What Are the Characteristics of Alumina in 3D Printing?
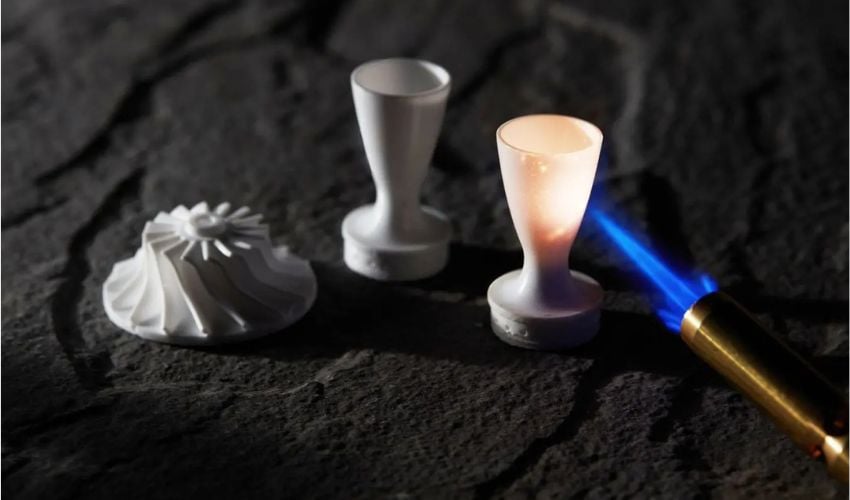
Alumina, also known as aluminum oxide, is a technical ceramic material that occurs naturally in bauxite, a rock that also contains iron oxide. Bauxite is typically purified using Bayer’s process, which extracts a white powder that can then be transformed into aluminum by electrolysis. Alumina is particularly interesting thanks to its chemical, thermal and electrical properties, and is one of the most widely used oxidized ceramics in additive manufacturing. But what are its characteristics, and which processes are compatible with it? Here, we’ll tell you more about alumina in 3D printing.
In 1754, German chemist Andreas Sigismund Marggraf first isolated alumina from alum. A few years later, the Bayer process was used to extract it from the ore known as bauxite. Today, 90% of aluminum oxide is used to produce aluminum, but it is also used as a technical ceramic, offering very interesting characteristics in terms of resistance to temperature and thermal shock. To give you an idea, alumina has a melting point of over 2,000°C. The material offers excellent dimensional stability, wear resistance and electrical insulation. Its hardness is comparable to that of tungsten carbide.
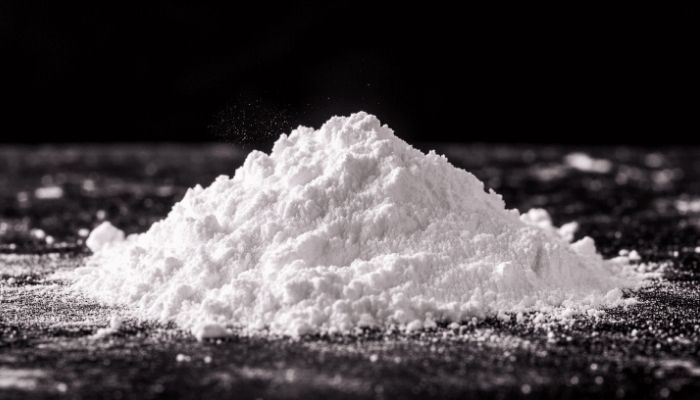
Once extracted, alumina is a white powder (Photo Credits: Itaforte)
Alumina in 3D Printing
Aluminum oxide is a powder that can be used in additive manufacturing in numerous ways. Firstly, the powder can be encapsulated in a plastic filament for use in FDM 3D printing. Once the part is ready, debinding and sintering are required to remove all solvent and plastic and to consolidate the material. It is also possible to use resin additive manufacturing. Post-processing steps will also be necessary to obtain a final part with interesting chemical and mechanical characteristics. Finally, we can mention binder jetting, which can be compatible with ceramics, including alumina. It should be noted, therefore, that alumina printing involves additional post-processing steps, which can lengthen the manufacturing process and add production constraints. However, some market players are seeking to automate this part of the process as far as possible.
Among the players on the market are 3D Ceram and Formlabs, which offer alumina-compatible resin machines; Nanoe, which has developed an aluminum oxide filament; and Concr3de, which offers a range of industrial solutions based on binder jetting technology. These are not all the suppliers on the market, but know that there are different options when it comes to using alumina in additive manufacturing.
Possible Applications
As you can imagine, alumina is of great interest to many industries requiring high temperature resistance or insulating properties, such as the aerospace and energy sectors. The material can be used to create connector housings, insulators, parts installed on electrical assemblies, and more. Thanks to additive manufacturing, we can obtain small quantities at lower cost and customize them as required.
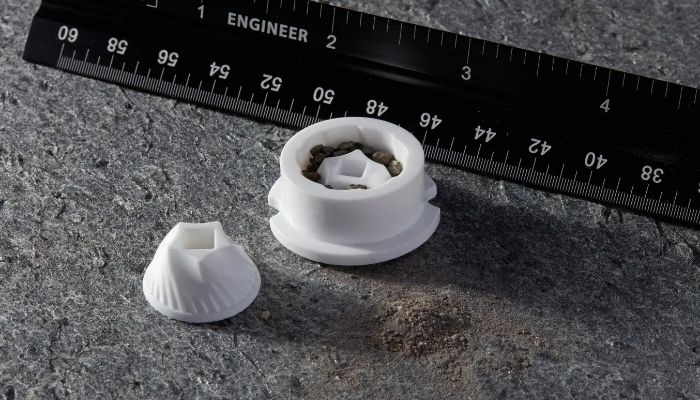
Ceramic grinding disc and milling cutter designed using Formlabs’ Alumina 4N 3D printing resin (Photo Credits: Formlabs).
3D printed alumina also enables the design of complex foundry cores, reducing lead times and the overall cost of the mold. We can, for example, imagine parts with internal channels for improved fluid or air flow, a complexity in terms of design rarely achievable via more traditional manufacturing processes. As you can see, additive manufacturing makes it possible to design tough, durable, complex alumina parts more efficiently.
What do you think of alumina 3D printing? Let us know in a comment below or on our LinkedIn or Facebook pages! Plus, don’t forget to sign up for our free weekly Newsletter to get the latest 3D printing news straight to your inbox. You can also find all our videos on our YouTube channel.
*Cover Photo Credits: Formlabs