Topology Optimization vs. Generative Design: Which Modeling Tool Should You Choose?
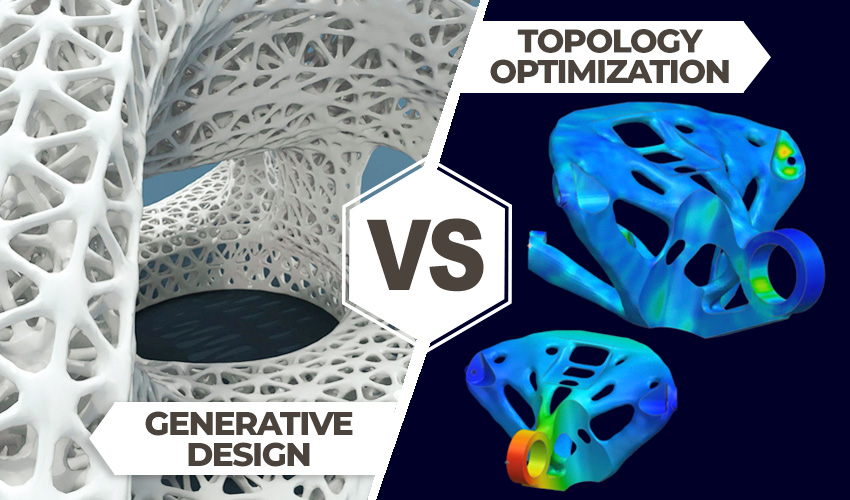
There is a constant race for even faster production, parts meeting higher demands and to surpass our current accomplishments. To achieve this, the products we manufacture have to be optimized in one way or another, so that they perform even better. Often, this means reducing the weight of parts while striving for greater strength and performance. And this “less is more” equation starts right at the design stage! While designers strive to work designs in this direction, new technologies such as artificial intelligence and machine learning bring new possibilities, as is the case with topology optimization and generative design.
Topology optimization and generative design are two approaches which, with the help of computer-aided calculations, optimize designs so that they are more efficient, saving on costs and resources during production, to name but a few incentives.Although the two methods pursue similar objectives, they should not be equated or confused. We took a closer look at what is meant by topology optimization and generative design, the advantages, challenges, concrete fields of application and examples, and explain their usefulness in combination with 3D printing.
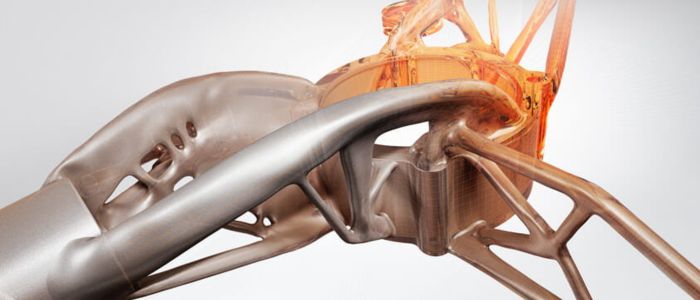
Photo Credits: Mensch und Maschine
Get the Best Design Faster With Topology Optimization and Generative Design
Topology optimization is not a new method in itself, and has been used since the early 1990s to optimize 3D models in such a way as to retain basic functions while saving materials when the part is not required to carry loads. Topology optimization always begins with a human design, which must be adapted so that performance is not reduced despite the savings made. To achieve this, however, it is necessary to define certain framework conditions, such as taking account of the forces at work and defining protected zones. Computer algorithms then create a mesh model whose structural integrity must be verified during finite element analysis (FEA). The result must then be checked and, if necessary, adapted by a CAD engineer.
Whereas the final design after topology optimization is always preceded by a pre-established concept that needs to be improved (usually with regard to materials and weight), generative design dispenses with basic design. This is a significant difference between the two. In generative design, “constraints” (conditions) are defined to create as many new designs as necessary to explore the many possibilities. These constraints can be blocking surfaces, the material used, the chosen manufacturing process, costs, etc. Artificial intelligence is then used to come up with different design possibilities that correspond to the previously defined parameters.
