TrueInsight on the Importance of Design Tools for Additive Manufacturing
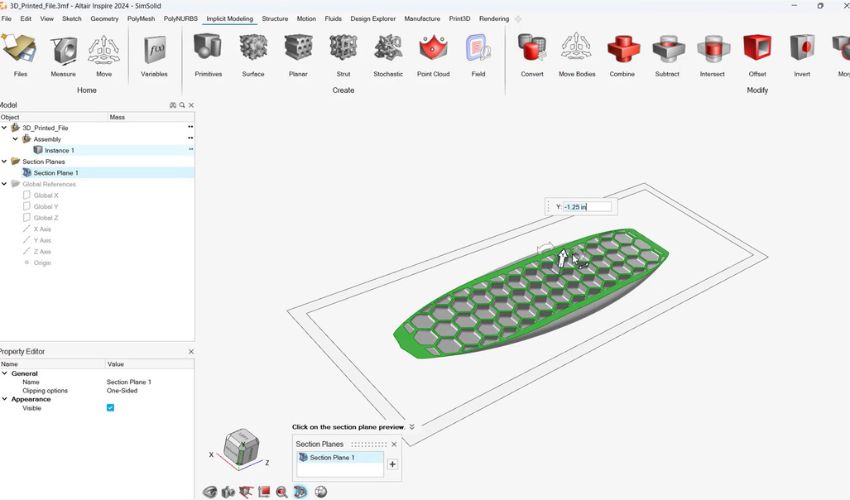
When you think of 3D printed parts, what comes first to mind is often the 3D printing process used or the chosen materials. But what if we told you there was a step even more critical than that which impacts each stage of additive manufacturing? Design is the core of 3D printing as the failure or success of the part often hinges on how well it was created. This is why tools and software, like Altair Inspire, are so critical, especially as the sector industrializes. To give us insights on this, we spoke to TrueInsight to learn more about the importance of DfAM and about using the right tools to create parts for 3D printing.
3DN: Could you introduce yourself and TrueInsight?
My name is Tyler Haggin and I am the COO at TrueInsight, we are a partner for the Altair Engineering software portfolio in the United States. TrueInsight was spun off the largest SOLIDWORKS (CAD) and Stratasys (AM) partner globally.
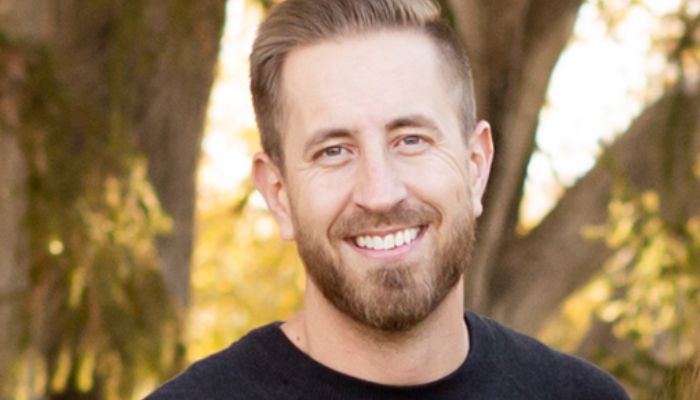
Tyler Haggin, the COO at TrueInsight
Within our leadership team, we have nearly 40 years of industry experience and worked closely with many customers as the early on 3D printing “trend” turned into a business-critical process. Now this is standard in most product development processes.
3DN: Could you tell us more about Altair? Why is it well-suited to additive manufacturing?
Altair has long been a leader in the topology optimization arena. This basically allows end users to reduce the mass or volume of their design, while maintaining the design intent. The shapes that are created with this process tend to be more organic looking, which means traditional manufacturing methods aren’t ideal. Additive manufacturing allows users the ability to take advantage of these shapes, which unlocks innovation at a different level.
Also, recently, Altair has integrated implicit modeling functionality into its Altair Inspire tool. Implicit modeling is field-driven and allows users to create complex lattice shapes including planar, strut and stochastic models. This ability, again, allows users to create stronger and lighter parts, which can easily be created with additive manufacturing.
