US Navy Partners with SPEE3D to Transform Submarine Manufacturing
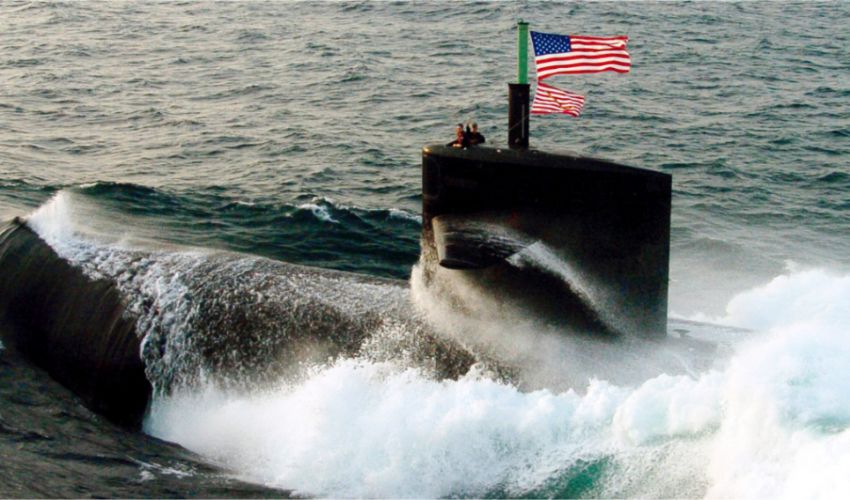
The Australian company SPEE3D, a leading metal additive manufacturing company, has been chosen by the US Navy for an exciting project that aims to develop Subsafe manufacturing materials using its patented cold spray additive manufacturing (CSAM) technology. This collaboration with the Naval Sea Systems Command (NAVSEA) is part of a larger project focused on Expeditionary Maintenance and Sustainment, with the goal of meeting the stringent quality standards of the Submarine Safety Program (SUBSAFE).
The partnership between SPEE3D and the US Navy marks a significant milestone as it represents the first time that cold spray additive manufacturing technology will be investigated as a manufacturing method for SUBSAFE-compliant applications. By working together with the Applied Research Laboratory of the Pennsylvania State University (ARL/PSU), a leading NAVSEA partner in cold spray technology development and transition, SPEE3D aims to develop an entirely new method to rapidly manufacture existing parts for critical submarine systems.
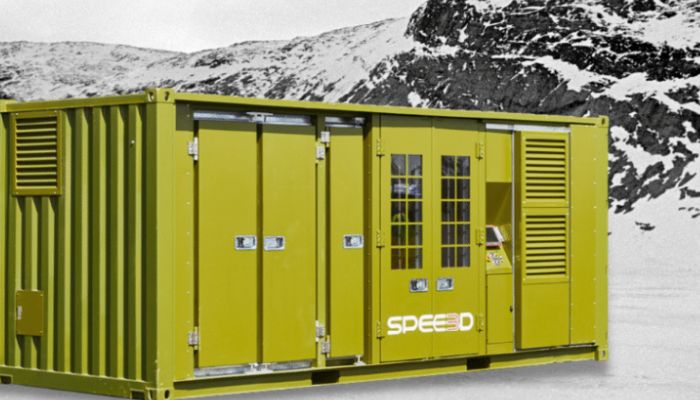
Metal cold spray additive manufacturing will be used to create NAVSEA’s submarine parts (Photo credit: SPEE3D)
The adoption of SPEE3D’s capabilities could revolutionize the manufacturing process for submarine parts, drastically reducing production time from months to hours. The technology, extensively tested by the US, UK, and Australian militaries, has already proven its reliability and effectiveness. Additionally, SPEE3D’s platform-agnostic approach allows for the manufacturing of various metals, including aluminum 6061, aluminum bronze, and copper.
US Navy’s Surge Toward 3D Printing
The U.S. Navy previously showed interest in 3D Printing earlier in the year with the acquisition of AML3D, focusing on supplying parts specifically to the submarine industrial base. While additive manufacturing has been used for ships, such as the USS Essex’s metal 3D printer, submarine-related projects had been relatively limited before the acquisition. However, the U.S. Navy recognized the potential of 3D printing in resolving supply chain issues plaguing submarine parts, leading to the collaboration with AML3D.
The centerpiece of the partnership was the adoption of AML3D’s Wire Additive Manufacturing (WAM) technology, a form of Directed Energy Deposition (DED) 3D printing. By combining an electric arc with welding wire, WAM enables the creation of industrial-grade parts. The ARCEMY® ‘X-Edition 6700’ system was stationed at the Oak Ridge National Laboratory, the largest science and energy laboratory within the U.S. Department of Energy system. The strategic location is facilitating the rapid scaling of part production, meeting the demands of the U.S. Navy’s submarine industrial base.
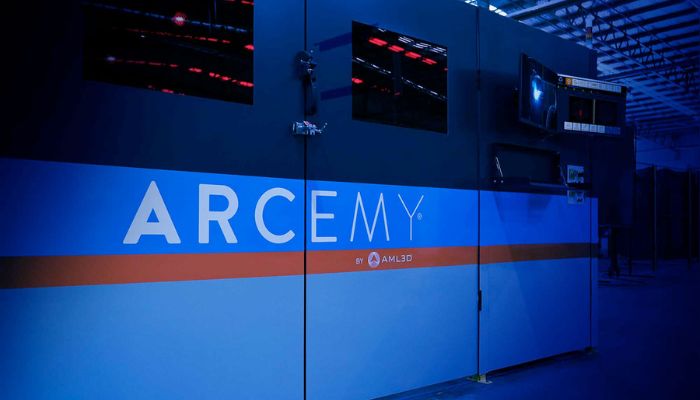
U.S Navy’s ARCEMY® ‘X- Edition 6700’ system from AML3D bought earlier in the year (photo credits: AML3D)
Now, with the U.S Navy’s recent collaboration with SPEE3D, Steven Camilleri, Co-Founder and CTO at SPEE3D, remarks, “We are honored to be chosen and trusted by the U.S. Navy to participate in this groundbreaking project. We have worked successfully with the U.S. Navy in the past and understand the unique challenges they face with the need for manufacturing capabilities that are fast, reliable, and easily deployable”
This partnership between SPEE3D, the US Navy, and ARL/PSU showcases the continuous drive for innovation and improvement within the defense industry. By leveraging the power of cold spray additive manufacturing, the project aims to advance the production of submarine parts, enhance maintenance and sustainment operations, and ultimately bolster the safety and efficiency of the US Navy’s submarine fleet. For more information about the project, find it HERE.
What do you think of this partnership between SPEE3D and the US Navy? Let us know in a comment below or on our LinkedIn, Facebook, and Twitter pages! Don’t forget to sign up for our free weekly Newsletter here, the latest 3D printing news straight to your inbox! You can also find all our videos on our YouTube channel.
*Cover photo credits: US Navy