US Army studies how to predict when metal AM parts will degrade or fail
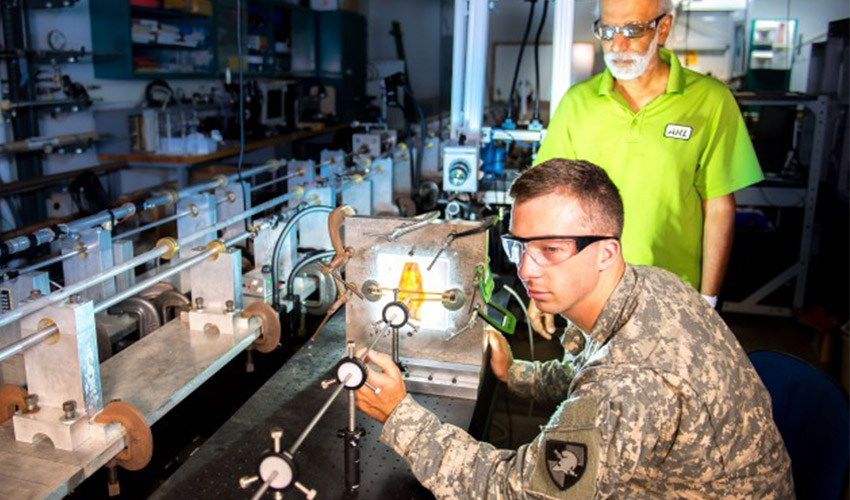
As you may know, the US Army has been investing in additive manufacturing technologies to leverage the benefits of increased design freedom, shorter lead times, lower costs for unique parts, and increased performance. In fact, US Army researchers from the CCDC Army Research Laboratory studied how to monitor the fatigue of additively manufactured maraging steel parts – which is of key importance to predict the maintenance these parts will require. This research could help soldiers maintain readiness as they will be able to predict when parts will degrade or fail and need replacement.
Their study was published in the International Journal of Advanced Manufacturing Technology, titled In-Situ Fatigue Monitoring Investigation of Additively Manufactured Maraging Steel, and looks specifically at how the US Army could detect and monitor the wear of metal additively manufactured maraging steel. Maraging steel are known for possessing superior strength and toughness without losing ductility. 3D printed using the Laser Powder Bed Fusion (LPBF) process, these parts benefit greatly from the AM process, however some features need to be checked. “3D printed parts display certain attributes, due to the manufacturing process itself, which, unchecked, may cause these parts to degrade in manners not observed in traditionally-machined parts,” explains Dr Jaret C Riddick, Director of the Vehicle Technology Directorate at the US Army’s Combat Capabilities Development Command’s Army Research Laboratory.
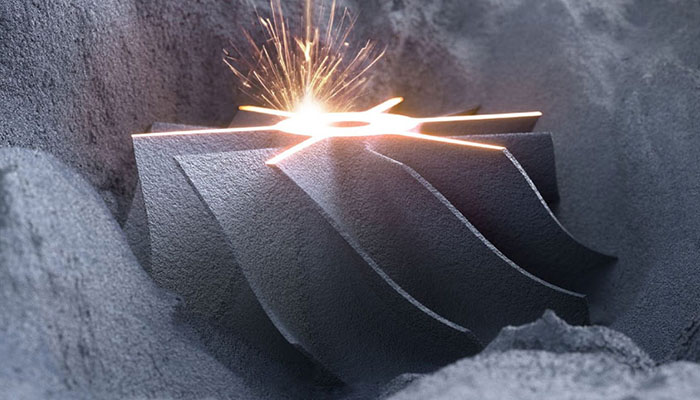
The laser powder bed fusion process
The best way to understand material fatigue is to consider a paper clip, and imagine bending it back and forth until it breaks. Taking different paper clips and repeating the process, they will break at different intervals depending on the internal imperfections associated with the steel. Dr Todd C Henry, a mechanical engineer at the laboratory, who co-authored the study explains in more detail: “Every real-world material and structure has imperfections that make it unique in terms of performance, so if the batch of paper clips take 21–30 cycles to break, what we would do today is after fifteen cycles throw the batch of paperclips away to be safe.” Essentially, the same holds true for 3D printed parts made of steel.
In AM, the imperfections are mostly due to the gap between the geometry modeled on the computer and the actual 3D printed output. The sensor technology developed by Dr Henry in the context of this study offers a way to track individual parts, predict failure points and replace them before they break. “With 3D printing, you might not be able to replace a part with the exact same material. There is a cost and time benefit with 3D printing that perhaps warrants using it anyway. Imagine a situation where you always chose the strongest material but there was another material that was cheaper and easier to get; however, you need to prove that this other material can be depended on,” he comments.
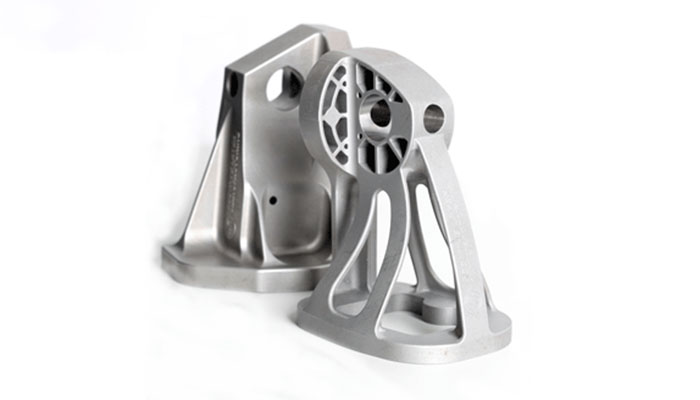
Metal additively manufactured parts
Understanding the performance of 3D printed metal parts long after they have been manufactured is of key importance to sectors on this aspect. Army researchers are said to be applying the findings of the study to new studies on the AM of stainless steel parts and using machine-learning techniques, instead of sensors, to characterise the lifespan of parts. You can find more information HERE.
What do you think of this study? Let us know in a comment below or on our Facebook and Twitter pages! Don’t forget to sign up for our free weekly Newsletter, with all the latest news in 3D printing delivered straight to your inbox!