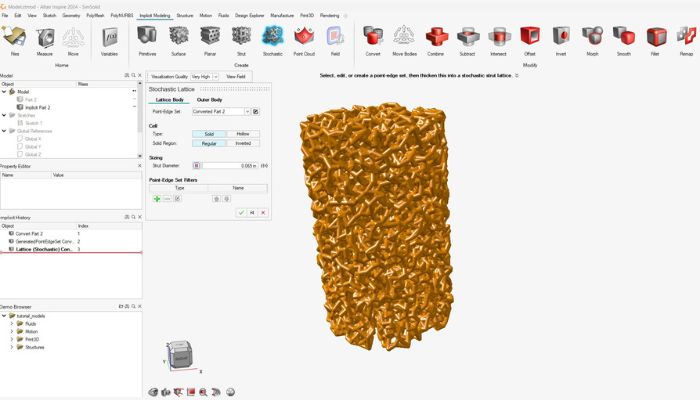
Altair Inspire can be used to make complex lattice shapes including stochastic models (pictured above)
3DN: What is the importance of DfAM for creating better parts? For example, with lattice structures or topological optimization?
With additive manufacturing now being a standard process across many industries, the trend of DfAM or Design for Additive Manufacturing has also become a requirement. Essentially, designers are having to change their way of thinking when designing a part, to metaphorically release those handcuffs of a part needing to be manufacturable or cost-effective by traditional methods.
New parameters now need to be considered. For example, understanding design guidelines for minimum feature size, maximum overhang angle, and minimum wall thicknesses will give you constraints on what can be reasonably be printed.
With additive manufacturing, these complex lattice structures can now be printed easily. As a result, more and more designs are starting to utilize lattice structures. The challenge with lattice structures is that they are often modeled with traditional boundary representation CAD (BREP), the resulting file sizes can be sizable or even unable to be created with traditional CAD. With huge file sizes the process of slicing these parts to be printed can often be very time-consuming and inefficient. This is where the implicit modeling within Altair Inspire can significantly impact that pain point, making it more efficient to print.
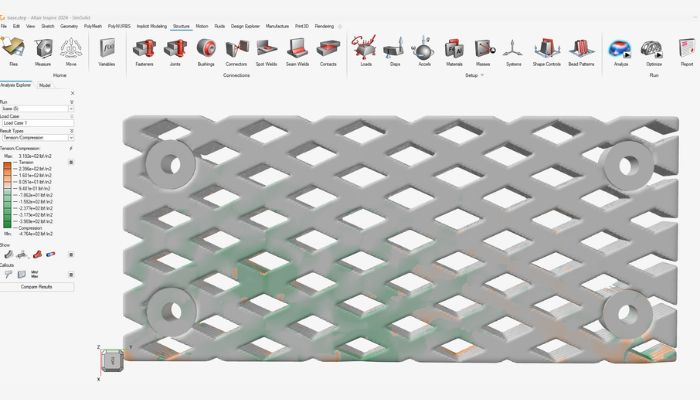
Altair Inspire can help improve efficiency in printing, including through ensuring the design can be efficiently 3D printed
3DN: What do users get wrong when it comes to design for 3D printing? How can Altair help improve it?
If anything, I think maybe there is a misconception about how simple and cost-effective it can be to incorporate these tools into your existing workflow.
For example, Altair Inspire includes the ability to create geometry through the traditional BREP process found in most CAD tools, but also implicit modeling for creating lattice structures. Then, it includes the Altair OptiStruct optimization solver for lightweighting and without leaving the Inspire interface users can run stress testing and even CFD simulations. Inspire is already known for its ease-of-use and its low price point, so I think the main challenge is just educating end-users that this is now more accessible.
Outside of just the education on the technologies, think there is one other common challenge that people run into when designing with this process in mind: Not enough time is spent considering the actual additive manufacturing process and how to be more efficient there.
For instance, a design engineer may work very hard to maintain stiffness by running a finite element simulation, running topology optimization to obtain a new part design. The part design may reduce mass by 30 percent while maintaining the stiffness, but the part design may be problematic for printing because of challenges in the manufacturing of that part due to things like overhang angles. Thankfully, Altair’s tools do allow for the users to not only design with fewer constraints, but also ensure its manufacturability all within the same interface.
