Topology Optimization for 3D printing
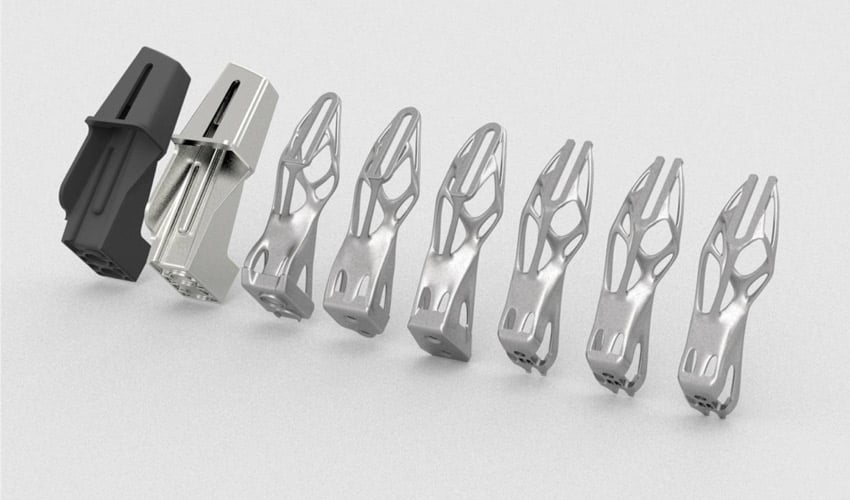
Additive manufacturing, in contrast to traditional machining techniques, makes it possible to produce parts with complex geometries whose total weight can be optimized using a numerical method called topology optimization. This method also maximizes the mechanical strength of the part created. Topology optimization is part of numerical design which allows to find, thanks to mathematical formulas, the optimal material distribution in a given volume subjected to more or less important mechanical constraints.
Topology optimization therefore consists of removing the material that is not subject to stress, using dedicated software. Among the most well-known solutions are Ansys Discovery, Tosca from Dassault Systèmes, Within Labs from Autodesk, Inspire from SolidThinking, Netfabb and Simufact Additive.
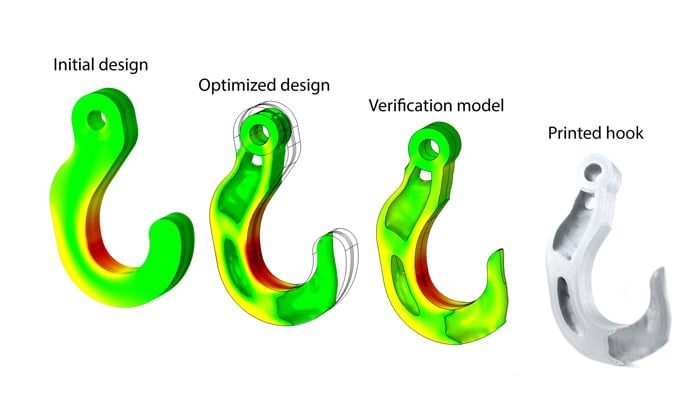
The design process via topology optimization
Topology optimization: how does it work?
Conventional numerical design processes involve applying loads to a part that has already been manufactured and evaluating where it weakens. Engineers must then alter the design until the part meets the given mechanical constraints. With topology optimization, the logic is different: the mechanical loads represent input data that will allow the software to propose a new geometry for the part. Therefore, there should be less iterations made to the design of the part, considerably reducing design and manufacturing lead times.
In concrete terms, topology optimization starts with rough 3D model of a new or existing part, to which different loads and forces will be applied to the part (a pressure on the fixing lugs for example). The software then calculates all the applied forces.
During this stage of design, the software will remove material where it calculates that the part is not subject to stress. A draft of the future optimized part is then already visible. The final geometry, meeting both mechanical and design requirements can then be obtained after smoothing the part. Topology optimization meets either a need for mass reduction or an increase in the mechanical strength of the part.
