Tree-Root Inspired Template-Constrained Additive Technique Creates Durable Electronic Circuits
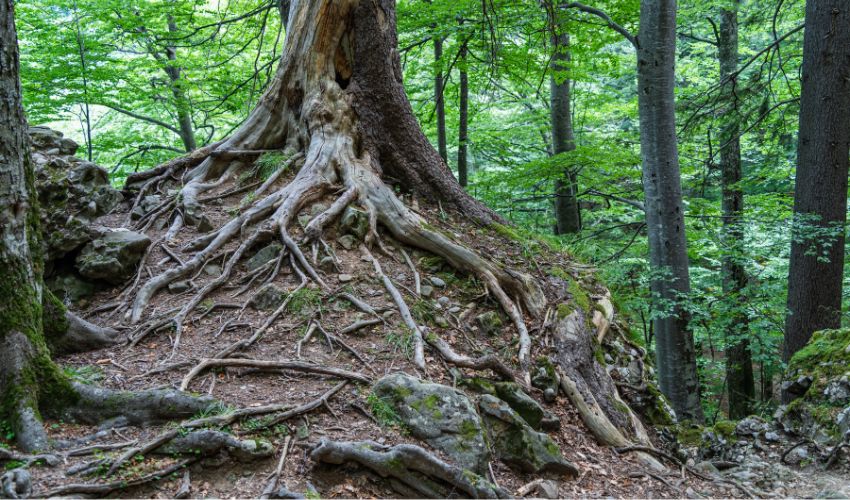
Conformal electronics are stretchable, flexible electronic devices often used for applications like smart skins and robotics. While 3D printing conformal electronics is possible, the process can come with challenges. Often, conformal electronics have significant mechanical and thermal vulnerabilities. Those made through traditional printing are often prone to tearing, cracking and other damage, which limits their performance and dependability. Furthermore, fabricating high-resolution circuits with diverse materials is cumbersome, and requires innovative manufacturing techniques to ensure mechanical durability and precision.
To address these issues with conformal electronic fabrication, Researchers at Xi’an Jiaotong University developed Template-Constrained Additive (TCA) printing technology and published their findings in December 2024. According to the results of their paper, titled Root-inspired, template-confined additive printing for fabricating high-robust conformal electronics, the new method promises to improve the durability and precision of additively manufactured electronic circuits.
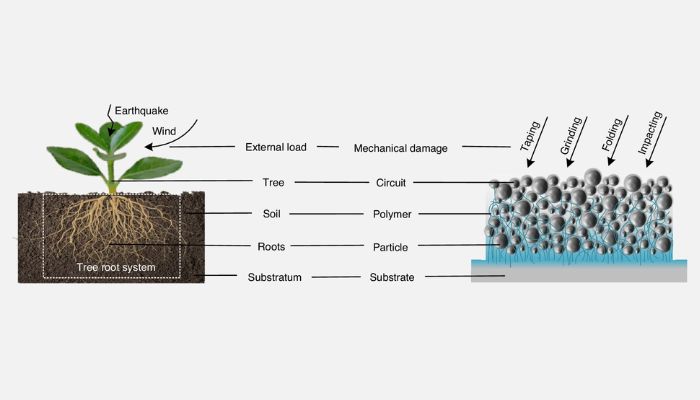
Image credit: Xi’an Jiaotong University
Template-Constrained Additive: Inspired by Tree Roots
This biomimetic approach was inspired by the strength of tree root systems. In the face of violent winds and earthquakes, tree roots keep a tree grounded. The key here is the roots’ relationship with the soil: they are interlocked, promoting tight stacking of the soil particles. So, the Xi’an Jiaotong University researchers aimed to replicate these circumstances by creating a circuit that interlocked polymers and conductive polymers.
To achieve this, they embedded adhesive into functional materials, creating a deep interlocking interface that significantly strengthens the circuit’s mechanical integrity. The embedded adhesive allowed the circuits to retain their electrical performance, even under extreme environmental conditions. Additionally, the method can create multi-layered, self-aligned circuits, overcoming several limitations of traditional printing techniques.
TCA allows the circuits to withstand temperatures up to 350°C and intense mechanical wear. The technology is also capable of achieving high-resolution printing, with a precision of up to 300 nm. Compatible with a variety of materials, including copolymers, carbon nanotubes and silver nanoparticles, the method could support diverse applications.
To test TCA’s viability, the researchers experimented with printing on arbitrary surfaces, including smooth (acrylic, glass, chili and nitrile gloves) and rough (egg, pigskin, sandpaper and magnesium alloy). The fact that TCA allowed printing on all of these surfaces demonstrates the method’s flexibility. On these surfaces, they printed conformal temperature and humidity sensors and ultra-thin energy storage systems to demonstrate the technology’s capabilities. This highlights TCA printing’s potential to transform the future of electronics.
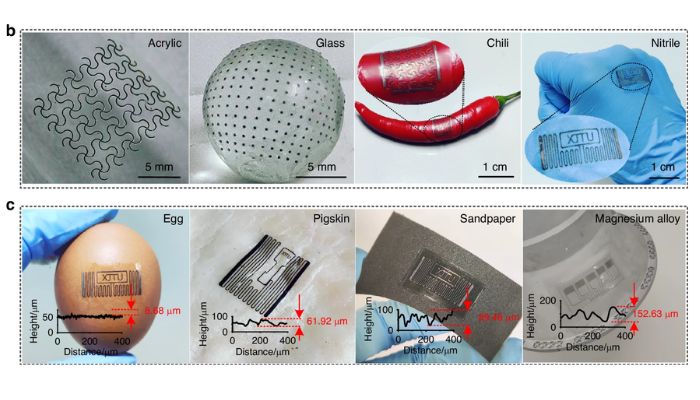
Image credit: Xi’an Jiaotong University
Dr. Jinyou Shao, a co-author of the study and the group leader, emphasized the significance of this innovation: “The TCA printing technology represents a major leap forward in the field of conformal electronics. By drawing inspiration from nature, we’ve developed a solution that not only enhances the durability of electronic circuits but also achieves remarkable precision and versatility. This makes it ideal for a wide array of applications, from wearables to advanced robotics.”
Potential Applications
Because the TCA method increases dependability, ensuring that electronic circuits can withstand extreme conditions like high temperatures and mechanical stress, it opens up opportunities for diverse applications. According to the press release, it seems like there is no limit. For one, the technology could be useful for autonomous vehicles, where sensors must endure harsh environmental conditions. Additionally, TCA could create electronic components for robotic skin and joints. Everyday objects could benefit from this technology as well, for the creation of wearable devices and smart textiles. Aerospace and biomedical projects could use TPA too, because durability and precision are critical in those spaces. For a more in-depth look at the study, read the full research paper HERE.
What do you think about the new method for printing conformal electronics? Let us know in a comment below or on our LinkedIn, Facebook, and Twitter pages! Don’t forget to sign up for our free weekly Newsletter here, the latest 3D printing news straight to your inbox! You can also find all our videos on our YouTube channel.