It is important to mention that generative design does not guarantee an optimal solution from the outset, but examines possible trade-offs between set objectives (such as weight, material consumption and costs) and proposes several options according to the user’s preferences. As with topology optimization, this requires engineers to first define these conditions and then select the final design from the countless possibilities.
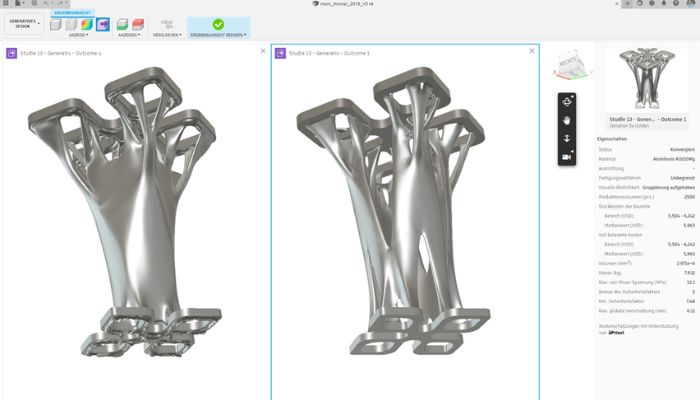
Comparison between topology optimization and generative design (photo credits: Mensch und Maschine)
Both solutions support product development using computer-aided mechanisms, and create optimized designs in terms of lightness, cost reduction and material savings, etc., while maintaining or improving component quality. It should also be added that the proposed designs are always inspired by nature, with similarities to bone structures, beehives, corals, and so on. Whereas topology optimization results in a single final design, generative design offers several possibilities, depending on the constraints defined.
Topology optimization and generative design therefore both lead to the creation of an optimal design in different ways, but it is possible that these designs may pose challenges in the next production phase. Not all manufacturing processes are capable of realizing complex designs with nested geometries, overhangs and variable wall thicknesses, which are sometimes proposed as part of the optimizations.
This is why the potential of these two tools can be particularly well exploited in combination with 3D printing. Why? Well, on one hand it is because both solutions generate designs that would be impossible or difficult to achieve with traditional processes; on the other, because designs can be generated according to the manufacturing method.
In the case of generative design, it is therefore possible to determine from the outset that the part will be manufactured by additive manufacturing, and the software will take this condition into account, generating only solutions that can be produced using 3D printing technology. This is not the case with topology optimization. A CAD engineer must check the generated design and, if necessary, refine it according to the manufacturing method. For example, if the part is manufactured by 3D printing, support structures may be required, depending on the method used. The design engineer must then determine where and how these can be placed.
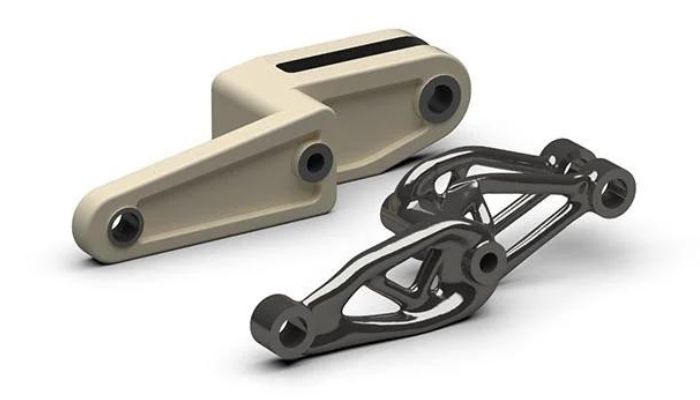
A representation of a part that has been optimized by generative design and can then be 3D printed (photo credits: Siemens PLM)
Benefits and Limitations
One of the advantages of both methods is that designs are optimized according to parameters defined using algorithms or artificial intelligence. This saves time, materials and therefore costs. Generative design makes it possible to create hundreds or even thousands of design options and compare them with each other without wasting time. Simulations and tests are already part of the design process, avoiding costly rework. Cost can also be defined as a condition in generative design, whereas topology optimization of a component concept gives no insight into costs.
