Unleashing Efficiency to Reduce Thermoforming Mold Production Time & Costs With 3D Printing
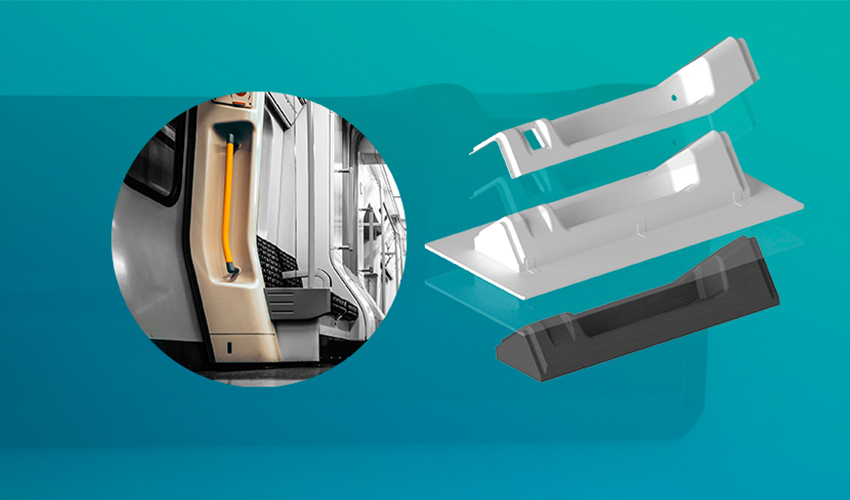
Thermoforming companies and manufacturers that utilize thermoformed components are currently under immense competitive pressure to improve production efficiency, minimize waste, and lower expenses. Simultaneously, they are grappling with a scarcity of skilled labor. Fortunately, additive manufacturing (AM) presents a compelling solution. With AM, companies can access high-performance molds that not only form top-notch parts but also significantly cut down on lead times and labor expenses when compared to conventional mold-making approaches. In this webinar, titled “Revolutionizing Thermoforming: Unleashing Efficiency to Drastically Reduce Mold Production Time & Costs“, you will learn how to achieve rapid validation by testing shapes and delivering first parts up to 65% faster with 3D printed molds.
Experts from 3D Systems will show how the company’s thermoforming customers claim to have run thousands of shots of 3D printed molds with virtually no signs of wear or performance degradation. Register now and discover how other companies used our pellet extrusion technology to decrease cost and shorten lead times for large thermoforming molds!
Subtractive versus additive manufacturing molds
Additive manufacturing offers numerous advantages over subtractive manufacturing, particularly in terms of design flexibility, production speed, and cost efficiency. It allows for the optimization of geometric features tailored to specific application needs without the compromises required by traditional processes. Turnaround times are significantly faster, as 3D printing can produce molds within hours or days compared to the weeks or months needed for traditional mold-making. This method also minimizes waste and reduces raw material costs by producing near net shapes, enabling manufacturers to machine printed parts rather than large blocks of material.
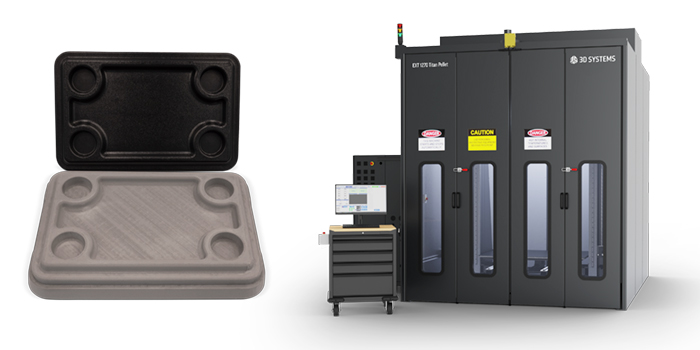
Register here to watch the webinar now.
Additionally, the costs of materials and parts are much lower compared to traditional ceramic, metal, and wood molds. Polymers, in particular, offer a longer shelf life and better resistance to environmental factors like moisture and temperature than wood. Additive manufacturing also allows for the creation of porous molds that optimize molten plastic flow by eliminating the need for drilled vacuum channels. Furthermore, maintaining a digital inventory of molds eliminates the need for physical storage, as users can recycle printed molds and retain their digital files, making mold replacement quick and easy through reprinting.
In conventional thermoforming, plastic sheet material is shaped over patterned molds to create the finished part, often using vacuum forming to help pull the plastic sheet over the mold. These molds can be produced through various methods, such as CNC machining of metals and ceramics or even hand-sculpting wood. These subtractive processes typically involve CNC milling and tooling, where material is selectively removed from a block using a spindle to achieve the desired shape. In contrast, additive manufacturing begins with nothing and builds a part, layer by layer on a build platform, using only the necessary material. This approach allows for the creation of parts from a wide range of polymers, including standard and high-performance thermoplastics, thermoset, filled and photopolymer resins, and even metals. Additive manufacturing systems come in various sizes, from small desktop units to large-format industrial machines, offering versatility in production capabilities.
Agenda of the webinar
- Introduction
- The Customer Challenge: Cost, Lead Time & Inventory
- The Additive Solution: Industrial, Large-Format Platforms; Pellet Extrusion vs Filament Extrusion; Tips & Best Practices for Printing Molds
- Assorted Customer Use Cases
- Conclusion and Q&A
Speaker
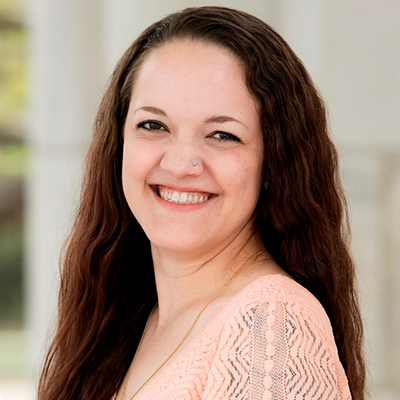
Haley Stump
Haley Stump is the Application Engineer Lead for the Titan division of 3D Systems. She is at the forefront of many exciting projects involving the advanced EXT Titan Pellet 3D printing system. In her previous role, she worked with Titan as a customer, developing time and cost saving manufacturing methods for a global retail merchandising company and joined the 3D Systems team in Colorado Springs in 2022. She works closely with our sales team to provide tailored solutions for various applications such as patterns, tooling, prototyping, and end-use products.
What did you think of the webinar on-demand about thermoforming and 3D printing? Let us know in a comment below or on our LinkedIn, Facebook, and Twitter pages! Don’t forget to sign up for our free weekly newsletter here for the latest 3D printing news straight to your inbox! You can also find all our videos on our YouTube channel.
*All photo credits: 3D Systems