Vapor Smoothing vs. Vibratory Finishing: Which Surface Finishing Process Should you Choose?
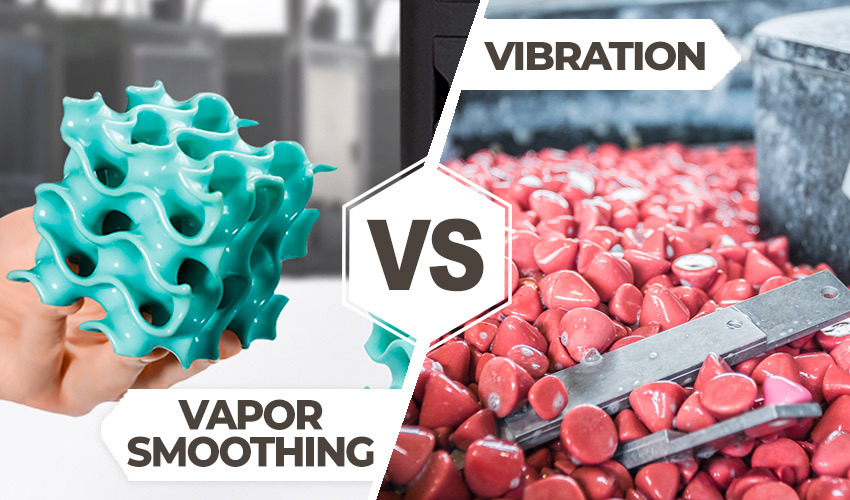
In order to achieve a polished and refined surface on 3D printed parts, engineers use a broad range of industrial finishing techniques including coating, sandblasting and hand finishing methods. Although 3D printing allows for the production of intricate and complex parts, the initial prints that come straight from additive manufacturing often exhibit rough surfaces and noticeable layer lines, particularly in parts produced using Fused Deposition Modeling (FDM). One of the final stages, post-processing, is undergone to take the rugged and unfinished surface and alter the part’s material surface by adding or removing layers of the part. In this article we will introduce you to two well-known surface finishing processes: Vapor Smoothing and Vibratory Finishing. You will learn all about the process of the methods, the advantages and disadvantages, and which method is best suited for your individual purpose.
Process
Vapor Smoothing
Vapor Smoothing, also known as Chemical Vapor Smoothing, is a technique that involves exposing the printed parts to vaporized solvent. The industrial Vapor Smoothing process requires carefully suspending single or multiple parts in a closed chamber for maximum exposure. A chemical solvent blend, such as FA 326, is injected and sprayed into the chamber, where it condenses and hardens on the part, removing surface irregularities through a controlled melt. As the chamber temperature increases, the residual solvent evaporates and is recovered. The final part becomes watertight and retains its smooth internal cavities, accurate dimensions, and original material volume. For optimal results in Vapor Smoothing, it is recommended to conduct the process in a controlled environment using industrial-grade equipment specifically designed for 3D printing Vapor Smoothing. For those interested in a DIY approach, Vapor Smoothing, or in this case called Solvent Dipping, can be achieved using acetone or ethanol as chemical solvents. However, it is essential to exercise caution and ensure proper safety measures and equipment are in place.
