VaporFuse Surfacing, a green solution for improved part properties
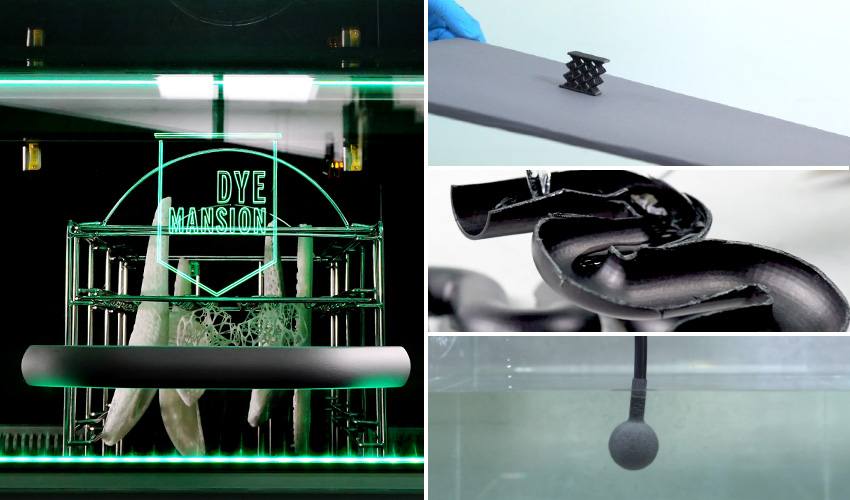
When it comes to the additive manufacturing workflow, we often discuss different printing technologies and modeling software, but it seems like post-processing is not being talked about enough. Yet the subsequent treatment of prints is a crucial step as it gives each piece its final state and color – it is basically the step that “seals the deal”. There exist a few companies that try to innovate in this area, but one particular initiative that caught our attention recently is the vapor polishing solution called VaporFuse Surfacing (VFS), developed by the AM company DyeMansion. Together with its Powerfuse S hardware, the solution is committed to offering post-processing that goes beyond aesthetics, in a green and industrial way.
The fast-growing company from Munich was chosen by the European Innovation Council (EIC) in the first-ever “Green Deal” call. The EIC distributes over EUR 307 million to 64 game-changing “Green Deal” startups out of 2,000 applications contributing to the objectives of the European Green Deal Strategy and the Recovery Plan for Europe.
DyeMansion is a leading company in 3D printing finishing systems for plastics, that started in 2015 by launching the world’s first coloring solution, the DM60. Today, the company offers a post-processing workflow, also known as Print-to-Product workflow, which includes the cleaning of parts, two different surfacing options, and coloring for almost any 3D polymeric technology and material.
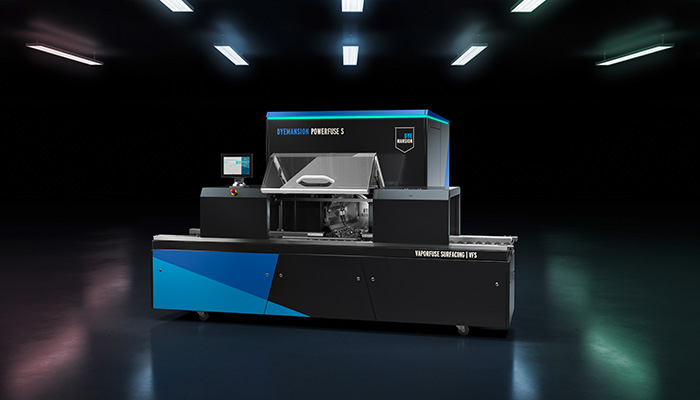
The Powerfuse S Solution with VaporFuse Surfacing Technology | Credits: DyeMansion
Improved part properties with VaporFuse Surfacing
VaporFuse Surfacing is a green industrial technology that delivers sealed and smooth surfaces with improved airtightness, bacteria protection and part strength. During the process, the surface roughness is reduced to a minimum. The technology is suitable for finishing parts made with laser sintering (SLS), HP Multi Jet Fusion or other technologies such as FDM. It is compatible with a wide range of materials, from tough PA12 to TPU and other soft materials. A recently published test series shows the remarkable results that VaporFuse helps achieve:
- Sealed surfaces: roughness is reduced by up to over 80%, both inside and outside. It results in a better flow of water and air in each piece.
- Productive spray painting: VaporFuse replaces the priming step and reduces time and material required down to a third.
