Knust-Godwin uses VELO3D’s metal AM system to create meter-tall parts
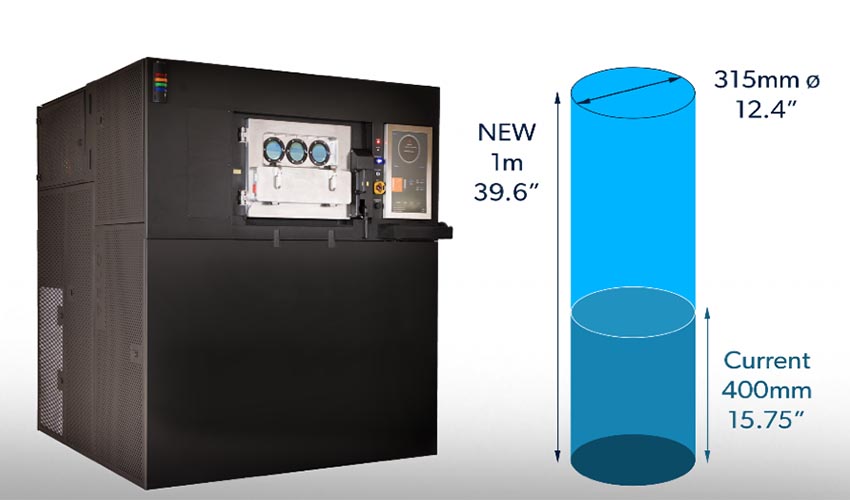
It’s been a busy first half of the year for VELO3D: the company launched a new metal 3D printer, and raised $28 million in a Series D funding round. A few days ago, the company also revealed it had raised an additional $12 million from new strategic investors, bringing total funding to $150M. During the launch, the company revealed that their next-generation metal AM system was developed with a focus on build-chamber size. According to the manufacturer, the 3D printer’s 1-meter vertical axis makes it the world’s tallest metal powder bed fusion system with a closed chamber. VELO3D also announced its first customer will be Knust-Godwin, an established precision-machining shop that is looking to expand into new industries and has recognized the tremendous potential of industrial metal 3D printing. The company should start shipping its new system in Q4 of 2020.
VELO3D’s Sapphire system relies on its proprietary technology to build metal parts without support structures. Support structures add considerable design and manufacturing constraints and are common in many metal AM technologies, including the most widely used technology, Laser Powder Bed Fusion. The ability to create metal parts without these constraints is one of the main benefits of VELO3D’s system. Mike Corliss, Vice President of Technology at Knust-Godwin, and Zach Murphree, Vice President, Technical Partnerships at VELO3D, are working together to bring the Sapphire system into Knust-Godwin’s fold of high-end manufacturing processes in order to leverage the benefits of 3D printing.
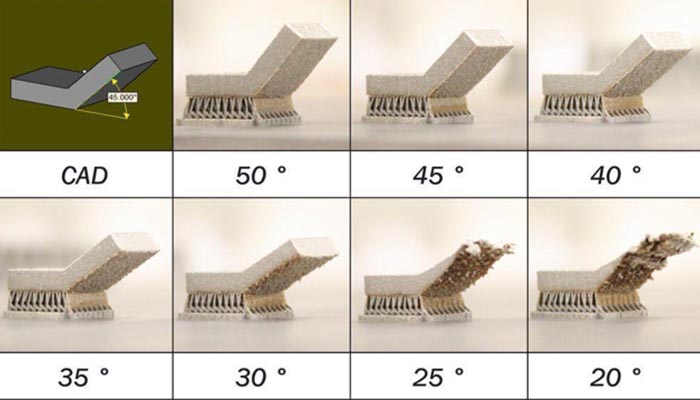
Support structures have always been a requirement to prevent warpage. VELO3D’s support-less process enables you to print low angles without part failure | Credits: Protolabs
What are the advantages of investing in metal AM?
Even though subtractive manufacturing will most likely always play an important role in production, AM has a key role to play too. Over the past 8 years, Knust-Godwin has been investing in metal AM, even though it still relies primarily on subtractive methods to manufacture its products. The precision-machining shop realized early on that it could apply additive manufacturing to many of the parts it produces. Mike Corliss explains: “We’re sure it will help reduce machine time, queue time, and even help reduce constraints with geometry—including the weight of the part and the size of the part—in some areas.”
This is because metal additive manufacturing offers huge potential for complex products, making components smaller, lighter, more durable, more functional, more reliable, and less expensive. In the case of Knust-Godwin, the company is known for precision machining in the high-end of Aerospace and Oil & Gas industry applications. Mike Corliss adds: “With machining, we approach such parts in a very linear manner. With AM, though, we can change that internal geometry, take advantage of it, condense the part, and then create it with a single manufacturing process. The overall length of the part may change for the better. The part may become shorter because you can take advantage of some of the geometry and of some of the internal features. And you may be able to arrange more features around the part in different orientations.”