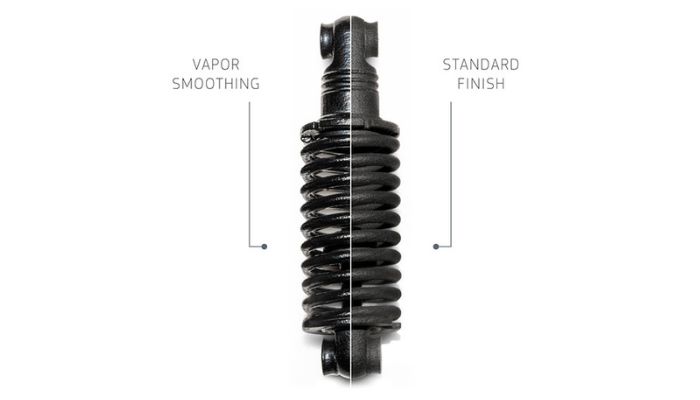
Vapor smoothed part on the left, versus standard finish on the right (Photo credits: ProtoLabs)
Vibratory Finishing
Vibratory Finishing, on the other hand, does not use chemicals for surface treatment. Instead, it relies on an abrasive medium to enhance the surface of 3D printed parts. In this process, several 3D printed parts are placed in a vibratory tub filled with a selected abrasive medium and a lubricating fluid known as the compound. When the machine is turned on, the tub begins to move, creating mechanical friction between the part and the abrasive medium. This subtractive process results in minimal and gentle removal of the outermost layer of material, improving the surface quality of the part. Vibratory Finishing requires special measures and equipment and offers two methods: the Vibration Method and the Tumbling Method. The Vibration Method is particularly suitable for larger, less detailed objects and achieves the desired result much faster. However, with the Tumbling Method, the movements are much slower and gentler, making it suitable for detailed and delicate parts.
The choice of abrasives, or chips, is crucial in Vibratory Finishing. Abrasive chips can be made of ceramic, plastic, or steel, each producing a different result. Ceramic abrasives are particularly suitable for deburring and achieving a shiny surface. Due to their high density, they can withstand high pressure, making them suitable for machining parts made of stainless steel, metal, and plastic. Plastic abrasives are ideal for soft and fine surfaces that require gentle machining. They are available in pyramid and cone shapes. Additionally, Walther Trowal has developed nipple-shaped abrasives, suitable for extra-small, detailed parts with hard-to-reach areas. Steel abrasives, mostly available in a spherical shape, cause minimal material removal and are especially suitable for polishing and mechanical cleaning of parts made of metal, silver, or aluminum, ensuring a smooth surface without scratches.
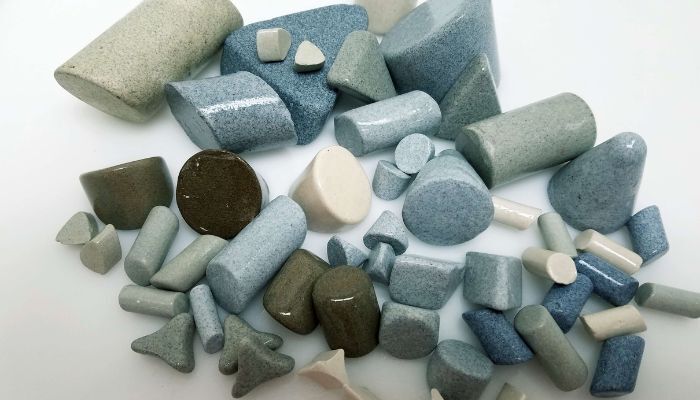
Abrasives made of ceramics can resist high levels of pressure. (Credits: Vibrafinish)
In addition to the abrasives, the Vibratory Finishing process also requires a lubricating fluid, the compound. The compound is used to absorb and remove the abrasion from the parts and to clean and degrease them. An acidic compound can be chosen for machining metal parts, allowing for pickling. After the treatment, drying processes are necessary. The parts can be dried in a vibrating dryer, where they are placed along with heated drying media, such as corncob meal, nut meal, or wood cubes, and set in vibration. Alternatively, a belt dryer is particularly suitable for sensitive and bulky parts with internal channels and holes. In the belt dryer, the 3D printed parts are passed through a hot air system on a belt and dried in this way.
Both Vapor Smoothing and Vibratory Finishing can take varying amounts of time to complete, ranging from ten minutes to several hours, depending on the quantity and complexity of the parts being processed.
Compatible Materials
Vapor Smoothing is compatible with most 3D printed polymers and elastomers. Common materials suitable for Vapor Smoothing include Acrylonitrile Styrene Acrylate (ASA), Acrylonitrile Butadiene Styrene (ABS), High-Impact Polystyrene (depending on the machine), Nylon 11 (PA 11), Nylon 12 (PA 12), Polypropylene (PP), and Polycarbonate/Acrylonitrile Butadiene Styrene (PC-ABS). However, it is important to note that TPU and certain specialty filaments are not recommended for Vapor Smoothing. Each solvent, such as acetone, methyl ethyl ketone (MEK), tetrahydrofuran (THF), dichloromethane (DCM), and ethyl acetate, has its own effectiveness and application considerations.
