Westinghouse Announces Milestone for 3D Printing in the Nuclear Sector
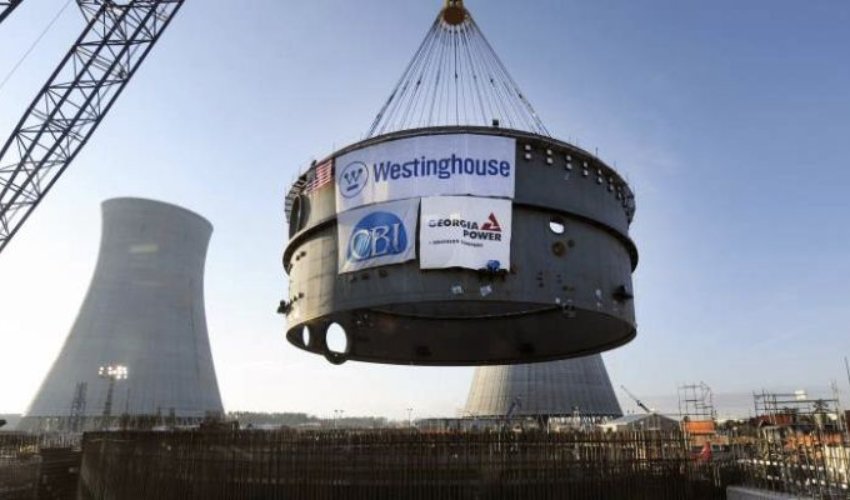
In a significant development for additive manufacturing, Westinghouse Electric Company, a global leader in nuclear energy technology, has produced its 1,000th 3D printed fuel flow plate for VVER-440 fuel assemblies. This achievement marks the first-ever safety-related 3D printed part to enter serial production within the nuclear energy industry, highlighting the expanding potential of 3D printing for critical applications. A significant milestone in the field.
The newly developed 3D printed fuel flow plates, crucial for the operation of VVER-440 reactors, have been seamlessly integrated into the assemblies. This in turn has lead to a significant enhancement in overall performance. By harnessing the capabilities of 3D printing, Westinghouse has showcased its continued commitment to driving innovation and upholding the highest safety standards in nuclear energy production.
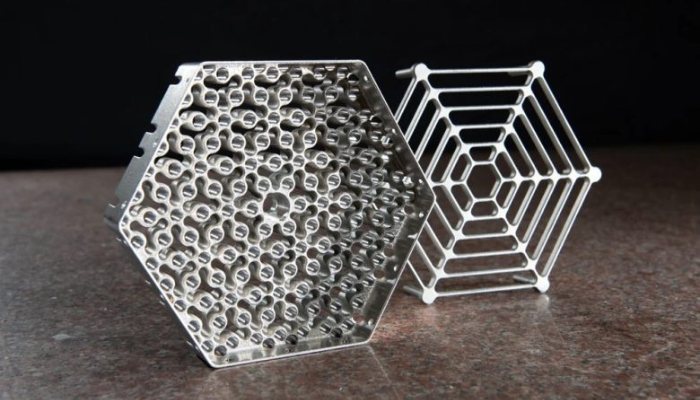
A 3D printed fuel assembly component from Westinghouse.
Lou Martinez Sancho, Westinghouse’s Chief Technology Officer and Executive Vice President, emphasized the importance of this accomplishment, stating, “This achievement showcases the development of additive manufacturing from prototyping to full-scale production, generating tangible value for our customers. This marks another Westinghouse pioneering achievement in AM Technology holding the commitment to strengthening safety, efficiency, sustainability and energy security.”
Since its adoption of 3D printing in 2015, the company has continued to achieve enhanced efficiency and productivity while enabling the development of cutting-edge energy solutions for the nuclear sector. Previous milestones of Westinghouse include the installation of the first-ever safety-related AM component, a Thimble Plugging Device, into a commercial nuclear reactor in 2020.
As global interest in cleaner and more sustainable energy solutions grows, the adoption of 3D printing technologies within the nuclear sector has gained considerable momentum. In this decade alone, we have already witnessed remarkable achievements owed to 3D printing technology, including the fabrication of metal nuclear reactor cores, the production of fuel assembly brackets for the United States’ second most powerful nuclear reactor, and the development of 3D printed microreactors in Indiana. These achievements underscore the viability of deploying certified 3D printed components in rigorously regulated environments such as the nuclear industry.
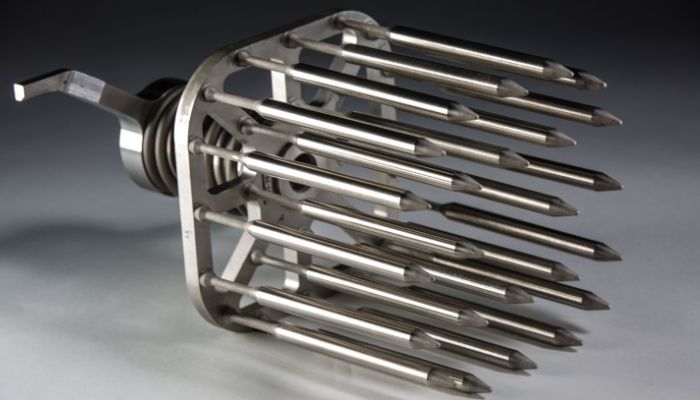
Westinghouse’s Thimble Plugging Device, used to hold nuclear fuel while it is lowered into the reactor core, and stop nuclear debris from escaping.
The company notes that 3D printing offers unmatched benefits, allowing for quick production of complex components that boast improved durability and precision-essential factors for upholding the safety and reliability standards of nuclear power plants. Moreover, it can significantly aid in the creation of materials and tools resistant to radiation, customized for maintenance and repair tasks in radioactive settings. As nuclear powerhouses like Westinghouse increasingly embrace AM technology, we can anticipate witnessing even more substantial advancements and achievements within the nuclear sector in the years ahead. To learn more about this milestone by Westinghouse, click here.
What do you think of Westinghouse’s use of 3D printing to improve overall safety? Let us know in a comment below or on our LinkedIn, Facebook, and Twitter pages! Don’t forget to sign up for our free weekly newsletter here, the latest 3D printing news straight to your inbox! You can also find all our videos on our YouTube channel.
*All Photo Credits: Westinghouse