The many design possibilities in generative design can be an advantage in showing varied solutions. With topology optimization, there is only one final design at the end. In this case, the engineer still has to improve and verify, whereas with the other tool, he applies his know-how to make a choice. A key advantage is that, at the end of the generative design process, the designs are available in a CAD file which can be exported as a STEP file, for example to manufacture the part by additive manufacturing and simplify the rest of the process chain.The model obtained by topology optimization must first be converted into a CAD file.
Although these two computer-aided design solutions offer many positive incentives, they are also associated with certain challenges. For example, software solutions for generative design and topology optimization are very expensive. Additionally, their correct and efficient use requires specialized knowledge.
Adding complexing, topology optimization is already a tried and tested method, and many large companies have become familiar with it over the years. But generative designhas only become possible and popular in recent years. As a result, generative design software is not yet widely used, although it can help identify more solutions.
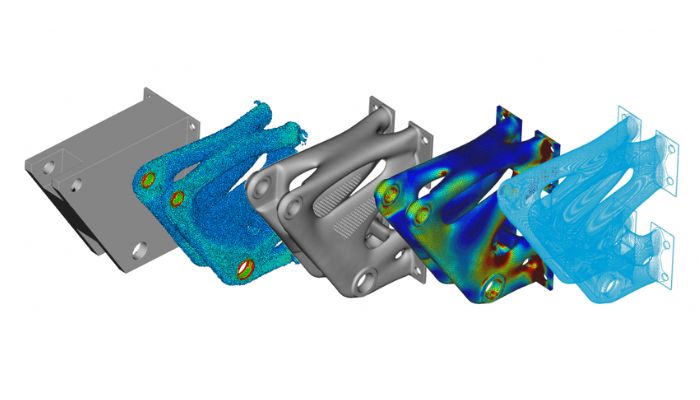
Topology optimization is mainly used to improve part weight (photo credits: Formlabs)
For both processes, they can’t do without CAD designers and their expertise. They need to look at material properties and manufacturing technology, and analyze designs in terms of feasibility. End use must also be taken into account in the design process. AI-generated designs may be the most functionally optimal, but they are often not very beautiful. Where this is the case, designers need to make adjustments not only in terms of aesthetics, but also haptics, acoustics and smell, as these sensory stimuli are decisive for the product’s end-users. It is precisely at these sensory points that topology optimization and generative design reach their limits, and cannot (yet) replace human involvement in the design process. Nevertheless, these two design solutions open up a wide range of possibilities in many applications.
Applications
Although the multiple fields of application often overlap, the methods differ in their approaches and applications. Topology optimization always works within defined limits, removing material from a given basic shape while performing FEA simulations to improve performance. Generative design, on the other hand, goes a step further. It uses algorithms to develop new and creative solutions that not only optimize material distribution, but also expand the design space. Topology optimization and generative design are used in the same sectors where the physical properties of a component are crucial, such as aerospace or automotive, but also in the creative and architectural sectors.
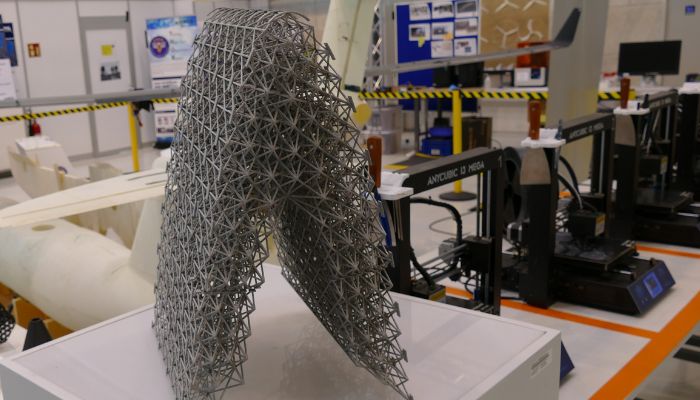
Part of an Airbus A320, developed using generative design (photo credits: Autodesk)
In the aerospace field, topology optimization can be used to improve existing designs to produce lighter aircraft structures, such as reinforcing ribs, thus reducing fuel consumption. One example is the work of Andreas Bastian, who has designed aircraft seats 54% lighter, significantly reducing the weight of the aircraft as a whole. But generative design is also used by companies like Airbus to create stronger parts and creative components. A well-known example is the bulkhead of the Airbus A320, which was manufactured using natural growth processes as inspiration.