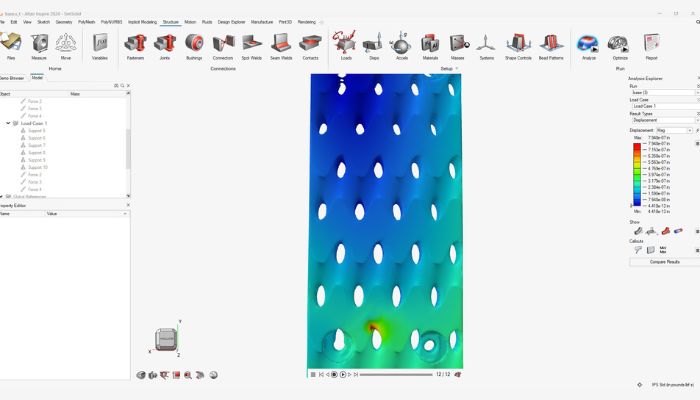
Altair Inspire integrates tools that allow users to ensure the manufacturability of the part
3DN: Could you tell us about some specific case studies where Altair software have been used to create better parts? Which sectors can they be used in?
We have seen the most adoption in areas where lightweighting is critical. So the aerospace or automotive sectors are the obvious ones, but in the last few years, we are seeing more and more users across industries start to use these technologies for creating more unique or innovative designs.
Some specific examples of these additional industry applications include the case of the Gondola lift station building where a topology optimization solver was used to improve the design of lift brackets. In this case, Etteplan was able to successfully use Altair OptiStruct™ and Altair Inspire™ to redesign their valve spring press tools used for mounting cylinder head valves. More specifically, these simulations solutions were used to run topology optimization and finite element (FE) analyses to create the design concepts. The resulting part was printed within one week and met both the cost and material usage targets.
Or another case is Nolato, a global provider of injection molded parts that developed its medical self-injector using Altair and Avalon Innovation. Given how important autoinjectors are for sufferers of diseases such as diabetes, part design is critical for ensuring that quality and durable injection molded parts are created. Altair was perfect because it allowed the company to have a single workflow going from a sketch to different concept designs. The resulting prototypes would then perform as expected, increasing confidence as Altair’s suite of integrated multidisciplinary tools provides timely, robust, and accurate answers.
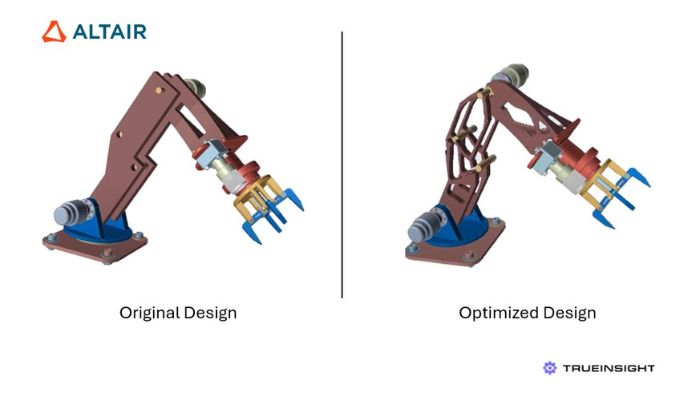
Altair Inspire can help optimize a design, as seen with this before and after image
3DN: Any last words for our readers?
I am really excited to see providers focusing on the software and design portion of the additive manufacturing process. As this space continues to evolve, I think we will see designers really unlock their creativity with regards to how they solve engineering problems. Altair is known for its leading CAE tools, and within the last few years I feel like their solution for additive manufacturing design is as good or better than any in the industry. You can learn more about TrueInsight as well as find the right Altair solution for you HERE.
What do you think about Altair? How important is software to ensuring a smooth design process for 3D printed parts? Let us know in a comment below or on our LinkedIn, Facebook, and Twitter pages! Don’t forget to sign up for our free weekly newsletter here for the latest 3D printing news straight to your inbox! You can also find all our videos on our YouTube channel.
*All Photo Credits: TrueInsight