However, Vibratory Finishing is compatible with many other different materials. For instance, Vibratory Finishing can be used not only for 3D printed parts made of thermosets, thermoplastics and elastomers, such as Polyethylene (PE), Polypropylen (PP) or Polyethylene terephthalate (PET), but also for metals such as aluminum, stainless steel, brass or copper. This makes it a more versatile method that can be used as a post-processing method of various 3D printing technologies, such as FDM/FFF and Powder Bed Fusion technologies.
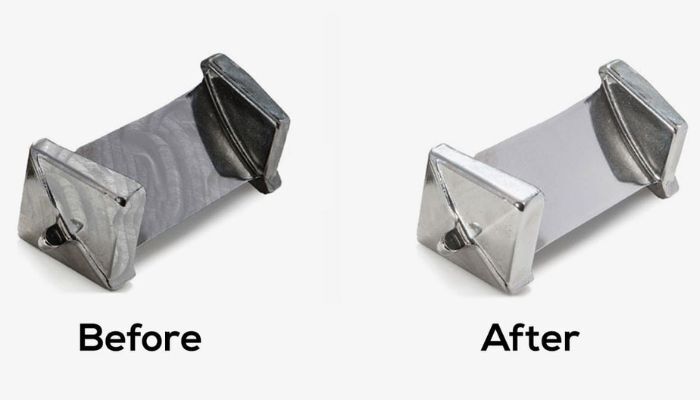
Before and after of a metal part treated with Vibratory Finishing (Credits: Acton Finishing)
Limitations and Advantages of the Techniques
Both processes offer numerous advantages in the result of the surface appearance and properties. With Vapor Smoothing you can achieve smooth and watertight surface finishes comparable to injection molded parts – boosting elongation, tensile, flexural performance, maintaining features, strength, and accuracy. Vibratory Finishing, on the other hand, does not achieve a waterproof finish, but also provides exceptionally smooth surfaces, removes coating marks, and produces scratch and stain resistant surfaces. Components processed through Vibratory Finishing and Vapor Smoothing methods yield smooth surfaces with a glossy appearance. However, Vapor Smoothing provides a shinier finish compared to Vibratory Finishing. Additionally, parts treated with Vibratory Finishing exhibit a notably softer and more pleasant tactile experience.
However, it is important to note that Vapor Smoothing isn’t the best solution for every print. Models that are too complex, small, large, or flat may deform or lose detail, and rack marks may be visible afterwards. After the Vapor Smoothing process, parts may experience defects such as bridging, bubbling, bite marks, edge pooling, speckling, holes, or incomplete features. In addition, it is important to note that flexible materials are more susceptible to surface imperfections compared to rigid ones. Therefore care must be taken with timing when Vapor Smoothing moving parts or pieces with joints to avoid compromising joint integrity or causing sticking by excessive exposure to vapors.
Vibratory Finishing, on the other hand, is suitable for a wider range of 3D printed parts than Vapor Smoothing, as it can be adapted to any individual needs, material properties and structures of the part by choosing different abrasives and methods. As long as the process is always done professionally by an expert, Vibratory Finishing is suitable for almost all 3D printed parts. Nevertheless, Vibratory Finishing can result in a loss of geometry of the component. For example, corners and tips of the component may round off too much and lose their shape, which can not occur with Vapor Smoothing. In addition, Vibratory Finishing sometimes requires further drying procedures afterwards, which prolongs the process.