- Improved airtightness: Parts with a very thin layer thickness become airtight due to VaporFuse, allowing more design freedom and the use of less manufacturing material.
- Reduced friction: Using VaporFuse Surfacing technology can create smooth parts with over 40% less friction, less abrasion and no chafing effect.
- Improved stability: Printed parts with greater flexibility & reduced embrittlement.
- Bacteria inhibition: VFS protects surfaces from bacterial growth, making them easier to clean and disinfect. That leads to washable surfaces, resistant to chemical and oily products, avoiding residues after cleaning the parts.
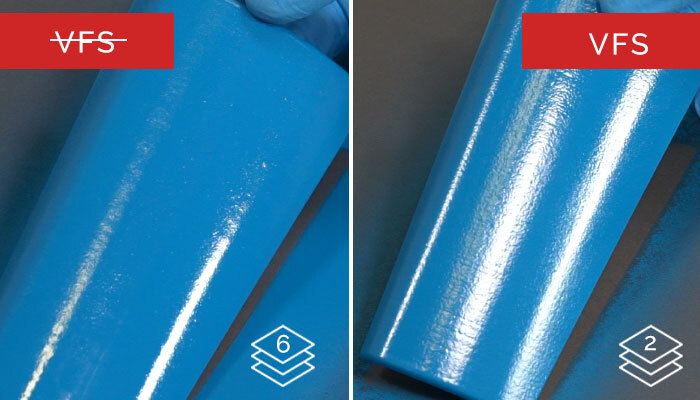
By using VFS technology, time and material are reduced to only a third when applying spray paint | Credits: DyeMansion
The example above shows the improvements VaporFuse Surfacing delivers for a more efficient spray painting. Tests showed that an untreated part required six layers of paint to achieve sufficient gloss and opacity. On the same part previously treated with VaporFuse, only two layers were needed to achieve the same effect. Also, for certain applications, the priming step can be replaced when using VaporFuse Surfacing.
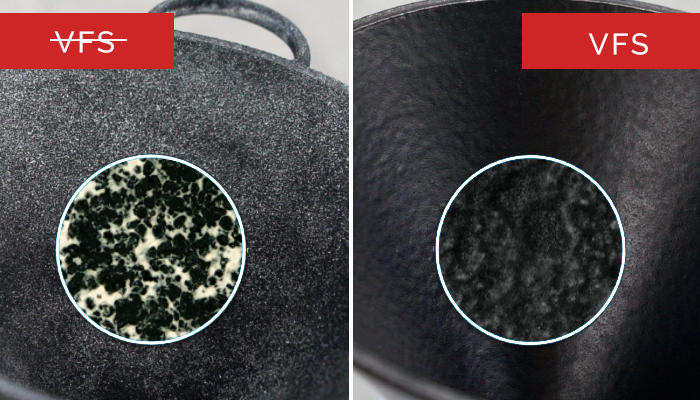
No residue (in this case oil & oil remover) is visible on the surface of the VaporFuse treated part. | Credits: DyeMansion
The second example shows the positive effect VaporFuse has on the cleanliness of components. In both cases oil was applied first, followed by oil remover. After a short waiting period, the oil was first removed with a cloth and the component was then washed off. The picture above shows the residue under the microscope. Only the component treated with VaporFuse could be completely cleaned.
VaporFuse Surfacing : Fields of application
The above-mentioned property improvements have a particularly important impact on the following sector applications:
- Industrial applications: Air & liquid pipes, tool inserts & covers
- Automotive applications: Visible interior parts, Air & liquid pipes
- Consumer applications: Eyewear, (sport) helmets, Bicycle seats, toys for children
- Medical applications: Orthotics & prosthesis, protective masks, laboratory equipment, centrifuges
- Food & Beverage applications: Pick & place applications, robotics, covers & pipes
- Aerospace application: Visible interior parts, seat inserts & covers
It is particularly the sealed surfaces – which are easier to clean, have less frictional effects and increased stability of the parts – that open up completely new applications.
