US Air Force and GE’s collaboration on metal AM reaches first milestone
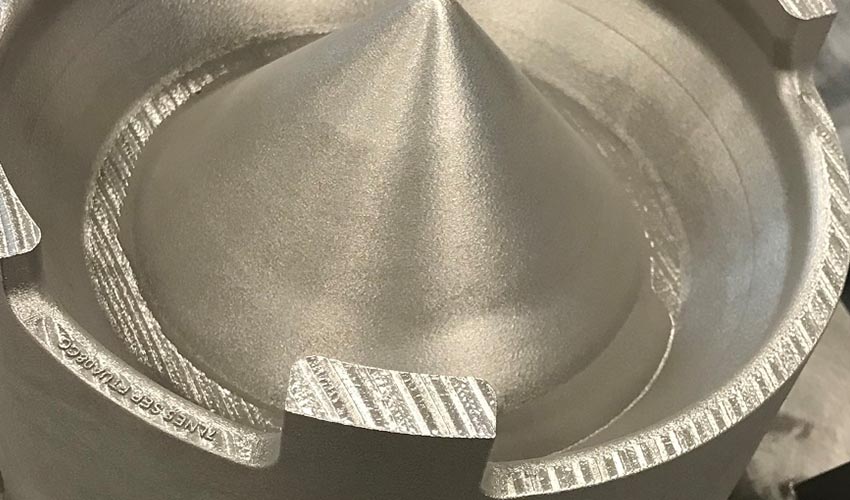
In mid-2019, GE Additive and GE Aviation approached the US Air Force to propose a metal additive collaboration program to address its specific sustainment, readiness and affordability needs. It’s the US Air Force’s Rapid Sustainment Office (RSO) that is in charge of the operation and sustainment of its fleet of aircraft. Given the number of aircraft soon entering their sixth decade of service, difficulties in sourcing and producing spare parts could represent a significant risk. This is where 3D printing technologies come in, enabling the production of unique, on-demand parts that meet the specific requirements of the aerospace industry.
GE has previous experience qualifying and certifying additively manufactured metal components that meet the commercial aviation sector’s rigorous regulatory requirements. Colonel Benjamin Boehm, director, AFLCMC/LP Propulsion Directorate, explains: “The collaborative effort between the US Air Force and GE shows great promise toward the adoption of metal 3D printed parts as an option to solve the US Air Force’s current and future sustainment challenges. This capability provides an alternate method to source parts for legacy propulsion systems throughout their life cycle.”
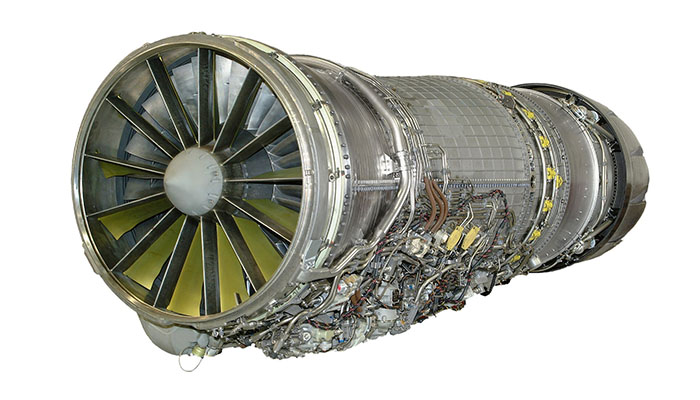
GE Aviation F110 engine | Credits: GE Additive
The benefits of metal additive manufacturing
The US Air Force and GE settled on a program based on a “spiral development” model that increases in complexity and scale with each phase. In this program, complexity involves moving from simpler part identification, progressing to part and family of parts consolidation and eventually tackling complex components and systems, such as common core heat exchangers. The key benefit of using additive manufacturing technologies in this case is the speed at which it is possible to develop these solutions.
Lisa Coroa-Bockley, general manager for advanced materials solutions at GE Aviation explains: “Speed is additive’s currency, and by applying our additive experiences with the LEAP fuel nozzle and other parts additively printed for the GE9X, being able to offer an end-to-end solution and also applying lessons learned of a robust certification processes, we’ve been able to accelerate the pace for the US Air Force.”
GE explains that phase 1 of the program has already been completed. It involved the identification of GE Aviation spare parts for the F110 and TF34 engines and demonstrating their airworthiness capability. Preliminary work had been completed on the sump cover for the General Electric F110 engine used on both F-15 and F-16 aircraft, and that part became the focus part for this first phase. Compared to other parts on the F110 engine, the sump cover might have lower functionality, but is incredibly important. It needs to be durable, form a seal and it needs to work for the entire engine to function. GE Additive Concept Laser M2 machines running cobalt-chrome at the ATC were used for the first builds of additively manufactured sump covers.
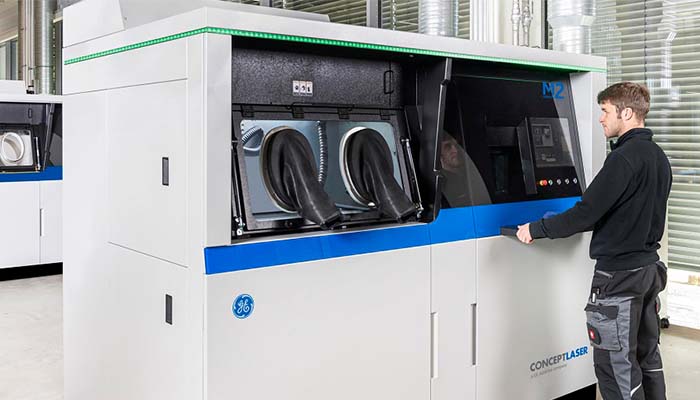
GE’s Concept Laser M2 machine
This collaboration truly encapsulates how additive manufacturing will advance and inform design, manufacturing and certification for things we’ve never seen before in the commercial and military aerospace sectors. During the entire process, the parties have been exploring how metal additive manufacturing might replace conventional manufacturing methods for parts no longer in production or where smaller production runs are needed. You can find more information HERE.
What do you think of this collaboration? Let us know in a comment down below or on our Facebook and Twitter pages! Don’t forget to sign up for our free weekly Newsletter, with all the latest news in 3D printing delivered straight to your inbox!