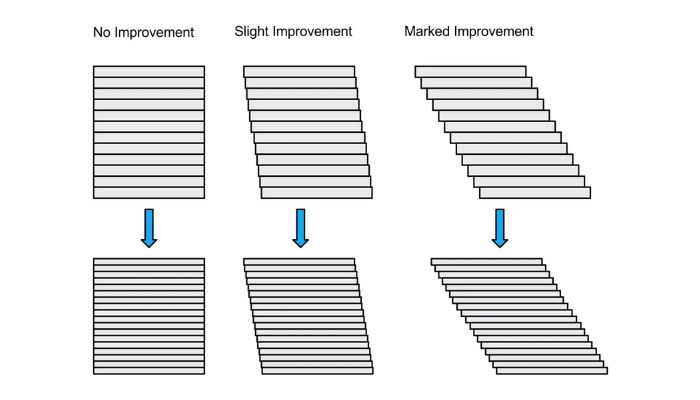
(Image credit: Formlabs)
The graphic above illustrates the effect of layer height on quality. If your model has mostly vertical and horizontal edges and 90-degree angles, like the print on the left, thinner layers may not be helpful. Alternatively, designs with intricate details, curved edges, small embossing and organic forms can greatly benefit from high-resolution settings. Some slicers, especially for FDM printing, will let you use variable layer height to help optimize the print time and resolution. Variable layer height can be set up either manually or automatically.
If you want to improve your prints’ resolutions, play around with the parameters mentioned in this article. In general, smaller layers indeed mean higher resolution—and this applies to all 3D printing technologies—but it is important to find the parameters that work for your specific printing needs. Don’t be afraid to experiment!
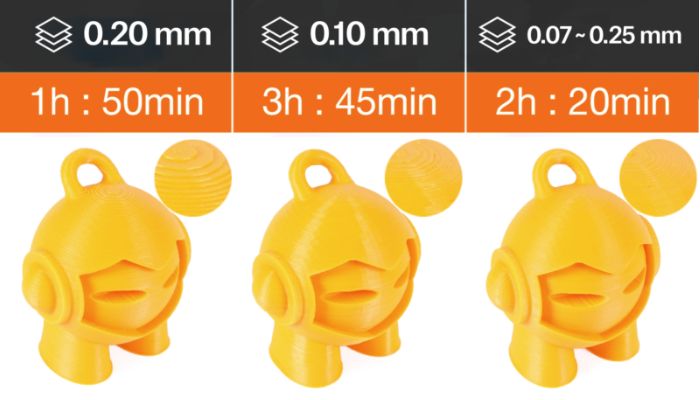
The left uses larger layers and achieves a faster print time, and the center uses smaller layers, resulting in a longer time. The third uses variable layer height, prioritizing smaller layers only where necessary. (Image credit: Prusa)
How would you find the optimal resolution for 3D printing? Let us know in a comment below or on our LinkedIn, Facebook, and Twitter pages! Don’t forget to sign up for our free weekly Newsletter here, the latest 3D printing news straight to your inbox! You can also find all our videos on our YouTube channel.
*Cover Photo Credit: Arthur on Thrinter