In the automotive industry, topology optimization contributes to the development of lightweight, stable and safe vehicles, by improving existing designs through weight reduction. Fiat Chrysler’s suspension system was lightened by 36% by integrating more than twelve different components into a single part.
Generative design is also used to optimize automotive components by creating new solutions. It enables companies to improve the performance of their products and meet growing environmental protection requirements. Bugatti, for example, used generative design software to develop the Chiron’s wing control system, which optimized assembly and reduced weight by over 50%. But Porsche also used generative design to manufacture an innovative piston for the 911 GT2 RS high-performance engine.
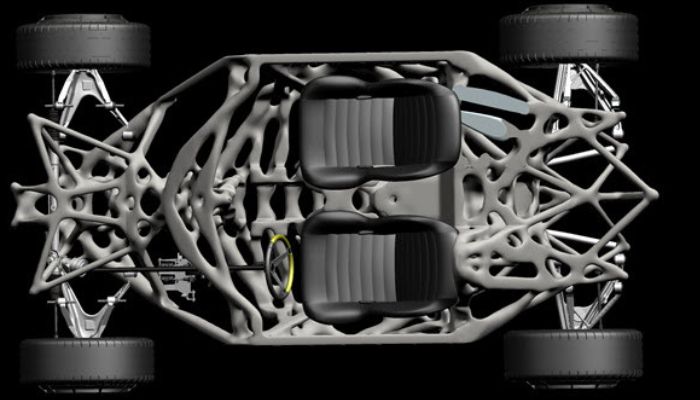
A vehicle design developed using generative design.The similarity with bone structures is particularly striking here, and optimized vehicles could resemble them in the future (photo credits: Siemens).
In the medical field, the two modeling tools also play a decisive role. NuVasive’s custom implants, which use lattice structures to reduce weight without compromising stability, are an example of the application of topology optimization.
In comparison, generative design enables advanced solutions, particularly in the field of osseointegration, where implants are designed to resemble the structure of natural bone. This encourages the growth of new bone tissue on the 3D-printed implant, improving long-term stability.
While topology optimization in the medical field is often aimed at efficiency and weight reduction, generative design focuses on optimal adaptation to the patient’s individual anatomy, particularly when manufacturing patient-specific prostheses.
In addition, generative design is used in architecture and construction to create novel, functional concepts for spaces, while offering solutions to complex design problems.Topology optimization is also increasingly used in architecture to improve existing building forms and increase load-bearing capacity. Both methods enable architects to design more efficient structures during the design phase, often drawing inspiration from natural structures. The MX3D bridge, built over a canal in Amsterdam using generative design, is a perfect example.
The fashion and jewelry industry makes extensive use of generative design, as the focus is less on optimizing factors such as weight, and more on creating creative and original shapes. Designer Julia Körner is such a case: she created innovative 3D-printed costumes for the blockbuster Black Panther. Anouk Wipprecht also uses generative design, for example for her ScreenDress, which was then realized using Multi Jet Fusion technology. Here, it’s all about pushing back the boundaries of traditional fashion and creating new aesthetic structures through digital design processes.
