Trio Labs and its Microscopic Metal 3D Printing Technology
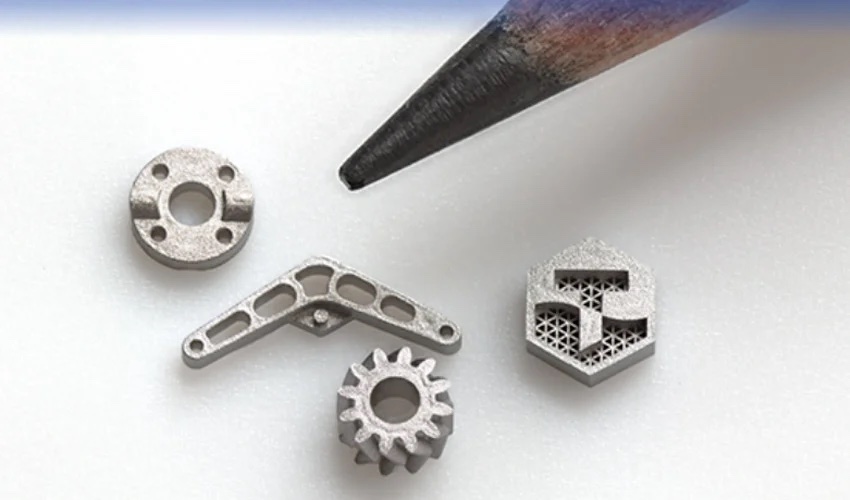
Trio Labs is an American company that has developed a metal additive manufacturing technology capable of designing parts on a microscopic scale. Called Resin Infused Powder Lithography, it can achieve a resolution of 5 microns, making it possible to design highly detailed and precise components. It is mainly used in the healthcare sector, where personalization is key. We caught up with its founder and CEO, Adam Steege, to find out more about how this process works and the prospects it offers.
3DN: Could you introduce yourself and tell us about your connection with 3D printing?
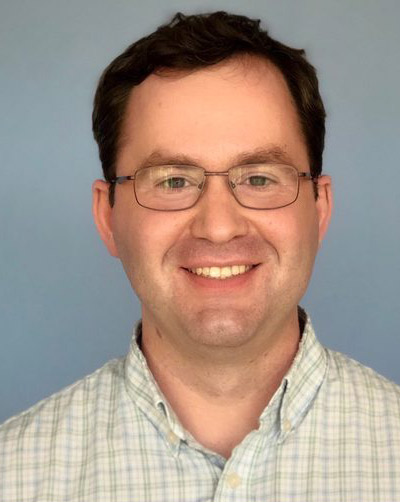
Adam Steege
I started my first company in 2010 to develop advanced laparoscopic surgical instrumentation, and utilized 3D printing, as well as CNC and casting processes to develop those devices. I’ve also worked extensively in medical device development in a consulting capacity over the past 10+ years, and have used those processes as well as stamping and molding to produce devices. I had a lot of the same frustrations with 3D printing that I think most design engineers have had, especially when it comes to metal printing (poor surface finish, poor tolerances) so I started Trio Labs to fix some of those problems.
3DN: What is Trio Labs’ mission?
Trio Labs has developed a technology called Resin Infused Powder Lithography (RIPL). This process provides the precision of CNC machining with the flexibility of 3D printing. We are primarily focused on healthcare applications, since there is a tremendous need for the parts we can make in the minimally invasive surgical space as well as in interventional catheters. More broadly, there is a continuous push towards miniaturization in many verticals, and we will support this type of innovation everywhere we can.
3DN: What are the special features of your micro-scale metal additive manufacturing technology? How did you manage to make it so precise?
RIPL can print metal parts at 5 micron resolution, which is about 10x better than standard metal 3d printing. It is scalable to high volume production to a level that is impossible with any other micro metal printing process. The quality of the parts produced, in terms of surface finish, tolerances, and mechanical properties, is truly unique. We achieved this by reinventing several key aspects of the printing process itself, to produce ultra-high quality green parts for sintering. We’ve combined this with high throughput and high quality sintering processes, with results that our customers routinely describe as the best they’ve ever seen from a 3D printing process.
3DN: What are the main advantages of additive manufacturing for Trio Labs?
By providing a digital manufacturing technology to our customers that matches their needs for precision and quality, and is scalable from 10 parts, to 100,000 parts and beyond, we are offering a faster and more efficient path to commercializing their new devices, while also opening up design opportunities that did not exist before. They can fully take advantage of the digital flexibility of 3D printing, without having to worry about qualifying a different process for production.
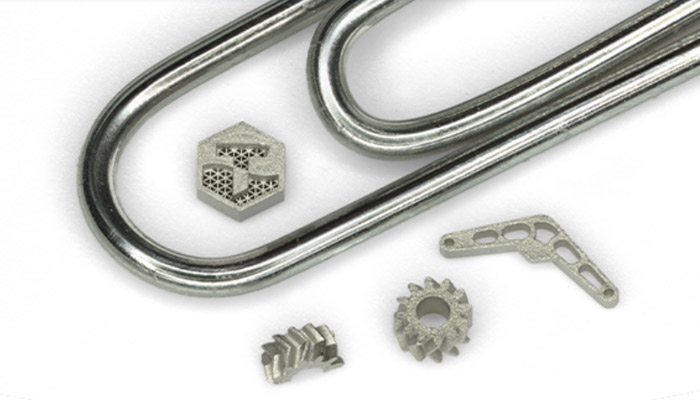
The technology allows for very precise resolutions
3DN: How do you see the continued role of 3D Printing in healthcare?
I think there are a lot of different ways that 3D Printing can impact healthcare, many of which are already happening. The ability to design solutions that are patient-specific is already being utilized in creating custom surgical guides and orthopedic implants. Beyond that, I see a lot of opportunity in targeting areas where there is value in being able to operate at different levels of scale seamlessly. The right 3D printing technology can make one part as easily as one million, which is a level of versatility that is an absolute necessity when operating in an environment like the healthcare space where there is a high mix of highly varied devices.
3DN: What are the main difficulties you have encountered in your work?
The main obstacle we run into is the accumulated fatigue that a lot of engineers have had with other 3D printing processes. They’re used to poor quality parts that don’t meet mechanical specifications, and material properties that don’t match spec sheets. At the same time, this challenge is our greatest opportunity. In every instance, we’ve provided parts to customers that have exceeded expectations, and that goes a long way toward building trust and getting engineers to reevaluate what’s possible with 3D printing.
3DN: Any last words for our readers?
If you have a project requiring micro-scale metal components, visit our website HERE.
What do you think of the technology developed by Trio Labs? Let us know in a comment below or on our LinkedIn, Facebook, and Twitter pages! Don’t forget to sign up for our free weekly Newsletter here, the latest 3D printing news straight to your inbox! You can also find all our videos on our YouTube channel.
*All Photo Credits: Trio Labs