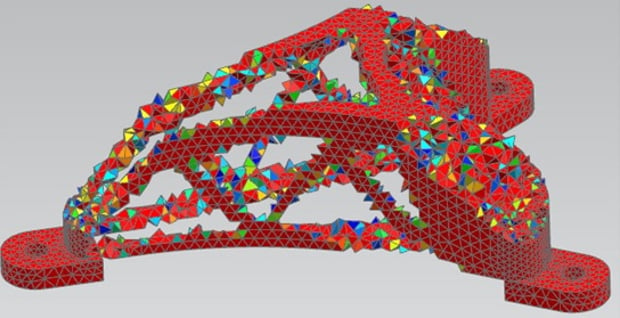
3D model after the removal of “unnecessary” material using the topology optimization method
Topology Optimization software
Not all CAD software offer these features: even if it is not necessarily used in the modeling and manufacturing process, it may be preferable to opt for a solution that includes it, to be sure to design an optimal part. Some developers have therefore created dedicated software. One of the pioneers is probably Altair with its very first OptiStruct solution, later joined by another solution, Altair Inspire. We can also mention Ansys, Dassault Systèmes, Autodesk and nTopology. There are many CAD software programs that include extra features to optimize your part such as Solidworks, Creo and Fusion 360.
Choosing your topology optimization software is a key step because the tool will allow you to define the constraints on the part you are creating according to the manufacturing material, the geometric properties and the mechanical loads. It will analyze the different load cases, whether the part is used normally or in extreme cases, but also the space available for the design and the areas of the part you do not wish to modify.
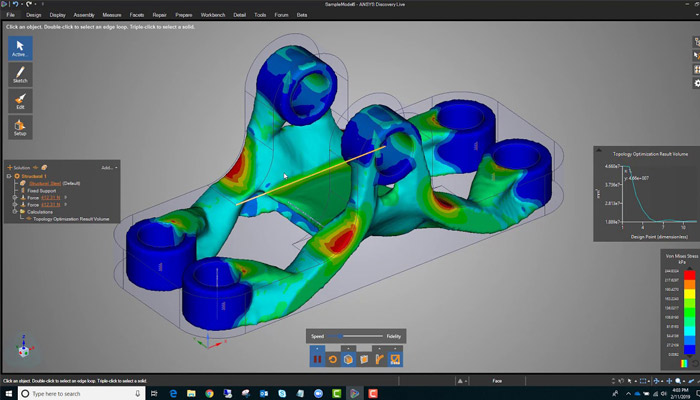
Several software are available today
Who uses topology optimization and for what purpose?
The automotive industry has been quick to address this problem to achieve cost reductions with material savings, especially in series production. Indeed, a gain of a few grams per vehicle, on a production of several million units, represents tons of material saved. We can give you the example of the 3D printed chassis of the Light Rider, a part that weighs only 6 kilos thanks to optimal material distribution. A more recent example is the suspension part for Fiat Chrysler Automobiles, which combines more than 12 different components into a single part. The designers stated they had reduced its weight by 36%.
The aerospace industry is undoubtedly another sector very interested in topology optimization; to reduce indirect costs. A lighter aircraft consumes less fuel, which in the long term generates significant savings for an airline company. This is what designer Andreas Bastian proved with his aircraft seats: he imagined a 54% lighter design for each seat, which represents a significant weight reduction for an aircraft. Beyond the weight aspect, topology optimization allows the aerospace sector to imagine much more complex shapes since the industry is freeing itself from the constraints imposed by a mold.
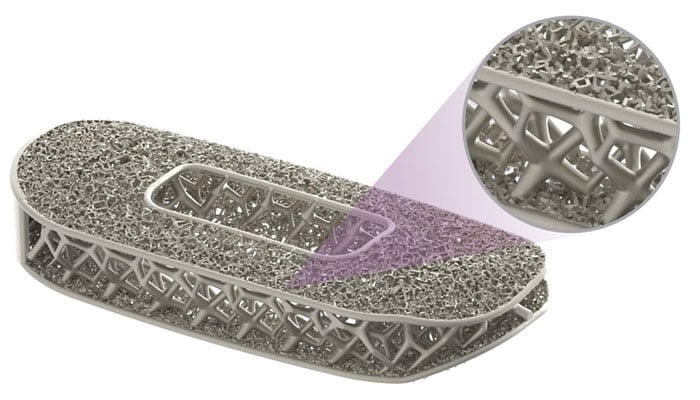
In the medical sector, topology optimization enables the design of more resistant implants | Image via Nuvasive
Finally, the medical profession is looking into this design method, particularly for the manufacture of custom-made implants: topology optimization enables to imitate bone density and rigidity, while reducing total weight. In fact, many implants integrate lattice structures and remain as strong as those traditionally designed, or even stronger in some cases.
Have you ever noticed topology optimization being used around you? Let us know in a comment below or on our Facebook and Twitter pages! And remember to sign up for our free weekly Newsletter, to get all the latest news in 3D printing send straight to your inbox!
It is an interesting for someone to develop his or her career.