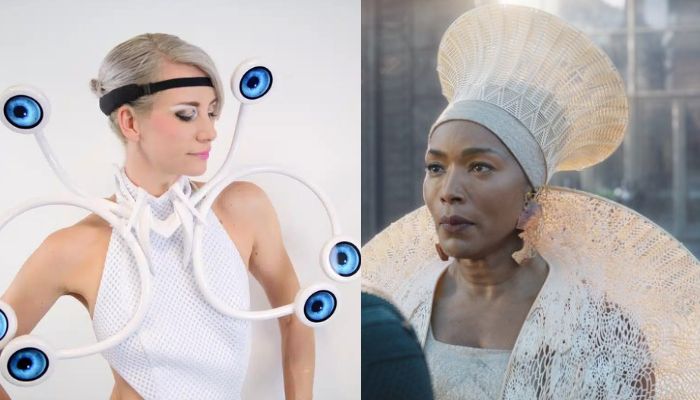
On the left, Anouk Wipprecht’s dress, and on the right, a design by Julia Körner (photo credits: Anouk Wipprecht, Julia Körner)
Software Providers
To make effective use of topology optimization and generative design, specialized software solutions are required. For topology optimization, tools like Oqton’s 3DXpert are ideal, especially for implants and complex geometries. But Altair Inspire is also ideally suited to applications in the automotive and aerospace industries. Ansys Discovery and Netfabb also offer topology optimization support to ensure stable 3D prints. Netfabb also offers a free trial version, otherwise the price is $7,690 for one year or $7,690 for three years. Another software solution is CogniCAD from ParaMatters, a cloud platform that combines topology optimization and generative design, and specializes in complex 3D constructions. To use CogniCAD, you can purchase tokens, which range in price from $14.90 to $5.90, depending on the software version you choose.
Z88Arion® is a free software package featuring three Z88Arion® is a free software package featuring three optimization algorithms for topology optimization.cSiemens NX-12 stands out for its integration of topology optimization based on convergent modeling technology, which enables flawless 3D modeling and results in lighter yet more robust components. The software is equally suited to generative design and topology optimization.
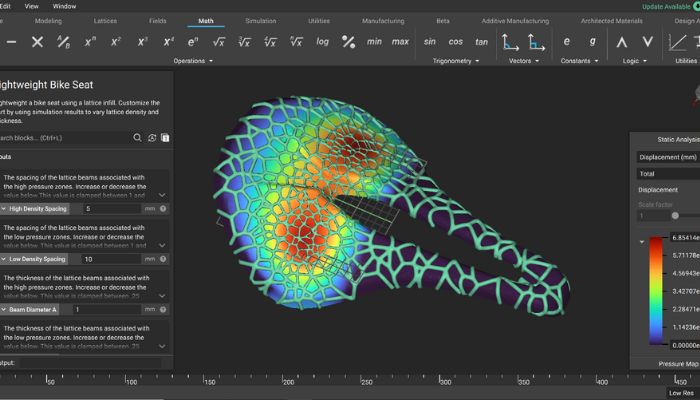
nTop is software for generative design (photo credits: nTopology)
For generative design, nTopology offers nTop, a powerful software package that provides generative tools for individual requirements. Fusion 360 from Autodesk is also a good choice, with functions such as sketching, surface modeling and rendering, and can be used for topology optimization and generative design. Others include Creo Parametric and Creo Generative Design, which use cloud technologies to create optimized design concepts and quickly implement cost-effective designs. Another software solution is Hexagon’s MSC Apex Generative Design, suitable for the production of detailed and complicated structures; or Cognitive Design, which will enable you to quickly obtain optimized designs.
The right software is the decisive partner for topology optimization and generative design projects.cIn today’s market, generative design solutions tend to be more expensive than topology optimization solutions. However, depending on budget and objectives, it is possible to find what you need in a rapidly expanding market.In all cases, engineers are encouraged to familiarize themselves with the software, as it is more or less intuitive. Expertise is essential to make the most of the design advantages of topology optimization and generative design. Below is a table comparing the main features.
Do you use topology optimization or generative design?Let us know in a comment below or on our LinkedIn, Facebook, and Twitter pages! Don’t forget to sign up for our free weekly newsletter here for the latest 3D printing news straight to your inbox! You can also find all our videos on our YouTube channel.