Fields of Application
Vapor Smoothing is a technique favored by industries such as medical, automotive and aerospace, providing watertight, bacteria-resistant, and chemical-free parts. When it comes to Vibratory Finishing, the medical, automotive, and sports industry in particular, benefit from this technique. In each of them, it is of great importance to have smooth surfaces, especially on metal parts, to ensure functioning processes and safe conditions. However, both Vapor Smoothing and Vibratory Finishing can be applied throughout the product development cycle, from concept models to prototypes to final products, and find wide application across various industries, such as medical, automotive, and consumer goods. Parts processed with the Vibratory Finishing process are, for example, car parts for the automotive industry or skate blades and fitness equipment for the sports industry. In addition, jewelry and cutlery are treated with Vibratory Finishing for consumers. One example that vapor smoothed parts are often used for in the automotive industry would be with the interior components of a vehicle, such as dashboards, door handles, and center console elements. Vapor Smoothing is also used for airplane parts in the aerospace industry, such as with wings, air ducts, and engine parts, among others.
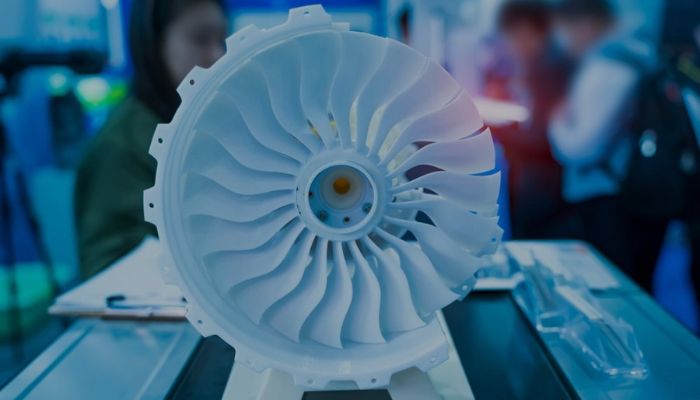
Vapor smoothing is commonly applied to airplane parts within the aerospace industry (Photo credits: Fast Radius)
Providers and Prices
Different service providers, for example SPALECK GmbH, VibraFinish or Rohde AG, offer Vibratory Finishing for both private clients and companies. For Vapor Smoothing, Xometry, AMT, DyeMansion, Protolabs, and Hubs are notable service providers offering Vapor Smoothing services with either a specified post-processing solution machine, or based on material. 3Faktur, a company out of Germany, offers both vapor smoothing and vibratory finishing services. Notable Vapor Smoothing machines like the AMT PostPro3D line, and Powerfuse S series, are solutions provided by Xometry and DyeMansion, whereas Protolabs and Hubs work with SLS and MJF HPA 12, PA 12, and MJF Ultrasint™ TPU-01 materials, respectively.
As for Vibratory Finishing, large industrial machines from manufacturers such as Walther Trowal, AVAtec or Garant range from about $18,000 – $21,000 (17,000 – 20,000 €). The abrasives vary between $21 – $44 (20 – 40 €) for 2kg and the compound also amounts to about $21 – $44 (20 – 40 €) for 5 liters. The price varies significantly depending on the quantity and size of the parts to be processed. For Vapor Smoothing, service fees to smooth a single part may range anywhere from $5 – $15 (4€ – 14€) depending on the complexity of the part, though many manufacturers will often only provide the service as part of a bundle of 10 parts or more. Purchasing a Vapor Smoothing machine unit itself can vary widely in cost depending on the needs, with the most basic solutions starting at $1000, while industrial solutions can go over $100,000 (900€ – 92,000€). Pricing may also be impacted depending on region, manufacturer, and quality.
Which surface finishing process would you choose for your parts? Let us know in a comment below or on our LinkedIn, Facebook, and Twitter pages! Don’t forget to sign up for our free weekly Newsletter here, the latest 3D printing news straight to your inbox! You can also find all our videos on our YouTube channel.
First, a “brickbat” – Vapour smoothing does not “melt” the surface, it dissolves it.
I use trichloromethane CHCL3 for both glueing and “dip-smoothing” both PLA and PETG parts. It has the advantage of not being flammable unlike either and acetone – although you still need to avoid breathing the fumes. The only real disadvantage is getting hold of it without alarming authorities or other ignorant people.