Weerg and Ursus Worked Together to Make a Custom Handlebar With Additive Manufacturing
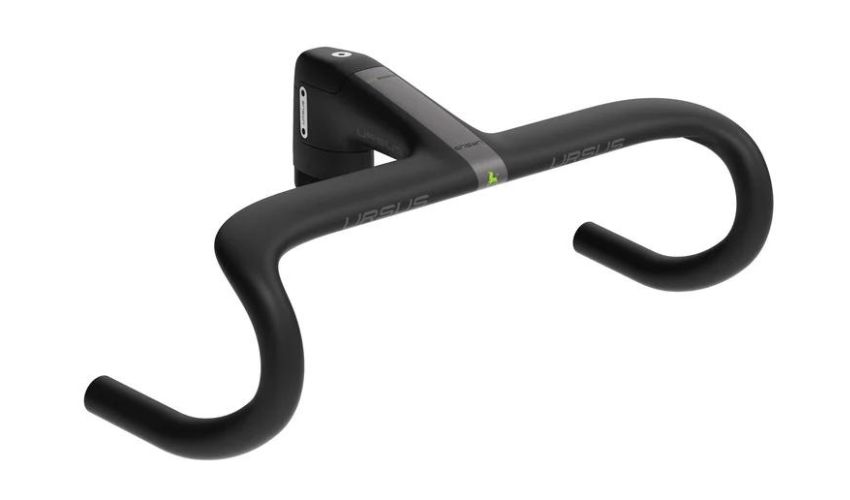
3D printing is becoming increasingly popular in all industries where customization, design and performance meet. The ability to create complex structures as well as to use 3D printing for rapid prototyping and thus to test materials and properties quickly and inexpensively, makes it suitable for sectors such as automotive, aerospace or sports. The cycling industry, for example, benefits from additive manufacturing for the creation of components, prototypes, but also end-use parts that fit customers’ needs or are even custom-made for athletes’ bodies. The case of the company Ursus, which turned to online 3D printing service Weerg to make a custom handlebar, is a good example.
In fact, companies that need to produce small and medium-sized, custom-designed parts in short runs encounter quite a few difficulties when they turn to traditional production methods. Injection molding does not meet such demands because of the long lead times and the large cost of molds. Additive manufacturing, on the other hand, is the ideal solution in such cases. Many companies are therefore turning to 3D printing service providers to optimize time and resources, achieving better results in terms of both performance and optimization of production processes.
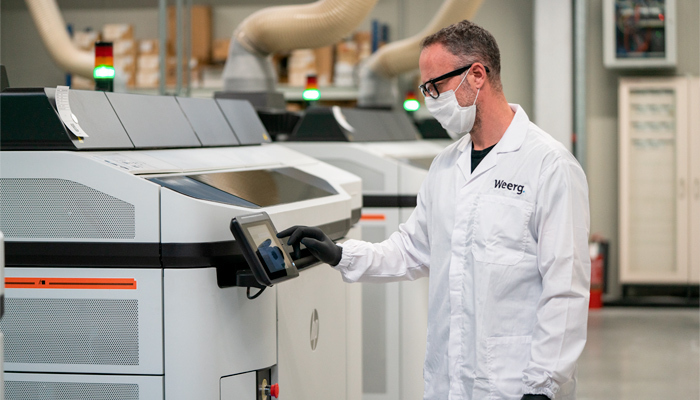
An operator at the headquarters of additive manufacturing service Weerg (photo credits: Weerg)
The Combination of Weerg’s Online Services and HP Multi Jet Fusion
Within this context is an all-Italian success story, born out of the collaboration between the company Ursus, which has been active for more than 50 years in the field of engineering and bicycle components, and the online manufacturing service Weerg. The two companies collaborated in the creation of the Magnus H.02 handlebar with HP’s Multi Jet Fusion technology, provided by Weerg. Based in Scorzè (Venice), Weerg is an online manufacturing service offering both CNC and 3D printing solutions, with 100 percent in-house production. In terms of additive manufacturing, the company offers FDM, SLA and HP Multi Jet Fusion (MJF) technologies, owning the world’s largest fleet of MJF 3D printers. Ursus therefore turned to Weerg in order to first test and then produce the new Magnus H.02 handlebar.
As a renowned company in the cycling world, Ursus is known for its drive for innovation through research and design of its products. Indeed, the Magnus H.02 handlebar was a challenge for Ursus’ designers, as it is a handlebar for racing bicycles that Ursus worked hard on to combine lightness, ergonomics and aerodynamics. During the design of the handlebar, the goal was to make an attachment system that would fit perfectly on different frames.
“Often, when some bicycle manufacturers contact us to put one of our products on their frames, they provide us with different sizes from project to project. Therefore, our goal is to create custom solutions so that we can fit our product perfectly to each frame,” explained Matteo Cortese, product designer at Ursus.
