University of Toronto Researchers Create ‘Strong as Steel, Light as Foam’ Nano-Architected Materials Using 3D Printing
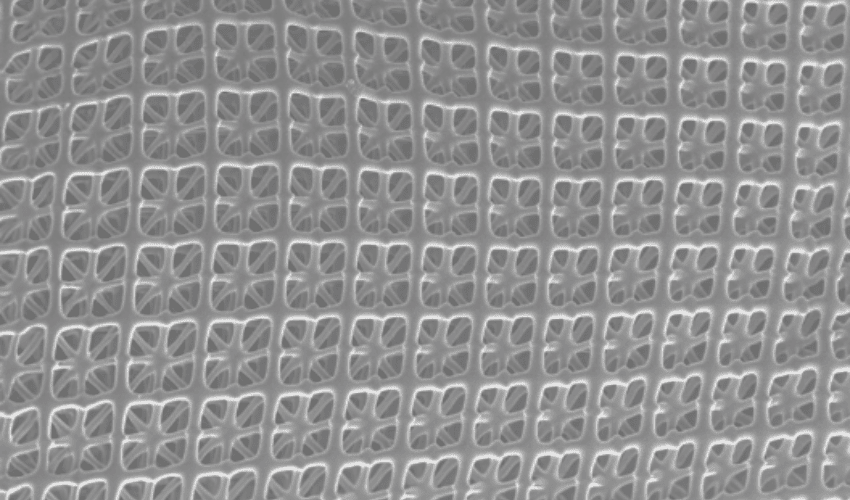
Thanks to machine learning and 3D printing, researchers at the University of Toronto have developed nano-architected materials that combine the strength of carbon steel with the lightness of polystyrene foam. 3D printing, which facilitates the creation of such innovative materials, is thus becoming an increasingly popular tool for designing materials with advantageous properties for a variety of fields. This development is not a first, as more and more new advances are emerging in this field, with a potential impact for many industries.
Under the direction of Professor Tobin Filleter, a team developed these nanomaterials with interesting characteristics, combining robustness, lightness and adaptability. This process could transform many sectors, from automotive to aerospace. But how was this material conceived, and what are its exact properties? Read on to find out more.
Nano-Architectured, 3D-Printed Materials for Ultra-Light, High-Strength Aerospace Applications
These materials are made up of small, repetitive units measuring just a few hundred nanometers. To reach the thickness of a human hair, more than 100 would have to be aligned. These units, mainly made of carbon, form complex 3D structures called nanolattices.
“Nano-architected materials combine high performance shapes, like making a bridge out of triangles, at nanoscale sizes, which takes advantage of the ‘smaller is stronger’ effect, to achieve some of the highest strength-to-weight and stiffness-to-weight ratios, of any material,” explains Peter Serles, one of the lead researchers. “However, the standard lattice shapes and geometries used tend to have sharp intersections and corners, which leads to the problem of stress concentrations. This results in early local failure and breakage of the materials, limiting their overall potential. As I thought about this challenge, I realized that it is a perfect problem for machine learning to tackle.”
Peter Serles and Tobin Filleter collaborated with the Korea Advanced Institute of Science & Technology (KAIST) in South Korea to develop their materials. The team used a machine learning algorithm to predict the best shapes to improve the materials’ strength and lightness. Next, Serles used a two-photon polymerization 3D printer to create micro- and nanoscale prototypes. The improved nanolattices more than doubled the strength of the previous models, capable of withstanding a stress of 2.03 megapascals per cubic meter per kilogram, around five times that of titanium.
“This is the first time machine learning has been applied to optimize nano-architected materials, and we were shocked by the improvements,” explains Serles. “It didn’t just replicate successful geometries from the training data; it learned from what changes to the shapes worked and what didn’t, enabling it to predict entirely new lattice geometries. Machine learning is normally very data intensive, and it’s difficult to generate a lot of data when you’re using high-quality data from finite element analysis. But the multi-objective Bayesian optimization algorithm only needed 400 data points, whereas other algorithms might need 20,000 or more. So, we were able to work with a much smaller but an extremely high-quality data set.”
The aim of these new designs is to create ultra-light components for aerospace applications, such as airplanes, helicopters and spacecraft. These materials could reduce fuel consumption while maintaining safety and performance standards. You can find out more in the research paper HERE.
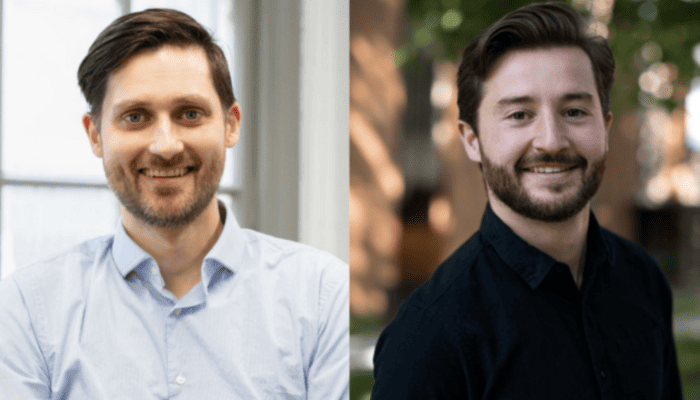
On the left, Tobin Filleter, and on the right, Peter Serles
What do you think of these materials? Let us know in a comment below or on our LinkedIn, Facebook, and Twitter pages! Don’t forget to sign up for our free weekly Newsletter here, the latest 3D printing news straight to your inbox! You can also find all our videos on our YouTube channel.
*All Photo Credits: University of Toronto