Additionally, being able to work with materials like Inconel, titanium, nickel super alloys are a huge benefit for industrial applications. These materials offer corrosion resistance and the ability to function in high-temperatures. Zach Murphree explains: “If you’re looking at compression technologies, industrial gas compression, or valving for wellhead applications, these are all places where you want to use high-strength, corrosion-resistant alloys. Inconel is a really good choice in that regard.”
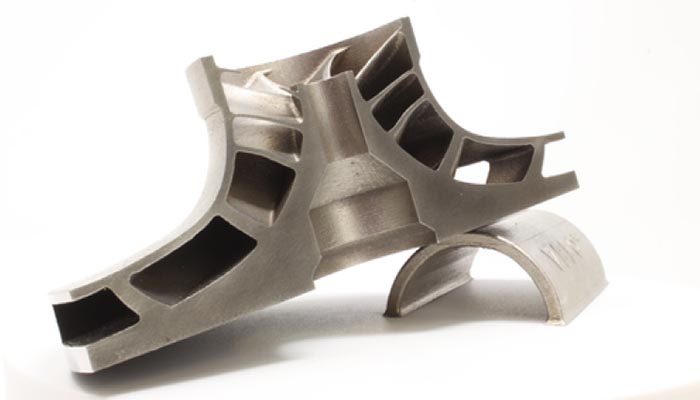
Impeller showcasing ultra-low angles of 0 degrees, which is very difficult to achieve with LPBF systems | Credits: VELO3D
What are the benefits of VELO3D’s technology?
As you may know, the key differentiator for VELO3D is its support-free capabilities and its impact on post-processing. Existing powder-bed systems often require supports for any surface below 45 degrees. On the other hand, the Sapphire 3D printer is able to print low angles and overhangs down to zero degrees horizontally, as well as large diameters and inner passageways up to 100 mm without the need for supports. As a result, post-processing steps are greatly reduced, and more freedom is allowed when designing and building complex components for a variety of industries.
For example, “With support-free printing, the flow of fluids and gasses through a component is optimized. Whether you have a shrouded impeller or a diffuser section, or a hydraulic wireline tool, the support-free structure of those fluid passage areas provides a tremendous advantage,” explains Zach Murphree. At Knust-Godwin, Mike Corliss explains that post-processing is always time-consuming and expensive. “I would rather take the laser powder-bed technology, print the product to the near net shape, reduce as much post-processing as possible, and then do the hipping and heat-treating. Additionally, with far fewer supports to deal with thanks to VELO3D’s technology, the process is streamlined. We can build a better product faster and at a lower final cost.”
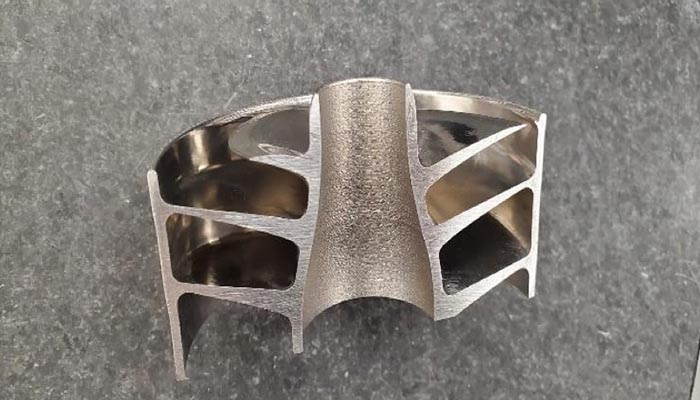
Cross-section of a mission-critical, 3D printed, CO2 pump inducer. These are typically produced through subtractive manufacturing. Printing them without support structures will be a tremendous enabler and cost saver moving forward | Credits: Barber-Nichols
Why increase the height but not the overall build volume of Sapphire?
VELO3D’s next-generation Sapphire system has an increased z-height. Why? Zach Murphree, Vice President, Technical Partnerships at VELO3D explains: “There are several different applications where having a taller system would be beneficial—even if the width or diameter were not changed. There are some obvious applications in aerospace and other industries where taller, tubular-shaped components would be clearly beneficial. You can do some really amazing things around light-weighting, stiffening, and part-reduction when you increase the height.” This is especially true for assemblies that are made from various components.
Finally, another reason for increasing the z-height without changing the diameter of the build volume is that identical process recipes can be maintained across the two machine configurations. Usually, when systems change size or number of lasers, the customer must requalify the new system and new process recipes.
Zach Murphree concludes: “We can’t be happier that a company like Knust-Godwin has become an early adopter of our technology. We look forward to doing great things with them this fall, and then expanding into new markets and new industries very quickly after that.” You can find out more about VELO3D’s next-generation system on their official website.
What do you think of the next-generation Sapphire system? Let us know in a comment below or on our Facebook and Twitter pages! Sign up for our free weekly Newsletter, all the latest news in 3D printing straight to your inbox!