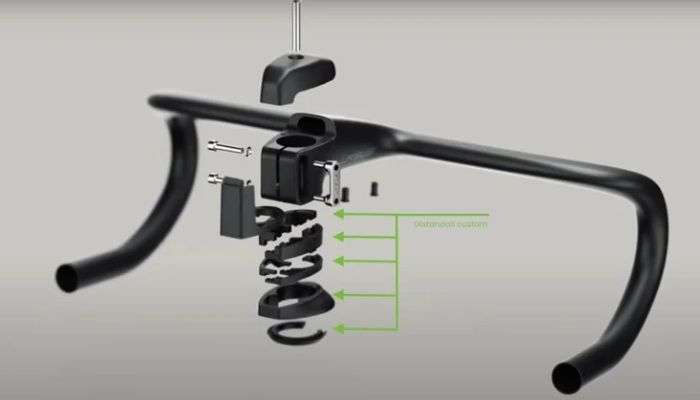
Photo Credits: Ursus/Weerg
Therefore, to adapt the Magnus H.02 handlebar, the solution was to create different spacers that would adjust the height of the attachment on the different frames. Given the low number of adaptation copies and the need for customization, the use of MJF technology provided by Weerg provided the ideal solution. MJF technology is in fact one of the most attractive in terms of time and cost optimization, presenting enormous advantages in terms of flexibility and ability to process a wide variety of complex geometries compared to other additive manufacturing technologies. It also allows the mechanical properties of the material to remain intact, making it suitable for this type of application.
The Manufacturing Process of the Magnus H.02 Handlebar From Ursus
The production process for the Magnus H.02 handlebar began for Ursus designers with turning to Weerg’s online platform to understand the feasibility of the design. Being a fully online service, Weerg makes it easy and intuitive to enter 3D files, specifications on materials, finishes, and delivery time in one interface and receive a free quote in seconds. In terms of materials, Weerg’s platform allows users to choose, for example, for 3D printing from numerous polymers including resin, polypropylene, PEEK, ABS, and nylon. Weerg then developed together with HP the innovative PA 12 White for MJF technology, among others.
Ursus’ design was then submitted and then analyzed internally by a Weerg engineer, who assisted Ursus in the manufacturing of the handlebar. The ability to have a specialized engineer dedicated to your project is undoubtedly an added value because it allows you to combine the efficiency of online service with the expertise and human assistance sometimes needed to bring projects to a successful conclusion.
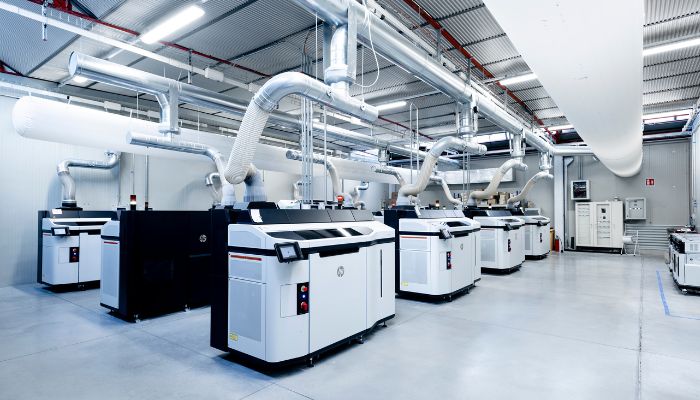
Weerg’s HP MJF machine farm (photo credits: Weerg)
In addition, the advantage of having 100% in-house production allowed Weerg to quickly deliver the first handlebar models for testing by Ursus designers. Matteo Cortese added, “Through MJF technology, Weerg allowed us to make excellent finished parts with good isotropic mechanical properties. On the site, we were able to order and receive in about ten days the few thousand units we needed for the project.”
In the specific case of Ursus, being able to use MJF technology for rapid prototyping of the handlebars was a breakthrough for the designers, who were able to test the mechanical properties of the handlebars quickly and inexpensively, modifying and customizing them from time to time until the final product was obtained. Once the tests were finished, they were then able to request the necessary units of the finished product. According to the company, the use of the HP MJF technology provided by Weerg saved up to 20 times the available budget and development time, confirming Additive Manufacturing as the ideal production method for performance and custom parts. Learn more about Weerg and HP MJF technology HERE.
What do you think about the use of MJF technology in Weerg’s collaboration with Ursus? Let us know in a comment below or on our LinkedIn, Facebook, and Twitter pages! Don’t forget to sign up for our free weekly Newsletter here, the latest 3D printing news straight to your inbox! You can also find all our videos on our YouTube channel.
*Cover Photo Credits: Ursus/Weerg