US Bobsled Team (USABS) Turns to 3D Printing Before the 2026 Olympics
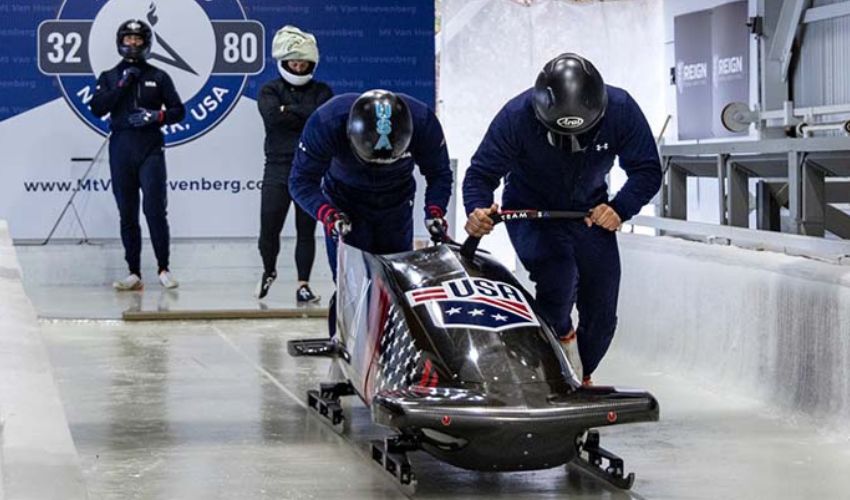
Bobsled is an incredible sport that has been increasingly winning over adrenaline junkies worldwide. Though in the USA, most people’s exposure to the sport is through the 1990s hit movie “Cool Runnings,” it is now a popular winter event. And now it has a connection to additive manufacturing as well. The US team has announced that it is already focusing on preparing for the next Winter Olympics in 2026 with the United States Bobsled and Skeleton Federation (USABS) is modernizing the sport by turning to 3D printing.
Although the means have changed since the sport’s beginnings, the parts for the bobsleds must be able to withstand increasingly high loads due to the speed and physical forces involved. In addition, the personalization of the equipment is playing an increasingly important role and, of course, the safety of the athletes, which requires appropriate measures. It is for these reasons that the USABS has turned to additive manufacturing to produce several sled parts.
3D printing does not require the casting of molds, resulting in lower costs and time savings. Moreover, parts can be customized and there are virtually no limits to the design, meaning that even complex components can be manufactured with ease. The USABS team was also convinced by these advantages and announced a new partnership with the American 3D printing service provider CRP USA on October 4, 2023.
This company uses SLS and PBF processes to produce functional parts for the aerospace, automotive, motorsport and defense sectors. As part of this alliance, the collaboration partners launched a new project for the 2026 Winter Games and equipped the US team’s racing bobsleds with 3D-printed parts, including push handles, grab handles and seats. It was also necessary to comply with the regulations of the Olympic Sports Authority with regard to the shape and size of the parts.
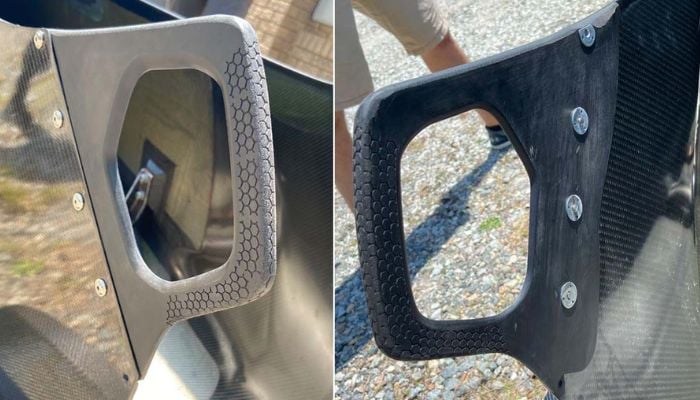
The USABS team prints several bobsled parts in 3D, including push handles
USABS Relies on Windform High-Performance Materials
In bobsled, the start with the push phase is crucial in order to build up maximum speed. The athlete must have complete trust not just in their teammates – unless they are competing individually – but also in the material. Due to the high risk of falling, the materials used in bobsleigh must be both flexible and robust so that they do not give way or break.
After extensive studies, CRP USA and the USABS team opted for the Windform materials from the Italian company CRP Technology. These high-performance materials are used in motorsports and aerospace applications, among others. CRP USA uses the SLS process to print the bobsled parts from the carbon fiber-reinforced materials Windform SP and Windform XT 2.0. Meanwhile, the seats and grab handles are made from Windform XT 2.0.
For the push handles, CRP USA and USABS use Windform SP, which is extremely resistant to impact, vibration and deformation. Nathanael Baker, Senior Project Coordinator for CRP USA, explained: “The USABS team needed to easily produce the push handles, in addition to customize the handles based on each athlete and easily change them out.”
The parts were printed quickly and after a few tests and adjustments, the optimized components could also be tested in a real situation. Notably focusing on stress resistance and ergonomics. “We don’t have an official test program, we assemble the parts and use them in a race. And so we did with the 3D printed parts in Windform: This means that the seat, hand grip and rear push handle were immediately tested in a real race!” further explained Marc van den Berg, Technology and Equipment Lead at USABS.
The official debut of the 3D-printed parts took place at the IBSF North American Cup (NAC) from November 15 to 19, 2023, with a special focus on the rear push handles. These must remain intact even in the event of a fall. In addition to the pleasing results of the competition, the components also passed their baptism of fire. USABS was not only impressed by the freedom of design and the logistical advantages of the 3D-printed parts thanks to their fast delivery, but also by their performance.
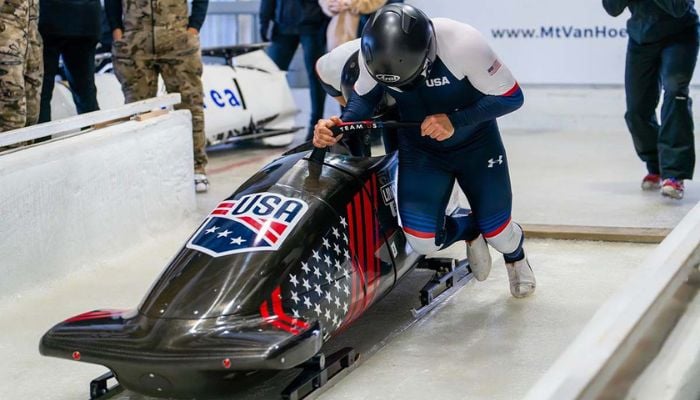
The start phase is crucial for the course of the race. The equipment must meet the highest standards
For Van den Berg, this is cause for further consideration: “Hopefully we can 3D print more parts in the future, perhaps even a complete bobsled!! “Who knows, maybe this is the next trick in the US team’s Olympic preparations. You can find out more about the 3D-printed bobsled components HERE.
What do you think of the USABS team’s 3D-printed bobsled parts? Let us know in a comment below or on our LinkedIn, Facebook, and Twitter pages! Don’t forget to sign up for our free weekly Newsletter here, the latest 3D printing news straight to your inbox! You can also find all our videos on our YouTube channel.
*All Photo Credits: USABS