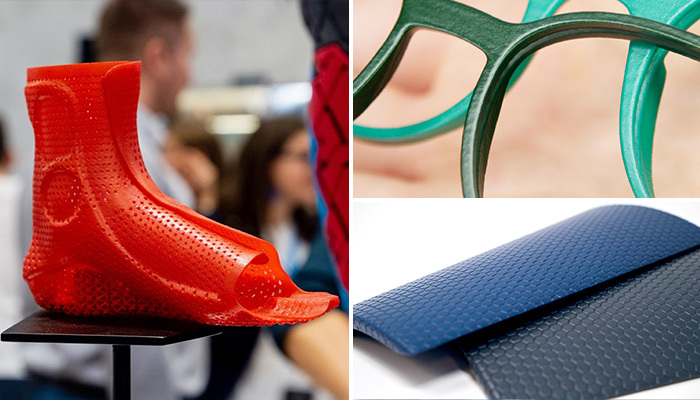
Multiple sectors can benefit from the adoption of the VFS technology | Credits: DyeMansion
A green & industrial solution
Until now, chemical smoothing was mostly linked to aggressive chemicals that can generate toxic waste, having a bad impact on the ecological footprint, but also might be potentially damaging for operators, as they were CMR solvents (carcinogens, mutagens, and reprotoxic). Therefore, the invention of a sustainable post-processing solution was necessary.
In 2019, DyeMansion launched the Powerfuse S, the vapor polishing system that fulfills all industrial health and safety standards. What the Munich-based company had in mind when developing the Powerfuse S, was the principle of economic sustainability, which enables long-term economic growth without negatively impacting social, environmental, and cultural aspects of the community.
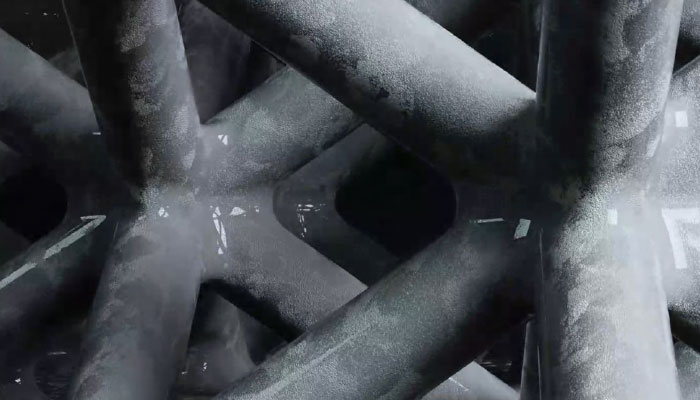
Finishing with VFS technology is done with an eco-friendly solvent | Credits: DyeMansion
With the “VaporFuse Eco Fluid”, a safe solvent for the industry, DyeMansion follows this principle. The solvent is a non-CMR solvent, eco-friendly and approved for the processing of plastics with food contact (Regulation EU 10/2011). In addition, the system does not produce waste, due to a completely closed circuit with the integrated recovery of the solvent. The system can operate autonomously 24 hours a day, 7 days a week and is applicable for Industry 4.0.
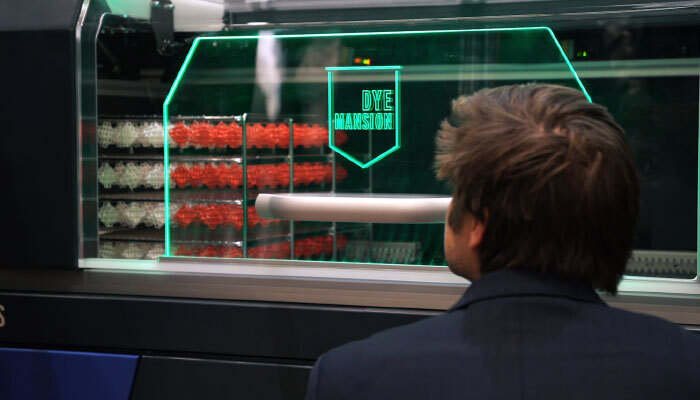
The solution does not produce waste, due to the closed-circuit chamber | Credits: DyeMansion
Meet the PowerFuse S
You are interested in Powerfuse & VaporFuse Surfacing? You can find out everything about the system at the Formnext Connect 2020 from November 10th to 12th. Tickets & further information can be obtained HERE.
You can also find more information about VaporFuse Surfacing and Powerfuse S HERE or in the following video. If you want to try it on your own parts, you can start with a free benchmark.
What do you think about VaporFuse Surfacing and its post-processing beyond aesthetics? Let us know in a comment down below or on our Facebook and Twitter pages! Don’t forget to sign up for our free weekly Newsletter, with all the latest news in 3D printing delivered straight to your inbox!
mostly interrested in double extrusion systems